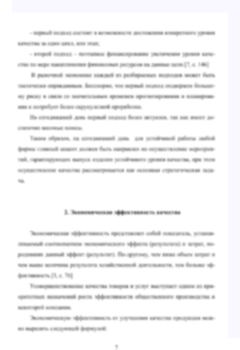
Автотермическая переработка углей методом частичной газификации в слое с пульсирующим дутьем
Введение……………………………………………………………………. 5
Глава 1. Обзор существующих методов термической переработки
угля…………………………………………………………………………. 11
1.1 Перспективность термической переработки углей низкой
степени метаморфизма……………………………………………… 11
1.2 Газификация угля………………………………………..……… 13
1.3 Производство облагороженного твердого топлива…………… 15
1.4 Зарубежный опыт полукоксования углей……………………… 17
1.4.1 Процесс ENCOAL………………………………………… 18
1.4.2 Печи Лурги для полукоксования………………………… 19
1.4.3 Переработка угля в печах типа SJ……………………….. 21
1.4.4 Технология LiMaxTM……………………………………… 25
1.4.5 Технология GEO-COAL………………………………….. 28
1.4.6 Технология сушки и брикетирования угля без
связующего BCB………………………………………………… 30
1.5 Отечественные технологии полукоксования…………………. 32
1.5.1 Разработка Энергетического института (ЭНИН)……… 32
1.5.2 Полукоксование на цепных колосниковых решѐтках…. 35
1.5.3 Полукоксование в туннельных печах…………………… 36
1.5.4 Получение кусковых углеродистых восстановителей в
печах вертикального типа……………………………………… 37
1.6 Технологии серии ТЕРМОКОКС ……………………………… 38
1.6.1 Технология частичной газификации угля в кипящем
слое (ТЕРМОКОКС-КС) ……………………………………… 39
1.6.2 Технология частичной газификации угля в слоевых
аппаратах (ТЕРМОКОКС-С)…………………………………… 41
1.7 Теоретическая база исследований в области карбонизации
угля…………………………………………………………………… 46
1.8 Основные выводы и постановка задач исследования………… 52
Глава 2. Экспериментальное исследование взаимосвязи тепловых
параметров процесса карбонизации с прочностными
характеристиками полукокса…………………………………………… 54
2.1 Постановка задач экспериментального исследования……….. 54
2.2 Методика проведения экспериментов и описание
экспериментальной установки……………………………………… 55
2.3 Исследование процесса сушки одиночных образцов угля…… 58
2.4 Исследование процесса карбонизации одиночных образцов
углей 3Б (разрез Большесырский) и Д (разрез Моховский)……… 65
2.5 Исследование процесса карбонизации углей других марок … 71
2.6 Обсуждение результатов исследований и основные выводы… 72
Глава 3. Исследование частичной газификации угля в слоевом
аппарате с пульсирующим обращѐнным дутьѐм……………………. 75
3.1 Постановка задач экспериментального исследования ……… 75
3.2 Поисковые эксперименты и обоснование необходимости
применения пульсирующего дутья………………………………… 78
3.3 Термическая переработка угля 3Б (разрез Большесырский)… 79
3.4 Термическая переработка угля марки Д (разрез Моховский).. 83
3.5 Термическая переработка угля марки Д (разрез Караканский) 85
3.6 Обсуждение полученных результатов………………………… 86
3.7 Краткие выводы………………………………………………… 87
Глава 4. Подготовка результатов исследования к практическому
использованию в промышленности……………………………………. 89
4.1 Постановка задач этапа…………………………………………. 89
4.2 Технические решения по аппаратурному оформлению
технологического процесса………………………………………… 89
4.3 Технологическая схема производства облагороженного
твердого топлива……………………………………………………. 94
4.4 Технические показатели производства………………………… 98
4.5 Экономические показатели производства……………………… 103
4.6 Краткие выводы…………………………………………………. 106
Заключение………………………………………………………………… 108
Список использованных источников………………………………….. 111
ПРИЛОЖЕНИЕ А: Экспериментальное оборудование…………………. 122
ПРИЛОЖЕНИЕ Б: Протоколы испытаний………………………………. 130
ПРИЛОЖЕНИЕ В: Технологический регламент………………………… 135
ПРИЛОЖЕНИЕ Г: Акты внедрения…………………….………………… 161
В России в последние годы уделяется особое внимание исследованиям в
области глубокой переработки бурых и длиннопламенных углей. На ближайшую
перспективу поставлена задача увеличения доли угля в энергетическом балансе
страны за счѐт снижения потребления природного газа [1].
Согласно принятой Правительством РФ «Энергетической стратегии России
на период до 2035 года» поставлена задача обеспечения конкурентоспособности
угольной продукции на внутреннем рынке с заменяющими еѐ энергоресурсами, а
на внешнем – с альтернативными поставщиками [2]. К сожалению, по целому
ряду причин эта программа не исполняется [3]. В то же время увеличение
потребления ископаемых углей будет сопровождаться ростом экологической
нагрузки на окружающую среду, поскольку при сжигании и переработке угля
образуется больше вредных побочных продуктов по сравнению с нефтью и
природным газом.
Снижение негативного воздействия угольной энергетики на окружающую
среду может быть достигнуто за счѐт совершенствования технологии сжигания
угля и перехода к использованию экологически более безопасных видов топлива
угольного происхождения. Традиционные методы энергетического и
технологического использования угля, по существу, достигли своего предела
экономической и экологической эффективности. В связи с этим значительный
интерес представляет разработка новых способов переработки угля, которые
обеспечивают качественное повышение энергоэффективности использования
угля, а также высокий уровень экологической безопасности, как получаемой
продукции, так и самих способов переработки [4].
Угли Канско-Ачинского бассейна (КАБ) являются одними из наиболее
перспективных для комплексной переработки. Бассейн располагает уникальными
запасами бурых углей, пригодных для добычи открытым способом. При выборе
того или иного способа переработки Канско-Ачинских углей прежде всего
необходимо использовать их преимущества: низкую себестоимость добычи;
низкую зольность; низкое содержание серы, фосфора, тяжелых металлов и других
вредных примесей; высокую реакционную способность; стабильность состава, в
т.ч. минеральной части [5].
В данной работе рассмотрены вопросы технической переработки углей с
высоким содержанием летучих веществ для получения высококалорийного
твердого топлива повышенной прочности. Такой продукт находит применение в
качестве бездымного коммунально-бытового топлива.
В результате выполненного обзора современного состояния проблемы
переработки молодых углей, была сформулирована цель и поставлены задачи
исследования для еѐ достижения. Для проведения исследования на частицах угля
создана экспериментальная установка и разработана методика проведения
экспериментов. В результате экспериментального исследования были выявлены
основные управляющие параметры процесса, критические температурные уровни
для сушки и карбонизации, была получена информация по влиянию различных
температурных уровней и скоростей нагрева на прочностные характеристики
частицы угля. По итогам экспериментов получен высококалорийный полукокс из
углей марки 3Б и Д с теплотой сгорания свыше 27,2 МДж/кг (6500 ккал/кг) с
высокими прочностными показателями, удовлетворяющими условиям хранения и
транспортировки.
На основе вышеописанных результатов обоснована конструкция установки
для переработки угольного сырья в промышленных масштабах. В качестве
основного перерабатывающего аппарата выбран слоевой газификатор с
обращенным воздушным дутьем. Предложен вариант переработки с
использованием пульсирующего режима подачи воздуха. Проведено
экспериментальное исследование в результате которого найдены режимы
переработки, обеспечивающие высокую прочность получаемого полукокса, для
углей: 3Б (разрез Большесырский, Красноярский край, ООО «Сибуголь»), Д
(разрез Моховский, Кемеровская область, ОАО «Угольная компания
Кузбассразрезуголь») и Д (разрез Караканский, Кемеровская область,
ООО «Каракан-Инвест»). Подана заявка на изобретение (заявка на пат.
2015143182 от 09.10.2015).
По итогам экспериментов на слоевом газификаторе с пульсирующим
обращенным воздушным дутьем, выполнена технико-экономическая оценка
организации углеперерабатывающего производства на территории одного из
разрезов Красноярского края.
Сформулированы основные результаты работы и выводы.
1. На основании анализа современных технологий переработки угля,
направленных на получение высококалорийного твердого топлива, определена
перспективность термической переработки углей с высоким содержанием летучих
веществ с возможностью комбинированного производства энергоносителей
исключающей стадию брикетирования конечного продукта и обеспечивающей
экологическую безопасность производства.
2. В результате экспериментальных исследований процесса нагрева
одиночных частиц бурого и длиннопламенного (каменного) углей установлены и
количественно определены основные управляющие параметры процесса
карбонизации (скорость нагрева, максимальная температура греющей среды),
изучено их влияние на показатели процесса карбонизации и прочностные
характеристики получаемого полукокса. Показано, что достаточно прочный
полукокс (прочность по ГОСТ 21289-75 не менее 8 МПа) получается при
соблюдении скорости нагрева не более 0,056 град/c.
3. Впервые обнаружен эффект «восстановления прочности» в области
температур 400–500°C. Предположительно, упрочнение происходит за счет
коксования части высокомолекулярной органики (смол), образующейся на
заключительной стадии пиролиза органической части угля.
4. На основе результатов исследований, полученных на одиночных частицах
угля, обоснована конструкция установки для нового процесса производства
полукокса. На данной установке экспериментально определены основные
технологические параметры процесса карбонизации угля: расход воздуха,
продолжительность периода подачи и останова дутья, которые обеспечивают
приемлемую для практики прочность полукокса.
5. Разработан новый технологический процесс переработки бурого и
длиннопламенного (каменного) углей в высококалорийный полукокс на основе
частичной газификации в слое с пульсирующим обращенным дутьем.
6. Разработаны технологическая схема и технологический регламент
производства, реализующие процесс автотермической переработки углей низкой
степени метаморфизма в слоевом аппарате с получением высококалорийного
бездымного топлива. Технологический регламент производства принят для
использования при проектировании углеперерабатывающих предприятий:
компанией ООО «Сибуголь» (г. Красноярск), проектным институтом
СибНИИуглеобогащение (АО «СУЭК»), ООО «СУЭК-Хакасия» (г. Черногорск).
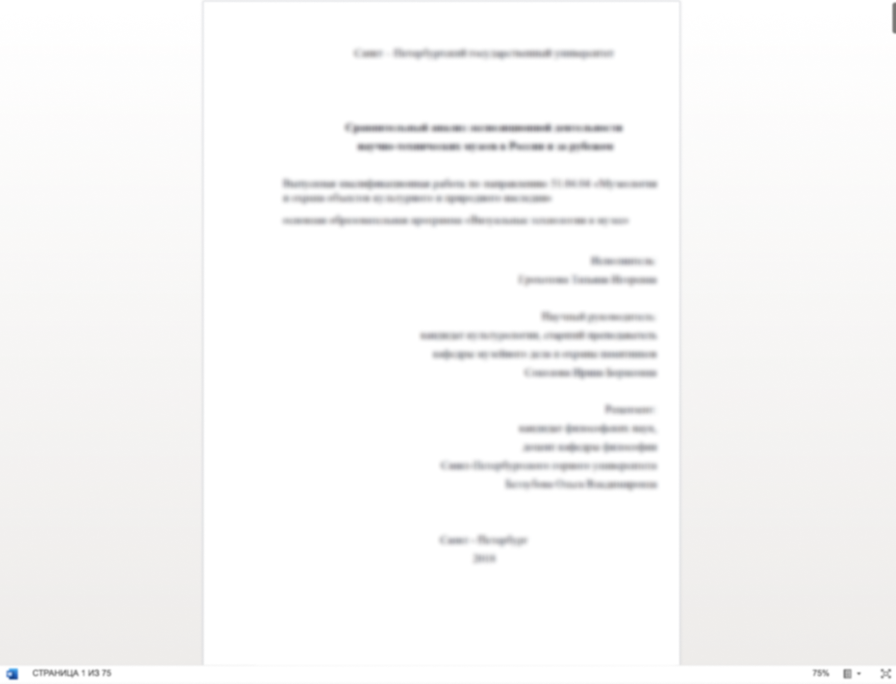
Помогаем с подготовкой сопроводительных документов
Хочешь уникальную работу?
Больше 3 000 экспертов уже готовы начать работу над твоим проектом!