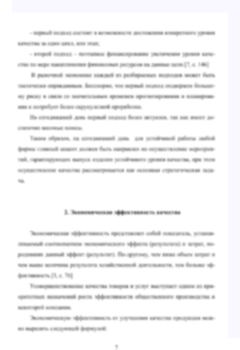
Разработка порошковых алюмоматричных композиционных материалов для газодетонационного напыления антифрикционных покрытий
Введение……………………………………………………………………………………… 5
ГЛАВА 1. Состояние вопроса получения антифрикционных покрытий тяжелонагруженных изделий ………………………………………………… 15 1.1 Антифрикционные покрытия …………………………………………………. 15 1.1.1 Углеродсодержащие покрытия …………………………………….. 17 1.1.2 Многофазные нанокомпозицонные покрытия……………….. 22 1.1.3 Твердые смазки ……………………………………………………………. 23 1.1.4 Пластичные металлы как твердые смазки …………………….. 26
1.1.5 Прочие материалы, используемые для создания
антифрикционных покрытий ………………………………………………… 27 1.2 Способы создания покрытий с особыми свойствами ………………. 30 1.2.1 Физическое газофазное осаждение покрытий ……………….. 30 1.2.2 Химическое газофазное осаждение покрытий ………………. 31 1.2.3 Метод наплавки электронными пучками ………………………. 32 1.2.4 Плазменная наплавка……………………………………………………. 33 1.2.5 Гибридная технология наплавки …………………………………… 34
1.2.6 Дуговая наплавка плавящимся и неплавящимся электродом …………………………………………………………………………… 35 1.2.7 Электроискровое легирование ……………………………………… 35 1.2.8 Лазерная наплавка ……………………………………………………….. 36 1.2.9 Детонационное напыление …………………………………………… 37 1.2.10 Плазменное напыление ………………………………………………. 37 1.2.11 Прочие способы создания покрытий …………………………… 38
1.3 Конструкторские и эксплуатационные особенности
поршня двигателя внутреннего сгорания ………………………………………………. 39 1.4 Выводы по главе…………………………………………………………………….. 48 ГЛАВА 2. Материалы и методы исследования …………………………….. 51
3
2.1 Оборудование для газодетонационного напыления по-
крытий …………………………………………………………………………………………………. 51 2.1.1 Сущность способа газодетонационного напыле- ния……………………………………………………………………………………….. 51 2.1.2 Экспериментальная установка газодетонационно-
го напыления «Катунь М», ее отдельные узлы и систе-
мы ……………………………………………………………………………………….. 57 2.2 Материалы для создания покрытий ………………………………………… 65 2.3 Подготовка порошков. Механоактивационная обработка
порошковых смесей ……………………………………………………………………………… 66 2.4 Методы исследования порошковой композиционной
смеси и покрытий …………………………………………………………………………………. 70 2.4.1 Оптическая микроскопия ……………………………………………… 70 2.4.2 Растровая электронная микроскопия…………………………….. 71 2.4.3 Рентгенофазовый анализ ………………………………………………. 72 2.4.4 Износостойкость и антифрикционность ……………………….. 72 2.4.5 Топография поверхности покрытия………………………………. 73 2.4.6 Методика моделирования процесса движения композиционной смеси в двухфазном потоке газодето- национной установки …………………………………………………………… 73
2.5 Выводы по главе…………………………………………………………………….. 74
ГЛАВА 3. Структурные исследования алюмоматричных композиционных материалов с углеродными компонентами…………………. 76
3.1 Исследование структурного состояния композиционной порошковой смеси состава «алюминий – углерод» после механи-
ческой активации………………………………………………………………………………….. 76
3.2 Исследование структурного состояния композиционной порошковой смеси состава «алюминий – фуллерен» после меха- нической активации ……………………………………………………………………………… 84
4
3.3 Исследование структурного состояния композиционной
порошковой смеси состава «алюминий – углерод/фуллерен – кар-
бид бора» после механической активации …………………………………………….. 88 3.4 Выводы по главе…………………………………………………………………….. 95
ГЛАВА 4. Газодетонационное напыление алюмоматричных композиционных материалов с углеродными структурами. Мор-
фология и свойства покрытий……………………………………………………………….. 98
4.1 Моделирование процесса движения напыляемых частиц
в стволе установки ……………………………………………………………………………….. 98
4.2 Оптическая микроскопия газодетонационных покрытий ………… 114
4.3 Растровый электронный анализ газодетонационных по-
крытий …………………………………………………………………………………………………. 118 4.4 Рентгенофазовый анализ покрытий ………………………………………… 125 4.5 Анализ поверхности газодетонационных покрытий………………… 131 4.6 Выводы по главе…………………………………………………………………….. 133
ГЛАВА 5. Триботехнические испытания и апробация ре-
зультатов экспериментальных исследований ………………………………………… 137
5.1 Исследование антифрикционных и износостойких
свойств газодетонационных покрытий ………………………………………………….. 137
5.2 Газодетонационное напыление рабочих поверхностей
поршня ДВС транспортного средства «Поларис» ………………………………….. 142
5.3 Рекомендации по газодетонационному напылению ан- тифрикционных покрытий поршня ДВС……………………………………………….. 144 5.4 Выводы по главе…………………………………………………………………….. 147 Заключение …………………………………………………………………………………. 149 Список использованных источников ……………………………………………. 152
Приложение А – Акт внедрения результатов диссертацион-
ной работы …………………………………………………………………………………………… 172
При эксплуатации машины ее детали, узлы и агрегаты так или иначе подвергаются трению и, в дальнейшем – износу. Это приводит к уменьшению эффективности работы трибосопряжений и существенным энергетическим потерям во время эксплуатации. В современной технике необходимо приме- нять более прогрессивные материалы при изготовлении трущихся пар. Это обусловлено ростом удельных нагрузок, которым подвергаются изделия, увеличением скоростей перемещения трибопар друг относительно друга, необходимостью эксплуатации машин в агрессивной среде и при повышен- ных температурах. В связи с этим достаточно актуален вопрос увеличения надежности трибопар, повышения их долговечности и уменьшения энергоза- трат, расходуемых на трения. Потери на трение в современных машинах и оборудовании достигают 30 % потребляемой ими энергии, а расходы на устранение последствий их износа в развитых промышленных странах со- ставляют до 2 % валового национального продукта.
Для снижения затрат на трение разработаны и успешно применяются различные покрытия, начиная от износостойких с керамической основой и заканчивая композиционными на основе металлокерамики. Области их при- менения достаточно обширны, но при контакте в режиме сухого трения, по- добные покрытия обладают высоким коэффициентом трения. Это приводит к значительным энергетическим затратам и нежелательному местному нагреву в области контакта трибосопряжения. Помимо этого, из-за высокого коэффи- циента трения в этом случае существенно возрастает износ трибопары.
Надежность и долговечность большинства изделий современной тех- ники в значительной степени зависит от работоспособности и срока службы многочисленных узлов трения (трибосистем) различных систем и механиз- мов машин и их агрегатов. Процессы разрушения деталей машин в подавля-
6
ющем большинстве случаев начинаются с поверхностных зон. В связи с этим огромную значимость носят работы по разработке принципиально новых ан- тифрикционных материалов, в том числе покрытий с антифрикционными свойствами, которые бы обеспечивали бесперебойную работу тяжелонагру-
женных изделий.
На наш взгляд, при стремительном развитии автомобильной и гусенич-
ной техники, в том числе и специального назначения, особое внимание стоит уделять разработке антифрикционных покрытий, которые бы способствовали бесперебойной работе всех узлов и агрегатов. Например, особенностью экс- плуатации автомобильного двигателя является частое и, в некоторых случа- ях, резкое изменение скоростного и нагрузочного режимов, поэтому к авто- мобильным двигателям внутреннего сгорания (ДВС) предъявляются высокие требования. Анализ комплексных потерь энергии в двигателе внутреннего сгорания показывает, что для дальнейшего повышения эффективности ис- пользования топлива необходимо максимально снизить потери энергии, обу- славливаемые трением, износом и соударением деталей двигателя в процессе его работы.
Сопоставление балансов механических потерь автотракторных ДВС показывает, что наибольшие потери энергии (от 45 до 60 %) происходят в цилиндро-поршневой группе. На поршень двигателя внутреннего сгорания действуют значительные нагрузки – как механические, так и тепловые, например, перезагрузка в процессе работы достигает величин в 1500-2000g, а температура рабочей смеси может составлять 1800-2600 °С. В связи с этим, условия эксплуатации поршня ДВС являются очень сложными.
Исходя из вышеизложенного, разработка новых видов антифрикцион- ных материалов, в том числе покрытий, предназначенных для обеспечения бесперебойной работы тяжелонагруженых деталей, является крайне актуаль- ной задачей.
7
Актуальность диссертационного исследования определяется необхо-
димостью разработки новых составов для формирования износостойких ком- позиционных покрытий с низким коэффициентом трения, а также установле- ния корреляции между структурой сформированных покрытий и их свой- ствами.
Актуальность темы диссертации подтверждается также тем, что часть исследований выполнялись в рамках государственного Задания No 11.1085.2017/4.6 на НИОКР Министерства образования и науки Российской Федерации.
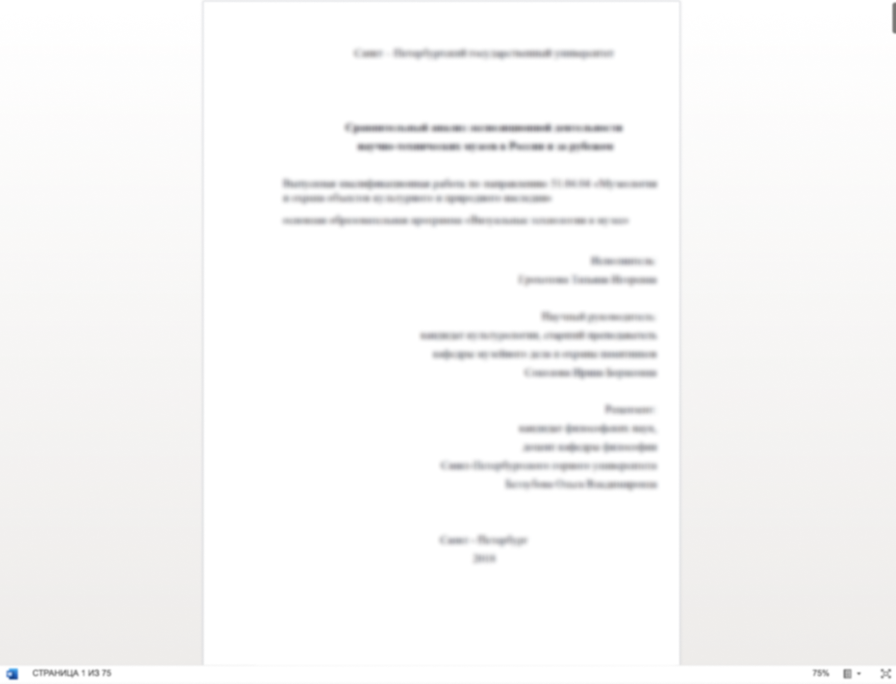
Помогаем с подготовкой сопроводительных документов
Хочешь уникальную работу?
Больше 3 000 экспертов уже готовы начать работу над твоим проектом!