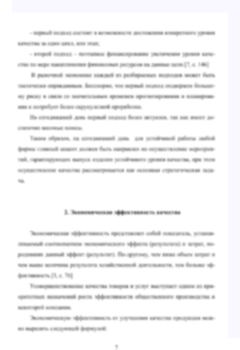
Нанесение медного покрытия на алюминиевые контактные поверхности плазмодинамическим методом
ВВЕДЕНИЕ………………………………………………………………………………………………. 4
ГЛАВА 1. АНАЛИЗ ВОЗМОЖНЫХ РЕШЕНИЙ ПРОБЛЕМЫ
СОВМЕЩЕНИЯ КОНТАКТНОЙ ПАРЫ МЕДЬ-АЛЮМИНИЙ ………….. 9
1.1 Электропроводящие смазки ………………………………………………………………… 10
1.2 Биметаллические прокладки ……………………………………………………………….. 12
1.3 Нанесение покрытий на алюминиевые контактные поверхности …………. 13
1.4 Прочие методы совмещения контактной пары медь-алюминий …………… 22
ГЛАВА 2. МЕТОДИКА ПРОВЕДЕНИЯ ИССЛЕДОВАНИЙ ……………….. 24
2.1 Экспериментальный стенд для проведения исследований по нанесению
медных покрытий на алюминиевые поверхности плазмодинамическим
методом …………………………………………………………………………………………………… 24
2.2 Принципиальная схема, устройство и работа коаксиального
магнитоплазменного ускорителя с медными электродами ………………………… 26
2.3 Регистрация энергетических параметров плазменного выстрела ………….. 30
2.4 Определение дифференциальных и интегральных характеристик
электроэрозионного износа медного ствола ускорителя ……………………………. 30
2.5 Регистрация динамических характеристик сверхзвуковой импульсной
струи медной электроэрозионной плазмы …………………………………………………. 31
2.6 Аналитические методы исследований …………………………………………………. 33
2.7 Методика определения переходного сопротивления контактных пар …… 34
ГЛАВА 3. ИССЛЕДОВАНИЕ ПРОЦЕССА НАНЕСЕНИЯ МЕДНОГО
ПОКРЫТИЯ НА АЛЮМИНИЕВЫЕ ПОВЕРХНОСТИ
ПЛАЗМОДИНАМИЧЕСКИМ МЕТОДОМ …………………………………………… 39
3.1 Инициирование дугового разряда в ускорительном канале коаксиального
магнитоплазменного ускорителя ………………………………………………………………. 40
3.2 Ускорение электроразрядной плазмы и исследование динамических
характеристик плазменной структуры ………………………………………………………. 45
3.3 Электроэрозионная наработка медного материала с поверхности
ускорительного канала …………………………………………………………………………….. 58
3.4 Исследование влияния параметров плазмодинамической системы на
величину площади медного покрытия ………………………………………………………. 66
3.5 Нанесение медного покрытия при двухимпульсном режиме работы
ускорителя ……………………………………………………………………………………………….. 74
ГЛАВА 4. ВЛИЯНИЕ ПАРАМЕТРОВ ПЛАЗМОДИНАМИЧЕСКОЙ
СИСТЕМЫ И ХАРАКТЕРИСТИК МЕДНОГО ПОКРЫТИЯ НА
ПЕРЕХОДНОЕ СОПРОТИВЛЕНИЕ КОНТАКТНОЙ ПАРЫ
МЕДЬ-АЛЮМИНИЙ …………………………………………………………………………….. 86
4.1 Исследования переходного сопротивления контактных пар ………………… 86
4.2 Микроструктура и фазовый состав медного покрытия на алюминиевой
подложке …………………………………………………………………………………………………. 95
4.3 Основные физико-механические свойства медного покрытия на
алюминиевой подложке ………………………………………………………………………….. 104
4.4 Прочность сцепления медного покрытия с алюминиевой подложкой … 109
4.5 Топология контактной поверхности медного покрытия …………………….. 112
4.6 Расчёт переходного сопротивления контактной пары медь-алюминий с
медным покрытием ………………………………………………………………………………… 118
ГЛАВА 5. НАНЕСЕНИЕ МЕДНОГО ПОКРЫТИЯ НА ВНУТРЕННИЕ
АЛЮМИНИЕВЫЕ КОНТАКТНЫЕ ПОВЕРХНОСТИ ……………………… 122
5.1 Реализация плазмодинамического метода нанесения медного покрытия на
внутреннюю поверхность конусных отверстий ……………………………………….. 123
5.2 Измерение и анализ переходного сопротивления контактной пары медь-
алюминий с медным покрытием конусной посадки ………………………………… 127
5.3 Микроструктура медного покрытия на внутренней поверхности
конусного отверстия, его элементный и фазовый состав, и механические
свойства …………………………………………………………………………………………………. 128
ЗАКЛЮЧЕНИЕ ……………………………………………………………………………………. 138
СОКРАЩЕНИЯ И УСЛОВНЫЕ ОБОЗНАЧЕНИЯ ……………………………. 140
СПИСОК ИСПОЛЬЗОВАННОЙ ЛИТЕРАТУРЫ ………………………………. 143
ПРИЛОЖЕНИЯ …………………………………………………………………………………… 157
Актуальность работы. Согласно статистическим данным потери
электрической энергии на контактных соединениях в электрических сетях
составляют до 10% от всей потребляемой электроэнергии. В условиях
развивающейся электроэнергетики снижение доли этой составляющей потерь
может дать ощутимый вклад в решение проблемы энергосбережения в целом.
Основными материалами токоведущих элементов в электрических сетях и
установках являются медь и алюминий. Как правило, из меди выполняются
вводы электроустановок, электрических машин и аппаратов, которые
соединяются с алюминиевыми проводами, шинопроводами и токопроводами
электрических сетей с помощью болтовых контактных соединений.
Известно, что контактная пара медь-алюминий (Cu-Al) характеризуется
относительно высоким переходным сопротивлением, в основном, из-за
образования на алюминиевой поверхности тонкой оксидной плёнки,
обладающей высоким удельным сопротивлением. Кроме того, контактные
соединения двух разнородных металлов Cu-Al представляют из себя
электрохимическую пару. Электрохимические процессы, активизируемые
протеканием токов силовой нагрузки, приводят к быстрой деградации
контактного перехода и повышению его сопротивления вплоть до полного
нарушения электрического контакта. Это, естественно, приводит к
значительному повышению джоулевых потерь энергии и возможности
возникновения аварийной ситуации. Поэтому проблема электрического
совмещения контактной пары Cu-Al и снижение её переходного
сопротивления до сих пор остаётся актуальной.
Существующие способы решения данной проблемы недостаточно
эффективны и имеют ряд недостатков. При использовании биметаллических
прокладок (Cu-Al) обеспечивается надёжное совмещение контактной пары,
но существенно увеличивается переходное сопротивление из-за появления
дополнительного переходного контакта алюминий-алюминий (Al-Al). При
длительной эксплуатации контактов с токопроводящими смазками на основе
меди их качество сильно ухудшается из-за высыхания и затвердевания
связующего. При ревизии соединений требуется очистка поверхностей и
нанесение нового слоя смазки. Традиционные электролитические и
газодинамические покрытия характеризуются плохой адгезией и низкой
устойчивостью к динамическим и термическим воздействиям, что
практически исключает их повторное использование.
В работе рассматривается новый плазмодинамический способ
нанесения медного покрытия на алюминиевые контактные поверхности с
помощью высоковольтного сильноточного коаксиального
магнитоплазменного ускорителя (КМПУ) эрозионного типа с медными
электродами и ускорительным каналом (УК). В отличие от существующих
способов он реализуется при атмосферном давлении и комнатной
температуре, обеспечивает нанесение устойчивого покрытия, отличается
экологичностью, не требует предварительной подготовки обрабатываемой
поверхности и дозированной подачи основного расходного материала.
Степень разработанности темы исследования. Различным аспектам
проблемы совмещения контактных элементов из меди и алюминия с низкой
величиной переходного сопротивления посвящено большое количество работ
отечественных и зарубежных ученых: R. Gravina, N. Pébère, A. Laurino, C.
Blanc, X.G. Wang, F.J. Yan, C.G. Wang, M. Winnicki, A. Małachowska, A.
Baszczuk, M. Rutkowska-Gorczyca, A. Ambroziak, Алхимов А. П., Косарев В.
Ф., Плохов А. В. и др. Несмотря на это, поиск эффективного решения
проблемы по-прежнему остаётся актуальным.
Цель диссертационной работы: разработка плазмодинамического
метода нанесения медного покрытия на алюминиевые поверхности на основе
В соответствии с целью работы проведены экспериментальные
исследования и разработаны научно-технические основы метода нанесения
медных покрытий на алюминиевые контактные поверхности различной
конфигурации с помощью высоковольтного сильноточного коаксиального
магнитоплазменного ускорителя эрозионного типа с медными электродами.
Основные результаты работы заключаются в следующем:
1. Разработан коаксиальный магнитоплазменный ускоритель с
оригинальной конструкцией ствола с медным ускорительным каналом и
способ инициирования в нём дугового разряда с помощью углеродной
разрушаемой перемычки. Определена оптимальная величина начального
сопротивления перемычки 300÷600 Ом, обеспечивающая минимальное время
безтоковой паузы между подачей напряжения и началом дуговой стадии
разряда.
2. Установлен характер влияния энергетических и конструктивных
параметров КМПУ на динамические характеристики сверхзвуковой струи
медной электроэрозионной плазмы в свободном пространстве в
одноимпульсном и двухимпульсном режимах работы плазмодинамической
системы.
3. Определены характер и основные закономерности влияния
параметров КМПУ на процесс электроэрозионной наработки материала с
поверхности ускорительного канала медного ствола для нанесения медного
покрытия на алюминиевые контактные поверхности.
4. Установлены закономерности влияния параметров
плазмодинамической системы на величину площади и качественные
характеристики медного покрытия.
5. Экспериментально показано, что плазмодинамическое медное
покрытие на алюминиевых контактных поверхностях обеспечивает снижение
переходного контактного сопротивления плоских и конусных контактных
пар до величин порядка 10-6÷10-7 Ом за счёт проявления специфических
особенностей: образования граничного слоя взаимного перемешивания
материалов покрытия (медь) и подложки (алюминий), обеспечивающего
высокопрочное сцепление покрытия с подложкой; образования слоёв из
высокотвёрдых синтезированных интерметаллидных фаз системы Cu-Al;
естественной шероховатости поверхности медного покрытия.
6. Предложен и реализован двухимпульсный режим работы КМПУ по
нанесению покрытий, обеспечивающий: снижение токов электропитания;
снижение электродинамических и термических нагрузок на ускоритель;
требуемую массу эродированного материала; нанесение качественного
медного покрытия с исключением эрозии на поверхности мишени.
7. В экспериментальных условиях получены медные покрытия на
контактных поверхностях стандартных алюминиевых шин и контактных
наконечниках, прошедших промышленные испытания.
Автор выражает признательность и благодарность своему научному
руководителю профессору ОЭЭ ИШЭ ТПУ, д.т.н. Александру Анатольевичу
Сивкову, а также коллективу научной группы «Лаборатория
магнитоплазменных технологий».
СОКРАЩЕНИЯ И УСЛОВНЫЕ ОБОЗНАЧЕНИЯ
КМПУ коаксиальный магнитоплазменный ускоритель;
УК ускорительный канал;
КФПС канал формирования плазменной структуры;
ЕНЭ емкостной накопитель энергии;
ЦЭ центральный электрод;
КР камера-реактор;
SEM сканирующая электронная микроскопия;
XRD рентгенофазовый анализ;
EDAX энергодисперсионный анализ;
ХГН холодное газодинамическое напыление;
СГП сверхглубокое проникание;
Cu-Al контактная пара медь-алюминий;
Cu-Cu контактная пара медь-медь;
Al-Al контактная пара алюминий-алюминий;
Cu-AlCu контактная пара медь-алюминий с медным покрытием;
CuAl-Al контактная пара алюминий медь с алюминиевым
покрытием;
AlCu-AlCu контактная пара алюминий-алюминий с медными
покрытиями;
С ёмкость накопителя энергии;
Uзар зарядное напряжение емкостного накопителя энергии;
Wс накопленная энергия емкостного накопителя энергии;
Р0 атмосферное давление в камере-реакторе;
dУК диаметра ускорительного канала;
ℓУК длина ускорительного канала;
VУК объём ускорительного канала;
ℓст-м расстояние от среза ускорительного канала до
алюминиевой мишени;
υс скорость плазменной струи на срезе ускорительного
канала;
I(t) осциллограмма импульсного тока электропитания;
U(t) осциллограмма напряжения на электродах ускорителя;
P(t) кривая мощности разряда во времени;
W(t) кривая изменения подведённой энергии во времени;
Im амплитуда импульсного тока электропитания;
Um амплитуда напряжения на электродах;
Pm максимальная мощность разряда;
W подведённая энергия;
Pср средняя мощность разряда;
Рср100 средняя мощность разряда на интервале 100 мкс;
tимп время импульса;
t1 момент запуска управляемых разрядников (начало
работы ускорителя);
tз момент задержки подачи второго импульса
относительно начала первого;
tп время безтоковой паузы между первым и вторым
импульсом;
η эффективность передачи энергии из накопителя в
нагрузку;
Δm величина удельного дифференциального износа;
m масса медного материала, эродированная с
поверхности ускорительного канала;
W/VУК удельной подведённой энергии на единицу объёма
ускорительного канала;
m/W удельная электроэрозионная наработка медного
материала;
Rк переходное контактное сопротивление;
Rш сопротивление шунта;
RП переходное сопротивление между медным покрытием
и алюминиевой подложкой;
R0 сопротивление углеродной перемычки;
S площадь, нанесённого медного покрытия;
Sк площадь контактной поверхности;
Н(х) эпюра твёрдости материала;
Е(х) эпюра модуля упругости материала;
Fтр сила трения;
Fн нормальная сила нагружения;
Fсц сила сцепления покрытия с подложкой;
Рсц прочность сцепления покрытия с подложкой;
Ае акустическая эмиссия;
D ширина царапины от индентора;
Rа средняя шероховатость профиля;
Sa средний шаг неровностей профиля;
hmax максимальная высота пиков поверхности профиля;
hср средняя высота пиков поверхности профиля;
δ толщина покрытия.
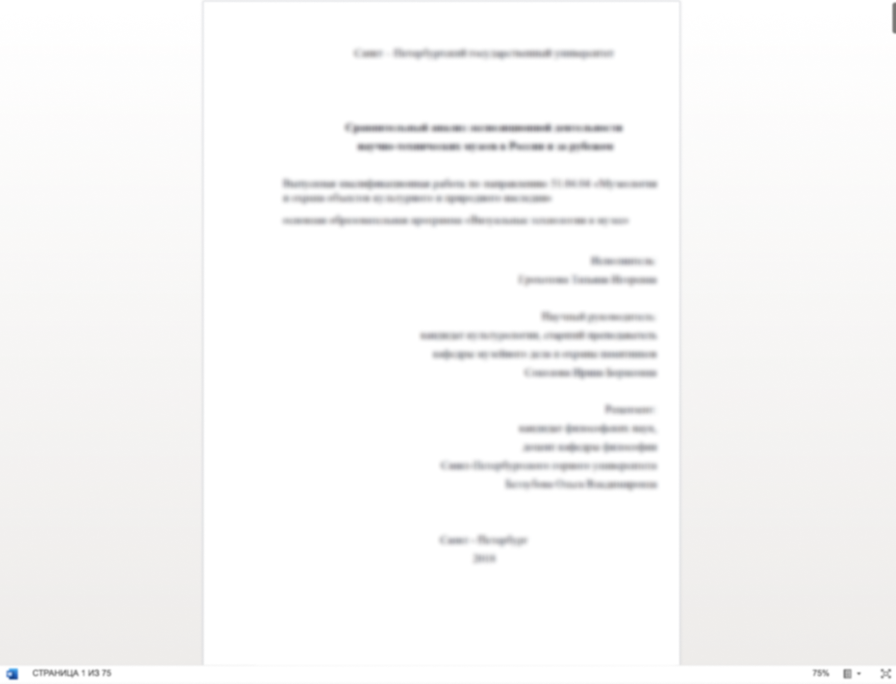
Помогаем с подготовкой сопроводительных документов
Хочешь уникальную работу?
Больше 3 000 экспертов уже готовы начать работу над твоим проектом!