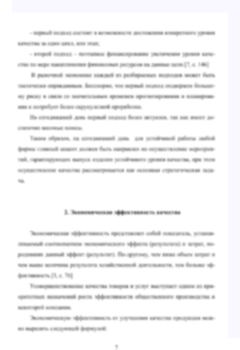
Разработка методики и моделей для повышения технологических характеристик процесса сборки при ремонте ротора компрессора высокого давления ГТД
ОГЛАВЛЕНИЕ
ВВЕДЕНИЕ
ГЛАВА 1 Проблемы и пути повышения точности сборочных параметров ремонтных роторов барабанно-дискового типа
1.1 Объект исследования
1.2 Анализ проблем технологии сборки ротора КВД при его ремонте
1.3 Способы обеспечения сборочных параметров при ремонте роторов барабанно-дискового типа
1.4 Обзор моделей расчёта сборочных параметров изделий
1.5 Выводы по главе 1. Цель и задачи исследования
ГЛАВА 2 Разработка методики и моделей для повышения точности сборки при ремонте ротора КВД
2.1 Методика оценки точности и определения условий выполнения при сборке ротора КВД
2.2 Обработка результатов измерений и математическое представление геометрии поверхностей деталей
2.3 Конечно-элементное моделирование сборки ротора КВД
2.3.1 Цифровая модель сборки ротора КВД
2.3.2 Теоретические исследования сборочных параметров ротора КВД
2.3.3 Модель оценки торцевых биений ротора КВД с параллельными связями деталей
2.4 Модель определения условий выполнения ремонта и сборки ротора ГТД
2.5 Теоретические исследования точности сборки ротора КВД
2.6 Выводы по главе 2
ГЛАВА 3 Методики исследования геометрической точности ротора компрессора высокого давления ГТД
3.1 Методика исследования точности сборки роторов КВД в условиях лаборатории
3.1.1 Последовательность проведения исследований
3.1.2 Проведение исследований
3.1.3 Результаты исследований
3
3.2 Методика исследования точности сборки роторов КВД в цеховых условиях
3.2.1 Проведение исследований
3.2.2 Результаты исследований
3.3 Выводы по главе 3
ГЛАВА 4 Практическое использование результатов диссертационного исследования на предприятиях отрасли
4.1 Программное приложение для определения условий сборки ротора КВД при ремонте на основе измерения геометрических параметров его деталей
4.2 Технологическая инструкция по сборке ротора КВД при его ремонте на основе использования программного приложения
ЗАКЛЮЧЕНИЕ
СПИСОК СОКРАЩЕНИЙ И УСЛОВНЫХ ОБОЗНАЧЕНИЙ
СПИСОК ЛИТЕРАТУРЫ
ПРИЛОЖЕНИЕ А
ПРИЛОЖЕНИЕ Б
ПРИЛОЖЕНИЕ В
ПРИЛОЖЕНИЕ Г
ПРИЛОЖЕНИЕ Д
ПРИЛОЖЕНИЕ Е
ПРИЛОЖЕНИЕ Ж
ПРИЛОЖЕНИЕ З Свидетельство о государственной регистрации программы для ЭВМ
ПРИЛОЖЕНИЕ И Свидетельство о государственной регистрации программы для ЭВМ
ПРИЛОЖЕНИЕ К Свидетельство о государственной регистрации программы для ЭВМ
ПРИЛОЖЕНИЕЛ Патентнаизобретение………………………………………………..168
Во введении обоснована актуальность темы исследования, приведена краткая характеристика
работы, сформулированы цель, задачи и изложена научная новизна исследований. Представлены
основные положения, выносимые на защиту и сведения об апробации результатов работы.
В первой главе описан объект исследования, выполнен анализ проблем технологии
сборки ротора КВД в ходе его ремонта, выявлены основные проблемы обеспечения заданной
точности при сборке роторов барабанно-дискового типа. При анализе статистических данных
определены проблемы, встречающиеся при ремонте ротора КВД. Рассматриваемый узел
включает с 10-й по 14-ю ступени ротора КВД. Выбор узла определялся следующими
особенностями: 1) наличием взаимосвязанных размерных связей между его деталями,
существенно усложняющих оценки сборочных параметров; 2) частой заменой промежуточных
колец 12-й и 13-й ступеней на новые в ходе ремонта ротора; 3) наибольшим влиянием угловых
положений деталей с 10-й по 14-ю ступени ротора на величину его сборочных параметров.
Выполнен обзор публикаций по проблеме обеспечения заданной точности при сборке
роторов ГТД. Проанализированы факторы, влияющие на точность и трудоёмкость
технологических операций сборки (работы И. Ф. Кравченко, А.М. Дальского, А.А. Маталина,
А. И. Максименко, А. С. Шевелева, Ф. И. Демина, В. В. Непомилуева, М.Е. Ильиной,
А.Н. Семенова, Е.В. Тимофеевой, В.П. Тимофеева, А.А. Гарькавого, Ю.В. Ерошкова,
В.А. Захарова, Е.А. Майорова, В. А. Иванова). Основными факторами, оказывающими
существенное влияние на геометрическую точность ротора, являются: отклонения формы и
расположения поверхностей деталей, жесткость и параллельные размерные связи между ними.
Достижение заданной точности сборки ротора КВД выполняется методом индивидуальной
подгонки деталей по месту. Сущность метода заключается во взаимном ориентировании деталей и
узлов друг относительно друга с целью взаимной компенсации геометрических отклонений
сопрягаемых поверхностей. Изменение углового положения деталей сопровождается выполнением
полной или предварительной сборки узла. Применение предварительных сборок позволяет
определять условия выполнения сборочных и ремонтных операций. Названные условия включают:
относительные угловые положения деталей в узле; размеры компенсационных деталей; детали,
требующие ремонта или замены на аналогичные новые. Использование предварительных сборок
приводит к увеличению трудоёмкости технологических операций и ухудшению качества деталей.
Перспективным путём достижения заданной точности роторов КВД является использование
цифровых моделей для замены предварительных сборок виртуальным моделированием.
Выполнен обзор публикаций, посвященных вопросам разработки моделей, позволяющих
оценивать геометрическую точность изделий и направленных на решение следующих задач:
1) представление геометрических отклонений деталей (работы, M.Y. Wang, E.P. Morse, J.D. Davidson,
M. Giordano, D. Teissandier, D. Bourdet, K.W. Chase, X. Yan, A. Ballu, E. Boyer, J.A. Clementa,
A. Desrochers); 2) оценка сборочных параметров изделий (работы Ф. И. Демина, П. Ф. Дунаева,
И. А. Иващенко, И. А. Коганова, М. Г. Косова, Ю. М. Соломенцева, А. С. Шевелева, А. И. Якушева,
И.Ф. Кравченко, Гарькавого, Ю.В. Ерошкова, В.А. Захарова, М.Е. Ильиной, В.В. Непомилуева,
В.П. Тимофеева, Е.В. Тимофеевой, А.А. Федорова). Анализ существующих методов расчёта
сборочных параметров узлов позволил сделать
вывод об отсутствии моделей, одновременно
учитывающихотклоненияформыи
расположения поверхностей деталей, жёсткость
и параллельные размерные связи между ними, и
ориентированныхнаиспользованиев
производственных условиях. Отличие сборки
ремонтных роторов от сборки новых,
заключается в необходимости выявления
деталей, требующих замены или механической
доработки, для обеспечения заданной точности
сборочныхпараметровузлов.В
разрабатываемых методике и моделях должна
быть предусмотрена возможность определения
конкретных деталей, требующих замены или
ремонта. Необходима разработка методик и
моделей, которые позволяют учитывать
названные недостатки, а также определять УВС
при ремонте роторов КВД. Актуальной задачей
является разработка методики оценки точности
сборки и определения УВС роторов с
параллельными размерными связями деталей.
На основании проведенного обзора публикаций Рисунок 1 – Блок схема методики оценки точности
сформированы задачи исследования.сборки и определения УВС при ремонте ротора КВД
Вторая глава посвящена разработке методики и моделей для повышения
технологических характеристик процесса сборки при ремонте ротора КВД. В первом
разделе главы представлена методика оценки торцевых биений и определения условий
сборки при ремонте роторов КВД ГТД, которая основана на использовании двух моделей:
оценки торцевых биений узлов и определения условий выполнения их сборки.
Разработанная методика представлена в виде блок схемы на рисунке 1.
Первый блок включает измерения поверхностей деталей ротора КВД. Результаты
измерений обрабатываются и преобразуются в массивы параметров, характеризующих
геометрические отклонения формы и расположения поверхностей деталей. Второй блок
предусматривает создание КЭМ узла ротора КВД для моделирования его сборки с учетом
отклонений формы и расположения поверхностей деталей. С помощью КЭМ выполняются
теоретические исследования, по результатам которых определяются значения параметров
модели оценки торцевых биений ротора КВД (этап 3.1 блок-схемы). Третий блок предполагает
использование двух моделей. Первая модель позволяет рассчитывать торцевые биения ротора
на основе загруженных параметров поверхностей его деталей. Вторая модель решает задачу
определения УВС при ремонте ротора и состоит из двух подмоделей. Первая подмодель
позволяет определять рациональные угловые положения деталей в ремонтном роторе, исходя
из целевой функции минимизации его торцевых биений. Вторая подмодель предназначена для
определения конкретных деталей, которые необходимо подвергнуть ремонту с целью
достижения заданной точности торцевых биений ротора. Выполняется проверка достижения
заданной точности сборочных параметров. Четвёртый блок предусматривает выполнение
ремонта деталей и последующую сборку ротора с учетом рассчитанных рациональных угловых
положений, найденных в процессе выполнения третьего блока.
Во втором разделе главы описывается последовательность обработки результатов
измерений и математического представления геометрии поверхностей деталей. Отклонения
геометрических параметров деталей имеют сложную форму и в общем виде могут быть
представлены поверхностями двойной кривизны. Геометрические отклонения деталей зачастую
характеризуются повторяющими особенностями, которые могут быть представлены с
использованием гармонических функций. Описание геометрических отклонений торцевых и
цилиндрических поверхностей деталей выполняется с использованием следующих параметров:
Ai , j – амплитуда отклонения формы торцевой поверхности, мм; ∆Ti, j – отклонение от
параллельности торцевой поверхности относительно базовой, мм; ji , j , γ i , j – углы наклона торцевой
поверхности к осям X и Y локальной системы координат детали, град.; ∆ iR, j – отклонение от
круглости цилиндрической поверхности детали, мм; Di , j – диаметр поверхности детали ротора,
мм. На четвертом этапе дискретно заданное отклонение формы сопрягаемой поверхности
представляется функцией, заданной относительно локальной системы координат детали.
Отклонение формы и расположения торцевой поверхности задаётся системой
уравнений с параметрами:
Di , jгде xtiT, j , ytiT, j , ztiT, j – координаты торцевой
⋅ cos(ti , j ) + xti , j
xt
T
i, j 2поверхностипоосямХ i , Yi , Z i
T Di , j , (1)
yti , j= M x (ji , j ) ⋅ M y (γ i , j ) ⋅ ⋅ sin(ti , j ) + yti0, jсоответственно;M x (ji , j ) ⋅ M y (γ i , j ) –
T 2матрицы трансформации соответственно
zti , j H i , j + Ai , j ⋅ sin ( ki , j ⋅ ti , j )
вокруг осей x и y на углы ji , j , γ i , j ;
Di , j – диаметр поверхности детали узла, мм;
ti , j – угловаякоординататочекповерхности,( 0 … 2π ),град;H i , j – координата
расположения поверхности относительно локальной системы координат детали, мм; Аi , j –
амплитуда отклонения формы, мм; ki , j – коэффициент, влияющий на вид отклонения
формы поверхности и выбираемый исходя из результатов измерений деталей; xti0, j , yti0, j –
координаты смещения рассматриваемой поверхности относительно базовой.
Отклонение формы и расположения цилиндрической поверхности задаётся системой
уравнений с параметрами:
R Di , jгде xtiR, j , ytiR, j , ztiR, j – координаты цилиндрической
xti , j =+ Ai , j ⋅ sin(ki , j ⋅ ti , j ) ⋅ cos(ti , j ) + xti , j
2(2) поверхности по осям Х i , Yi , Z i соответственно.
R Di , j
yti , j =В третьем разделе главы приведено описание
+ Ai , j ⋅ sin( ki , j ⋅ ti , j ) ⋅ sin(ti , j ) + yti0, j ,
2
взаимодействия используемых программ для создания
zti , j = H i , j
R
параметризованной КЭМ узла ротора КВД (рисунок
2). Представлена КЭМ для оценки сборочных
сборочных параметров ротора КВД газотурбинного двигателя. Основными сборочными
параметрами ротора КВД являются торцевые и радиальные биения контрольных
поверхностей деталей узла.
Разработанная КЭМ узла ротора КВД
предназначена для формирования исходных данных с
целью обучения регрессионной модели, которая
представлена в четвертом разделе второй главы. С
помощью КЭМ получены результаты теоретических
исследованийдляопределениявзаимосвязи
геометрических отклонений поверхностей деталей и
биений узла ротора КВД. Исследовались зависимости
сборочных параметров узла ротора КВД от амплитуд Рисунок2 – Взаимодействие
отклонений формы сопрягаемых поверхностей:используемых программных систем
1) торцевых; 2) цилиндрических; 3) торцевых и цилиндрических совместно. На рисунке 3
представлены результаты биений контрольных торцевых и цилиндрических поверхностей
ротора КВД.
аб
Рисунок 3 – Зависимость биений диска 12-ой ступени от его углового положения в
узле ротора КВД и отклонений формы поверхностей: а) торцевых и цилиндрических
раздельно; б) торцевых и цилиндрических – совместно
Можно сделать вывод о том, что величина отклонений формы торцевых
поверхностей деталей является основным фактором, влияющим на биения дисков. В
дальнейших исследованиях будут рассматриваться только отклонения формы торцевых
поверхностей деталей узла ротора КВД. При этом погрешность оценки торцевых биений
узла ротора составит не более 16%, что соответствует требованиям оценки точности
сборочных работ.
Во второй части третьего раздела второй главы представлена разработка модели
оценки торцевых биений ротора узла КВД по значениям отклонений формы и
расположения сопрягаемых поверхностей деталей, а также по их угловым положениям.
Выражение для оценки торцевого биения j-ой поверхности i-го диска узла ротора КВД
имеет вид:
()( )(
Тбi , j A,α , DT ,j , γ , D =b0 + F1 A + F2 DT ,j , γ , D + F3 A;α ,) ( )(3)
гдеb0 – коэффициент;()
F1 A – функция,учитывающая влияние отклонений формы
поверхностей деталей на постоянный уровень торцевого биения дисков, имеющая вид:
( )
n
F1 A = ∑ Ai ki0 ; F2 ( D,ϕ , γ , D ) – функция, учитывающая влияние отклонений расположения
i =1
поверхностейдеталейнаторцевоебиениедисков,имеющаявид
D _1
T
j
1 n m Di , j ki , j ⋅ sin(α i + ji , j + ki ) + …
()()
T
F2 D ,j , γ , D = ∑∑
T
⋅; F3 A, α – функция, учитывающая влияние
2=i 1 =j 1 Di , j + k DT_ 2 ⋅ sin(α + γ + k γ )
i, jii, ji
отклонений формы поверхностей деталей и их угловых положений в узле на торцевое
∑ ( A)()
n
биениедисков,имеетвид:,α )
F3 ( A=⋅ kiA, j + fi , j ⋅ sin α i , j + kiα, j ;
i =1
i, j
∆T∆T
ki0 ; ki , j_1 ki , j_ 2 ; kiϕ ; kiγ ; kiA, j ; kiα– коэффициенты. Приведенные коэффициенты находятся
посредством решения регрессионной задачи.
В четвертом разделе главы представлена модель определения условий выполнения
сборки и ремонта ротора ГТД. Модель состоит из двух подмоделей. Первая подмодель
определяет рациональные угловые положения деталей в ремонтном роторе. Вторая
подмодель предназначена для определения деталей, требующих ремонта или замены на
новые, с целью достижения заданной точности торцевых биений ротора. Определение
рациональных угловых положений деталей в роторе при его ремонте может выполняться
из условия минимизации торцевых биений в следующем виде:
α ∈ 0; ;2π
(
minimize Тб1,1 (α ) , Тб1,2 (α ) , Тб1,3 (α ) …Тбi , j (α ) ,
π
(4))
n
π
где α ∈ 0; ;2π – вектор, задающий допустимые угловые положения деталей в роторе;
n
n ∈ N – количество угловых положений деталей в роторе; Тбi, j – Тб1,1 (α ) ≤ Тб1,1д ;
торцевое биение контрольной поверхности i-го диска на j-ом радиусе
Тб (α ) ≤ Тб2,1д
;
( i ∈ N ). Согласно требованиям конструкторской документации 2,1(5)
величины торцевых биений контрольных поверхностей Тбi , j д2
Тбi , j (α ) ≤ Тбi , j ;
д
ремонтного ротора не должны превышать заданных значений:
где Тбi , j – допустимые значения торцевого биения Тбiд, j . Нахождение рациональных
угловых положений деталей, исходя из условий (4) с учетом ограничений (5), заданных в
конструкторской и технологической документации, является задачей многофакторной
многокритериальной оптимизации. Вторую подмодель необходимо использовать в случае,
если использование рациональных угловых положений деталей в роторе не позволяет
достичь заданной точности торцевых биений (3).
Для определения деталей, требующих ремонта, предлагается использовать
обобщённый коэффициент, который имеет следующий вид:K=i, j, p dbinorm
,j⋅ Ainorm
,k, (6)
где dbinorm
,j
– нормированный коэффициент, учитывающий влияние геометрических отклонений i-ой
детали на величину j-ого торцевого биения; Аinorm,k
– нормированный по отношению к величине
допуска коэффициент, учитывающий геометрические отклонение i-ой детали. Коэффициент dbinorm,j
рассчитываются по следующей формуле:
dbi , j − dbminгде dbi , j – коэффициент, учитывающий влияние геометрических
dbinorm=, (6)
dbmax − dbmin
,j
отклонений i-ой детали на j-ое торцевые биения узла ротора;
dbmax , dbmin – максимальное и минимальное значение из рассчитанных значений dbi . Коэффициент
dbi , j рассчитывается по следующей формуле:
Amax a = 2π
где Amax , Amin – соответственно максимальная и минимальная
∫ a∫Тбi , j dAi , j da i
величины амплитуд отклонений формы сопрягаемых
dbi =
Amin=0, (7)
nAmax a = 2π
поверхностей; α – угловое положение i-ой детали в роторе.
∑∫ ∫
i =1 Amin
Тбi , j dAi , j da i
Коэффициент Аinorm рассчитывается по формуле:
a=0
Аi , p − Аiномгде Аi , p – величина отклонения p-го геометрического параметра
А norm
=,p
,(8)
i-ой детали; Аiном
, p – величина середины поля допуска или
i
Ti , p
номинальноезначение p-ого
геометрического параметра i-ой
детали; Ti , p – допуск на p-ый
геометрический параметр i-ой
детали. Выбор ремонтных
деталейосуществляется
технологомисходяиз
максимальногозначения
обобщенного коэффициента в
порядке его убывания.
Впятомразделе
представленырезультаты
исследований торцевых биений
контрольныхповерхностей
дисков узла ротора КВД,
который состоит из четырех
ступеней.Исследования
содержалиразличные
сочетаниягеометрических
отклоненийповерхностей
деталейиихугловых
положенийвузле,
встречающихся в производстве.
Рисунок – 4 Блок схема последовательности исследований
Полученные данные разделены на две выборки: обучающую (95%) и тестовую (5%).
Заключение об удовлетворительном качестве модели получено с использованием
коэффициента детерминации, величина которого составила от 0.65 до 0.88.
Третья глава посвящена анализу взаимосвязей геометрической точности деталей и
торцевых биений роторов КВД при их сборке и ремонте.
В первом разделе приведено описание последовательности теоретико-экспериментальных
исследований, включающих три блока (рисунок 4). Первый блок предусматривает измерения
поверхностей деталей и обработку результатов. Второй блок включает расчёт торцевых биений и
определение условий сборки. Третий блок содержит сравнение теоретических и
экспериментальных исследований и формирование выводов. Была выполнена проверка
достоверности разработанных моделей. Измерения выполнялись на координатно-измерительной
машине (КИМ) DEA Global. Выполнялось две серии исследований.
Перваясериясодержитсравнение
рассчитанных и измеренных величин торцевых
биений контрольных поверхностей узла ротора
КВД на КИМ. Сборка узла выполнялась в пять
этаповдлядвухвариантов: совмещения
«нулевых» меток деталей, по существующей
технологии его ремонта; рационального углового
положения деталей с заменой промежуточного
кольца (ПК) 12-ой ступени, полученных с
помощью разработанных моделей. Измерялись
торцевые биения сопрягаемых и контрольных
поверхностей промежуточных колец, а также
дисков соответственно. Измерение контрольных
поверхностей узла ротора представлено на
рисунке 5. Торцевые биения, полученные
посредством измерения на КИМ и рассчитанные
спомощьюразработанныхмоделей,Рисунок 5 – Измерение узла ротора
представлены в таблице 1.КВД на пятом этапе
Таблица 1 – Результаты теоретико-экспериментальных исследований
Торцевые биения, ммАбсолютная
НаименованиеРассчитанныеИзмеренныепогрешность, мм
Этап
деталиРациональ-Рациональ-Рациональ-
«0»«0»«0»
ныеныеные
1ПК 10-й ступени0.03520.02350.05340.03350.01600.0100
2ПК 11-й ступени0.04750.02940.06510.04090.01760.0115
3Проставка0.05350.04000.07530.05800.02030.0180
4ПК 12-й ступени0.07070.05080.08930.07060.01860.0198
5ПК 13-й ступени0.1100.04110.10470.04800.00370.0069
В таблице 1 рассматриваются два варианта угловых положений: «0» – сборка узла
по нулевым меткам; «рациональные» – сборка узла по рациональным угловым
положениям, рассчитанным с помощью разработанных моделей при учёте замены ПК
12-й ступени. Решение о замене промежуточного кольца 12-й ступени принято, исходя из
величин обобщённых коэффициентов влияния геометрических отклонений деталей на
торцевые биения узла ротора КВД. Значения обобщенных коэффициентов влияния для
комплекта деталей узла ротора КВД представлены в таблице 2.
Таблица 2 – Обобщенные коэффициенты влияния
НомерДетали узла
дискаВалДиск 11ПроставкаПК 11 ТКДиск 12ПК 12Диск 13
10.690.950.8500.630.100.730.75
20.690.930.630.60.600.250.740.81
30.570.4510.290.520.660.670.54
40.620.510.850.340.520.730.600.54
Детали узла ротора КВД при сборке по второму варианту имеют следующие
угловые положения: ПК-11 – 1200; ПК-12 и проставка – 2400; Диск 13 – 1800. Угловые
положения остальных деталей равны нулевым. Полученные данные позволяют сделать
следующие выводы: расхождение между рассчитанными и измеренными величинами
торцевых биений составило не более 0.03 мм; рассчитанные угловые положения деталей
позволили снизить величины торцевых биений в 2 раза по сравнению со сборкой по
нулевым меткам.
Вторая серия исследований включала сравнение рассчитанных и измеренных
величин торцевых биений контрольных поверхностей четырёх роторов КВД при их сборке
в цеховых условиях. Сборка и измерение биений роторов КВД выполнялась по
существующей технологии при помощи имеющихся приспособлений. Определение
угловых положений деталей в роторе выполнялось
экспериментальным способом с использованием
предварительныхсборок.Проверялась
достоверность разработанных моделей при их
использовании в цеховых условиях. На рисунке 6
представленырасхожденияизмеренныхи
рассчитанных торцевых биений роторов, которые не
превысили 0.031 мм. Использование разработанных
моделей позволило повысить точность торцевых
биений ротора КВД на 0.02-0.05 мм путем изменения
угловых положений его деталей без выполнения
предварительных сборок. Полученные результаты Рисунок – 6 Результаты расхождения
позволяют сделать вывод об удовлетворительной измеренных и рассчитанных торцевых
сходимости разработанных моделей.биений роторов
Эффективность использования разработанных моделей в снижении трудоёмкости
технологических процессов сборки при ремонте ротора КВД оценивалась на основе
исходных данных, представленных в таблице 3.
Таблица 3 – Исходные данные
Сборка ротора с использованием:
Существующий ТПУлучшенный ТП
№Наименование операций(с использованием (с использованием
предварительныхпрограммного
сборок)приложения)
1Измерение 22-ух деталей ротора КВД на КИМ, час16.518.3
2Обработка результатов измерений, час–1
3Расчёт (поиск) условий сборки, час–0.25
4Анализ результатов, час–0.3
5Измерение сборочных параметров, час11
6Повторная сборка ротора с трактовыми кольцами, час1-
7Время сборки, час166
Итого, час33.526.85
Отличия, %24.7
Оценка эффективности не учитывает следующего: снижения вероятности снятия
изделий с испытаний по причине повышенной вибрации; исключения затрат на ремонт или
изготовление деталей, которые подлежат замене по результатам выполнения
предварительных сборок узла ротора КВД.
Из анализа можно сделать вывод, что использование разработанного программного
приложения позволяет сократить трудоёмкость технологических операций сборки ротора
КВД при его ремонте на 24.7%.
В четвертой главе представлена практическая реализация результатов
исследований в виде программного приложения и технологической инструкции.
Первый раздел главы содержит описание разработанного программного приложения
для определения условий выполнения сборки и ремонта ротора КВД на основе измерения
его деталей. Разработка программного приложения и его интерфейса выполнялась в
программе MATLAB.
Во втором разделе главы приведена технологическая инструкция, использование
которой в цеховых условиях позволяет повысить точность и снизить трудоёмкость сборки
роторов КВД при их ремонте за счёт управления производственным процессом.
Выводы и основные результаты работы
В работе представлено решение значимой научно-технической задачи,
направленной на определение условий выполнения сборки при ремонте ротора КВД,
путем создания методики, базирующейся на разработанных конечно-элементной и
математических моделях.
На основании выполненных исследований получены следующие результаты:
1. Разработана методика повышения технологических характеристик сборки при
ремонте ротора КВД её отличительной особенностью является использование
регрессионных моделей, описывающих взаимосвязь между геометрическими
отклонениями собираемых деталей и торцевыми биениями ротора КВД. Обучение
регрессионной модели предусмотрено с использованием данных, получаемых с помощью
параметризованной КЭМ ротора КВД.
2. Разработана параметризованная КЭМ узла ротора КВД авиационного двигателя,
отличающаяся от существующих использованием 3D моделей деталей с геометрическими
отклонениями торцевых и цилиндрических поверхностей задаваемых системой уравнений
с параметрами, а также возможностью учёта параллельных связей деталей в узле.
3. Разработана модель оценки торцевых биений ротора барабанно-дискового типа,
учитывающая параллельные связи по торцевым поверхностям его деталей. Погрешность
оценки торцевых биений узла ротора КВД авиационного двигателя не превысила 0.021 мм
при апробации в лабораторных условиях; 0.031 мм при апробации в цеховых условиях.
4. Разработана модель определения УВС и ремонта деталей ротора КВД.
Использование рациональных условий, рассчитанных с помощью названной модели,
позволило повысить технологические характеристики сборки ротора КВД при его ремонте:
снизить торцевые биения в 2 раза при сборке узла ротора КВД. Согласно существующей
технологии сборки ротора КВД выполняются предварительные сборки узла с целью
обеспечения заданной точности сборочных параметров. Количество предварительных
сборок составляет от 2 до 4. Использование разработанных моделей позволяет исключить
предварительные сборки узла ротора КВД, что снизит трудоёмкость выполнения
технологических операций сборки на 24.7%.
5. Выполнено исследование влияния отклонений формы торцевых и радиальных
поверхностей деталей ротора КВД на его биения с использованием разработанной КЭМ.
Отклонение формы торцевых поверхностей деталей является основным фактором,
влияющим на торцевые биения ротора КВД. Погрешность оценки торцевых биений узла
ротора без учета отклонений цилиндрических поверхностей составила не более 16%.
Данный вывод позволит упростить разработку моделей оценки торцевых биений дисков
узла ротора.
Таким образом, поставленная цель достигнута, работа может считаться
выполненной в полном объеме. Разработанное программное приложение позволяет
повысить точность торцевых биений при сборке ремонтных роторов КВД. Предложенные
методика и модели позволяют решать практические задачи для обеспечения заданной
точности сборочных параметров при сборке ремонтных роторов КВД, и предназначены
для использования сборщиками в цеховых условиях предприятий авиадвигателестроения.
Перспектива дальнейшего развития темы состоит в разработке модели определения
условий сборки всего ротора ВД.
Актуальность темы исследования. Одним из наиболее ответственных и важнейших этапов изготовления авиационных газотурбинных двигателей (ГТД) является этап сборки, оказывающий существенное влияние на геометрическую точность ротора компрессора высокого давления (КВД). Требуемая точность узлов достигается методами: неполной и групповой взаимозаменяемости, пригонки и регулирования. Используются предварительные сборки узла ротора КВД для определения условий выполнения сборочных операций в ходе его ремонта. В контексте данной работы под условиями выполнения сборки (УВС) понимается: требования к относительным угловым положениям деталей в узле; требования к размерам компенсационных деталей; выявление деталей, требующих замены или ремонта. Предварительные сборки узла приводят к увеличению трудоёмкости технологических операций и ухудшению качества деталей (появлению локального смятия, задиров, отклонений формы и расположения поверхностей). Исключение предварительных сборок узлов является резервом улучшения технологии сборки ГТД. Добиться этого возможно за счет оценки геометрии узлов по результатам измерений его деталей и принятия решений о корректировке технологического процесса сборки. К сборочным параметрам ротора ГТД относятся линейные размеры, радиальные и торцевые биения деталей, осевые, радиальные зазоры и др. Основным показателем точности геометрической оси ротора является значение его торцевых биений. Важным этапом является оценка сборочных параметров по результатам измерений. Особенностью ротора КВД является наличие в нём маложестких деталей и наличие параллельных размерных связей деталей по торцевым поверхностям. В роторах барабанно-дискового типа параллельные размерные связи ротора образованы сопряжением его деталей по нескольким торцевым поверхностям в осевом направлении. Данные обстоятельства существенно затрудняют разработку моделей, позволяющих оценивать сборочные параметры узлов ротора с необходимой достоверностью. Под технологическими характеристиками понимается трудоёмкость и точность сборки узлов. Актуальной задачей является разработка математических моделей оценки сборочных параметров узлов, позволяющих учитывать геометрию и жесткость деталей, а также наличие параллельных размерных связей в роторе.
В связи с этим тема диссертационной работы – повышение технологических характеристик процесса сборки при ремонте ротора КВД ГТД на основе разработки методики и моделей определения условий выполнения его ремонта является актуальной для современного авиадвигателестроения и соответствует заявленной специальности.
Степень разработанности темы.
Проблемами оценки и обеспечения точности технологического процесса сборки роторов ГТД занимались: Ф.И. Демин, А.С. Шевелев, И.А. Иващенко, В.В. Непомилуев, М.Е. Ильина, А.Н. Семенов, Е.В. Тимофеева, В.П. Тимофеева, А.А. Гарькавый, Ю.В. Ерошкова, В.А. Захарова, Е.А. Майорова, В.А. Иванов, K.W. Chase, X. Yan, A. Ballu, E. Boyer, J.A. Clementa и другие.
Представленными авторами сформирован существенный теоретический и практический задел в данной области исследований. Обзор опубликованных работ позволяет выделить ряд перспективных направлений в решении рассматриваемой проблемы: 1) учёт геометрических отклонений поверхностей деталей при выполнении размерных расчётов; 2) оценка сборочных параметров узлов роторов с учетом параллельных связей деталей по их торцевым поверхностям; 3) определение рациональных условий сборки роторов, исходя из минимизации погрешностей его сборочных параметров; 4) адаптация разработанных методик и моделей с целью их использования в цеховых условиях на предприятиях.
Исследование указанных направлений связано с необходимостью решения следующих задач: 1) разработка методики управления технологическим процессом ремонта ротора КВД на основе результатов измерений его деталей; 2) разработка моделей, позволяющих определять геометрические сборочные параметры ротора КВД на основе измерений их деталей; 3) разработка моделей для определения УВС при ремонте ротора КВД. Цель диссертационной работы. Снижение трудоёмкости и повышение точности сборки ротора КВД за счёт разработки методики и моделей, позволяющих рассчитывать торцевые биения, определять рациональные угловые положения деталей в узле, а также выявлять детали, требующие ремонта или замены.
Задачи исследования.
1. Разработать методику оценки точности и определения УВС при ремонте ротора КВД.
2. Разработать параметризованную конечно-элементную модель (КЭМ) сборки ротора КВД с параллельными размерными связями деталей.
3. Разработать модель оценки торцевых биений ротора КВД и реализовать ее в виде программного приложения.
4.Разработать модель определения УВС при ремонте ротора КВД и реализовать её в виде программного приложения.
5. Выполнить исследования влияния геометрических отклонений деталей на торцевые биения при ремонте ротора КВД.
6. Разработать технологическую инструкцию по сборке ремонтного ротора КВД на основе использования программного приложения.
Объект исследований. Технологический процесс сборки ремонтного ротора КВД ГТД.
Предмет исследований. Определение условий выполнения сборки ротора КВД в ходе его ремонта.
Методы и средства исследований. Решение поставленных задач выполнялось посредством математического и цифрового моделирования процесса сборки узла ротора КВД. При выполнении теоретических исследований использовался метод конечных элементов, метод регрессионного анализа с применением цифровой модели, теории вероятностей и математической статистики, теории подобия, линейной алгебры и аналитической геометрии, имитационного моделирования размерных цепей, метода Монте-Карло. Реализация разработанных моделей и алгоритмов выполнялась в системе MATLAB и NX. Выполнение экспериментальных исследований проводилось с использованием разработанного программного приложения, координатно- измерительной машины и специализированной оснастки на ремонтных роторах авиационных двигателей.
Научная новизна.
1. Предложена методика оценки точности и определения УВС при ремонте ротора КВД, отличительная особенность которой заключается в подготовке и использовании регрессионных моделей, описывающих взаимосвязь между отклонениями торцевых и цилиндрических поверхностей деталей и торцевыми биениями ротора.
2. Разработана модель оценки торцевых биений ротора КВД, отличающаяся от существующих учётом параллельных размерных связей деталей и сопряжений по нескольким торцевым поверхностям в осевом направлении.
3.Разработана модель определения УВС при ремонте ротора КВД, отличительная особенность, которой заключается в определении рациональных угловых положений деталей в узле и конкретных деталей, требующих доработки с целью обеспечения заданных величин торцевых биений.
4. Предложен обобщённый коэффициент, по величине которого принимается решение о ремонте или замене деталей комплекта узла, отличительной особенностью которого является учёт влияния их геометрических отклонений на торцевые биения узла ротора КВД.
Теоретическая значимость работы заключается в разработанной методике оценки точности и определения УВС при ремонте ротора КВД, а также в предложенных моделях: «Оценки торцевых биений ротора КВД» и «Определения условий выполнения сборки».
Практическая значимость результатов работы заключается в разработанной технологической инструкции, позволяющей снизить трудоёмкость и повысить точность технологического процесса сборки ротора КВД за счёт использования разработанного программного приложения в цеховых условиях.
Соответствие диссертации паспорту научной специальности 05.07.05 – Тепловые, электроракетные двигатели и энергетические установки летательных аппаратов. Соответствует п. 9 – Теоретические основы и технологические процессы изготовления деталей двигателей и агрегатов летательных аппаратов, включая технологическую подготовку производства, в том числе автоматизированные системы проектирования и управления, технологические процессы и специальное оборудование для формообразования и обработки деталей двигателей, их защита. Работа направлена на совершенствование технологического процесса сборки КВД ГТД за счёт расчёта торцевых биений и определения условий выполнения его сборки и ремонта. Предложена методика и модели для реализации программной системы, позволяющей формировать рекомендации по сборке ротора на основе измеренных сопрягаемых поверхностей его деталей. Теоретические и практические результаты работы могут быть использованы в цеховых условиях при ремонте ротора КВД для определения условий его сборки и достижения заданной точности. Полученные практические результаты позволяют повысить точность и снизить трудоемкость технологического процесса сборки при ремонте ротора КВД ГТД.
На защиту выносятся следующие положения:
1. Методика оценки точности и определения условий выполнения сборки при ремонте ротора КВД.
2.Параметризованная КЭ модель сборки ротора КВД с параллельными размерными связями деталей.
3. Модель оценки торцевых биений ротора КВД на основе результатов измерения деталей, реализованная в программном приложении.
4. Модель определения УВС при ремонте ротора КВД, реализованная в программном приложении.
5. Обобщённый коэффициент, учитывающий влияние геометрических отклонений деталей на величину торцевого биения узла ротора КВД, по величине которого принимается решение о ремонте или замене комплекта деталей.
Достоверность результатов обеспечивается обоснованностью принятых допущений в математических моделях; применением известных и проверенных численных методов, обладающих высокой точностью, при проведении вычислительных экспериментов; использованием в процессе исследований поверенного метрологического оборудования и сертифицированного программного обеспечения; высокой сходимостью результатов теоретических и экспериментальных исследований.
Апробация работы. Основные положения работы докладывались на всероссийских и международных конференциях, в том числе: на Всероссийской научно-технической конференции «Актуальные проблемы ракетно-космической техники», г. Самара, Самарский университет, с 30 сентября по 03 октября 2019г.; на Международной научно-технической конференции «Информационные технологии и нанотехнологии» ИТНТ-2019 и ИТНТ-2020, г. Самара, Самарский университет, 21-24 мая 2019г. и 26-29 мая 2020г.; на Международной научно- практической конференции, посвященной памяти генерального конструктора ракетно-космических систем академика М. Ф. Решетнева, г. Красноярск 11-15 ноября 2019г.; на Международной мультидисциплинарной конференции по промышленному инжинирингу и современным технологиям FarEastCon-2019 и FarEastCon-2020, г. Владивосток, Дальневосточный федеральный университет, остров Русский, 1-4 октября 2019г. и 6-9 октября 2020г.; на Международной конференции MIST: Aerospace-III 2020 (Передовые технологии в аэрокосмической отрасли, машиностроении и автоматизации), г. Красноярск, Красноярский Дом Науки и Техники, 20-21 ноября 2020г.; на Международной конференции MIP: Engineering-II 2020 (Модернизация, Инновации, Прогресс: Передовые технологии в материаловедении, машиностроении и автоматизации) г. Красноярск, Красноярский Дом Науки и Техники, 16-18 апреля 2020г. Получены документы: свидетельства о государственной регистрации программ для ЭВМ «Программное обеспечение для повышения качества изделий посредством создания и использования их цифровых двойников» No2020618796 от 4 августа 2020 г., «Программный модуль для расчета параметров сопряжения реальных поверхностей собираемых деталей», No2020618835 от 05 августа 2020 г. и «Программный модуль для формирования действительных поверхностей деталей», No2020662039 от 07 июля 2020 г.; патент на изобретение «Устройство для автоматизированного контроля соосности и центровки механических конструкций» No2639993 от 25.12.2017 г.
Реализация результатов работы. Исследование выполнено при финансовой поддержке РФФИ в рамках научного проекта No 19-38-90263.
Публикации. По теме диссертации опубликовано 16 научных работ, в том числе 2 статей в периодических изданиях, включенных в перечень ВАК России, и 9 статей в изданиях, индексируемых в базе данных Scopus.
Структура и объём работы. Диссертационная работа состоит из введения, четырех глав, заключения, списка литературы (включающего 125 наименований) и одиннадцать приложений. Общий объём диссертации составляет 169 страниц, 67 рисунков и 19 таблиц.
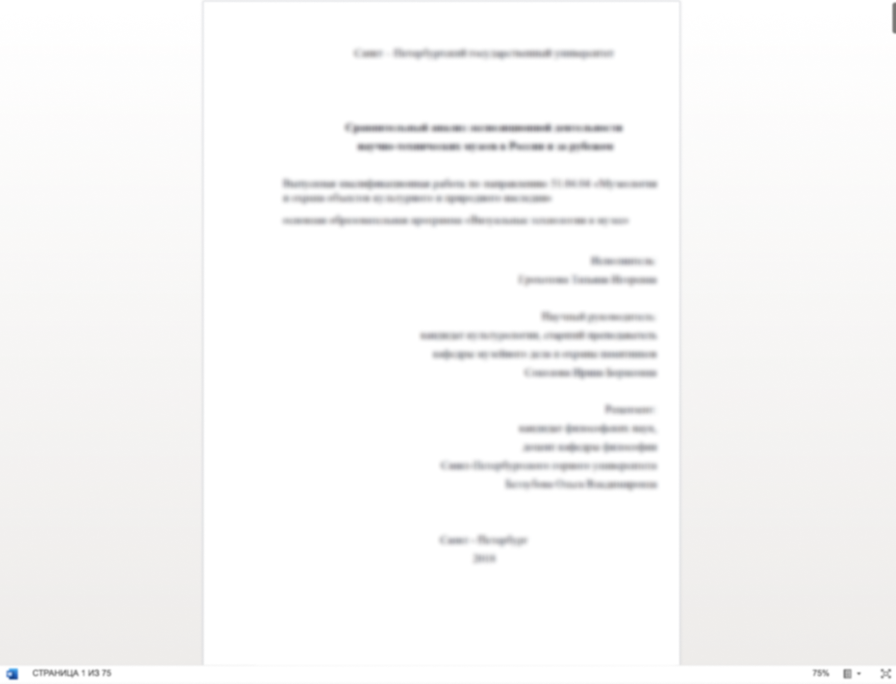
Публикации автора в научных журналах
Помогаем с подготовкой сопроводительных документов
Хочешь уникальную работу?
Больше 3 000 экспертов уже готовы начать работу над твоим проектом!