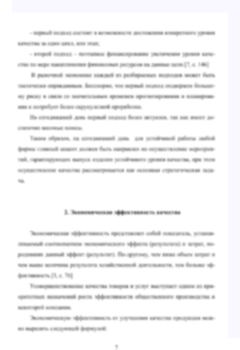
Повышение энергоэффективности систем пылеприготовления с шаровыми барабанными мельницами при работе на непроектных углях
Введение …………………………………………………………………………………………………………… 4
Глава 1. Анализ методов повышения энергоэффективности систем
пылеприготовления …………………………………………………………………………………………. 12
1.1. Особенности эксплуатации систем пылеприготовления с шаровыми
барабанными мельницами ……………………………………………………………………………. 12
1.2. Обзор результатов исследований энергоэффективности пылесистем ……… 16
1.3. Обзор работ по моделированию пневмотранспорта ……………………………….. 20
1.4. Постановка задач работы ………………………………………………………………………. 28
Глава 2. Моделирование течения газовзвеси в основных элементах систем
пылеприготовления …………………………………………………………………………………………. 29
2.1. Характеристика объекта исследования…………………………………………………… 29
2.2. Физико-математическая постановка задачи ……………………………………………. 31
2.3. Описание инструмента моделирования ………………………………………………….. 34
2.4. Исходные данные для расчета ……………………………………………………………….. 35
2.5. Численный эксперимент. Обработка результатов …………………………………… 38
2.6. Верификация результатов численного эксперимента ……………………………… 44
2.7. Выводы по главе 2 …………………………………………………………………………………. 46
Глава 3. Моделирование аэродинамического сопротивления основных элементов
пылесистем с учетом инжекции угольных частиц ……………………………………………. 48
3.1. Скорость витания и средний диаметр частиц угольной пыли …………………. 48
3.2. Аэродинамическое сопротивление, возникающее при инжекции угольных
частиц в ШБМ……………………………………………………………………………………………… 53
3.3. Аэродинамическое сопротивление, возникающее при инжекции частиц в
центробежных сепараторах пыли …………………………………………………………………. 57
3.4. Выводы по главе 3 …………………………………………………………………………………. 62
Глава 4. Анализ энергоэффективности шаровой барабанной мельницы ……………. 63
4.1. Сушильная производительность ШБМ…………………………………………………… 63
4.2. Расчет удельного расхода электроэнергии мельницы ШК-32 …………………. 65
4.3. Верификация полученных уравнений …………………………………………………….. 68
4.4. Анализ влияния режимных и внешних параметров на
энергоэффективность мельницы ШК-32 ………………………………………………………. 70
4.5. Определение оптимальной производительности мельницы ШК-32 при
размоле мугунского угля ……………………………………………………………………………… 73
4.6. Выводы по главе 4 …………………………………………………………………………………. 74
Заключение …………………………………………………………………………………………………….. 76
Список литературы …………………………………………………………………………………………. 79
Приложение А ………………………………………………………………………………………………… 93
Приложение Б …………………………………………………………………………………………………. 96
Приложение В ……………………………………………………………………………………………….. 101
Приложение Г ……………………………………………………………………………………………….. 111
Приложение Д ……………………………………………………………………………………………….. 117
Актуальность темы исследования. Экономия топливно-энергетических
ресурсов рассматривается в Федеральной программе «Энергетическая стратегия
России на период до 2030 года» [1] в качестве основного фактора повышения
конкурентоспособности отечественной продукции и минимизации техногенного
воздействия на окружающую среду. Значительные резервы экономии энергии
имеются в различных технологических процессах, в том числе в процессах размо-
Данная работа посвящена повышению энергоэффективности систем пыле-
приготовления с шаровыми барабанными мельницами при работе на непроектных
углях с использованием методов численного моделирования.
Основные выводы и результаты диссертационной работы:
1. Разработан подход к решению проблемы повышения энергоэффективно-
сти систем пылеприготовления с шаровыми барабанными мельницами при работе
на непроектных углях, основанный на моделировании пневмотранспорта уголь-
ной пыли.
2. Предложена математическая модель аэродинамического сопротивления
шаровых барабанных мельниц и центробежных сепараторов пыли, согласно кото-
рой полное аэродинамическое сопротивление складывается из ΔPгом – потерь дав-
ления гомогенного потока газовзвеси, вызванных трением и местными потерями,
и ΔPинж – потерь давления, обусловленных инжекцией угольных частиц в поток
воздуха.
Установлено, что аэродинамическое сопротивление шаровых барабанных
мельниц состоит на 80% из ΔPинж и на 20% из ΔPгом, аэродинамическое сопротив-
ление центробежных сепараторов – на 50% из ΔPинж и на 50% из ΔPгом.
3. Получены критериальные уравнения, описывающие зависимость аэроди-
намического сопротивления элементов пылесистем от средней скорости витания
и среднего диаметра частиц угольной пыли.
Коэффициент сопротивления гомогенного потока угольной газовзвеси для
шаровых барабанных мельниц
1
0,6
гом 1200 0,4
kL
Reв
Коэффициент сопротивления, вызванного инжекцией частиц, для шаровых
барабанных мельниц
инж 36,6(1 ) kвит
0,0216
kL ,
инж 36,6(1 ) kd0,0432kL .
Коэффициент сопротивления гомогенного потока угольной газовзвеси для
центробежных сепараторов пыли
9,12 104 се 1 се
0,343
гом
се
Reв0,657 .
Коэффициент сопротивления, вызванного инжекцией частиц, для центро-
бежных сепараторов пыли
инж
се
16,7 се
1,5
(1 )k вит ,
0,16
инж
се
16,7се
1,5
(1 )kd
0,317
.
Пределы применимости полученных уравнений:
Re в 3 105 2 106 ,
0,16 0,76,
kв ит 0,6 6,8,
kd 0,8 2,6.
Полученные уравнения согласуются с известными формулами для опреде-
ления потерь давления и с экспериментальными данными.
4. Предложена формула, позволяющая найти минимальный удельный рас-
ход электроэнергии на пылесистему с мельницей ШК-32, исходя из режима ра-
венства сушильной и размольной производительностей
0.0746 Dб3 Lб nб ψб0.56 γ н.ш К бр К тл 1.86 Dб Lб nб Sб ηэл ηпр N доп
ЭШБМ
ηэл ηпр Bс
1 μ Vв гом инж pв .
ηэл η мв Bс
Так минимальные затраты на размол азейского угля влажностью W р 25%
,опт 13.8 м /с (что соответствует
с шаровой загрузкой ψб = 0,2 достигаются при Vвнфу 3
производительности мельницы B = 57 т/ч) и составляют ЭШБМ = 18,9 кВт∙ч/т; при
размоле мугунского угля ( W р 22% , ψб = 0,2) минимум энергозатрат получается
,опт 12.9 м /с (B = 68 т/ч) и равен 15,8 кВт∙ч/т.
при Vвнфу 3
Средние отклонения результатов расчетов по предложенной формуле от
аналогичных экспериментальных данных находятся в диапазоне ±5%.
5. Полученные результаты внедрены в ПАО «Иркутскэнерго» для опреде-
ления энергозатрат пылесистемы с мельницей ШК-32 при размоле мугунского
бурого угля до тонины помола R90 = 35% (Приложение А).
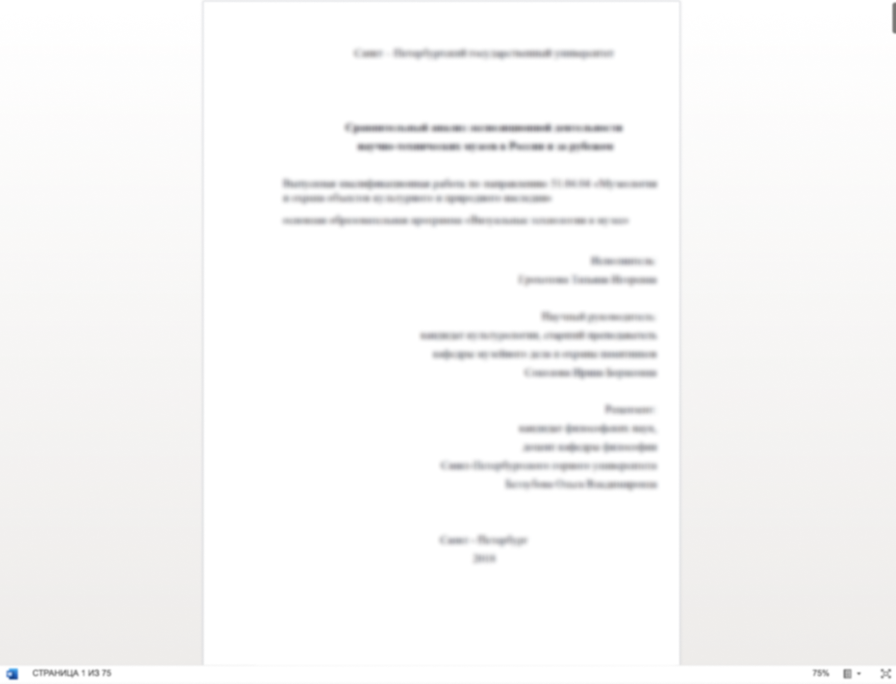
Помогаем с подготовкой сопроводительных документов
Хочешь уникальную работу?
Больше 3 000 экспертов уже готовы начать работу над твоим проектом!