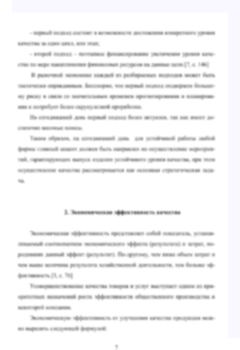
Электрофизическая обработка длинномерных электротехнических материалов при пониженных давлениях
Введение…………………………………………………………………………………………………………… 6
Глава 1. Исследование глубины залегания газа в стальной проволоке ……………… 14
1.1 Обзор методов определения механизма выделения газа ……………………………… 15
1.1.1 Определение механизма выделения газа из анализа кривых …………………….. 15
газовыделения…………………………………………………………………………………………………. 15
1.1.2 Определение механизма выделения газа из анализа коэффициентов
диффузии ………………………………………………………………………………………………………… 16
1.1.3. Определение механизма выделения газов по анализу десорбционных
кривых ……………………………………………………………………………………………………………. 17
1.2. Экспериментальный комплекс ………………………………………………………………….. 19
1.2.1. Методика обработки спектрограмм ………………………………………………………… 21
1.2.2. Методика количественной градуировки омегатрона ……………………………….. 21
1.2.3. Расчет согласования времен индикации потока ………………………………………. 23
1.2.4 Метод накопления при анализе механизма выделения газа………………………. 24
1.2.5. Методика расшифровки спектра масс …………………………………………………….. 25
1.3. Определение механизма выделения газов из электродной проволоки ………… 26
1.3.1. Исследование спектров общего газовыделения из стальной электродной
проволоки ……………………………………………………………………………………………………….. 27
1.3.2. Исследование механизма выделения кислорода из стальной электродной
проволоки ……………………………………………………………………………………………………….. 28
1.3.3. Анализ выделения газа из электродной проволоки в процессе вакуумного
отжига …………………………………………………………………………………………………………….. 29
1.3.4. Анализ выделения газа на переменных скоростях нагрева ……………………… 31
Глава 2. Исследование формирования защитных пленочных покрытий на
длинномерных материалах, вводимых из атмосферы в область низкого давления34
2.1. Визуализация потока пара…………………………………………………………………………. 35
2.2. Анализ способов управления формированием толщины пленки ………………… 38
2.2.1. Параметрическое управление потоком пара ……………………………………………. 39
2.2.2. Общая схема параметрического управления потоком пара ……………………… 40
2.2.3. Геометрическое управление потоком пара ……………………………………………… 42
2.2.4. Влияние плазмы электронного потока на конденсацию пара ………………….. 44
2.2.5. Формирование пленочных покрытий при повышенных давлениях………….. 47
2.3.1. Фазовая диаграмма и изобарный потенциал ……………………………………………. 50
2.3.2 Моделирование формирования защитного покрытия на
электротехническом материале при обмене газа………………………………………………. 51
Глава 3. Исследование условий уменьшения потребляемой мощности для ввода
длинномерных материалов из атмосферы в вакуум и вывода из вакуума в
атмосферу ……………………………………………………………………………………………………….. 57
3.1 Суть проблемы ………………………………………………………………………………………….. 57
3.2. Анализ течения газа в устройстве ввода/вывода проволоки ……………………….. 59
3.2.1. Визуализация течения потока газа в устройстве для обработки проволоки 59
3.2.2. Влияние параметров устройства ввода/вывода на давление в камере
обработки ……………………………………………………………………………………………………….. 61
3.2.3. Зависимость давления в плазменной камере от формы выводных
элементов ……………………………………………………………………………………………………….. 63
3.2.4. Устройства вывода с отклонением газового потока ………………………………… 65
3.2.5. Устройство вывода с дополнительной подачей газа ………………………………… 67
3.2.6. Предельные возможности повышения перепада давления за счет
усложнения формы элементов …………………………………………………………………………. 69
3.3. Электрофизические способы создания перепада давления ………………………… 70
3.3.1. Предельные возможности создания перепада давления с помощью
газодинамических эффектов ……………………………………………………………………………. 70
3.3.2. Исследование влияния разряда на расход газа в устройство ввода/вывода . 72
3.3.3. Стационарный дуговой разряд между элементами ………………………………….. 73
3.3.4 Откачивающее действие разряда……………………………………………………………… 73
3.4. Устройства ввода/вывода с виртуальными элементами ……………………………… 74
3.5. Выводы по электрофизическим способам повышения эффективности
выводных устройств ……………………………………………………………………………………….. 76
Глава 4. Конструирование устройств для электрофизической обработки
электротехнических материалов ……………………………………………………………………… 78
4.1. Рекомендации по расчету и согласованию устройств для поточной
обработки электротехнических материалов……………………………………………………… 78
4.1.1. Расчет потребляемой мощности ……………………………………………………………… 78
4.1.2. Согласование по необходимой производительности откачных средств …… 79
4.1.3. Расчет устройства для ввода/вывода проволок ……………………………………….. 79
4.1.4. Согласование передаточных характеристик устройства для вывода с
работой вакуумных насосов …………………………………………………………………………….. 83
4.1.5. Согласование вольтамперной характеристики устройства ………………………. 83
4.1.6. Защита системы с выводом длинномерных электротехнических
материалов от электрических пробоев …………………………………………………………….. 84
4.2. Схемы устройств для поточной обработки проволок …………………………………. 85
4.2.1. Устройство для обработки проволочных материалов ……………………………… 85
4.2.2. Устройство с камерой ионной очистки и камерой плазменного
нагревателя …………………………………………………………………………………………………….. 88
4.2.3. Устройство для очистки толстых проволок в импульсном дуговом
разряде ……………………………………………………………………………………………………………. 90
Устройство для очистки и отжига «столбовой» проволоки ………………………………. 92
4.2.5. Устройство для отжига проволочных испарителей с магнитным полем и
плазменным контактом……………………………………………………………………………………. 94
4.2.6 Устройство для поточного отжига электродной проволоки между
разнесенными плазменными контактами …………………………………………………………. 95
4.3 Схемы устройств для формирования пленок ………………………………………………. 96
4.3.1 Устройство для поточного алюминирования фторопластовых и
полиэтиленовых пленок ………………………………………………………………………………….. 96
4.3.2. Устройство для поточного алюминирования проволочных материалов …… 99
4.3.4. Устройство для цинкования длинномерных материалов ……………………….. 101
4.3.5 Устройства для переработки полимеров и формирования полимерных
покрытий ………………………………………………………………………………………………………. 103
5. Заключение. Основные результаты работы ………………………………………………… 107
Список литературы ……………………………………………………………………………………….. 114
Приложение А Документы об использовании результатов работы …………………. 137
Актуальность темы исследования. В последнее время расширяется
применение методов обработки электротехнических материалов потоками
электронов ионов и плазмы взамен энергоемких и громоздких механических и
химических методов [1–15]. Актуальность темы исследования определяется
высокой потребностью в разработке основ электрофизических технологий,
обеспечивающих эффективную высокопроизводительную обработку
длинномерных электротехнических материалов и нанесение покрытий в
условиях поточной обработки. Однако при применении поточной
электрофизической обработки длинномерных электротехнических материалов
возникает задача ввода материала из атмосферы в область низких давлений,
очистки от загрязнений и газов, формирование защитного покрытия и вывода
материала обратно в атмосферу. Вместе с тем пока недостаточно исследованы
процессы обеспечения вакуума при открытых отверстиях вакуумных камер,
необходимых для ввода материала в область обработки. Недостаточно
исследованы физико-химические процессы выделения газа из материала в
процессе электрофизической обработки, а также процессы формирования
покрытий в условиях поточной обработки материала при пониженном
давлении.
Актуальность работы в научном аспекте определяется необходимостью
исследования процессов, сопровождающих поточную электрофизическую
обработку длинномерных электротехнических материалов. Актуальность в
прикладном аспекте определяется тем, что недостаточно разработаны основы
проектирования проточных вакуумных систем с вводом материалов из
атмосферы в область пониженного давления [16 – 75].
В связи с этим, работа, направленная на исследование закономерностей
электрофизической обработки длинномерных электротехнических материалов
при пониженном давлении является актуальной.
Работа выполнена в рамках приоритетных направлений развития науки,
технологий и техники в РФ (п. 8: Энергоэффективность, энергосбережение,
ядерная энергетика) по направлению «Производственные технологии»;
Федеральная целевая программа: «Исследование и разработки по приоритетным
направлениям развития научно-технического комплекса России на 2014 – 2020
г.г; постановление Правительства № 218 по созданию высокотехнологичного
производства в рамках подпрограммы «Институциональное развитие научно-
исследовательского сектора»; гранты Президента Российской Федерации для
государственной поддержки ведущих научных школ НШ-422.2014.8 (2014–2015
г.г.), а также Федеральной целевой программы «Кадры, гос контракт № 02.740.
11.0553», госзадания Минобрнауки РФ (проект 7.2647.2011)
Объект исследования: промышленные процессы поточной ионной и
термической обработки металлических проволочных электротехнических
материалов, которые вводятся из атмосферы в область газоразрядной плазмы
высоковольтного тлеющего разряда с давлением 1 – 10 Па и выводятся обратно
в атмосферу.
Предмет исследования. Исследование процесса ионной очистки,
удаления газов и отжига модифицированных электродных проволок марки
Св-12 ГС для сварочных электродов марки Э-138/50 Н. Определение
закономерности сорбционных процессов кислорода в таких материалах,
определяющих коррозионную стойкость сварочных швов. Исследование
закономерности формирования защитного цинкового покрытия на железной
проволоке в условиях совмещения процессов ионной очистки и отжига в
условиях поточной обработки в проточной вакуумной системе с натеканием и
откачкой газа, а также закономерности поточной электрофизической обработки
вольфрамовой и молибденовой проволок.
Степень разработанности темы. Исследованием процессов обработки
электротехнических материалов с использованием электронов, ионов и плазмы
при пониженном давлении занимаются в Институте электрофизики УрО РАН, г.
Екатеринбург, (Гаврилов Н.В., Овчинников В.В. и др.), ИСЭ СОРАН, г. Томск
(Коваль Н.Н, Королев Н.Д., Окс Е.М. и др.), ИФПМ СОРАН, Томск (Кульков
С.Н., Зуев Л.Б, Сараев Ю.Н., Лотков А.И. и др.), ИФM CОРАН г. Улан-Удэ
(Семенов А.П) и ряде других предприятий (практически везде, где имеются
вакуумные технологии).
Недостаточно изученными являются процессы определения глубины
залегания газа в материале; процессы отжига, очистки, формирования
пленочных покрытий в форвакуумном диапазоне давлений 1 – 10 Па.
Традиционные технологии не приспособлены для формирования пленок на
материалах, вводимых из атмосферы. Обеспечение вакуума в генераторе
плазмы требует большой мощности для обеспечения вакуума в вакуумной
камере, имеющей отверстие в атмосферу для ввода материала. Затраты
мощности составляют 5–10 кВт на 1 мм2 площади выводного отверстия, что
сдерживает технологии поточной электрофизической обработки длинномерных
электротехнических материалов.
Целью работы является исследование физико-химических процессов,
определяющих свойства длинномерных электротехнических материалов и
изделий при их обработке в проточных форвакуумных системах в условиях с
непрерывным поступлением и откачкой газа и наносимых в таких условиях
тонкопленочных покрытиях.
Метод решения задач (идея) состоит в обработке материала потоком
ионов или электронов в процессе его непрерывной протяжки через отверстия
вакуумной камеры. В камере обеспечивается высоковольтный тлеющий разряд
при давлениях 1 – 10 Па. Электротехнический материал подвергается ионной
очистке, термическому отжигу и формированию на нем защитного покрытия.
Для уменьшения энергетических затрат на отжиг проводится определение
глубины залегания газа в материале. Для формирования защитных покрытий
проводится визуализация потока пара испаряемого материала. Для
формирования качественных защитных покрытий исследуется формирование
пленок при натекании газа в систему с одновременной откачкой газа. Для
уменьшения энергетических затрат на откачку газа, поступающего через
отверстия протяжки материала, материал последовательно протягивается через
камеру промежуточной откачки и рабочую камеру. Камера промежуточной
откачки обеспечивает уменьшение давления до величины 1 – 20 кПа, которое
обеспечивается отдельным вакуумным насосом. Остальной газ откачивается из
рабочей камеры до давления 1 – 10 Па, при котором возможно горение
высоковольтного разряда. Для повышения эффективности удаления газа
используются газодинамические и электрофизические эффекты.
Для осуществления поставленной цели решены следующие задачи:
1) разработана методика анализа глубины залегания газа в материале.
Это минимизирует энергетические затраты на последующие операции удаления
газа и отжига материалов;
2) исследованы закономерности формирования защитных пленочных
покрытий в условиях натекания газа и ограниченном пространстве разлета
паров;
3) определены закономерности повышения эффективности удаления газа
для обеспечения вакуума при вводе электротехнических материалов из
атмосферы;
4) разработаны рекомендации по расчету и конструированию систем для
обработки длинномерных электротехнических материалов.
Научная новизна работы заключается в следующем:
1) Впервые показана связь потока газовыделения и скорости нагрева
материала с глубиной залегания газов в материале. Теоретически и
экспериментально обоснован метод оперативной диагностики глубины
локализации газов в металле.
2) Показано, что при термическом испарении материалов в проточных
системах (с откачкой и напуском газа) эффективность химического
взаимодействия паров распыляемого материала с парами окружающей
атмосферы существенно уменьшается по сравнению с формированием
пленочных покрытий в непроточных системах без напуска газа. Это
обусловлено уменьшением температуры в области взаимодействия газа с
испаряемым материалом за счет охлаждения поступающим потоком газа.
3) Установлены закономерности формирования покрытий в условиях
ограниченного пространства. Они заключаются в том, что при повышении
давления область однородности паров испаряемого материала смещается в
сторону источника. Необходимым условием получения покрытий с высокой
равномерностью и адгезией является нагрев испаряемого вещества до
температуры, при которой давление паров испаряемого металла превышает
давление остаточного газа.
4) Предложены критерии расчета взаимного расположения и выбора
формы элементов для ввода и вывода материала из атмосферы в вакуум, при
которых повышается эффективность удаления газа из системы поточной
обработки.
5) Впервые предложены электрофизические способы повышения
эффективности удаления газа из проточных систем обработки материалов.
6) Показано, что тлеющий разряд повышает равномерность конденсации
пара на подложке и оказывает частичное экранирующее действие на
конденсацию пара.
Теоретическая значимость работы заключается в установлении
закономерностей протекания процессов в проточных системах при обмене газа,
изменении геометрических размеров оборудования, давления или температуры.
Практическая значимость работы. Разработаны экспериментальные
устройства для поточной ионной очистки и отжига стальной электродной
проволоки, вольфрамовой проволоки для тел накала, молибденовой проволоки
для держателей тел накала; разработаны устройства для непрерывного
алюминирования рулонного фторопласта для конденсаторов. Разработаны
устройства для утилизации отходов фторопласта в порошок. Получены
практические рекомендации для конструирования систем с вводом материалов
из атмосферы в область пониженного давления.
Результаты работы могут найти применение в системах промышленного
нагрева, в строительстве, в научных исследованиях. Результаты работы
защищены 5 патентами.
Реализация работы. Результаты работы внедрены в ИФПМ СОРАН, в
ТУСУРе.
Методология и методы диссертационного исследования. Анализ
результатов проводился с привлечением математического моделирования
вакуумной техники, аппарата динамики газовых потоков для расчетов и оценки
совпадения экспериментальных и расчетных данных. Измерения толщины
пленок проводились на микроскопах МИИ-4, МИМ-7. Направление реакции
взаимодействия паров с остаточным газом оценивалось измерением давления
за время напыления. Оценка изменений в составе пленки проводилась по
измерению показателя преломления на эллипсометре ЛЭМ-2. В отдельных
случаях элементный состав покрытий исследовался на растровом сканирующем
микроскопе HITACI TM 3000. Визуализация потока пара и газа проводилась в
плазме тлеющего разряда. Потоки выделяющихся газов и их спектр
оценивались измерителем парциальных давлений ИПДО-1, с записью
интенсивности компонент спектра (кислород, азот, аргон, вода) на осциллограф
С8-17 с приставкой для расширения времени развертки.
Положения, выносимые на защиту
1. При нагреве электротехнического материала в форвакуумном диапазоне
давлений (1 – 10 Па) суммарное выделение газа из материала формируется
потоками газа с поверхностных и внутренних слоев. Относительный вклад этих
двух потоков зависит от скорости нагрева. Оценивая интенсивность суммарного
потока при разных скоростях нагрева, можно определить, на какой глубине
преимущественно располагается газ. Если с увеличением скорости нагрева
суммарный поток уменьшается, то это свидетельствует о смещении максимума
распределения концентрации сорбированных газов в глубь материала.
Информация о глубине залегания газа может использоваться для
минимизации энергетических затрат на удаление газов из материала за счет
оптимизации режимов нагрева.
2. При нанесении пленочных покрытий термическим испарением в
вакуумной камере в диапазоне форвакуумных давлений необходимым условием
получения тонкопленочных покрытий с высокой равномерностью и адгезией
является нагрев испаряемого вещества до температуры, при которой давление
паров испаряемого металла превышает давление остаточного газа. В этих
условиях в результате изменения механизма массопереноса от молекулярного
(при низких давлениях) к рассеянию на газе, область пространства
однородности паров смещается в сторону источника. В результате равномерные
по толщине пленочные покрытия формируются в условиях ограниченных
размеров рабочих камер вакуумных установок при повышенных давлениях
остаточного газа.
3. При формировании пленочных покрытий термическим испарением
металлов в проточных системах с напуском и откачкой газа происходит
снижение концентрации соединений элементов испаряемого материала с
компонентами рабочего газа по сравнению с непроточными системами. Это
связано с тем, что поступающий в камеру газ понижает температуру паров
материала, что приводит к снижению скорости реакции паров испаряемого
материала с компонентами рабочего газа. Изменяя поток газа, можно изменять
состав пленки от металлической до промежуточных соединений металлов с
компонентами рабочего газа.
4. В проточной вакуумной системе, содержащей последовательно
расположенные камеру для промежуточной откачки газа и рабочую камеру,
зажигание локального дугового или тлеющего разряда в камере промежуточной
откачки газа приводит к изменению вектора направленности потока газа из-за
его нагрева. Это приводит к уменьшению интенсивности поступающего в
рабочую камеру газового потока и позволяет снизить мощность, необходимую
для откачки газа из рабочей камеры.
Степень достоверности результатов диссертационной работы
подтверждается результатами, полученными с использованием независимых
дублирующих экспериментальных методик; проведением измерений на
различных экспериментальных установках; совпадением результатов
экспериментов с результатами теоретического моделирования, а также
сравнением полученных результатов с результатами других исследователей;
обсуждением основных положений работы на всероссийских и международных
конференциях и их публикациях в рецензируемых научных журналах;
практической реализацией научных положений и выводов при создании
конкретных устройств.
Личный вклад. Автор внес определяющий вклад в проведение
экспериментов, анализ полученных результатов и разработку конструкций
устройств. Соавторы, принимавшие участие в работе, указаны в списке
публикаций по теме диссертации. Все результаты, составляющие научную
новизну диссертации и выносимые на защиту, получены автором лично.
Апробация работы. Результаты работы доложены на международных
конференциях: 4, 5, 6, 7-я Международные конференции «Актуальные
проблемы электронного приборостроения» Новосибирск 1998, 2000, 2002;
Саратов 2000 г., «Конверсия науки – международному сотрудничеству», Томск,
1999; «Высоковольтная микроволновая электроника»: MIA-ME’99
Новосибирск, 1999 г.; «Измерения и контроль» (ИКИ-2000), Барнаул, 2000 г.;
«Интеллектуальные и природные ресурсы Сибири», Барнаул 2001;
Радиационная физика и химия РФХ-12, Томск, 2003; Химия твердого тела и
современные микро- и нанотехнологии, Кисловодск, 2008; «Радиационно-
термические эффекты и процессы в неорганических материалах 2008 г., 2014 г.
Томск; «Исследование, разработка и применение высоких технологий в
промышленности». С-Петербург 2010; «Энергосбережение, электромагнитная
совместимость и качество в электрических цепях». Пенза, ПДЗ, 2010;
материалы и технологии XXI века, Пенза, ПДЗ, 2004 г., 2015 г.
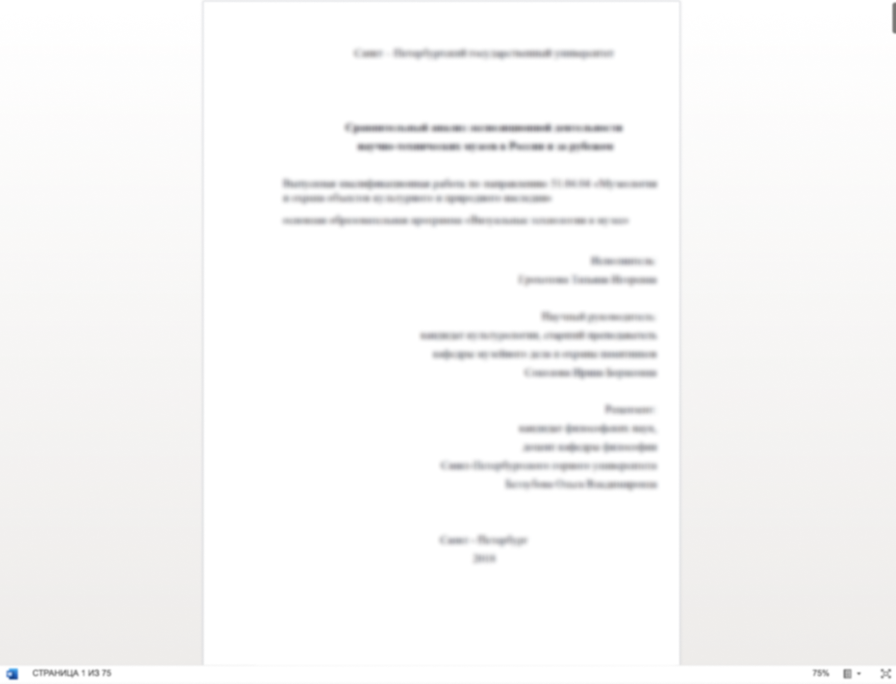
Помогаем с подготовкой сопроводительных документов
Хочешь уникальную работу?
Больше 3 000 экспертов уже готовы начать работу над твоим проектом!