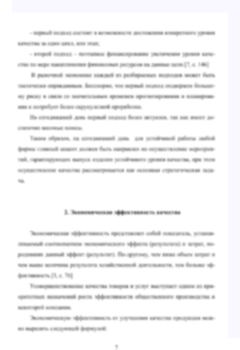
Обеспечение заданной шероховатости при высокоскоростном фрезеровании деталей из алюминиевых сплавов с учетом дисбаланса инструментальных наладок
Содержание
ВВЕДЕНИЕ
1 Литературный обзор, постановка цели и задач исследования
1.1 Высокопроизводительное фрезерование авиационных деталей из алюминиевых сплавов
1.2 Особенности высокопроизводительной обработки (HPC)
1.3 Особенности высокоскоростной обработки (HSC)
1.4 Конструктивные особенности деталей, изготавливаемых из алюминиевых сплавов
1.5 Анализ процесса балансировки инструмента
1.5.1 Общие сведения
1.5.2 Понятие дисбаланса
1.5.3 Неразрушающие методы балансировки инструментальных наладок
1.5.4 Разрушающие методы балансировки инструментальных наладок
1.5.5 Анализ требований инструментальных наладок
1.5.6 Сравнение действующих стандартов на балансировку
1.6 Выходные показатели фрезерования
1.6.1 Качество поверхности
1.6.2 Вибрации
1.7 Основные выводы, постановка цели и задач исследования
2 Математическое моделирование процесса концевого фрезерования
2.1 Стратегии обеспечения стабильного процесса обработки
2.2 Описание математической модели
2.3 Алгоритм формирования обработанной поверхности
2.4 Выводы по второй главе
3
3 Экспериментальная оценка влияния остаточного дисбаланса инструментальной наладки на качество обработанной поверхности детали.
3.1 Измерение остаточного дисбаланса инструментальной наладки на базе корпусной фрезы R790-032C5S2-16M
3.2 Измерение остаточного дисбаланса инструментальной наладки с концевой твердосплавной фрезой AZ-3D16R6L65
3.3 Результаты сборки и балансировки инструментальных наладок
3.4 Определение режимов резания
3.4.1 Проведение модального анализа для исследуемых инструментальных
наладок
3.5 Результаты испытаний корпусной фрезы R790-032C5S2-16M
3.5.1 Обобщение результатов, построение зависимостей
3.6 Результаты испытаний фрезы AZ-3D16R6L65, припуск 0,3 мм
3.6.1 Обобщение результатов, построение зависимостей
3.7 Результаты испытаний фрезы AZ-3D16R6L65, припуск 0,5 мм
3.7.1 Обобщение результатов, построение зависимостей
3.8 Выводы по третьей главе
4 Теоретико-вероятностный подход для вывода эмпирической зависимости шероховатости обработанной поверхности от величины остаточного дисбаланса инструментальной наладки
4.1 Вывод эмпирической зависимости
4.2 Анализ корректности работы математической модели
4.3 Множественный регрессионный анализ и построение поверхностей отклика
4.4 Технологические рекомендации
4.4.1 Основные положения
4.4.2 Требования, предъявляемые к режущему инструменту и системе крепления
4.4.3 Требования, предъявляемые к измерительному оборудованию
4.4.4 Особенности балансировки инструментальных наладок
4.5 Выводы по четвертой главе
ЗАКЛЮЧЕНИЕ
СПИСОК ЛИТЕРАТУРЫ
Приложение А
Приложение Б
Приложение В
Приложение Г
Во введении дана краткая характеристика состояния проблемы, обоснована актуальность выполненной работы, определена цель и поставлены задачи иссле- дования, сформулированы научная новизна и практическая значимость работы.
В первой главе приведены конструктивные особенности рассматриваемых деталей и анализ их геометрической формы. Проанализированы технологиче- ские факторы, оказывающие влияние на качество получаемой после концевого фрезерования поверхности. Проанализированы основные положения теории и методик расчета технологических параметров процесса концевого фрезерования и процесса балансировки инструментальных наладок.
Анализ исследований, представленных в научно-технической литературе, нормативно-технических материалах. Влияние вибраций на шероховатость по- верхности и режимы резания исследовались Жарковым И.Г., Кашириным А.И., Петрухиным В.В., Потаповым В.А. Повышение эффективности чистового фре- зерования, обеспечение точности обработки и методы демпфирования колеба- ний исследовались Кирющенко Е.В., Малютиным Г.Е., Кузнецовым С.Ф.
Результаты исследований в области моделирования динамики процесса фрезерования наиболее полно раскрыты в работах Киселева И.А., Гуськова А.М., Воронова С.А., Огневенко Е.С., Дуюн Т.А., Дерябина И.П., Сергеева С.В., Галловэя Д.Ф.(D.F. Galloway), Эма С. (S. Ema), Дж. Ц. Рукема (Roukema J.C.), М. Пиртини (Pirtini M.), Ю. Алтинтаса (Altintas Y.), K. Ахмади (Ahmadi K.).
Методики расчета и измерения точности балансировки на основе величины остаточного дисбаланса инструментальных наладок приведены в международ- ных стандартах ISO/FDIS 1940-1:2002(E) и DIN 69888:2008-09.
Формирование поверхности в результате концевого фрезерования пред- ставляет собой сложный процесс, определяемый геометрическими параметрами инструмента, вибрационными характеристиками и режимами резания.
Анализ публикаций показал, что обеспечение наилучшего качества поверх- ности с сохранением высокой производительности процесса обработки возмож- но с использованием методов математического моделирования.
Требования для инструментальных наладок должны рассчитываться исходя из обусловленных дисбалансом нагрузок на подшипниковые опоры шпинделя. Расчет должен учитывать, чтобы остаточный дисбаланс наладки в составе шпинделя не оказывал значительного влияния на технологический процесс.
Анализ нормативных документов, регламентирующих процесс балансиров- ки, показал, что резонанс с собственными частотами – параметр, специфичный для конкретной комбинации инструмента и конструктивных элементов металло- режущего оборудования и, следовательно, его влияние не поддается учету. Нор- мируемым параметром может являться непосредственно величина дисбаланса U,
г×мм. Также не имеет смысла сопоставлять данный параметр с классами балан- сировки по ISO 1940-1, поскольку масса инструмента не оказывает влияние на динамические нагрузки несбалансированной инструментальной наладки.
Таким образом, на основании анализа литературных источников и дей- ствующих нормативных документов были сформулированы цель и задачи дис- сертационного исследования.
Вторая глава посвящена математическому моделированию процесса кон- цевого фрезерования. В рамках представленной работы математическое модели- рование сводится к расчету мгновенного значения толщины срезаемого слоя зу- бом фрезы и построению микропрофиля обработанной поверхности с учетом остаточного дисбаланса инструментальной наладки.
Основываясь на положениях работ Minis L., Yanushevsky R., Tembo A., процесс концевого фрезерования рассматривается как система 2-я степенями свободы в системе координат X-Y (рисунок 1).
Рисунок 1 – Система с 2-я степенями свободы Динамика процесса описывается двумя уравнениями:
̈ + ̇ + = ∑ −1 (1) 1 1 1 =0
̈+ ̇+ =∑ −1 , (2) 2 2 2 =0
где m1, b1, k1, m2, b2 и k2 – модальные параметры инструмента;
Fxt и Fyt – компоненты силы резания, которая действует на i-ый зуб фрезы; n – число зубьев фрезы.
Исходя из рисунка 1 Ui и Vi выступают в качестве поворотных осей, благо- даря которым мы можем определять мгновенное положения i-ого зуба фрезы, что дает нам возможность рассматривать каждый зуб как отдельный резец, соот- ветственно полученные в дальнейшем уравнения могут быть, теоретически, ис- пользованы и для точения.
Угол определяет положение локальной системы координат Ui -Vi относи- тельно системы координат X-Y. Данный прием позволяет нам определить пери- од врезания и выхода зуба из материала = 2 / .
= + 2 = ( + ), =0,1,…, −1, (3)
где – угловая скорость вращения зуба фрезы.
вид:
толщина срезаемого слоя f будет определяться по формуле:
Соответственно матрица, связывающая обе системы координат, принимает
= ( ( + ) ( + )) (4) − ( + ) ( + )
= = ( + ), (5)
где – подача на зуб.
Рассматривая процесс изменения и формирования срезаемой поверхности
(рисунок 2), необходимо ввести 2 новых параметра, а именно:
1 – модуляция срезаемого слоя обрабатываемой поверхности , параметр
определяется по нормали к этой поверхности и представляет собой отклонение i- ого зуба от траектории, по которой он бы прошел, без приложения к нему како- го-либо усилия;
2 – параметр 0, определяющий траекторию движения предыдущего зуба.
Данный подход позволяет нам учесть 2 простейших случая, возникающих во время обработки:
случай No1 – i-ый зуб находится в контакте с обрабатываемой поверхно-
стью;
− 0 + 0> 0
= −h ( )[ ( − + ) + ̇ ] (6)
= −h (θ )[ ( − 0 + θ ) + ̇ ],
где h – глубина резания ap, kd и bd – коэффициенты определяющие показатели жесткости и демпфирования, (θ ) – функция, определяющая ненулевое значе- ние составляющей силы резания.
( ) = 1 при 2 + 1 ≤ ≤ 2 + 2 = 0, 1 …, а в других случаях ( ) = 0;
случай No2 – i-ый зуб потерял контакт с поверхностью;
− 0 + < 0 (7)
= =0
Рисунок 2 – Траектория движения i-ого зуба
Для связи величины остаточного дисбаланса с шероховатостью Ra обра- ботанной поверхности и построения её профилограммы в математической моде- ли учтено воздействие тангенциальной составляющей силы резания на зуб фре- зы, которое вызвано несбалансированностью массы инструментальной наладки. Для этого в уравнение расчета тангенциальной силы резания введен коэффици-
ент , рассчитываемый исходя из результатов балансировки. Уравнение тан- генциальной силы резания приняло следующий вид:
, ( , ) = [ ∙ h ( ( )) + + ] (8) = ∙ ∙ 2= ∙( )2, (9)
где Ktc , Kte – постоянные коэффициенты тангенциальной силы резания; Krc , Kre –
постоянные коэффициенты нормальной силы резания; dz – дискретный шаг по
оси инструмента, ( )−текущий угол режущей кромки j, относительно оси
инструмента (j=1, ... ,k), k – число режущих кромок; − несбалансированная
масса; расстояние от оси инструмента до этой массы; – остаточный дисба-
ланс; 9549 – эмпирический коэффициент, связывающий рабочую частоту вра- щения инструмента с его угловой скоростью.
В случае моделирования процесса концевого фрезерования, математиче- ская модель, в зависимости от сложности может учитывать ряд механизмов воз- буждения вибраций, возникающих при обработке резанием. Анализ публикаций авторов Minis L., Yanushevsky R., Tembo A., Balachandran B., Zhao M.X. Cam- pomanes M.L., Altintas Y. показал, что основным является механизм запаздыва- ния – возникновение автоколебаний при «резании по следу».
Для реализации механизма запаздывания в работе применен метод «Ими- тационного моделирования». Он заключается в численном интегрировании уравнения движения системы. Для этого применяется алгоритм геометрического моделирования с определением мгновенных значений толщины срезаемого слоя с учетом запаздывания. Это возможно благодаря сохранению истории формиро- вания поверхности.
Запаздывание в системе образуется за счет регенерации поверхности. Что- бы исключить ошибку при формировании обработанной поверхности необходи- мо учитывать моменты, когда происходит врезание и выход инструмента из ма- териала. Для этого в алгоритме перед расчетом толщины срезаемого слоя и сил резания происходит учет взаимного положения режущих кромок и поверхности детали, проверяя тем самым, находился ли зуб фрезы в металле или нет.
При моделировании процесса концевого фрезерования расчет упругих пе- ремещений инструмента производился для момента вхождения зуба фрезы в за- готовку (с учетом заданных параметров демпфирования, жесткости и дисбалан- са) при формировании обработанной поверхности. При этом по вновь сформи- рованной поверхности было принято, что проходит следующий зуб. Подобный подход позволяет учесть переменную толщину срезаемого слоя, а, следователь- но, и смоделировать регенеративные вибрации при резании. На основе получен- ных на выходе координат точек обработанной поверхности строится её микро- профиль и определяются требуемые параметры шероховатости (Рисунок 3).
Разработанная математическая модель реализована на языке MATLab. Ре- зультаты расчетов позволяют построить профилограмму обработанной поверх- ности (рисунок 3), которую можно сравнить и сопоставить с полученной экспе- риментально (рисунок 4).
9549
Рисунок 3 – Микропрофиль поверхности при моделировании
Рисунок 4 – Микропрофиль поверхности при эксперименте
Сравнение расчетных и экспериментальных данных (рисунок 5), с учетом особенностей представления результатов моделирования программой, проводи- лось по наибольшей высоте неровностей профиля Rmax.
Рисунок 5 – Сравнение результатов моделирования
3,5 3 2,5 2 1,5 1 0,5 0
3,3
3,1
2,5
2,9
2,3
0,8 5,3
8,6 16,1
27,4 36,7
1,1
1,5 1,4 1,6 1,4
1,8
2,1
Точность балансировки G, мм/с
Rmax, мкм
Эксперимент Модель
В третьей главе приведены результаты экспериментальной оценки влия- ния величины дисбаланса инструментальной наладки на шероховатость обрабо- танной поверхности детали.
Эксперимент заключался в продольном фрезеровании уступов в заготовке 800 x 400 x 80 мм из высокопрочного алюминиевого сплава 1933 с варьировани- ем величины остаточного дисбаланса инструментальной наладки при фиксиро- ванных режимах резания.
За основу были приняты режимы, рекомендуемые справочной литературой, а также используемые на практике. В дальнейшем для выбора режимов резания было принято решение воспользоваться методом модального анализа и прово- дить эксперимент согласно его результатам (рисунок 7). Скорректированные режимы резания указаны в таблице 1.
Таблица 1 – Режимы резания по результатам модального анализа
Инструмент
24
12120 2029 20200
0,2
0,5
3600 754 15000
0,08
R790-032C5S2-16M 7 AZ-3D16R6L65 20
В эксперименте участвовали 2 инструментальные наладки (рисунок 6).
аб
Рисунок 6 – Исследуемый инструмент: а – корпусная фреза R790-032C5S2-16M; б –фреза AZ-3D16R6L65
Наладка No1 – корпусная фреза со сменными твердосплавными пластинами (рисунок 6, а). Инструментальная наладка включает в себя элементы системы Capto C5: базовый держатель C5 для инструментального конуса HSK-63A с втулкой для внутреннего подвода СОЖ и фрезу R790-032C5S2-16M со сменны- ми твердосплавными пластинами R790-160408PH-NM H13A.
Глубина резания ap, мм
Ширина резания ae, мм
Минутная подача Vf, мм/мин
Окружная скорость резания vc, м/мин
Частота вращения шпинделя n, мин-1
Подача fz, мм/зуб
Наладка No2 – модульная инструментальная наладка включает в себя эле- менты системы Capto C5: базовый держатель C5 для инструментального конуса HSK-63A с втулкой для внутреннего подвода СОЖ и адаптер на базе гидравли- ческого патрона CoroGrip, а также переходную цангу с внешним и внутренним диаметрами равными 20 и 16 мм соответственно, а также цельную твердосплав- ную фрезу AZ-3D16R6L65 (рисунок 6, б).
аб
Рисунок 7 – График областей стабильного резания: а – для цельной твердосплав- ной фрезы; б – для корпусной фрезы
В области I на рисунке 7 обозначены режимы, реализация которых на прак- тике невозможна в силу ограничения частоты вращения шпинделя станка (28000 мин-1), а также максимальной глубины резания, равной длине зуба фрезы (20 мм для AZ-3D16R6L65 и 12 мм для R790-032C5S2-16M). Для фрезы R790-032C5S2- 16M на рисунке 7, б дополнительно указана область III, при работе в которой будут превышены рекомендации производителя на максимальную скорость ре- зания для данных пластин (635 м/мин).
На рисунках 8 и 9 представлены результаты проведенного эксперимента.
аб
Рисунок 8 – Результаты эксперимента для наладки No1: а – зависимость парамет- ра шероховатости Ra обрабатываемой поверхности от точности балансировки инструментальной наладки; б – зависимость сил резания от точности баланси- ровки инструментальной наладки
700 600 500 400 300 200 100 Px
G8,4 G16,7 G21,7 G29,4 G37,4
Py
Pz
P, H
50
40 Px 30
10
G5,3 G8,6 G16,1 G27,4 G36,7
Py
Pz
0,6 0,5 0,4 0,3 0,2 0,1
G5,3 G8,6 G16,1 G27,4 G36,7
аб
Рисунок 9 – Результаты эксперимента для наладки No2: а – зависимость парамет- ра шероховатости Ra обрабатываемой поверхности от точности балансировки инструментальной наладки; б – зависимость сил резания от точности баланси- ровки инструментальной наладки
Для наладки No1 дисбаланс варьировался при помощи балансировочных колец. Для наладки No2 дисбаланс варьировался разрушающим методом – «вы- сверливанием».
Серьезное влияние на качество балансировки до классов выше G5.0 оказы- вает чистота посадочных поверхностей наладки и адаптера и инструментальной наладки в целом.
Проведен модальный анализ для 2-х инструментальных наладок с цельным твердосплавным инструментом и сборной фрезой. Определены зоны стабильно- го резания.
С увеличением остаточного дисбаланса в пределах от 0,8 до 55,1 г×мм ше- роховатость обработанных поверхностей изменялась в диапазоне 0,42 – 0,56 мкм. Ra поверхности соответствовало поверхности после чистового фрезерова- ния.
В четвертой главе приведены результаты экспериментальных исследова- ний, нацеленных на проверку корректности работы математической модели, а также на определение и формулировку основных рекомендаций по балансировке инструментальных наладок при скоростном фрезеровании. Определялась реаль- ная зависимость шероховатости обработанной поверхности от точности балан- сировки инструментальной наладки, состоящей из 3-х зубой концевой твердо- сплавной фрезы диаметром 16 мм и термоусадочного патрона Haimer A63.140.16, выполненного под инструментальную систему HSK (рисунок 10, а). Выбор данного патрона обусловлен его высокой точностью, радиальное биение составляет 0,006 мкм, а также возможностью производить балансировку ин- струментальной оснастки при помощи балансировочных винтов. Данное реше- ние позволяет варьировать величину остаточного дисбаланса в пределах рабоче- го диапазона, не прибегая к разрушающим методам балансировки.
Ra, мкм
P, H
аб
Рисунок 10 – Проведение эксперимента: а – исследуемая инструментальная
наладка, закрепленная в шпинделе станка; б – рабочая зона станка HSC75V linear
Исследование проводилось по дробному 4-х факторному плану «Бокса- Бенкена» с 3 уровнями (таблица 2).
Таблица 2 – Уровни факторов
Uост, г×мм ximax +1 14,7
xmin –1 3,7 0,05 2 1
В качестве исследуемого фактора для оценки влияния точности баланси- ровки на шероховатость получаемой поверхности была выбрана величина оста- точного дисбаланса инструментальной наладки. Данный параметр универсален и позволяет определить качество балансировки инструмента вне зависимости от используемого стандарта.
Эксперимент заключался в продольном фрезеровании уступов в заготовке 250 x 80 x 80 мм из высокопрочного алюминиевого сплава 1933. Дисбаланс ва- рьировался при помощи балансировочных винтов. Измерение сил и контроль вибраций проводились при попутном фрезеровании (рисунок 10, б). За основу были взяты режимы резания, используемые на практике с учетом рекомендаций справочной литературы. В последствие они были скорректированы по результа- там проведенного модального анализа (таблица 3).
Таблица 3 – Режимы резания
16 3 1256 10 2 25000 0,15 11250 Верхний уровень Uост соответствует максимально допустимому дисбалансу для вращающегося инструмента. Нижний уровень Uост соответствует минималь-
Уровень фактора
Факторы fz, мм/зуб
ae, мм 10
ap, мм 2
0,15
xi0 0 8,9 0,10 6 1,5
Dc ,
мм
z
Vc , м/мин
ae , мм
ap , мм
n,
мин-1
fz ,
мм/зуб
Vf, мм/мин
ной величине дисбаланса. На рисунке 11 представлена стружка и обработанная поверхность.
аб
Рисунок 11 – Результаты проведения экспериментов: а – получаемая стружка; б – обработанная поверхность
Используя пакет программ Statistica, были проведены расчеты для получе- ния эмпирической зависимости шероховатости обработанной поверхности от исследуемых факторов процесса концевого фрезерования:
Ra e117.096U
2.632 0.715 ln(ae ) 0.893 ln( f z )
34.831 2.657ln( U
0.8960.512ln(f ) z
) fz0.859ap
Поверхности отклика, представленные на рисунке 12, выполнены в про-
аб
в
Рисунок 12 – Поверхности отклика шероховатости обработанной поверхности от остаточного дисбаланса: а – зависимость параметра Ra от Uост и ae; б – зависи- мость параметра Ra от Uост и ap; зависимость параметра Ra от Uост и fz.
ост
ae ; грамме Statistica.
ост
(10)
Согласно положениям, представленным в работах Адлера Ю.П., Маркова Е.В., Грановской Ю.В. расчетная модель может считаться адекватной при значе- нии коэффициента уровня значимости «p» 0,05, а также коэффициенте детер- минации «R» 0,3, т.е. изменение отклика происходит под воздействием пред- ставленных в модели факторов. Данные коэффициенты показывают долю изме- няемости отклика, происходящую под одновременным воздействием всех фак- торов. Другими словами, результаты регрессионного анализа говорят об адек- ватном подборе факторов, а также о целесообразности прогнозов по данной мо- дели.
ЗАКЛЮЧЕНИЕ
В диссертационной работе на основе проведенных исследований обоснова- на возможность повышения качества поверхностного слоя и эффективности подготовки производства, процесса высокоскоростного фрезерования деталей из высокопрочных алюминиевых сплавов за счет снижения трудоемкости баланси- ровки инструментальных наладок, обеспечивающей заданные параметры шеро- ховатости обработанных поверхностей.
Логическим продолжением исследований по данной тематике может быть расширение используемых схем обработки торцевым и плунжерным фрезерова- нием.
В ходе исследований получены следующие научные и практические ре- зультаты.
1. Методика устранения дисбаланса, разработанная на основе технологиче- ских рекомендаций по балансировке инструментальных наладок, обеспечиваю- щая заданную шероховатость поверхности, позволит сократить время на подго- товку инструмента в 2-3 раза, а также снизить трудоемкость работ по подготовке инструментальных наладок с одновременным обеспечением заданной шерохова- тости поверхности деталей без снижения производительности процесса фрезеро- вания, стойкости инструмента и ресурса дорогостоящего оборудования.
2. Выполнена оценка влияния точности балансировки инструментальной наладки на шероховатость обработанной поверхности детали при концевом фре- зеровании.
3. Эмпирическая зависимость, выведенная на основе экспериментальных исследований, даёт возможность оценить влияние остаточного дисбаланса ин- струментальной наладки и режимов резания на параметр шероховатости Ra об- работанной поверхности деталей из высокопрочных алюминиевых сплавов при высокоскоростном фрезеровании.
4. На основе анализа существующих математических моделей и механиз- мов возбуждения вибраций при моделировании процесса фрезерования разрабо- танный алгоритм расчета мгновенного значения толщины срезаемого слоя и формирования микропрофиля обработанной поверхности при концевом фрезе- ровании позволяет учитывать остаточный дисбаланс и вибрационные характери- стики инструментальной наладки, модальную жесткость технологической си- стемы, геометрические параметры режущего инструмента. В основе разработан- ного алгоритма лежит механизм запаздывания. Запаздывание в системе образу-
ется за счет регенерации поверхности.
5. Проведенные исследования позволяют сделать вывод, что требования
стандарта DIN 69888 к качеству балансировки вращающегося инструмента обоснованы. Рекомендуется руководствоваться ими и отказаться от практики оценки качества балансировки параметром G. При оценке точности балансиров- ки инструментальной наладки следует руководствоваться допустимой величи- ной остаточного дисбаланса.
6. Ужесточение требований к остаточному дисбалансу инструментальных наладок приводит к высоким затратам на подготовку производства. При средней продолжительности процесса балансировки в 10 минут время проведения опера- ций для соблюдения требования дисбаланса в 1 г×мм может возрастать до 2,5-3 раз. С учетом эксцентриситета шпинделей станков e = 2,5 мкм, достижение по- добных требований не имеет смысла. В случаях, требующих проверки качества балансировки инструментальной наладки, следует руководствоваться требова- ниями стандарта DIN 69888 взамен действующего ISO 1940-1. Действующий же стандарт ISO 1940-1 в практике механообработки рекомендуется использовать только для балансировки инструментальных наладок в составе шпинделя станка.
7. При анализе вибраций, вызванных остаточным дисбалансом инструмен- тальной наладки, рекомендуется пользоваться встроенными средствами фрезер- ного обрабатывающего центра для контроля вибрационного состояния опор шпинделя.
Актуальность темы исследования. Повышение эффективности технологи-
ческих процессов механической обработки на основе применения современных металлообрабатывающих станков и комплексов, переход на прогрессивные тех- нологии обработки, повышение качества выпускаемой продукции являются глав- ными задачами современного машиностроительного производства. Актуальность темы исследования обусловлена следующим:
1. Практика показывает, что при высокоскоростном концевом фрезеровании повышение качества детали с заданным уровнем параметров шероховатости по- верхности можно достичь только при условии учета влияния остаточного дисба- ланса инструментальной наладки на процесс формообразования. Обоснованное назначение допустимого дисбаланса при концевом фрезеровании позволяет не только получать детали с высоким качеством поверхности, но и сократить цикл их производства за счет исключения последующей чистовой обработки и дово- дочных работ, а, следовательно, и снизить себестоимость изделий, обеспечив ста- бильную работу технологической системы.
2. Требования рекомендаций зарубежных и отечественных компаний, по- ставляющих предприятиям оборудование, инструмент и станочную оснастку, к допустимому уровню дисбаланса инструментальных наладок, как правило, не- обоснованно завышены, что приводит к увеличению затрат на подготовку произ- водства. Эти рекомендации базируются на стандартах, регламентирующих балан- сировку жёстких роторов, что не в полной мере учитывает особенности инстру- ментальных наладок, используемых при высокоскоростном фрезеровании, и не позволяет установить связь результатов балансировки с технологическими по- следствиями получения поверхностей деталей с заданной шероховатостью.
Требуемого качества изделий можно добиться за счет применения рекомен- даций по ограничению уровней балансировки инструментальных наладок, разра- ботанных на основе теоретических и экспериментальных исследований влияния остаточного дисбаланса на шероховатость поверхности при фрезеровании. Именно изучению влияния дисбаланса инструментальных наладок на фор- мирование микрогеометрии поверхностей деталей из высокопрочных алюминие- вых сплавов, разработке на основе исследований математической модели процес- са концевого фрезерования посвящена представляемая к защите диссертационная работа. Использование полученных результатов позволит по заданным конструк- торской документацией параметрам микрогеометрии поверхностного слоя уста- навливать допустимые пределы дисбаланса инструментальных наладок и опреде- лять максимально допустимые режимы обработки деталей из высокопрочных алюминиевых сплавов на высокоскоростном технологическом оборудовании, а также снизить трудоемкость подготовительных работ в механообработке и повы- сить производительность процесса концевого фрезерования при сохранении стой- кости инструмента и ресурса дорогостоящего оборудования.
Степень разработанности проблемы. Современное металлорежущее обо- рудование работает в условиях увеличивающихся скоростей и динамических нагрузок, приводящих к колебаниям в технологической системе, что негативно сказывается на качестве поверхностей деталей, получаемых после обработки. Од- ним из путей, направленных на повышение качества, считается снижение влияния вибраций, которые являются неизменным спутником любого процесса механиче- ской обработки, в частности – фрезерования. В работах [49,63,64,92,93] авторами исследуется процесс фрезерования с применением концевого твердосплавного инструмента. Выделяют три основные группы вибраций в зависимости от источ- ника.
Первая группа – вибрации сочлененной технической системы, связанные с наличием соединений и кинематических связей между элементами этой системы, такими как станок, приспособление, инструмент, деталь.
Вторая группа – термомеханические вибрации, возникающие в зоне резания и связанные с температурными деформациями заготовки, стружки и режущей ча- сти инструмента. В работах [78,79,90] авторы рассматривают влияние нагрева на структуру, свойства инструментальных материалов и остаточные напряжения в режущей кромке инструмента. Третья группа – это регенеративные вибрации. При фрезеровании каждый зуб фрезы, совершая колебания, оставляет за собой волнистую поверхность на за- готовке. Каждый последующий зуб срезает слой заготовки переменной толщины, что в свою очередь приводит к осцилляциям силы резания и появлению регенера- тивных вибраций [95,96,97].
При фрезеровании деталей из высокопрочных алюминиевых сплавов на со- временном оборудовании влияние вибраций возрастает, так как обработка ведётся на высоких скоростях. С увеличением рабочих частот вращения инструмента, в частности концевых фрез, ужесточаются требования к балансировке инструмента [55,58]. Повышенные требования к дисбалансу шпинделя станка, инструменталь- ной оснастки и собственно самого инструмента существенно усложняют и замед- ляют процесс проведения подготовительных операций и не гарантируют качество получаемых деталей. Как следствие, это может привести к увеличению парка вспомогательного оборудования на предприятии, численности персонала для ра- боты и его обслуживания, что, в конечном счете, сказывается на себестоимости продукции.
Нельзя однозначно сделать заключение о том, какой тип вибраций оказывает решающее воздействие на процесс резания – это зависит от типа и условий обра- ботки конкретной детали и требует тщательного анализа. Свести к минимуму вибрации, относящиеся к первой группе и связанные непосредственно с функцио- нированием механической системы станка можно при помощи балансировки шпинделя в целом. По объективным причинам балансировка шпинделя выполня- ется по частям: мотор-шпиндель в составе станка балансируется заводом- изготовителем, а инструментальная наладка – пользователем.
Балансировка осевого инструмента – сравнительно новая практическая про- блема в машиностроении. Несмотря на общую тривиальность процесса, многие моменты этого процесса до сих пор не ясны. В частности, нет единого мнения о том, какими требованиями и нормативными документами следует руководство- ваться при балансировке инструмента, в какой степени влияет остаточный дисба- ланс инструментальной наладки на качество обработки, насколько хорошо дол- жен быть отбалансирован конкретный инструмент для выполнения тех или иных задач.
Исходя из опыта изготовления и проведения входного контроля инструмен- тальных патронов, используемых при высокоскоростной обработке, на многих предприятиях исполнители сталкиваются с проблемой оценки рационального и реального качества балансировки. Причина проблемы основана на противоречии между качеством балансировки, указываемом изготовителем в протоколе прием- ки, и измеренном потребителем при входном контроле. На предприятиях возника- ет вопрос, насколько необходимо выполнять требование спецификаций качества балансировки G2,5 согласно международному стандарту ISO 1940-1 и насколько рационально его назначение [26].
При подготовке инструмента к технологической операции, в которой будет применяться высокоскоростное фрезерование, величина допустимого остаточного дисбаланса, выставляемая в качестве допуска для инструментальной наладки, может принимать очень малые или вовсе недостижимые на практике значения. Данная проблема связана с жесткой привязкой качества балансировки к рабочей частоте вращения инструмента, а также особенностям эмпирических вычислений, в которых фигурирует масса инструментальной наладки. В связи с этим возникает необходимость пересмотра требований балансировки инструментальных наладок с целью сокращения времени и трудоемкости процесса подготовки инструмента к работе без потери качества обработки, уменьшения стойкости инструмента и сро- ка службы шпинделя станка.
Анализ публикаций [20,21,27,28,39,40] показал, что обеспечение наилучшего качества поверхности с сохранением высокой производительности процесса об- работки возможно с использованием методов математического моделирования. Особого внимания заслуживают работы [24,25,37,41,42], однако авторами работ не учитывается дисбаланс инструментальных наладок, особенности используе- мых инструментальных систем и состояние системы в целом. Для решения этой задачи необходимо установить влияние режимов резания и точности балансировки инструментальных наладок на формирование качества поверхности.
Исходя из вышеизложенного, была сформулирована цель диссертационной работы: обеспечение качества поверхностного слоя деталей из высокопрочных алюминиевых сплавов при высокоскоростном фрезеровании за счет достижения заданных параметров шероховатости обработанных поверхностей.
Достижение данной цели возможно при условии решения следующих за- дач:
1. Экспериментальная оценка влияния величины остаточного дисбаланса ин- струментальной наладки на процесс концевого фрезерования и шероховатость обработанной поверхности детали.
2. Разработка алгоритма расчета мгновенного значения толщины срезаемого слоя и формирования микропрофиля обработанной поверхности при концевом фрезеровании.
3. Установление эмпирической зависимости шероховатости обработанной поверхности от величины остаточного дисбаланса инструментальной наладки.
4. Разработка рекомендаций по балансировке инструментальных наладок, направленных на сокращение времени подготовки инструмента и обеспечиваю- щих получение обработанной поверхности с заданной шероховатостью.
Научная новизна работы
1. Теоретически и экспериментально установлено влияние режимов резания и величин остаточного дисбаланса инструментальной наладки на шероховатость обработанных поверхностей деталей из высокопрочных алюминиевых сплавов при высокоскоростном фрезеровании.
2. Разработана математическая модель расчета мгновенного значения толщи- ны срезаемого слоя и формирования микропрофиля обработанной поверхности при концевом фрезеровании. 3. Установлены закономерности, позволившие обеспечить заданный уровень параметров шероховатости при минимальных требованиях к качеству баланси- ровки.
Теоретическая значимость работы. Выведена эмпирическая зависимость шероховатости обработанной поверхности детали от величины остаточного дис- баланса инструментальной наладки и режимов обработки. Определены диапазоны допустимых значений остаточного дисбаланса инструментальных наладок.
Практическая значимость работы. Полученные результаты позволяют обеспечить:
– заданное качество обработанных поверхностей деталей из высокопрочных алюминиевых сплавов с остаточным дисбалансом инструментальных наладок;
– сокращение времени подготовки инструмента к работе за счет рациональ- ного выбора условий балансировки и режимов обработки;
– снижение технологической себестоимости изготавливаемых деталей за счет сокращения числа подготовительных операций.
Методология и методы исследования. Теоретические исследования бази- руются на научных основах технологии машиностроения, теории резания матери- алов, математического моделирования и модального анализа. Математическое моделирование исследуемого процесса выполнено в программе MATLab. Стати- стический анализ данных осуществлен с использованием пакета программ Statis- tica. Экспериментальные данные получены по результатам обработки высоко- прочных алюминиевых сплавов на 5-и координатном обрабатывающем центре HSC 75V linear. Измерения проводились с помощью приборов:
– контактного профилометра Taylor Hobson Form Talysurf i200 для измерения шероховатости обработанной поверхности,
– балансировочной машины Haimer TD2009 Comfort Plus для определения остаточного дисбаланса инструментальных наладок,
– динамометрического комплекса Kistler 9253B23 для контроля сил резания при фрезеровании, – программного комплекса для модального анализа для построения диаграмм стабильного резания,
– устройства для измерения и контроля геометрических параметров инстру- мента Zoller Genius 3.
По результатам проделанных работ автор выносит на защиту:
1. Алгоритм расчета мгновенного значения толщины срезаемого слоя и фор- мирования микропрофиля обработанной поверхности при концевом фрезерова- нии.
2. Построенную на основе результатов экспериментальных исследований эм- пирическую зависимость, отражающую влияние режимов резания и величины остаточного дисбаланса инструментальной наладки на шероховатость обработан- ной поверхности деталей из высокопрочных алюминиевых сплавов.
3. Технологические рекомендации по определению диапазона допускаемого дисбаланса инструментальных наладок и режимов высокоскоростной обработки фрезерованием деталей, гарантирующих получение заданной шероховатости об- работанной поверхности и существенное сокращение времени подготовительных операций.
Достоверность результатов обусловлена использованием современного, вы- сокоточного обрабатывающего и измерительного оборудования и лицензионного программного обеспечения. Математические расчеты, теоретические подходы, предложенные автором, подтверждаются проведенными экспериментальными ис- следованиями.
Апробация работы. Результаты диссертационной работы докладывались и обсуждались на X Международной конференции по технологии машиностроения, системам управления и автоматизации» (г. Томск, 2016), IX Всероссийской науч- но-практической конференции «Авиамашиностроение и транспорт Сибири» (г. Иркутск, 2017), XII Международной научно-технической конференции «Авиама- шиностроение и транспорт Сибири» (г. Иркутск, 2019), XIII Международной научно-технической конференции «Авиамашиностроение и транспорт Сибири» (г. Иркутск, 2019), XVIII Всероссийской научно-технической конференции «МО- ЛОДАЯ МЫСЛЬ: НАУКА, ТЕХНОЛОГИИ, ИННОВАЦИИ» (г. Братск, 2020), III Международной научно-технической конференции «APITECH-III 2021: Applied Physics, Information Technologies and Engineering» (г. Красноярск, 2021), XI Все- российской научно-технической конференции с международным участием «Жиз- ненный цикл конструкционных материалов» (г. Иркутск 2021).
Публикации. На основе материалов диссертационной работы опубликовано 9 работ, в том числе 4 статьи в научных изданиях, рекомендованных перечнем ВАК РФ для публикации результатов кандидатских и докторских диссертаций; 2 публикации в международных изданиях, входящих в базу Scopus.
Личный вклад автора. Формулировка цели и задач диссертационной рабо- ты. Разработана математическая модель, позволяющая определять микрогеомет- рию обработанной поверхности при концевом фрезеровании с учётом дисбаланса инструментальной наладки. Экспериментальные исследования, анализ, обработка и интерпретация полученных результатов, подготовка к публикации материалов исследований; формулировка выводов и положений, выносимых на защиту. Тех- нологические рекомендации по определению рациональной точности баланси- ровки инструментальных наладок с учетом режимов обработки и используемых инструментальных систем. Автор принимал непосредственной участие в разра- ботке и совершенствовании технологии механической обработки деталей авиаци- онной техники на высокопроизводительном оборудовании на Иркутском авиаци- онном заводе – филиале ПАО «Корпорация «Иркут».
Структура и объем работы. Диссертация включает введение, четыре главы, заключение, список литературы из 108 наименований и 4 приложений. Основная часть работы изложена на 137 страницах. Общий объем работы 168 страниц, включая 16 таблиц и 115 рисунков.
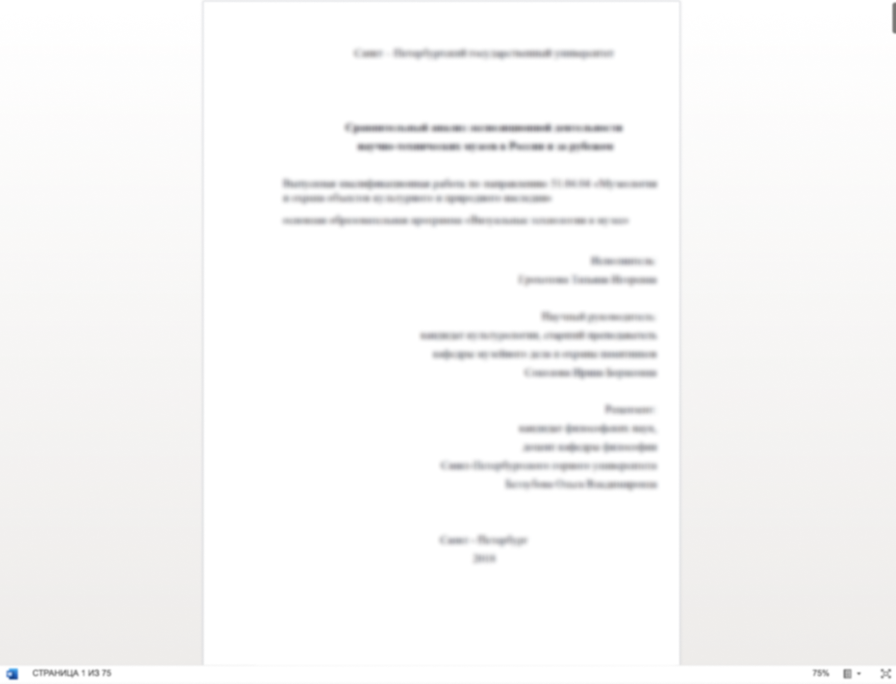
Публикации автора в научных журналах
Помогаем с подготовкой сопроводительных документов
Хочешь уникальную работу?
Больше 3 000 экспертов уже готовы начать работу над твоим проектом!