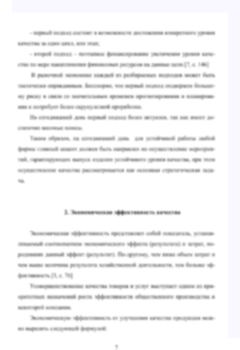
Повышение точности горячей прокатки плит из алюминиево-магниевых сплавов
ВВЕДЕНИЕ ……………………………………………………………………………………………….. 4
ГЛАВА 1 СОСТОЯНИЕ ВОПРОСА ПО ТЕОРИИ И ТЕХНОЛОГИИ
ПРОКАТКИ ПЛИТ ИЗ АЛЮМИНИЕВО-МАГНИЕВЫХ СПЛАВОВ ………. 10
1.1 Сортамент плит, материалы, применение………………………………………. 10
1.2 Управление толщиной при горячей прокатке плит …………………………… 15
1.3 Расчет силы прокатки ……………………………………………………………………… 17
1.4 Расчет теплового режима прокатки …………………………………………………. 24
1.5 Модели и моделирование горячей прокатки …………………………………….. 30
1.6 Выводы по главе ……………………………………………………………………………… 35
ГЛАВА 2 РАЗРАБОТКА КОМПЛЕКСНОЙ МАТЕМАТИЧЕСКОЙ МОДЕЛИ
ГОРЯЧЕЙ ПРОКАТКИ ПЛИТ ИЗ АЛЮМИНИЕВО-МАГНИЕВЫХ
СПЛАВОВ ДЛЯ РАСЧЕТА РАСТВОРА ВАЛКОВ В ПОСЛЕДНЕМ
ПРОХОДЕ ……………………………………………………………………………………………….. 37
2.1 Постановка задачи…………………………………………………………………………… 37
2.2 Анализ результатов моделирования напряженно-деформированного и
температурного состояния горячей прокатки плит ………………………………… 44
2.2.1 Анализ неравномерности напряжений ………………………………………. 44
2.2.2 Анализ неравномерности деформаций ………………………………………. 48
2.2.3 Анализ неравномерности температурного поля …………………………. 55
2.3 Методика определения силы прокатки …………………………………………….. 62
2.4 Оценка качества аппроксимации и адекватности модели …………………. 66
2.5 Методика определения температуры заготовки перед последним
проходом ……………………………………………………………………………………………… 69
2.6 Методика определения величины раствора между рабочими валками
при прокатке плит в последнем проходе ……………………………………………….. 71
2.6.1 Расчет температуры заготовки перед последним проходом …… 71
2.6.2 Расчет силы прокатки в последнем проходе ………………………….. 72
2.6.3 Расчет поправочного коэффициента ……………………………………… 73
2.6.4 Расчет величины раствора между рабочими валками в последнем
проходе …………………………………………………………………………………………….. 74
2.7 Выводы по главе ……………………………………………………………………………… 75
ГЛАВА 3 ЭКСПЕРИМЕНТАЛЬНЫЕ ДАННЫЕ ………………………………………. 77
3.1 Исследование реологических свойств обрабатываемых материалов …. 77
3.1.1 Методика проведения эксперимента …………………………………………. 77
3.1.2. Реологические свойства сплава АА5182 …………………………………… 84
3.1.3 Реологические свойства сплава 1565ч ……………………………………….. 90
3.1.4 Реологические свойства сплава 01570 ……………………………………….. 96
3.1.5 Сравнение реологических свойств сплавов АА5182, 1565ч, 01570
……………………………………………………………………………………………………….. 103
3.2 Определение коэффициента внешнего трения ……………………………….. 106
3.3 Определение коэффициента жесткости станины реверсивной клети
стана 2800 АО «Арконик СМЗ» ………………………………………………………….. 107
3.4 Сравнение точности результатов моделирования горячей прокатки плит
из алюминиево-магниевых сплавов в программе DEFORM 3D ……………. 110
3.5 Выводы по главе ……………………………………………………………………………. 117
ГЛАВА 4 ОПЫТНО-ПРОМЫШЛЕННАЯ АПРОБАЦИЯ РЕЗУЛЬТАТОВ
ИССЛЕДОВАНИЙ …………………………………………………………………………………. 119
4.1 Описание комплексной математической модели горячей прокатки плит
повышенной точности на реверсивном стане ………………………………………. 119
4.2.1 Описание технологии прокатки плит в реверсивной клети стана 123
4.2.2 Верификация комплексной математической модели горячей
прокатки плит повышенной точности на реверсивном стане ……………. 125
4.2.3 Оценка точности отработки модели…………………………………………. 126
4.3 Технологические рекомендации по горячей прокатке плит требуемого
качества из алюминиево-магниевых сплавов особо-твердой группы: АМг6,
5182, 1565ч, 1580, 01570 ……………………………………………………………………… 130
4.4 Расчет экономического эффекта…………………………………………………….. 139
4.5 Выводы по главе ……………………………………………………………………………. 141
ЗАКЛЮЧЕНИЕ ……………………………………………………………………………………… 142
СПИСОК СОКРАЩЕНИЙ И УСЛОВНЫХ ОБОЗНАЧЕНИЙ …………………. 144
СПИСОК ЛИТЕРАТУРЫ……………………………………………………………………….. 148
ПРИЛОЖЕНИЕ А ………………………………………………………………………………….. 163
ПРИЛОЖЕНИЕ Б …………………………………………………………………………………… 168
Во введении обоснована актуальность выбранной темы, степень разработан-
ности темы, сформулированы цель и задачи исследования, показана научная но-
визна и практическая значимость полученных результатов, приведены основные
положения, выносимые на защиту, достоверность полученных результатов.
В первой главе диссертации приведены основные сведения о плитах из алю-
миниевых сплавов системы Al-Mg, их свойствах и эксплуатационных характери-
стиках, анализ традиционного подхода к расчету силы прокатки и задачи теплово-
го баланса, текущая ситуация по настройке стана и существующие модели и мето-
ды моделирования горячей прокатки плит, сформулирована цель и задачи иссле-
дований.
Вторая глава посвящена постановке и описанию численного многофактор-
ного эксперимента, проведенного при помощи компьютерного моделирования
процесса горячей прокатки крупногабаритных плит выходной толщиной от 15 до
200 мм.
В качестве переменных выбраны технологические параметры, которые может
контролировать оператор стана: коэффициент формы очага деформации
m= /ℎср (где – длина дуги захвата, ℎср – средняя толщина заготовки), среднемас-
совая температура заготовки Т и частота вращения валков ω. Целевыми величи-
нами являются сила прокатки и среднемассовая температура раската. Численный
расчёт процесса горячей прокатки плит проведен методом конечных элементов в
программном комплексе DEFORM 3D с общепринятыми допущениями.
Анализ полей напряжений, деформаций и температур по результатам расче-
тов, показал, что прокатка плит в диапазоне толщин от 20 до 200 мм характеризу-
ется значительной неоднородностью, которая увеличивается с уменьшением ко-
эффициента формы очага деформации m. При m <1 неравномерность распределе-
ния напряжений по толщине полосы становится существенной на протяжении
всей длины очага деформации. Ввиду значительного отвода тепла, возникающего
вследствие контакта заготовки с рабочими валками, возникает заметный перепад
температур между поверхностью заготовки и центральными слоями.
На основе результатов численного моделирования разработана математиче-
ская модель и определены ее параметры для расчета силы прокатки плит из
сплавов АМг6, 5182, 1565ч, 1580 и 01570 в следующем виде:
�, �)� · ,
= � 1 ( ) + ( (1)
где B – ширина раската, мм.; 1 ( ) - базовая сила прокатки при Т=440 ℃ и ω=20
�, �) – величина изменения силы прокатки в зависимости от безраз-
об/мин.; (
мерных показателей скорости вращения валков � и температуры �:
�
−440� −20
� =,(2)�=
;(3)
44020
�, �) представлены полиномами первой степени:
Функции 1 ( ) и (
1 ( ) = 0 + 1 · � � + 2 · ,(4)
�, �) = 0 + 1 · � + 2 ·
( �, �,
� + 12 · (5)
Здесь 0 , 1 , 2 , 0 , 1 , 2 , 12 − расчетные коэффициенты, представленные в
таблице 1. Коэффициенты определяются методом наименьших квадратов при ап-
проксимации данных моделирования уравнением (4).
Коэффициенты 0 , 1 , 2 , 12 определяются также методом наименьших квад-
ратов по результатам расчетных данных полного факторного эксперимента 22 , па-
раметры которого представлены в таблице 2.
Таблица 1 - Коэффициенты уравнений (4) и (5), Н/мм
Сплав 0 1 2 0 1 2 12
АМг6623132813593-133-22703700-1343
5182680529133087102-215111025-220
1565ч728629633253-7-22921820-422
0157071242962318240-22764981-428
1580658330353305270-23471849-312
Таблица 2 – Уровни факторов и интервалы варьирования при моделировании процесса горя-
чей прокатки плит
Уровни варьи-
Обозначение
Интервал ва-
Единица из-
рьирования
мерения
Наименованиерования
№
параметра
-10+1
Температура
1 �°С40044048040
заготовки
Частота вра-
2щения рабо-�
об/мин5203515
чих валков
Результаты расчета силы прокатки заготовки из сплава АМг6 по формулам
(4) и (5) в зависимости от параметров m и T при ω = 20 об/мин приведены на ри-
сунке 1.
Рисунок 1 - Рассчитанная сила прокатки плит из сплава АМг6 в зависимости
от коэффициента формы очага деформации, температуры заготовки при ω = 20 об/мин
При малых значениях m (m<0,5) повышенные значения силы прокатки объ-
ясняются подпирающим действием заднего жесткого участка плиты, при более
высоких значениях параметра m (m>1) увеличение силы прокатки обусловлено
действием сил трения.
Для учета градиента температур в поперечном сечении заготовки разработана
модель расчета среднемассовой температуры заготовки перед последним прохо-
дом. Модель основана на аппроксимации результатов моделирования теплообмена
заготовки с окружающей средой и при взаимодействии с эмульсией в программ-
ном комплексе DEFORM 3D. Среднемассовую температуру плиты в сечении
определяли как среднеарифметическую по температуре узлов конечных элемен-
тов, находящихся в поперечном сечении. Моделирование охлаждения было прове-
дено для всех интересующих толщин. Результаты моделирования обработаны в
пакете MS Excel, построены линии тренда, характеризующие скорость охлаждения
в зависимости от температуры и толщины заготовок.
Модель расчета среднемассовой температуры заготовки перед последним
проходом (Т ) реализована в следующем виде:
Т = Т −1 − в − эм(6)
где Т −1 – температура раската после предпоследнего прохода, ℃; в и эм –
потери температуры в результате охлаждения заготовки на воздухе и при взаимо-
действии с эмульсией, соответственно:
в = 2,73 · τв /ℎ −1(7)
τэм
эм = [0,3(Т −1 − в ) − 105] ·,(8)
ℎ −1
ℎ −1 – толщина раската перед последним проходом, мм; τв и τэм – время от край-
него замера температуры до входа металла в клеть и время нахождения металла
под эмульсией, соответственно, с:
τв = тр + τз(9)
тр и τз – время транспортировки и время на неплановые задержки, с
τтр = ( р +22,5)/υр(10)
р – длина раската, м; υр – скорость рольганга, м/с;
Время нахождения металла под эмульсией τэм, зависит от размеров заготов-
ки и скорости прокатки и рассчитывается по следующей формуле:
τэм=υэм(11)
пр
где Lэм – активная длина площади теплообмена раската и эмульсии, м (расстояние
от оси рабочих валков до сдува составляет 10 м); υпр – средняя скорость прокатки,
м/с:
υпр= ω · π · D.(12)
где D – диаметр рабочих валков, м.
На базе разработанных моделей создана комплексная модель для определе-
ния величины раствора между рабочими валками в последнем проходе. Величина
раствора в последнем проходе является функцией от целевой толщины плиты и
смещения валков (ΔS) в результате упругих деформаций валков и клети ( ) и
поправочного коэффициента Δ. Поправочный коэффициент позволяет учесть от-
клонения от базового нуля и вычисляется по результатам калибровки модели на
предпоследнем проходе. Величина раствора определяется по формуле:
= -Δ.(13)
Упругое растяжение клети определяется по формуле:
= ∙ (14)
где – усилие на последнем проходе прокатки, рассчитанное по модели (1) с уче-
том среднемассовой температуры (6).
Учитывая величину смещения валков, определяется величина раствора ,
которую необходимо выставить для того, чтобы получить целевую толщину пли-
ты на выходе из клети ℎ :
= ℎ − ∙ + Δ.(15)
В третьей главе приведены результаты исследования реологических свойств
алюминиево-магниевых сплавов, в том числе дополнительно легированных пере-
ходными металлами, определена величина упругой деформации станины ревер-
сивной клети стана 2800 АО «Арконик СМЗ», методом предельных обжатий опре-
делен коэффициент трения, проведена оценка адекватности результатов модели-
рования горячей прокатки плит из алюминиево-магниевых сплавов в программном
комплексе DEFORM 3D.
Исследование реологических свойств проводилось на образцах с литой
структурой из сплавов АМг6, 5182, 1565ч, 1580 и 01570 на установке Gleeble 3800
с использованием модуля Hydrawedge при температурах 350–450 ℃ и скоростях
деформации ɛ̇ = 1-40 с−1 .
Модель реологических свойств задана общепринятой для алюминиевых спла-
вов формулой Селларса:
1
1/ n
Z
s m = arcsh ,(16)
a A
где Z – параметр Зинера-Холломона, который описывает деформационное поведе-
ние металлических материалов:
Q
Z = e exp .(17)
RT
В выражении (18) ε и T – соответственно скорость (с-1) и абсолютная темпе-
ратура (К) деформации, R=8,314 Дж/моль ⋅ К – газовая постоянная, Q – энергия ак-
тивации (Дж/моль) процесса, контролирующего горячую деформацию; α, n, A – ко-
эффициенты, значения которых определяются при помощи регрессионного анали-
за результатов испытаний образцов при разных температурах и скоростях дефор-
мации (таблица 3).
Таблица 3 – Коэффициенты для уравнения Селларса
Q,
Сплавnα, МПа−1A, −1
кДж/моль
АМг63,20,0235,2 ⋅ 109174
51822,6730,0276,551 ⋅ 109171
1565ч3,4530,01953,819 ⋅ 1010177,3
015702,3930,0255,558 ⋅ 1010178,5
15803,16580,02093,7783 ⋅ 1010175,7
%
Рисунок 2 – Изменение силы прокатки при производстве плит из сплава АМг6, Т=440 ℃,
ω= 20 об/мин (сплошная линия – расчетная кривая, маркер – фактические значения)
Анализ полученных данных показал высокую точность при моделировании в
DEFORM 3D (погрешность не более 3%).
В четвертой главе на основании комплексной математической модели расчета
раствора валков при горячей прокатке плит, разработан алгоритм для полуавтома-
тического управления толщиной на реверсивной клети стана 2800 на АО «Арко-
ник СМЗ». Алгоритм реализован на ЭВМ в пакете MS Excel и состоит из шести
модулей.
Первый модуль позволяет оператору перед началом прокатки ввести основные
данные для расчета. Для корректной работы модели необходимо из выпадающего
списка выбрать требуемый сплав, указать ширину, толщину, температуру раската
на предпоследнем проходе, а также и толщину hi, которая должна получиться по-
сле последнего прохода (рисунок 3). В модель заранее введены, но могут быть из-
менены, следующие параметры: частота вращения валков, радиус валков и модуль
жесткости клети.
Рисунок 3 – Модуль – Ввод данных
Второй модуль содержит реологические зависимости для каждого сплава. В
третьем и четвертом блоках рассчитывается среднемассовая температура заготов-
ки и сила прокатки. Пятый модуль необходим для калибровки модели, с целью
учета отклонений в размерах валковой системы (Δ), возникающих в течение дли-
тельного периода прокатки, например, тепловое расширение валков. Для калиб-
ровки производится расчет силы прокатки на предпоследнем проходе −1 и заме-
ряется толщина полосы после предпоследнего прохода ℎ −1 (при помощи лазерно-
го толщиномера или оператором вручную штангенциркулем). Исходя из расчет-
ной силы прокатки определяется абсолютная упругая деформация клети и попра-
вочный коэффициент по следующим формулам:
∆ −1 = −1 · ,(19)
Δ = −1 + ∆ −1 − ℎ −1 ,(20)
где −1 – раствор валка на предпоследнем проходе.
В шестом модуле рассчитывается величина раствора , которую должен вы-
ставить оператор для того, чтобы получить целевую толщину плиты.
Для определения точности разработанной математической модели технологиче-
ского процесса прокатки плит проведен сравнительный анализ данных получен-
ных с мониторинговых систем стана при прокатке плит на последних проходах и
рассчитанных с помощью разработанной математической модели по следующим
факторам, таким, как температура прокатки, сила прокатки, целевая толщина и
фактическая, при прокатке плит из сплава АМг6 (таблица 4).
Фактическую температуру раската измеряли ручной термопарой типа К, пер-
вого класса точности с индикацией данных на приборе TESTO 735–2, общая по-
грешность измерения всего комплекта +/-2℃. Сила прокатки измерялись штатны-
ми месдозами фирмы Kelk, установленными под подушками нижних опорных
валков, погрешность измерения 0,1%, с индикацией значения силы прокатки на
панели оператора. Отклонение фактической температуры от расчетной не превы-
шало 3 %, а фактической силы прокатки находилось в пределах от -0,4 до +1,6 %.
Таблица 4 – Сравнение расчетных и фактических значений температуры и силы прокатки при
прокатке слитков из сплава АМг6
Температура заго-
Размеры плитыСила прокатки, кН
товки, ℃
Толщина, ммШирина,
Расчет Эксп.∆,%РасчетЭксп.∆,%
Вх.Вых.мм
3019,51200379383-1,024 36924 1650,8
3725,41560382390-2,127 64927 2191,6
4333,315004003941,519 48519 567-0,4
46351200436446-2,216 60816 5890,1
4736,61560405416-2,623 43023 465-0,1
5040,41200447457-2,213 47613 2981,3
5040,51200440453-2,913 54513 3451,5
После получения удовлетворительных результатов расчета было получено
разрешение на прокатку плит из сплава АМг6 с использованием разработанной
модели.
Фактические замеры толщины производили лазерной системой измерения
толщины с погрешностью измерения +/- 0,1 мм. Финальная проверка результатов
проводилась на холодной плите, с замерами толщины штангенциркулем (точность
измерений 0,01 мм) в нескольких местах. Результаты сведены в таблице 5.
После успешного апробирования модели на плитах из сплава АМг6 было по-
лучено разрешение на опытную прокатку плит с применением модели в течение
месяца.
Таблица 5 – Результаты измерений на холодных плитах сплава АМг6
№ Заданная Ширина Предельное отклонение*Фактические
п/п толщина, плиты, Нормальной Повышенной отклонения,
мммммм
точноститочности
1801500±2,5±1,6+0,10
2601500±1,75±1,3+0,35
3851200±3,0±2,5+0,28
4701200±2,0±1,5+0,43
5401200±1,0±0,8+0,32
6401200±1,0±0,8+0,35
7401200±1,0±0,8+0,15
8401200±1,0±0,8+0,07
9201200±0,5±0,5+0,40
* – предельные отклонения по толщине плит согласно ГОСТ 17232–99.
Результаты замера толщин плит после опытной прокатки показаны на
рисунке 4. Как видно из диаграммы, благодаря применению комплексной модели
расчета требуемого раствора валков в последнем проходе, процесс прокатки плит
стал гораздо стабильней. Разнотолщинность резко снизилась, особенно на тонких
плитах – в три раза. Стабильность процесса прокатки обеспечивается за счет ис-
ключения вероятности ошибки оператора.
Рисунок 4 – Отклонение толщины плиты от номинальной до и после внедрения системы рас-
чета раствора валков
Внедрение модели в производство позволило:
– производить плиты повышенной точности по толщине;
– повысить выход годного на горячекатаных плитах с 62,7% до 65,7%;
– свести к единичным случаям отбраковку плит по выпадам за предельные
отклонения по толщине (с 3% до 0,5%).
Годовой экономический эффект от внедрения разработанной системы за счет
снижения отбраковки плит по признаку «несоответствие толщины» составил
1,6 млн. рублей.
ОСНОВНЫЕ ВЫВОДЫ
1. С применением комплекса Gleeble 3800 проведено физическое моделиро-
вание деформации образцов в условиях плоской деформации, в диапазоне темпе-
ратур 350-500℃ и скорости деформации 1–40 −1 . Выбранный диапазон соответ-
ствует промышленным условиям горячей прокатки плит. Построены кривые
упрочнения и определены истинные значения сопротивления пластической де-
формации алюминиево-магниевых сплавов, в том числе легированных переход-
ными металлами: АМг6, 5182, 1565ч, 1580 и 01570. Показано, что поведение но-
вых сплавов соответствует общепринятым представлениям, а закономерности мо-
гут быть описаны моделью Селларса.
2. Исследованием методом конечных элементов процесса прокатки плит про-
веден анализ степени влияния каждого фактора на величину силы прокатки. Один
из основных факторов, который необходимо учитывать — это форма очага де-
формации, которая определяется диаметром рабочих валков и толщиной плиты на
входе и выходе из очага деформации. Минимальное значение силы прокатки
наблюдается при m≈0,7 (плиты от 80 мм до 110 мм). При m<0,54 (толщина плит
от 120 мм до 200 мм) ввиду влияния жестких концов, сила прокатки увеличивает-
ся, и разница от минимального значения может доходить до 30%. При m>0,9 (пли-
ты толщиной менее 70 мм) также наблюдается увеличение силы прокатки, по при-
чине действия сил трения, увеличение силы прокатки в этом случае может дости-
гать до 45%. Второй фактор – это природа обрабатываемого материала, которая
выражается через сопротивление материала. Для учета данного фактора необхо-
димо максимально точно рассчитывать температуру в очаге деформации и ско-
рость деформации. Расчетами показано, что изменение температуры заготовки в
интервале температур от 400 до 480 ℃, а частоты вращения валков от 5 до 35
об/мин, приводит к изменению силы прокатки практически линейно.
3. На основе обработки результатов численного моделирования горячей про-
катки плит из алюминиево-магниевых сплавов получены математические модели
для расчета силы прокатки с учетом их реологических свойств, коэффициента
формы очага деформации, температуры и частоты вращения рабочих валков.
4. На основе результатов моделирования остывания заготовки плиты во время
взаимодействия с эмульсий и окружающей средой получены математические мо-
дели для расчета среднемассовой температуры заготовки перед последним прохо-
дом.
5. Предложена комплексная математическая модель расчета раствора валков
в заключительном проходе при горячей прокатке плит повышенной точности, ос-
нованная на разработанных моделях расчета силы прокатки и среднемассовой
температуры, упругого растяжения станины клети, с учетом поправки на величину
теплового расширения валков с адаптацией к технологическим особенностям ре-
версивного стана 2800 АО «Арконик СМЗ». Разработанная модель реализована на
базе табличного редактора MS Excel и установлена на ПК оператора пульта управ-
ления реверсивной клетью.
6. Разработанная комплексная модель прошла апробацию в условиях прокат-
ного производства и внедрена на реверсивном стане 2800 АО «Арконик СМЗ».
Внедрение модели в технологический процесс позволило повысить точность про-
катки плит по толщине до уровня повышенной точности ГОСТ 17232 и повысить
выход годного с 62,7% до 65,7%. Экономический эффект от внедрения результа-
тов работы составил 1,6 млн. рублей.
ПУБЛИКАЦИИ ПО ТЕМЕ ДИССЕРТАЦИОННОЙ РАБОТЫ
В изданиях, рекомендованных ВАК
1. Яшин, В.В. Влияние микролегирования переходными и редкоземельными ме-
таллами системы алюминий—магний на механические свойства при термоме-
ханической обработке / В.В. Яшин, Е.В. Арышенский, Н.Г. Колбасников,
М.С. Тептерев, И.А. Латушкин // Производство проката. – 2017. – №. 8. – С. 42–
48.
2. Яшин В. В. Анализ процесса прокатки крупногабаритных слитков с плакирую-
щим материалом при помощи метода конечных элементов / В.В. Яшин,
Э.Д Беглов, Е.В. Арышенский, И.А. Латушкин // Производство проката. – 2018.
– №. 1. – С. 24–29
3. Яшин, В.В. Обоснование технологии изготовления плоского проката из алюми-
ниевых сплавов системы Al-Mg-Sc для аэрокосмической промышленности /
В.В. Яшин, Е.В. Арышенский, М.С. Тептерев, И.А. Латушкин // Цветные ме-
таллы. – 2018. – №. 7. – С. 75–82.
4. Яшин, В.В. Реологические свойства деформируемых алюминиевых сплавов
01570 и 5182 в условиях горячей деформации / В.В. Яшин, С.В. Рушиц,
Е.В. Арышенский, И.А. Латушкин // Цветные металлы – 2019. – № 3. – С. 64–69.
5. Yashin, V.V. et al. Modeling of structure evolution during hot rolling of aluminum
alloys in the software package Deform / V.V. Yashin, M.S. Tepterev, E.V. Aryshen-
sky, V.V. Kolotilin // Journal of Siberian Federal University. Engineering & Technol-
ogies. – 2016. – Т. 9, №. 6. – P. 830-835.
6. Yashin, V. et al. Large size metal-clad ingots rolling process analysis using finite el-
ements method / V. Yashin, E. Beglov, E. Aryshensky, I. Latushkin // Journal of Sibe-
rian Federal University. Engineering & Technologies. – 2018. – Т. 11, №. 4. – P. 419-
426.
В издании, индексируемом Scopus/Web of Science
7. Yashin, V.V. Development of a Mathematical Model of Plate Rolling on Hot Revers-
ing Mills / V.V. Yashin, E.V. Aryshenskii, E.D. Beglov, M.S. Tepterev, A.F. Grechni-
kova // Key Engineering Materials. 2017. – Т. 746. – P. 48–55.
Учебное пособие
8. Каргин, В.Р. Элементы теории и технологии прокатки листов и плит из алюми-
ниевых сплавов: учебное пособие / В.Р. Каргин, В.В. Яшин, Е.В. Арышенский
// Самара: Изд-во Самарского университета, 2020. -136 с.
Актуальность темы исследования. В последние десятилетия в
отечественном транспортном машиностроении, судостроении,
мостостроении и аэрокосмической промышленности растет доля
алюминиевых сплавов. Замена стальных конструкций на алюминиевые в
железнодорожных, автомобильных и морских транспортных системах
позволяет существенно сократить их массу, и экономить на расходе топлива
увеличивая массу перевозимых грузов. В технологиях создания ракетно-
космической и транспортной техники нового поколения, включенных в
перечень критических 1.07.2011, предусмотрено применение новых
алюминиевых сплавов взамен менее легированных сплавов за счет
повышенной удельной прочности.
В связи с этим растет спрос на плиты из алюминиево-магниевых
сплавов, особенно стоит отметить спрос в промышленных масштабах на
плиты из новых труднодеформируемых сплавов с добавками переходных
металлов. К таким плитам предъявляют не только повышенные
требованиями к прочностным свойствам, но и к точности по толщине.
Реверсивный стан горячей прокатки кварто 2800 входящий в состав
производственных мощностей АО «Арконик СМЗ» обладает
характеристиками для выполнения заказов на плиты. Однако данный стан
используется как черновая клеть для непрерывной чистовой 5-клетьевой
группы, уровень оснащения, и действующая технология не позволяют
получать плиты повышенной точности.
Степень разработанности. Для получения плит повышенной точности
станы оснащают системами регулирования толщины, позволяющие
учитывать жесткость клети, температурно-скоростные параметры прокатки,
температурной расширение валков и другие факторы. Известные
теоретические математические модели базируются на математической
теории пластичности и механике сплошных сред. Развитием данных теорий
занимались многочисленные ученые: С.И. Губкин, Н.А. Соболевский,
А.И. Целиков, И.М. Павлов, В.С. Смирнов, И.Я. Тарновский, П.И. Полухин,
А.А. Королев, Б.П. Бахтинов, Е.С. Рокотян, Е. Зибель, Т. Карман, Р. Симс,
О. Павельски и другие. Прокатке заготовок из алюминиевых сплавов
посвящены работы А.И. Колпашникова, И.М. Мееровича, С.И. Ковалева,
Н.И. Корягина и И.В. Ширко. Существенный вклад по расчету
энергосиловых параметров внесли Т. Карман, А.И. Целиков и
температурного режима И.М. Меерович, В.К. Орлов. Из современных работ
следует отметить работы Г.С. Никитина, В.А. Рудского, А.Г. Колесникова и
С.Б. Сидельникова. Из современных самарских ученых прокату
алюминиевых сплавов посвящены работы Ф.В. Гречникова,
В.Ю. Арышенского и А.М. Оводенко.
Большое практическое применение нашел способ построения
математических моделей посредством анализа статистических данных, а
физический эксперимент все больше вытесняют виртуальные модели.
Цель работы – повышение точности горячей прокатки на
одноклетьевом стане плит из алюминиево-магниевых сплавов за счет
прогнозирования упругого растяжения клети с учетом её жесткости,
реологических свойств обрабатываемых материалов и геометрии очага
деформации.
Для достижения поставленной цели сформулированы следующие
задачи исследования:
1. Проведение исследований реологических свойств алюминиево-
магниевых сплавов, в том числе легированных переходными металлами в
условиях плоской деформации, в диапазоне температур промышленной
прокатки 350–500 ℃ и скорости деформации 1-40 −1 и использование
полученных данных для моделирования горячей прокатки.
2. Исследование методом конечных элементов напряженно-
деформированного состояния и температурных условий горячей прокатки
плит.
3. Разработка методики построения математической модели для
расчета усилия прокатки плит из алюминиево-магниевых сплавов с помощью
численного моделирования прокатки, с учетом реологических свойств
материалов, напряженного состояния, коэффициента внешнего трения,
температуры заготовки и частоты вращения рабочих валков.
4. Разработка методики построения математической модели расчета
среднемассовой температуры заготовки при помощи численного
моделирования прокатки.
5. Разработка комплексной математической модели горячей прокатки
плит в заключительном проходе, основанная на методиках расчета усилия
прокатки и среднемассовой температуры заготовки перед последним
проходом, упругого растяжения станины клети, величины термического
расширения валков с адаптацией к технологическим особенностям
реверсивного стана 2800 АО «Арконик СМЗ».
6. Апробация разработанной комплексной математической модели
горячей прокатки плит из алюминиево-магниевых сплавов в условиях
прокатного производства АО «Арконик СМЗ» на реверсивном стане 2800.
Объект исследования: процесс горячей прокатки плит из алюминиево-
магниевых сплавов: АМг6, 5182, 1565ч, 1580 и 01570.
Предмет исследования: математическая модель формирования
толщины при горячей прокатке плит из алюминиевых сплавов АМг6, 5182,
1565ч, 1580 и 01570.
Область исследования: п. 1 «Закономерности деформирования
материалов и повышения их качества при различных термомеханических
режимах, установление оптимальных режимов обработки», п. 8 «Технологии
продольной и поперечно-винтовой прокатки заготовок деталей, методы
конструирования деталепрокатных станов» паспорта специальности 2.5.7.
1. С применением комплекса Gleeble 3800 проведено физическое
моделирование деформации образцов в условиях плоской деформации, в
диапазоне температур 350–500 ℃ и скорости деформации 1–40 −1 .
Выбранный диапазон соответствует промышленным условиям горячей
прокатки плит. Построены кривые упрочнения и определены истинные
значения сопротивления пластической деформации алюминиево-магниевых
сплавов, в том числе легированных переходными металлами: АМг6, 5182,
1565ч, 1580 и 01570. Показано, что поведение новых сплавов соответствует
общепринятым представлениям, а закономерности могут быть описаны
моделью Селларса.
2. Исследованием методом конечных элементов процесса прокатки
плит проведен анализ степени влияния каждого фактора на величину силы
прокатки. Один из основных факторов, который необходимо учитывать —
это форма очага деформации, которая определяется диаметром рабочих
валков и толщиной плиты на входе и выходе из очага деформации.
Минимальное значение силы прокатки наблюдается при m≈0,7 (плиты от 80
мм до 110 мм). При m <0,54 (толщина плит от 120 мм до 200 мм) ввиду
влияния жестких концов, сила прокатки увеличивается, и разница от
минимального значения может доходить до 30%. При m>0,9 (плиты
толщиной менее 70 мм) также наблюдается увеличение силы прокатки, по
причине действия сил трения, увеличение силы прокатки в этом случае
может достигать до 45%. Второй фактор – это природа обрабатываемого
материала, которая выражается через сопротивление материала. Для учета
данного фактора необходимо максимально точно рассчитывать температуру
в очаге деформации и скорость деформации. Расчетами показано, что
изменение температуры заготовки в интервале температур от 400 до 480 ℃, а
частоты вращения валков от 5 до 35 об/мин, приводит к изменению силы
прокатки практически линейно.
3. На основе обработки результатов численного моделирования
горячей прокатки плит из алюминиево-магниевых сплавов получены
математические модели для расчета силы прокатки с учетом их
реологических свойств, коэффициента формы очага деформации,
температуры и частоты вращения рабочих валков.
4. На основе результатов моделирования остывания заготовки плиты во
время взаимодействия с эмульсий и окружающей средой получены
математические модели для расчета среднемассовой температуры заготовки
перед последним проходом.
5. Предложена комплексная математическая модель расчета раствора
валков в заключительном проходе при горячей прокатке плит повышенной
точности, основанная на разработанных моделях расчета силы прокатки и
среднемассовой температуры, упругого растяжения станины клети, с учетом
поправки на величину теплового расширения валков с адаптацией к
технологическим особенностям реверсивного стана 2800 АО «Арконик
СМЗ». Разработанная модель реализована на базе табличного редактора MS
Excel и установлена на ПК оператора пульта управления реверсивной
клетью.
6. Разработанная комплексная модель прошла апробацию в условиях
прокатного производства и внедрена на реверсивном стане 2800 АО
«Арконик СМЗ». Внедрение модели в технологический процесс позволило
повысить точность прокатки плит по толщине до уровня повышенной
точности ГОСТ 17232 и повысить выход годного с 62,7% до 65,7%.
Экономический эффект от внедрения результатов работы составил 1,6 млн.
рублей.
СПИСОК СОКРАЩЕНИЙ И УСЛОВНЫХ ОБОЗНАЧЕНИЙ
hi-1 – толщина проката до рассчитываемого прохода,
hi – толщина после рассчитываемого прохода (требуемая толщина),
i – номер прохода,
ℎ − высота очага деформации в нейтральном сечении,
Hсл, Всл и Lсл – толщина, ширина и длина слитка
B – номинальная ширина листа, полосы, плиты,
Вi – ширина полосы в n-м проходе,
Вi-1 – ширина полосы в предыдущем проходе,
∆Вi – уширение при прокатке,
– длина дуги захвата,
m – показатель геометрии очага деформации,
R – радиус рабочего валка,
D, Dр – диаметр рабочих валков,
Dоп – диаметр опорных валков,
Lбоч – длина бочки валка,
ω – число оборотов рабочих валков в минуту,
Δh – абсолютное обжатие полосы,
α – угол захвата,
P – сила прокатки;
Мпр – момент прокатки;
А – работа прокатки;
N – мощность прокатки;
ср – среднее удельное давление металла на валки
εn – величина относительного обжатия,
∑ – величина суммарного относительного обжатия,
Z – параметр Зинера-Холломона,
– скорость деформации,
λ – коэффициент вытяжки,
– длина заготовки после прокатки,
−1 – длина заготовки перед прокаткой,
Fк – площадь контакта металла с валком,
ОПД – очаг пластической деформации,
ℎср – средняя высота ОПД,
в – окружная скорость валков,
пр – скорость прокатки (выхода металла из валков),
, −1 – величина раствора между рабочими валками в последнем и
соответственно в предпоследнем проходе,
ϒ – нейтральный угол,
— коэффициент, учитывающий влияние напряженного состояния,
′ – коэффициент, учитывающий влияние внешнего трения,
′′ – коэффициент, учитывающий влияние внешних зон до входа в очаг
деформации и на выходе из него,
′′′ – коэффициент переднего и заднего натяжения,
T – температура деформации,
в – предел прочности,
0,2 – предел текучести условный,
– предел текучести фактический,
о.д. – сопротивление деформации при одноосной деформации,
К , К , К – температурный, степенной и скоростной коэффициенты
прокатываемого сплава соответственно,
а, b, c, d, k, l, m, , n, A, Q, 0 , 1 , 2 , 0 , 1 , 2 , 12 – эмпирические
коэффициенты, зависящие от природы материала,
Z – параметр Зинера-Холломона,
δ, A – относительное удлинение после разрыва,
Ψ – относительного сужения,
ψ – коэффициент плеча,
– контактные силы терния,
μ – коэффициент трения,
Тнач – температура начала прокатки,
Токон – температура окончания прокатки,
Tв – падение температуры вследствие теплоотдачи рабочим валкам,
Tэм – падение температуры за счет, охлаждения эмульсий,
T и T – падение температуры за счет теплоизлучения и конвекцией,
T – повышение температуры за счет теплового эффекта,
Q – потеря тепла полосой,
Qв – потеря тепла вследствие теплоотдачи рабочим валкам,
Qэм – тепло, отведенное эмульсий,
Q и Q – потери тепла теплоизлучением и конвекцией,
Qн – тепло, приобретенное полосой, от пластической деформации металла,
в – теплопроводность материала валков,
в – удельный вес материала валков,
Св – теплоемкость материала валков,
Вв – константа для материала валков,
Tв – температура рабочих валков,
– время соприкосновения,
Вп – константа для материала прокатываемой полосы,
п – теплопроводность материала полосы,
Сп – теплоемкость материала полосы,
в – коэффициент теплопередачи на контакте валка и полосы,
п – плотность полосы,
п – теплоемкость полосы,
п – скорость выхода полосы из валков,
0 – напряжение, вызванное задним натяжением полосы,
1 – напряжение, вызванное передним натяжением полосы,
0 , 1 – сопротивление чистому сдвигу соответственно на входе в валки и
выходе из них металла,
t – коэффициент лучеиспускания,
Тп – температура полосы,
α – коэффициент конвекции;
Tвозд – температура окружающей среды,
охл – длительность паузы от крайнего замера температуры до входа металла
в клеть.
̅ – относительный безразмерный показатель смещения температуры раската
от базовой величины (440 ℃),
̅ – относительный безразмерный показатель смещения частоты вращения
рабочих валков от базовой величины (20 об/мин),
s – среднее квадратичное отклонение в Н,
S – среднее квадратичное отклонение в %.
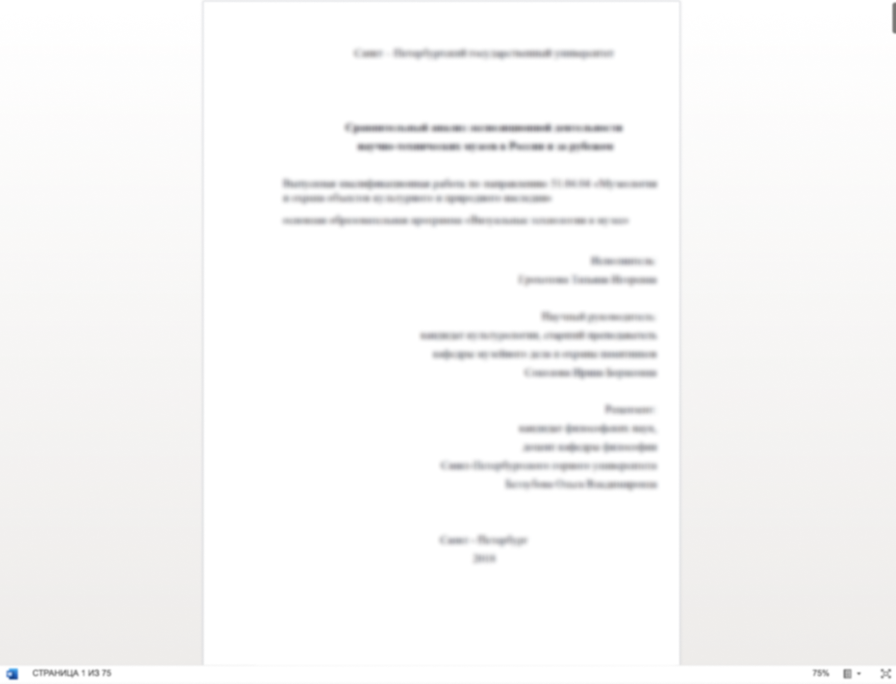
Публикации автора в научных журналах
Помогаем с подготовкой сопроводительных документов
Хочешь уникальную работу?
Больше 3 000 экспертов уже готовы начать работу над твоим проектом!