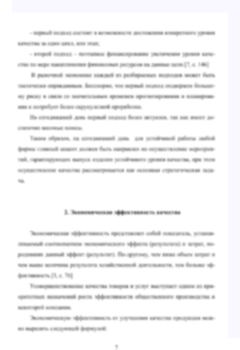
Разработка технологии получения гранулированного алюмооксидного носителя для катализаторов изомеризации углеводородов
ВВЕДЕНИЕ ………………………………………………………………………………………………………. 5
1 ЛИТЕРАТУРНЫЙ ОБЗОР ……………………………………………………………………………. 14
1.1 Физико-химические основы процесса изомеризации углеводородов ………… 14
1.1.1 Равновесие процесса изомеризации углеводородов ……………………………. 14
1.1.2 Механизмы и кинетика процесса изомеризации углеводородов ………….. 16
1.2 Катализаторы процесса изомеризации углеводородов ……………………………… 19
1.2.1 Структура и свойства носителей катализаторов изомеризации …………… 23
1.2.2 Промышленные катализаторы изомеризации углеводородов ……………… 25
1.3 Структура, свойства и получение активных оксидов алюминия ……………….. 28
1.4 Гидроксиды алюминия – предшественники γ- и η- активных оксидов
алюминия …………………………………………………………………………………………………….. 32
1.4.1 Кристаллическая структура и методы получения псевдобемита …………. 33
1.4.2 Кристаллическая структура и методы получения байерита ………………… 34
1.5 Реологические аспекты получения гранулированных носителей ……………… 36
Заключение к главе 1 ………………………………………………………………………………………. 41
2 ЭКСПЕРИМЕНТАЛЬНАЯ ЧАСТЬ: МЕТОДИЧЕСКОЕ ОБЕСПЕЧЕНИЕ
ИССЛЕДОВАНИЯ ………………………………………………………………………………………….. 43
2.1 Получение образцов гидроксида алюминия – байерита ……………………………. 43
2.2 Приготовление гранулированных образцов η-Al2O3-носителя ………………….. 45
2.3 Исследование физико-химических свойств образцов гидроксида и оксида
алюминия …………………………………………………………………………………………………….. 47
2.4 Изучение свойств формовочных паст ………………………………………………………. 51
2.5 Определение функции кислотности поверхности синтезированных образцов
носителей …………………………………………………………………………………………………….. 52
2.6 Исследование структурно-прочностных свойств гранулированных носителей
…………………………………………………………………………………………………………………….. 54
2.7 Тестирование синтезированных образцов носителей в модельном процессе
изомеризации н-бутана …………………………………………………………………………………. 56
3 ОБОСНОВАНИЕ ВЫБОРА УСЛОВИЙ ОСАЖДЕНИЯ ГИДРОКСИДА
АЛЮМИНИЯ – БАЙЕРИТА ИЗ ВОДНОГО РАСТВОРА НИТРАТА
АЛЮМИНИЯ …………………………………………………………………………………………………. 60
3.1 Влияние условий синтеза на фазовый и химический составы осажденного
гидроксида алюминия и получаемого из него оксида алюминия ……………………. 61
3.2 Результаты ИК-спектроскопического анализа синтезированных порошков
байерита и η-Al2O3 ……………………………………………………………………………………….. 79
3.3 Анализ дисперсного состава синтезированных порошков байерита и η-Al2O3
…………………………………………………………………………………………………………………….. 81
3.4 Исследование характеристик алюмогидроксидного связующего –
псевдобемита ……………………………………………………………………………………………….. 82
4 РАЗРАБОТКА СПОСОБОВ ФОРМОВАНИЯ БАЙЕРИТА И
РЕГУЛИРОВАНИЯ ТЕКСТУРЫ И ПРОЧНОСТИ ЭКСТРУДАТОВ ……………….. 86
4.1 Изучение реологических свойств формовочных паст для экструдирования 86
4.1.1 Формовочные пасты на основе свежеосажденного гидроксида алюминия
– байерита …………………………………………………………………………………………………. 86
4.1.2 Формовочные пасты на основе порошка гидроксида алюминия –
байерита ……………………………………………………………………………………………………. 90
4.1.3 Формовочные пасты из порошков синтезированных гидроксида или
оксида алюминия и псевдобемита в качестве связующего ………………………….. 92
4.2 Влияние условий приготовления гранулированного η-Al2O3-носителя на его
кислотно-основные и структурно-прочностные свойства ………………………………. 97
4.3 Исследование распределения объема пор по их размерам на основании
анализа изотерм адсорбции-десорбции азота гранулированных носителей ….. 101
4.4 Исследование гранулированных носителей в процессе изомеризации н-
бутана ………………………………………………………………………………………………………… 110
4.5 Принципиальная технологическая схема получения гранулированного
алюмооксидного носителя и оценка эффективности разработанной технологии
…………………………………………………………………………………………………………………… 113
ЗАКЛЮЧЕНИЕ …………………………………………………………………………………………….. 118
СПИСОК ИСПОЛЬЗОВАННОЙ ЛИТЕРАТУРЫ …………………………………………… 122
ПРИЛОЖЕНИЕ А Акт о наработке опытных партий алюмооксидных носителей
……………………………………………………………………………………………………………………… 142
ПРИЛОЖЕНИЕ Б Технологическая инструкция на процесс изготовления
опытных партий алюмооксидных носителей ………………………………………………….. 144
Во введении обоснована актуальность диссертационной работы, а именно получение
гранулированного η-Al2O3-носителя для катализаторов изомеризации углеводородов, сформулированы цель и задачи работы, отражены научная новизна, теоретическая и практическая значимость, сформулированы основные положения, выносимые на защиту.
В первой главе, являющейся обзором научной литературы, обосновывается перспективность разработок технологий производства катализаторов изомеризации и носителей для них. Рассмотрены вопросы термодинамики и механизма реакций изомеризации н-алканов, основные промышленные процессы и катализаторы изомеризации парафинов. Проведен анализ данных о носителях катализаторов изомеризации. Особое внимание уделено методам получения и свойствам активных модификаций оксида алюминия, в частности γ- и η-Al2O3, и свойствам их гидроксидов-предшественников – бемита/псевдобемита и байерита, соответственно. Отмечена актуальность использования η-Al2O3 в качестве носителя катализаторов изомеризации углеводородов в связи с большей удельной поверхностью и более высокой кислотностью поверхности по сравнению с γ-Al2O3. Проанализированы литературные данные, касающиеся реологических аспектов получения гранулированных носителей и способов регулирования свойств формовочных паст в технологии гранулированных носителей.
Во второй главе представлены методики получения гидроксида алюминия – байерита и гранулированных η-Al2O3-носителей, а также описание методов исследования их свойств.
С целью получения осадков байерита чистого как в фазовом отношении, так и в отношении примесей натрия и железа (ввиду существования жестких ограничений по данному показателю: не более 0.02%масс. для носителей катализаторов изомеризации), образцы гидроксида алюминия были синтезированы с использованием водных растворов нитрата алюминия и аммиака. Известно, что для образования тригидроксида алюминия байеритной структуры методом осаждения благоприятны следующие условия: высокое значение рН реакционной среды (10 – 11), низкие температуры реакционной среды (преимущественно 10 – 20 0С), продолжительное старение в щелочных маточных растворах. Температурно-временные условия осаждения гидроксида алюминия приведены в таблице 1.
Гранулированные η-Al2O3-носители были приготовлены термообработкой при (500 ± 10) 0С в течение 4часов предварительно высушенных при (110±10)0С до постоянства массы экструдатов, полученных из формовочных паст различного состава.
Для получения формовочных паст использовали как свежеосажденные осадки гидроксида алюминия – байерита, так и его порошки. В качестве свежеосажденных осадков гидроксида алюминия – байерита (Ба) использовали образцы с максимальным содержанием байерита, полученные их отмывкой и отжатием на фильтре. Порошки байерита (Ба(п)) получали высушиванием при температуре (110 ± 10) 0С до постоянной массы свежеосажденных осадков гидроксида алюминия – байерита.
В связи с тем, что осадки, содержащие байерит, плохо поддаются формовке методом экструзии, свойства формовочных паст регулировали изменением их влажности за счет разной степени отжатия на фильтре свежеосажденных осадков гидроксида алюминия – байерита; изменением свойств дисперсной фазы введением в формовочную пасту порошка оксида алюминия (η-Al2O3), полученного термообработкой порошка байерита при (500 ± 10) 0С, и использованием в качестве алюмогидроксидного связующего порошка псевдобемита (ПБ); изменением свойств дисперсионной среды введением в формовочную пасту в качестве пластификатора водорастворимого поверхностно-активного вещества – поливинилового спирта (ПВС) и кислоты-пептизатора – азотной кислоты (HNO3). В работе были приготовлены пять серий гранулированных образцов η-Al2O3-носителя. Характеристики составов формовочных паст, приготовленных для гранулирования алюмооксидных носителей приведены в таблице 2.
Для изучения свойств полученных образцов в работе использовались современные физико- химические методы исследования: рентгенофазовый анализ (РФА), дифференциальный термический (ДТА) и термогравиметрический анализы (ТГА), дисперсный анализ, атомно-эмиссионную спектроскопию с индуктивно-связанной плазмой ((ICP-AES).
Таблица 1 – Температурно-временные условия осаждения образцов гидроксида алюминия и результаты определения их фазового состава
No образца
Фазовый состав по данным ТГА, %масс. байерит псевдобемит аморфная фаза
τосаждения, час
1 0,5 – – –
τстарения, час
tосаждения(старения) = (10 ± 1) 0С
21
3 1,5 0** 42 53 64
7 2
8 2
9 0,5 – – –
2 24 48
10 1
11 1,5 0** 122 133 144
15 2
16 2
40 33 27 55 25 20 65 19 16 57 23 20 53 27 20 70 17 13
80 13 7 tосаждения(старения) = (20 ± 1) 0С
2 24 48
42 37 21 57 29 14 70 228 60 26 14 55 31 14 75 18 7
85 15 0
*все образцы были получены при рН реакционной среды равном 10,5 ± 0,1 **образцы, полученные без старения
Таблица 2 – Характеристики формовочных паст при получении гранул носителей
Состав, %масс. по Al2O3 μк,
моль Образец ПБ HNO3/
кг Al2O3
ПВС, %масс. по отношению к гидроксиду алюминия
Влажность* Ф, %масс.
82,6 78,6 60,9
56,7
54,5 52,0 51,0 47,0
Ба
Ба(п)
η-Al2O3
Формовочные пасты на основе свежеосажденного гидроксида алюминия – байерита Ба–Ф1
Ба–Ф2 100 – – – – – Ба–Ф3
Формовочные пасты на основе порошка гидроксида алюминия – байерита Ба–1,0ПВС 1,0 Ба–1,5ПВС – 100 – – – 1,5
Ба–2,7ПВС Ба–3,5ПВС
Ба80–η20–1,5ПВС
Ба60–η40–1,5ПВС – 60 – 40 – 1,5 Ба40–η60–1,5ПВС 40 60
Ба20–η80–1,5ПВС 20 80
2,7
3,5 Формовочные пасты на основе порошков байерита и η-Al2O3
80 20
Формовочные пасты на основе порошков гидроксидов алюминия – байерита и псевдобемита
Ба80–ПБ20 Ба80–ПБ20–1,5ПВС Ба80–ПБ20–HNO3
компонентов формовочной пасты
20
–
– –
1,5 56,8
–
Формовочные пасты на основе порошков псевдобемита и η-Al2O3
0,017 –
ПБ20–η80 ПБ20–η80–1,5ПВС ПБ20–η80–HNO3
–
–
20 80
– –
1,5 47,5
0,017 –
*отношение суммарной массы воды, содержащейся в каждом компоненте, к сумме масс всех
7
РФА проводили с помощью многофункционального рентгеновского дифрактометра «Rigaku SmartLab 3» (Rigaku Corporation, Япония)1 с использованием CuKα-монохроматического излучения в интервале углов (10–80)0 (2Θ) со скоростью сканирования 100/мин. Расшифровка рентгенограмм выполнена с помощью программного обеспечения дифрактометра.
ДТА и ТГА проводили на дериватографе «Shimadzu DTG-60H» (Shimadzu, Япония)1 в атмосфере воздуха при скорости нагревания 10 0/мин от комнатной температуры до 800 0С. Количественно фазовый состав образцов гидроксида алюминия определяли, исходя из наблюдаемых потерь массы в результате термолиза соединений, входящих в состав образцов. Разность масс исходной навески высушенного образца и суммы масс кристаллических фаз относили к аморфной фазе.
Дисперсный состав порошков определяли методом лазерного рассеивания на анализаторе размеров частиц SALD-2201 Laser Diffraction Particle Size Analyzer (Shimadzu, Япония)2 с излучением твердотельного лазера и диапазоном частиц от 10 нм до 5000 мкм при предварительном ультразвуковом диспергировании.
ICP-AES проводили на спектрометре OPTIMA 4300 DV (Perkin Elmer, США)3.
Реологические характеристики формовочных паст определяли на ротационном вискозиметре РЕОТЕСТ–2 при помощи конусно-пластиночных измерительных устройств.
Изотермы адсорбции/десорбции азота и исследования распределения объема пор по их размерам проводили методом азотной порометрии при 77К с использованием установки «Autosorb 6iSA» (Quantachrome Instruments, США)2 после дегазации образцов в вакууме при 250 0C в течение 1 часа. Удельная поверхность, удельный объём пор (заполнение пор адсорбатом при его относительном давлении ≈ 1) и средний эффективный размер пор определялись методом теории функционала плотности (DFT).
Исследование кислотно-основных свойств поверхности носителей проводили методом рН- метрии.
Значения механической прочности образцов носителей на раздавливание «по образующей» (P○) и «по торцу» (P□) определяли на экстензометре МП-2С в воздушной атмосфере при комнатной температуре.
Суммарный объем пор (V∑) образцов носителей определяли по пикнометрической жидкости – воде.
Объем сорбирующих пор (WS) предварительно дегидратированных при (250 ± 10) 0С образцов носителей определяли адсорбцией паров воды при Р/Рs = 0,99 в статических условиях.
Удельную поверхность (Sуд) образцов носителей определяли по тепловой десорбции азота по одноточечному методу Брунауэра–Эммета–Теллера (БЭТ) с использованием хроматографического анализа.
Каталитические испытания образцов носителей в тестовой реакции изомеризации н-бутана3 проводили в проточном реакторе со стационарным слоем катализатора при атмосферном давлении, температуре 150 0С, с мольным отношением Н2:н-бутан, равным 1.
В третьей главе представлены результаты исследований фазового и химического состав синтезированных осадков гидроксида алюминия и получаемого из него оксида алюминия и алюмогидроксидного связующего псевдобемита, использованных затем для приготовления формовочных паст.
Анализ результатов РФА показал, что проведение процесса осаждения в условиях эксперимента (таблица 1) приводит к образованию смеси различных модификаций гидроксида алюминия, при этом все осадки содержали кристаллические фазы байерита и бемита. Типичные рентгенограммы образцов полученных осадков приведены на рисунке 1.
На представленных рентгенограммах (рисунок 1) видно, что с увеличением времени осаждения до 2 часов наблюдается рост интенсивности байеритных рефлексов. Образец 12 отличается высокой степенью совершенства рефлексов, что свидетельствует о меньшей аморфизованности осадка. Дальнейшее увеличение длительности процесса осаждения не приводит к качественному изменению фазового состава осадков: на рентгенограммах сохраняются рефлексы бемита и байерита. Отмечено, что размер ОКР байерита независимо от времени осаждения практически остается неизменным (~ 17 нм). Это можно объяснить формированием байерита по механизму ориентированного наращивания, выдвинутому Р.А. Буяновым и О.П. Криворучко. Данный механизм предполагает образование первичной
1 Исследования выполнены в лаборатории Инжинирингового центра СПбГТИ(ТУ)
2 Исследования выполнены в лаборатории «Каталитические технологии» СПбГТИ(ТУ) 3 Исследования выполнены в ООО «НПФ «ОЛКАТ»
частицы, в результате перестройки полимерной структуры которой образуется зародыш кристаллической фазы. Далее путем перестройки полимерной структуры зародыша за счет протекания реакций дегидратации образуются центры кристаллизации. Вторичные кристаллы образуются за счет ориентированного наращивания зародышей на центрах кристаллизации с образованием мозаичной структуры.
Рисунок 1 – Рентгенограммы образцов 9 – 14 (* – бемит, ♦ – байерит), полученных при температуре (20 ± 1) 0С в течение различного времени осаждения (9 – 0,5 часа; 10 – 1 час;
11 – 1,5 часа; 12 – 2 часа; 13 – 3 часа; 14 – 4 часа)
Методами ДТА и ТГА проведена количественная оценка содержания кристаллических фаз в полученных осадках (таблица 1). Согласно выполненным расчетам, основной кристаллической фазой в
синтезированных осадках является байерит. Причем, во всех осадках обнаружена и псевдобемитная составляющая, характеристические рефлексы которой по данным РФА идентифицируются как фаза бемита.
Данные таблицы 1 показывают, что в рассматриваемом диапазоне температур проведения процесса осаждения, содержание байерита в полученных осадках достигает максимального значения при времени осаждения 2 часа и составляет 65 – 70 %масс. Отмечено, что повышение температуры реакционной среды от 10 до 200С сопровождается ростом содержания байерита и примесного псевдобемита при одновременном снижении количества аморфной составляющей.
Раннее был сделан вывод о том, что кристаллизация байерита протекает по механизму ориентированного наращивания, что предполагает образование первичных частиц. Состав первичных частиц определяется природой исходных форм полиядерных гидроксокомплексов, от строения ближнего порядка которых зависит направление фазовых превращений при кристаллизации осадков.
По литературным данным при растворении соли алюминия в водной среде образуются катионы алюминия, которые координируются шестью молекулами воды, образуя Al(H2O)63+. Проведение процесса осаждения в условиях эксперимента (таблица 1) приводит к формированию ионов вида Al2(OH)2(H2O)84+, которые полимеризуются в полигидроксокомплексы двух видов: Al13O4(OH)24(H2O)127+ и Al7O2(OH)14(H2O)103+. Известно, что аморфные гидроксиды наследуют структуру исходных форм полигидроксокомплексов и от строения их ближнего порядка зависит направление фазовых превращений при старении осадков. Так, первичные частицы, полученные из Al13O4(OH)24(H2O)127+, должны кристаллизоваться в форме байерита; из Al7O2(OH)14(H2O)103+ может кристаллизоваться гидроксид алюминия только псевдобемитной морфологии.
Таким образом, образование байерита протекает по следующей схеме:
Al(NO3)3 → Al(H2O)63+ ↔ Al2(OH)2(H2O)84+ ↔ Al13O4(OH)24(H2O)127+ → первичная частица → центр
кристаллизации → вторичный кристалл
Исходя из предложенной схемы, наблюдаемое увеличение содержания псевдобемита и
уменьшение содержания байерита при проведении процесса осаждения более 2 часов предположительно можно объяснить следующим образом. В процессе осаждения по истечении определенного времени ввиду старения раствора нитрата алюминия уменьшается количество образующихся полигидроксокомплексов вида Al13O4(OH)24(H2O)127+ по сравнению с Al7O2(OH)14(H2O)103+. Это ведет к снижению количества образующихся первичных частиц байерита и, следовательно, центров кристаллизации.
Данные о проведении процесса старения синтезированных осадков в течение 2, 24 и 48 часов приведены в таблице 1 и на рисунке 2.
На рентгенограммах, приведенных на рисунке 2, идентифицированы рефлексы байерита и бемита и обнаружено, что увеличение длительности старения приводит к росту интенсивности байеритных рефлексов.
Количественная оценка содержания кристаллических фаз в продуктах старения осадков с максимальным содержанием байерита показала, что с увеличением времени старения осадков содержание байерита в них возрастает, а количество псевдобемитной и аморфной составляющей уменьшается. При этом независимо от температуры, процесс старения во всех случаях имел одинаковую динамику. Таким образом показано, что максимальный выход байерита при температуре (10 ± 1) 0С достигает 75 %масс. и 85 %масс. при (20 ± 1) 0С за время осаждения и старения 2 и 24 часа, соответственно. Полученные данные подтверждают концепцию, согласно которой псевдобемит является промежуточным продуктом при кристаллизации байерита.
Анализ примесного состава полученных осадков гидроксида алюминия показал, что содержание примесей натрия и железа составляет 0,01 %масс и 0,015 %масс. соответственно. Суммарное содержание примесей металлов составляет менее 0.05 %масс.
Дисперсный анализ порошков синтезированного гидроксида алюминия с максимальным содержанием байерита (образец 16) (далее байерит) показал, что ведение процесса осаждения при температуре (20±1)0С приводит к образованию осадков с размером частиц от 0,2 до 50мкм с преобладанием частиц размером от 1 до 10 мкм (42 %). Термообработка байерита при (500 ± 10) 0С приводит к образованию оксида алюминия, состоящего преимущественно из η-модификации (85 %масс.) (далее η-Al2О3) с размером частиц до 0,5 – 100 мкм. При этом наблюдается практически полное спекание частиц фракции 0,2 – 0,5 мкм, уменьшение количества частиц фракции 0,5 – 1 мкм и повышение доли фракции более 10 мкм при сохранении практически неизменным их преобладающего размера (19 и 20 мкм).
Промышленный гидроксид алюминия – псевдобемит (ПБ), использованный в качестве связующей добавки при приготовлении формовочных паст ряда образцов, был получен переосаждением гиббсита по нитратной технологии при 68 – 70 0С. При сопоставлении результатов РФА, ДТА и ТГА сделан вывод о том, что образец ПБ представляет собой практически 100 %-ный псевдобемит с высокой степенью аморфизованности. Анализ примесного состава образца ПБ показал, что содержание примесей натрия и железа составляет по 0,01 %масс. Дисперсный анализ порошка ПБ показал, что распределение частиц по размерам лежит в пределах от 0,25 до 40 мкм с преобладанием частиц размером более 4 мкм (67,5 %).
Рисунок 2 – Рентгенограммы образцов 12, 15 и 16 (* – бемит, ♦ – байерит), полученных при температуре (20 ± 1) 0С в течение 2 часов осаждения при различном времени старения
(12 – без старения; 15 – 2 часа; 16 – 24 и 48 часов)
В четвертой главе обсуждены результаты исследования реологических свойств формовочных паст для экструдирования, влияния состава формовочных паст на кислотные, структурно-прочностные и текстурные свойства гранулированных η-Al2O3-носителей и на активность последних в тестовой реакции изомеризации н-бутана. На основании полученных результатов разработана принципиальная
технологическая схема получения гранулированного алюмооксидного носителя и технологическая инструкция на процесс его изготовления.
На рисунках 3-10 и в таблице 3 представлены кривые течения и эффективной вязкости формовочных паст различного состава и результаты расчета показателей их реологических свойств, соответственно.
Таблица 3 – Показатели реологических свойств формовочных паст
Образец
Предельное напряжение сдвига, Па
Эффективная вязкость, Па·с
Прочность коагуляционной структуры ΔN, МВт/м3
Индекс течения, n
Рстат
Рдин
ηmax
ηmin
Формовочные пасты на основе свежеосажденного гидроксида алюминия – байерита Ба–Ф1 —— Ба–Ф2 80 290 40 3 0,07 – Ба–Ф3 250 590 75 4 0,32 –
Формовочные пасты на основе порошка гидроксида алюминия – байерита
Ба–1,0ПВС 1010 2370 505 Ба–1,5ПВС 640 2000 320 Ба–2,7ПВС 420 1330 210 Ба–3,5ПВС 270 640 80
9 4,3 – 7 3,1 – 5 1,5 – 4 0,38 –
Формовочные пасты на основе порошков Ба80–ПБ20 5330 9325 Ба80–ПБ20–1,5ПВС 3465 6395 Ба80–ПБ20–HNO3 1600 2930
гидроксидов алюминия – байерита и псевдобемита 890 35 18,0 0,42 345 25 11,0 0,44
90 20 4,9 0,72 Формовочные пасты на основе порошков псевдобемита и η-Al2O3
ПБ20–η80 1760 2130 ПБ20–η80–1,5ПВС 1040 1545 ПБ20–η80–HNO3 585 1225
295 25 6,9 0,16 175 6 5,7 0,20 100 5 3,4 0,42
Наблюдения при экструдировании формовочных паст на основе свежеосажденного гидроксида алюминия – байерита позволили отнести их к твердообразным жидкостям, проявляющим тиксотропный характер течения. Подтверждением этому является разжижение этих паст, независимо от их влажности, под воздействием сдвиговых нагрузок (при экструдировании) и вид их реологических кривых (рисунки 3, 4). При этом отмечено, что формовочная паста Ба–Ф1 резко отличается от паст Ба–Ф2 и Ба–Ф3. Она обладает излишней текучестью и, в буквальном смысле слова, вытекает из фильеры, а экструдаты, получаемые при ее формовании, не сохраняют свои форму и размер. Это свидетельствует о разрушенной структуре пасты Ба–Ф1, что подтверждается видом кривых течения и эффективной вязкости, характерных для ньютоновских жидкостей. Формовочная паста Ба–Ф3 имеет более высокую прочность коагуляционной структуры ΔN и значение предельного статического напряжения сдвига Рстат, чем Ба– Ф2. Это согласуется с тем, что для экструдирования пасты Ба–Ф3 в начальный момент времени требуется больше усилий для продавливания через фильеру, чем для пасты Ба–Ф2. Причиной этих явлений является увеличение прочности единичного контакта частиц, осуществляемого через дисперсионную прослойку, со снижением влажности рассматриваемых формовочных паст за счет уменьшения толщины межчастичных прослоек. Тем не менее, в связи с малой прочностью коагуляционной структуры ΔN (считается, что формовочная паста пригодна к экструзии при прочности коагуляционной структуры не менее 2 МВт/м3), рассмотренные системы не пригодны к экструзии.
Введение в состав формовочных паст на основе порошка гидроксида алюминия – байерита поливинилового спирта не влияет на характер их течения. Рассматриваемые формовочные пасты также могут быть отнесены к тиксотропным твердообразным жидкостям, разжижающимся в процессе формования (рисунки 5, 6). Однако, добавка поливинилового спирта до (1,5 ± 0,1) %масс. (в пересчете на гидроксид алюминия) в такие формовочные пасты повышает прочность их коагуляционной структуры по сравнению с таковыми на основе свежеосажденного байерита за счет увеличения диапазона напряжений сдвига, отвечающих течению жидкости с неразрушенной структурой. Причиной наблюдаемого является увеличение как числа межчастичных контактов (ПВС препятствует их агрегированию), так и прочности единичного контакта частиц, осуществляемого через коллоидную прослойку оптимальной толщины между частицами. По-видимому, такое содержание поливинилового спирта в формовочной пасте отвечает полному обволакиванию им всей доступной поверхности твердой
фазы, что препятствует выделению коллоидно-связанной воды из структуры байерита. Дальнейшее добавление в формовочные пасты поливинилового спирта уменьшает значение максимальной эффективной вязкости ηmax, способствуя увеличению подвижности коагуляционных связей при увеличении толщины межчастичных прослоек.
Рисунок 3 – Зависимость скорости сдвига от напряжения сдвига для формовочных паст на основе свежеосажденного байерита
с различной влажностью
Рисунок 4 – Зависимость эффективной вязкости от напряжения сдвига для формовочных паст на основе свежеосажденного байерита
с различной влажностью
Рисунок 6 – Зависимость эффективной вязкости от напряжения сдвига для формовочных паст на основе порошка байерита
с различным содержанием ПВС
Рисунок 5 – Зависимость скорости сдвига от напряжения сдвига для формовочных паст на основе порошка байерита
с различным содержанием ПВС
Введение порошка псевдобемита в состав формовочных паст на основе порошка гидроксида алюминия – байерита приводит к исчезновению разжижения формовочных паст. Это подтверждается изменением вида кривых течения и эффективной вязкости для этих формовочных паст (рисунки 7, 8) по сравнению с таковыми из «чистого» байерита (рисунки 3, 4). Реологические кривые формовочных паст приобретают вид, характерный для псевдопластичного течения. При сравнении по данным таблицы 3 характеристик формовочных паст с добавлением псевдобемита (Ба80–ПБ20) и без него (Ба–Ф3) наблюдается увеличение прочности коагуляционной структуры ΔN первых, что сопровождается ростом значения предельного статического напряжения сдвига Рстат. Это происходит за счет большей реакционной способности частиц псевдобемита, чем байерита, по отношению к воде. Наблюдаемые тенденции отмечены и для формовочных паст с добавлением поливинилового спирта (Ба–1,5ПВС и Ба80–ПБ20–1,5ПВС). Применение поливинилового спирта и пептизатора – азотной кислоты для приготовления формовочных паст на основе порошков байерита и псевдобемита приводит к снижению прочности их коагуляционной структуры ΔN и значения предельного статического напряжения сдвига Рстат.
Замена в составе формовочных паст байерита на η-Al2O3 (рисунки 9, 10) приводит к уменьшению прочности их коагуляционной структуры ΔN, что сопровождается уменьшением значения предельного статического напряжения сдвига Рстат, независимо от содержания поливинилового спирта или азотной кислоты. Это может быть обусловлено уменьшением количества межчастичных контактов в связи с уменьшением дисперсности твердой фазы и реакционной способности оксида алюминия по отношению к воде. Применение поливинилового спирта и пептизатора – азотной кислоты для приготовления формовочных паст на основе порошков η-Al2O3 и псевдобемита, как и в случае с байеритом, приводит к снижению прочности их коагуляционной структуры ΔN и значения предельного статического напряжения сдвига Рстат.
Рисунок 7 – Зависимость скорости сдвига от напряжения сдвига для формовочных паст на основе порошков байерита и псевдобемита в соотношении 80:20
Рисунок 8 – Зависимость эффективной вязкости от напряжения сдвига для формовочных паст на основе порошков байерита и псевдобемита
в соотношении 80:20
Рисунок 10 – Зависимость эффективной вязкости от напряжения сдвига для формовочных паст на основе порошков псевдобемита и η-Al2O3
в соотношении 80:20
Рисунок 9 – Зависимость скорости сдвига от напряжения сдвига для формовочных паст на основе порошков псевдобемита и η-Al2O3
в соотношении 80:20
В результате анализа данных о реологических свойствах формовочных паст, полученных разными способами, установлено, что:
– формовочные пасты на основе свежеосажденного гидроксида алюминия – байерита имеют тиксотропный характер течения и в процессе экструдирования разжижаются. Варьирование влажности таких формовочных паст позволяет регулировать прочность их коагуляционной структуры за счет изменения прочности единичного контакта частиц, осуществляемого через дисперсионную прослойку;
– добавление в формовочные пасты на основе порошка байерита в качестве пластификатора – поливинилового спирта не влияет на характер течения первых;
– применение поливинилового спирта в количестве до (1,5 ± 0,1) %масс. в пересчете на гидроксид алюминия позволяет увеличить прочность коагуляционной структуры формовочных паст за счет расширения диапазона напряжений сдвига, отвечающих за течение паст с неразрушенной структурой, а
также обволакивания поливиниловым спиртом всей доступной поверхности твердой фазы, препятствуя выделению коллоидно-связанной воды из структуры байерита и тем самым, уменьшая разжижаемость формовочных паст;
– добавка порошка псевдобемита в формовочные пасты на основе порошка байерита в количестве 20 %масс. в пересчете на оксид алюминия позволяет изменить характер течения формовочных паст на псевдопластичный, увеличивая при этом прочность их коагуляционной структуры из-за большей реакционной способности частиц псевдобемита, чем байерита, по отношению к воде и раствору пептизатора;
– изменение дисперсности применяемых порошков для приготовления формовочных паст заменой в их составе порошка байерита на порошок η-Al2O3 ведет к изменению прочности их коагуляционной структуры ввиду изменения числа межчастичных контактов и реакционной способности порошков к воде;
– применение азотной кислоты и поливинилового спирта при приготовлении формовочных паст, содержащих псевдобемит, приводит к уменьшению прочности коагуляционной структуры этих паст из- за увеличения подвижности коагуляционных связей.
Текстурные и структурно-прочностные характеристики гранулированных носителей, полученных из формовочных паст различного состава, приведены в таблице 4.
Таблица 4 – Структурно-прочностные характеристики гранулированных носителей, полученных из формовочных паст различного состава
Образцы носителя Sуд, м2/г VƩ Ws Vмакро P□, МПа Δ, г/см3 см3/г
Носители из формовочных паст на основе свежеосажденного гидроксида алюминия – байерита
Ба–Ф1 305 Ба–Ф2 260 Ба–Ф3 230
0,76 0,30 0,73 0,30 0,65 0,30
0,46 1,5 0,54 0,43 2,0 0,56 0,35 2,4 0,60
Носители из формовочных паст на основе порошка гидроксида алюминия – байерита
Ба–1,0ПВС 305 Ба–1,5ПВС 365 Ба–2,7ПВС 260 Ба–3,5ПВС 240
0,55 0,33 0,22 0,5 0,69 0,62 0,37 0,25 2,0 0,62 0,65 0,31 0,34 1,9 0,60 0,66 0,25 0,41 1,7 0,59
Носители из формовочных паст на
основе порошков байерита и η-Al2O3
Ба80–η20–1,5ПВС Ба60–η40–1,5ПВС Ба40–η60–1,5ПВС Ба20–η80–1,5ПВС
310 0,69 0,35 285 0,72 0,33 270 0,73 0,32 250 0,75 0,29
0,34 1,9 0,57 0,39 1,8 0,56 0,41 1,7 0,56 0,46 1,6 0,55
Носители из формовочных паст на основе порошков гидроксидов алюминия
– байерита и псевдобемита 7,8 0,63 6,6 0,60 13,6 0,65
Ба80–ПБ20 300 Ба80–ПБ20–1,5ПВС 335 Ба80–ПБ20–HNO3 255
0,60 0,33 0,65 0,36 0,57 0,30
0,27 0,29 0,27
Носители из формовочных паст на основе порошков псевдобемита и η-Al2O3
ПБ20–η80 250 ПБ20–η80–1,5ПВС 270 ПБ20–η80–HNO3 230
0,80 0,29 0,83 0,28 0,79 0,28
0,51 7,2 0,50 0,55 3,4 0,48 0,51 13,4 0,52
Результаты определения интегральной характеристики кислотно-основных свойств поверхности носителей, экструдированных из формовочных паст на основе свежеосажденного байерита, порошка байерита и смеси порошков байерита и η-Al2O3 свидетельствуют об отсутствии влияния соотношений гидроксидно-оксидных компонентов на значение функции Гаммета, равное 6,7 ± 0,1. Использование в качестве связующего гидроксида алюминия – псевдобемита в составе формовочных паст ведет к снижению кислотности поверхности образцов носителей (Н0 возрастает до 7,2), что хорошо согласуется с литературными данными.
Уменьшение влажности формовочных паст на основе свежеосажденного гидроксида алюминия – байерита способствует снижению объема макропор в экструдатах, при этом объем сорбирующих пор (мезопор) остается неизменным. Это можно объяснить уплотнением формовочных паст по мере
уменьшения их влажности, что приводит к увеличению прочности на раздавливание и снижению удельной поверхности и суммарного объема пор носителей.
Введение в качестве пластификатора – поливинилового спирта в состав формовочных паст на основе порошка гидроксида алюминия – байерита приводит к росту удельной поверхности гранулированных носителей. Рост содержания поливинилового спирта в формовочных пастах ведет к увеличению суммарного объема пор в экструдатах за счет уменьшения объема сорбирующих пор и увеличения объема макропор в них. Определено оптимальное количество поливинилового спирта, равное (1,5 ± 0,1) %масс. в пересчете на гидроксид алюминия, вводимое в формовочную пасту, обеспечивающее, как уже было сказано выше, максимальную степень обволакивания им всей доступной поверхности твердой фазы и получение гранулированных носителей с высокой удельной поверхностью (365 м2/г) и прочностью на раздавливание (2,0 МПа).
Введение в качестве инертной добавки порошка η-Al2O3 в состав формовочных паст на основе порошка гидроксида алюминия – байерита приводит к следующим изменениям текстурных характеристик гранул носителей, Эти изменения могут быть объяснены суммарным влиянием на вторичную пористую структуру и прочность гранул следующих изменений, которые протекают при взаимной упаковке частиц в пастах и гранулах и формировании межчастичных контактов, обеспечивающих прочность пористого тела. С ростом содержания η-Al2O3 в формовочных пастах снижается доля более мелких частиц байерита, то есть уменьшается число единичных контактов на единицу контактного сечения, а также доля реакционноспособных частиц (гидроксид по сравнению с оксидом), то есть уменьшается число контактов более высокой силы. Это в совокупности способствует снижению удельной поверхности, прочности на раздавливание и увеличению суммарного объема пор экструдатов.
Применение порошка псевдобемита в количестве 20 %масс. в пересчете на Al2O3 в качестве алюмогидроксидного связующего в формовочных пастах как на основе порошка байерита, так и на основе η-Al2O3 позволяет увеличить прочность носителей на раздавливание. Экструдаты, полученные из формовочных паст на основе порошков псевдобемита и η-Al2O3, имеют более высокие значения суммарного объема пор по сравнению с таковыми из формовочных паст на основе порошков байерита и псевдобемита за счет развития объема макропор и снижения объема сорбирующих пор. Полученные результаты объясняют более высокую удельную поверхность носителей из формовочных паст на основе порошков байерита и псевдобемита.
Добавление поливинилового спирта в формовочные пасты, содержащие псевдобемит позволяет увеличить удельную поверхность и суммарный объем пор носителей. Наблюдаемое является следствием незначительного роста как объема сорбирующих пор, так и объема макропор. Применение в качестве пептизатора – азотной кислоты в составе таких формовочных паст приводит к увеличению механической прочности образцов носителей на раздавливание почти вдвое.
Изотермы адсорбции-десорбции азота при 77К для синтезированных образцов носителей, представленные на рисунках 11, 12, позволяют оценить влияние состава формовочной пасты на параметры пористой структуры. Регулирование состава формовочных паст изменением их влажности, введением пластификатора – поливинилового спирта, порошков η-Al2O3 и псевдобемита, а также пептизатора – азотной кислоты не приводит к изменению типа изотерм.
Все изотермы синтезированных образцов носителей при некотором количественном различии в величинах адсорбции, достигаемых при определенных значениях Р/Р0, имеют одинаковую форму. Адсорбционные ветви этих изотерм по классификации Бранауэра могут быть отнесены к IV типу, что является характерным для мезопористых систем. Однако, типы гистерезисных петель на изотермах в области выраженной капиллярной конденсации при Р/Р0 ≥ 0,40 отличаются друг от друга. Это может быть объяснено различием геометрических характеристик пор данных образцов.
Гистерезисные петли на изотермах адсорбции образцов носителей из формовочных паст без добавления псевдобемита по классификации ИЮПАК отнесены к типу Н4 и свидетельствует о щелевидной микропористости. Введение в состав формовочных паст алюмогидроксидного связующего – псевдобемита приводит к появлению гистерезисных петель, характерных для изотерм адсорбции типа Н3, наблюдаемых, как правило, при наличии щелевидных пор с почти плоскопараллельными стенками. Сопоставление изотерм адсорбции образцов, приготовленных из формовочных паст с применением и без псевдобемита, свидетельствуют об изменениях морфологии полученных алюмооксидных носителей.
Данные о распределении объемов пор по их размерам, рассчитанные из интегральных и дифференциальных кривых, полученных из результатов азотной порометрии, приведены в таблице 5. Согласно проведенным расчетам, все образцы носителей обладают широким полимодальным распределением объема пор по размерам.
Рисунок 11 – Изотермы адсорбции-десорбции азота при 77 K образцов носителей из формовочных паст на основе порошков байерита и η-Al2O3
Рисунок 12 – Изотермы адсорбции-десорбции азота при 77 K образцов носителей из формовочных паст на основе порошков псевдобемита и η-Al2O3
Таблица 5 – Распределение объема пор синтезированных носителей по размерам
Образец носителя Характеристика
Диапазон размера пор, нм
3-10 10-50 50-80
Носители из формовочных паст на основе свежеосажденного гидроксида алюминия – байерита
Ба–Ф1 Ба–Ф2 Ба–Ф3
dmax, нм 3 4,7 46,0 77,7 Объем пор, см /г 0,05 0,12 0,24 dmax, нм 3 4,4 38,8 75,5 Объем пор, см /г 0,06 0,11 0,22 dmax, нм 3 3,7 30,5 67,2 Объем пор, см /г 0,06 0,11 0,20
Носители из формовочных паст на
основе порошка гидроксида алюминия – байерита dmax, нм 3,5 29,4 67,2 Объем пор, см3/г 0,07 0,15 0,15 dmax, нм 4,1 30,5 69,2 Объем пор, см3/г 0,13 0,11 0,16 dmax, нм 4,2 31,5 75,5 Объем пор, см3/г 0,11 0,11 0,23 dmax, нм 4,6 31,5 77,7 Объем пор, см3/г 0,09 0,11 0,33
Ба–1,0ПВС Ба–1,5ПВС Ба–2,7ПВС
Ба–3,5ПВС
Носители из формовочных паст на основе порошков байерита и η-Al2O3
Ба80–η20–1,5ПВС Ба60–η40–1,5ПВС Ба40–η60–1,5ПВС
dmax, нм Объем пор, см3/г
dmax, нм 3 Объем пор, см /г
dmax, нм 3 Объем пор, см /г
4,3 30,5 71,3 0,11 0,11 0,21 4,4 30,5 71,3 0,09 0,12 0,25 4,6 31,5 71,3 0,08 0,13 0,27 4,6 31,5 71,3 0,07 0,14 0,33
dmax, нм Объем пор, см3/г
Ба20–η80–1,5ПВС
Носители из формовочных паст на основе порошков гидроксидов алюминия – байерита и псевдобемита
Ба80–ПБ20 Ба80–ПБ20–1,5ПВС Ба80–ПБ20–HNO3
dmax, нм 4,1 Объем пор, см3/г
dmax, нм 4.3 Объем пор, см3/г
dmax, нм 3 3,9 Объем пор, см /г
0,11 0,12 0,10
6,3 6.3 6.3
27,4 27.4 27.4
49,1 69,2 0,14 0,21 52.4 71,3 0,13 0,22 46,0 69.2 0,15 0,20
Носители из формовочных паст на основе порошков псевдобемита и η-Al2O3
ПБ20–η80 ПБ20–η80–1,5ПВС ПБ20–η80–HNO3
dmax, нм Объем пор, см3/г dmax, нм Объем пор, см3/г
dmax, нм 3 Объем пор, см /г
4,6 27,4 49,1 71,3 0,05 0,13 0,31 4,9 27,4 52,4 75,5 0,06 0,11 0,33 4,4 27,4 46,0 69,2 0,04 0,13 0,30
Уменьшение влажности формовочных паст на основе свежеосажденного гидроксида алюминия – байерита способствует смещению значений преобладающего размера пор dmax в носителях в сторону меньших размеров во всех рассматриваемых диапазонах. При этом объем пор диаметром 50 – 80 нм снижается, а диаметром 3 – 50 нм остается практически неизменным.
В носителях, полученных из формовочных паст на основе порошка гидроксида алюминия – байерита с ростом содержания поливинилового спирта в формовочных пастах объем пор диаметром 10 – 50 нм уменьшается, а диаметром 50 – 80 нм увеличивается. Добавка поливинилового спирта в количестве до (1,5 ± 0,1) %масс. в пересчете на гидроксид алюминия позволяет получить носители с
максимальным объемом пор диаметром 3 – 10 нм.
В экструдатах, полученных из формовочных паст на основе порошков байерита и η-Al2O3, с
увеличением доли байерита в формовочной пасте растет объем пор диаметром 3 – 10 нм. Одновременно с этим в носителях с ростом доли η-Al2O3 в формовочной пасте увеличивается объем пор диаметром 50 –
80 нм.
Применение в качестве алюмогидроксидного связующего – псевдобемита при приготовлении формовочных паст на основе порошков гидроксида алюминия – байерита способствует перераспределению пор в носителях диаметром 3 – 10 нм и 10 – 50 нм: в этих диапазонах наблюдается по два преобладающих размера пор dmax. Изменение дисперсности применяемых порошков для приготовления формовочных паст на основе псевдобемита заменой в их составе порошка байерита на порошок η-Al2O3 приводит к смещению в носителях преобладающего размера пор dmax диаметром 3 – 10 и 50 – 80 нм в область больших значений, уменьшению объема пор диаметром 3 – 10 нм и увеличению объема пор диаметром 50 – 80 нм.
Таким образом, на основании полученных результатов можно установить, что изменение влажности формовочных паст, применение порошков η-Al2O3 и псевдобемита с целью изменения свойств дисперсной фазы, добавка поливинилового спирта и азотной кислоты для изменения свойств дисперсионной среды при приготовлении формовочных паст позволяют регулировать не только их реологические свойства, но и пористую структуру получаемых экструдатов из них.
В таблице 6 приведены результаты испытаний образцов носителей в тестовой реакции низкотемпературной изомеризации н-бутана.
Таблица 6 – Результаты каталитических испытаний образцов носителей в тестовой реакции низкотемпературной изомеризации н-бутана
Глубина изомеризации, Степень конверсии Селективность, % н-бутана, % %
Образец носителя
Носители из формовочных паст на основе свежеосажденного гидроксида алюминия – байерита
Ба–Ф1 Ба–Ф2 Ба–Ф3
27,9 25,0 95,3 28,0 25,2 95,6 28,0 25,1 95,8
Носители из формовочных паст на основе порошка гидроксида алюминия – байерита
Ба–1,0ПВС Ба–1,5ПВС Ба–2,7ПВС Ба–3,5ПВС
29,0 26,1 96,1 29,4 30,4 96,4 26,9 28,7 95,4 24,6 28,4 95,1
Носители из формовочных паст на основе порошков байерита и η-Al2O3
Ба80–η20–1,5ПВС Ба60–η40–1,5ПВС Ба40–η60–1,5ПВС Ба20–η80–1,5ПВС
27,4 28,5 95,5 26,3 28,4 95,4 24,8 27,7 95,3 24,5 26,2 95,4
Носители из формовочных паст на основе порошков гидроксидов алюминия – байерита и псевдобемита
Ба80–ПБ20 Ба80–ПБ20–1,5ПВС Ба80–ПБ20–HNO3
23,0 22,1 94,7 23,9 23,0 94,9 21,2 21,6 94,3
Носители из формовочных паст на основе порошков псевдобемита и η-Al2O3
ПБ20–η80 ПБ20–η80–1,5ПВС ПБ20–η80–HNO3
η-А12О3(Sasol) η-Аl2О3 («НПФ «ОЛКАТ»)
18,6 18,8 94,7 20,5 21,2 94,7 17,0 17,5 94,2 Образцы сравнения
27,9 28,6 94,3 23,8 24,3 95,0
Образец сравнения η-Аl2О3(Sasol) получен из импортного порошка гидроксида алюминия байеритной структуры Pural BT производства Sasol Germany GmbH (Германия). Образец η-Аl2О3(«НПФ «ОЛКАТ») получен из опытно-промышленного образца байерита, произведенного по «алюминатной» технологии осаждения (нейтрализацией алюмината натрия азотной кислотой). Образцы представляют собой экструдаты в форме черенков с диаметром (3,0 ± 0,1) мм и содержат 85 %масс. и 64 %масс. η-Аl2О3 соответственно.
Результаты, приведенные в таблице 6, позволяют сделать заключение, что все образцы хлорированных носителей обеспечивают достаточно высокую и сопоставимую селективность с эталонными образцами и перспективны при получении катализаторов низкотемпературной
изомеризации углеводородов. Однако, следует отметить, что степень конверсии и глубина изомеризации н-бутана зависят от фазового состава и текстурных характеристик носителей. Так носители, полученные из формовочных паст, содержащих 20 %масс. псевдобемита, имеют более низкую изомеризующую активность по сравнению с таковыми, полученными из формовочных паст без добавления псевдобемита. Это связано с тем, что γ-Al2O3, образующийся при термообработке псевдобемита, имеет более низкую кислотность поверхности по сравнению с η-Al2O3.
Сопоставление результатов, приведенных в таблицах 4, 5 и 6, свидетельствует о падении изомеризующей активности носителей при снижении их удельной поверхности. Наряду с этим выявлено, что уменьшение в носителях объема пор диаметром 3 – 10 нм также ведет к падению их изомеризующей активности. Так активность носителей с приблизительно одинаковыми объемами таких пор, но с различной величиной удельной поверхности, оставалась неизменной.
Таким образом, на основании анализа кислотно-основных и текстурных свойств носителей и их изомеризующей активности в качестве носителя катализаторов процесса изомеризации углеводородов ввиду высокой удельной поверхности (365 м2/г) при одновременно высоком значении объемной доли пор с диаметром 3 – 10 нм (32,5 %) и высокой изомеризующей активности рекомендуется использовать образец Ба–1,5ПВС, принципиальная технологическая схема получения которого представлена на рисунке 13.
Рисунок 13 – Принципиальная технологическая схема получения гранулированного алюмооксидного носителя
Представленная на рисунке 13 принципиальная схема получения гранулированного η-Аl2О3- носителя для процесса низкотемпературной изомеризации углеводородов состоит из двух участков: осаждения (а) и формования (б). Конечным продуктом на участке осаждения является порошок гидроксида алюминия, из которого на участке формования получают гранулированный алюмооксидный носитель.
В качестве исходного сырья предлагается использовать 9-водный азотнокислый алюминий и раствор аммиака. Водные растворы нитрата алюминия (позиция 1) и аммиака (позиция 2) одновременно подаются в реактор с мешалкой (позиция 4), содержащий компенсаторный аммиачный раствор (позиция 3). Одновременная подача растворов ведется в течение 2 ч при поддержании постоянного значения рН = (10,5 ± 0,1) и температуры реакционной среды, равной (20 ± 1) 0С. По окончании слива растворов суспензия гидроксида алюминия выдерживается в отстойнике (позиция 5) для проведения процесса старения полученного осадка в маточном растворе в течение 24 ч. После окончания процесса старения осадок фильтруется на установке фильтрации, представляющей собой ленточный фильтр (позиция 6), где происходит разделение маточного раствора и осадка, представляющего собой гидроксид алюминия. Промывка производится с помощью подачи воды из емкости (позиция 7) до нейтральной реакции среды. Остающийся на фильтре осадок подвергается сушке в электрическом сушильном шкафу (позиция 8) при температуре (110 ± 10) 0С до постоянной массы.
Из полученного на участке осаждения порошка гидроксида алюминия готовится формовочная паста в лопастном смесителе (позиция 10) с введением раствора поливинилового спирта и воды. Приготовленная паста формуется на шнековом аппарате-грануляторе (позиция 11). Далее экструдаты в виде нитей подсушиваются в осушителе с продувкой воздухом (позиция 12) и дробятся с отсевом мелочи и пыли с помощью специального устройства (позиция 13) до образования гранул необходимого размера, которые подвергаются термообработке в муфельной печи (позиция 14) при температурах (110 ± 10) 0С до постоянной массы и (500 ± 10) 0С в течение (4,0 ± 0,1) ч.
Отпускная цена гранулированного алюмооксидного носителя, произведенного по разработанной технологии, учитывающая затраты на основные сырьевые и вспомогательные ресурсы, опытно- конструкторские разработки, административные и маркетинговые расходы, в первом приближении составит 8 263 рубля/кг Аl2О3. Для сравнения стоимость 1 кг импортного η-Аl2О3-носителя производства Sasol Germany GmbH (Германия) составляет ≈ 250 $, то есть 18 750 рублей при курсе 1 $ = 75 рублей, что подтверждает экономическую целесообразность предлагаемой технологии.
ЗАКЛЮЧЕНИЕ
В работе изучено влияние условий осаждения гидроксида алюминия на фазовый состав получаемого осадка, оценено влияние состава формовочных паст на основе синтезированных осадков на их реологические характеристики, структурно-прочностные свойства и каталитическую активность гранулированных носителей, полученных из них.
По результатам проведенных исследований сделаны следующие выводы:
1 Определены температурно-временные условия осаждения гидроксида алюминия – байерита из водных растворов нитрата алюминия и аммиака, обеспечивающие его максимальный выход при минимальном содержании примесей натрия и железа в полученных осадках на уровне менее 0,02 %масс. Установлено, что в изотермических условиях содержание байерита в полученных осадках, независимо от температуры проведения эксперимента, достигает максимального значения в течение времени осаждения, равного ≈ 2 часам. Повышение температуры процесса осаждения в интервале от 10 до 20 0С сопровождается увеличением количества образовавшегося байерита с 65 до 70 %масс., соответственно, повышением содержания псевдобемита и уменьшением аморфной составляющей в смеси твердых фаз. Последующее старение осадков с максимальным содержанием байерита в маточных растворах в течение 24 часов при температурах процесса осаждения приводит к фазовому превращению «аморфная фаза, псевдобемит → байерит» и получению твердофазных смесей с содержанием байерита 80 – 85 %масс.
2 С целью получения формовочных паст для экструдирования и приготовления гранулированного η-Al2O3-носителя исследованы концентрированные суспензии на основе синтезированного байерита, представляющие собой твердообразные структурированные жидкости. Установлен тиксотропный характер их течения под воздействием нагрузок, прилагаемых при экструдировании, препятствующий формообразованию и получению гранул для дальнейшей переработки. Отрицательный эффект чрезмерного тиксотропного течения, препятствующий формообразованию при экструдировании, усиливается при введении в формовочные пасты пептизатора – азотной кислоты.
3 Показано, что изменение влажности формовочных паст на основе свежеосажденного гидроксида алюминия – байерита в диапазоне от 82,6 до 60,9 %масс. не влияет на характер их течения и способствует лишь изменению прочностных и текстурных характеристик носителей, полученных из них, за счет изменения плотности формовочных паст и прочности единичного контакта частиц, осуществляемого через дисперсионную прослойку.
4 Установлено, что применение поливинилового спирта в качестве пластификатора при приготовлении формовочных паст из порошка гидроксида алюминия – байерита в количестве (1,5±0,1)%масс. в пересчете на гидроксид алюминия необходимо и достаточно для увеличения прочности коагуляционной структуры формовочных паст и уменьшения степени выделения коллоидно- связанной воды из межслоевого пространства байерита. Показано, что это количество поливинилового спирта, несмотря на сохранение тиксотропного характера течения, обеспечивает максимальную степень обволакивания всей доступной поверхности твердой фазы в формовочных пастах, увеличивая тем самым возможность их экструдирования без чрезмерного разжижения, что обеспечивает тиксотропное восстановление структуры на выходе из фильеры экструдера и высокие удельную поверхность, суммарный объем пор и прочность алюмооксидных носителей на раздавливание.
5 Установлено, что введение в формовочные пасты из порошка байерита инертной добавки – порошка η-Al2O3 позволяет регулировать пористую структуру носителей, способствуя росту как размеров пор, так и доли пор диаметром 50 – 80 нм.
6 Показано, что добавление порошка псевдобемита в количестве 20 %масс. в формовочные пасты как на основе порошка байерита, так и на основе порошка η-Al2O3 позволяет изменить характер их течения, увеличивая при этом прочность их коагуляционной структуры из-за большей реакционной способности частиц псевдобемита по отношению к воде. Кроме того, добавка псевдобемита в формовочные пасты позволяет изменять геометрические параметры пор в носителях.
7 Показано, что применение в качестве пептизатора азотной кислоты при приготовлении формовочных паст на основе смесей порошков псевдобемита с байеритом и псевдобемита с η-Al2O3, приводит к уменьшению прочности коагуляционной структуры этих паст в пределах их экструдируемости из-за увеличения подвижности коагуляционных связей и позволяет увеличить механическую прочность образцов носителей на раздавливание почти вдвое.
8 На основании проведенных испытаний гранулированных носителей в модельном процессе изомеризации н-бутана подтверждена высокая эффективность использования η-Al2O3 в данном процессе. Выявлено, что полученные образцы алюмооксидного носителя позволяют обеспечить достаточную активность и высокую селективность по изо-бутану, равную 94,2 – 96,4 %, сопоставимую с импортными и опытно-промышленными образцами сравнения. Показано, что наилучшие каталитические свойства достигаются на образцах алюмооксидного носителя, полученного из формовочной пасты на основе порошка байерита с содержанием поливинилового спирта в количестве (1,5 ± 0,1) %масс. в пересчете на гидроксид алюминия. Разработанная технология получения гранулированного алюмооксидного носителя из формовочной пасты на основе порошка байерита с добавкой поливинилового спирта может быть использована и в случае промышленной реализации технологии производства байерита по «алюминатной» технологии.
9 Разработаны принципиальная технологическая схема получения гранулированного η-Al2O3-носителя и «Технологическая инструкция на процесс изготовления алюмооксидных носителей Ба–1,5ПВС и Ба80–ПБ20–1,5ПВС», предназначенных для получения катализаторов низкотемпературной изомеризации углеводородов. В соответствии с разработанной технологической инструкцией наработаны опытные партии алюмооксидных носителей. Результаты определения физико-химических, прочностных и текстурных характеристик опытных партий алюмооксидных носителей катализаторов удостоверены актом «О наработке опытных партий алюмооксидных носителей Ба–1,5ПВС и Ба80–ПБ20–1,5ПВС».
По результатам исследований подготовлена и подана в Федеральный институт промышленной собственности (ФИПС) «Федеральной службы по интеллектуальной собственности, патентам и товарным знакам» заявка на выдачу патента на изобретение (регистрационный No2021114421 от 20.05.2021 года).
Актуальность темы диссертации. В мировом производстве моторных
топлив наблюдается постоянное ужесточение требований к показателям качества
продукции [1]. Это связано с тем, что транспорт является одним из основных
источников загрязнения воздуха токсичными веществами [2, 3]. Наряду с
необходимостью снижения вредных выбросов, стоит задача повышения
октановых характеристик топлив, так как использование бензинов с большим
октановым числом (определяется по моторному (ММ) и исследовательскому
методам (ИМ)) позволяет значительно повышать мощность двигателей без
изменения их габаритов за счет снижения удельного расхода топлива [4-7].
Базовым компонентом при компаундировании моторных топлив в РФ
является катализат процесса риформинга, содержащий 50 – 70 % ароматических
углеводородов, при сгорании которых образуются токсичные и канцерогенные
вещества [8-11]. Следовательно, необходимым компонентом для увеличения
октанового числа является неароматическая часть бензина, в частности,
изомеризат пентан-гексановой фракции [7, 9, 12-14]. Этот продукт
характеризуется высоким значением октанового числа (89 – 92 пунктов по ИМ),
низкой себестоимостью по сравнению с другими неароматическими
высокооктановыми компонентами, а также отсутствием серосодержащих,
непредельных и ароматических углеводородов в своем составе [7, 15]. Эти
преимущества указывают на приоритетное значение процесса изомеризации и ее
экономическую целесообразность в решении проблемы повышения качества
современных автомобильных бензинов [16, 17].
По прогнозам, в России к 2030 году число установок изомеризации
возрастет вдвое. Следовательно, можно ожидать, что существенно возрастет и
потребление катализаторов процесса изомеризации как в натуральном, так и в
стоимостном выражении. Однако, реализуемые на отечественных
нефтеперерабатывающих заводах процессы изомеризации базируются на
зарубежных технологиях, что предполагает применение импортных
катализаторов. Решение проблемы импортозамещения за счёт применения
технологических процессов, разработанных учёными Советского Союза
невозможно, даже несмотря на высокий уровень этих технологий, так как
источники сырья, на которых они базировались, после распада СССР остались за
пределами Российской Федерации [14]. Поэтому на сегодняшний день существует
острая необходимость разработки отечественных импортозамещающих
технологий производства катализаторов изомеризации на основе отечественного
сырья, а также носителей для них, от которых зависят в первую очередь
селективность, экономичность и простота технологии рассматриваемого
процесса.
Процессы изомеризации подразделяются на три основных типа: высоко-,
средне- и низкотемпературные [18]. Наиболее широкое применение в
промышленности получили процессы низкотемпературной изомеризации
парафиновых углеводородов. Хлорированные алюмоплатиновые катализаторы
(Pt/Al2O3-Cl), содержащие платину в количестве 0,3 – 0,4 %масс., являются
наиболее активными и широко применяемыми катализаторами
низкотемпературной изомеризации из предлагаемых в настоящее время.
Повышенная активность данного катализатора позволяет вести изомеризацию с
высокой степенью превращения и селективностью по целевым продуктам при
низких температурах (100 – 180 ⁰С) и, следовательно, получать продукты с более
высокими октановыми числами [19, 20].
В качестве носителей для упомянутых катализаторов применяют
преимущественно метастабильные модификации оксида алюминия (γ- и η-Al2O3),
которые имеют значительный температурный диапазон существования фаз
(γ-Al2O3 – (450 – 850) ⁰С; η-Al2O3 – (250 – 550) ⁰С) [21-32].
Исследователи [22, 24, 26, 29, 30, 33-36] считают, что эти модификации
фактически представляют собой одну и ту же нестехиометрическую шпинельную
структуру, однако, γ- и η-Al2O3 демонстрируют разные свойства в полиморфных
превращениях. Это обусловлено различным структурным расположением
алюминиевых вакансий, образующихся в результате прокаливания
соответствующего гидроксида алюминия при повышенных температурах, что
приводит к различию координационного числа и эффективного заряда атомов
алюминия на поверхности [26, 27, 29, 30, 33, 35-37]. Такие изменения состояния
поверхностных атомов приводят к увеличению кислотности у η-Al2O3 по
сравнению с γ-модификацией, что является безусловным преимуществом для
носителей катализаторов изомеризации [27, 30-32, 38].
η-Al2O3 получают, как правило, термическим разложением тригидроксида
алюминия – байерита (Al2О3·3Н2О) [26, 29, 30, 39, 40]. Наиболее
распространенным методом получения байерита является его осаждение из
водных растворов солей алюминия (Al(NO3)3, AlCl3, Al2(SO4)3, NaAlO2)
растворами осадителя (NH4OH, NaOH, KOH, HNO3, H2SO4) [24, 26, 34, 39, 40-45].
При осаждении байерит выпадает в виде крупных, малогидратированных и
рыхлоупакованных кристаллов. Промежутки между кристаллами заполнены
коллоидно-связанной водой, связь которой в байерите непрочна [46, 47]. По этой
причине осадки байерита склонны к тиксотропному течению и под воздействием
сдвиговых нагрузок, имеющих место при приготовлении формовочных паст и их
экструдировании, резко разжижаются, а при снятии сдвиговых нагрузок резко
структурируются. Это значительно усложняет процесс формования
рассматриваемого тригидроксида и ставит задачу нахождения условий
приготовления гранулированного η-Al2O3-носителя, соответствующего
требованиям пригодности для катализаторов изомеризации углеводородов
(содержание натрия и железа не более 0,02 %масс., объем пор не менее 0,32 см3/г,
удельная поверхность не менее 300 м2/г) [48].
Отечественными компаниями, специализирующимися на производстве
оксида алюминия для нефтеперерабатывающей промышленности, а также
катализаторов и носителей на основе оксида алюминия являются: «Ишимбайский
Специализированный Химический Завод Катализаторов», ЗАО «Промкатализ»,
АО «СКТБ «Катализатор», «Ангарский завод катализаторов и органического
синтеза», производящие, главным образом, γ-Al2O3 по «алюминатной»
технологии осаждения, сопряженной с образованием большого количества
сточных вод. Однако, η-Al2O3 в промышленном масштабе в России не
производится. Единственным мировым производителем этого продукта,
удовлетворяющего требованиям, предъявляемым к носителям катализаторов
изомеризации (в части допустимого количества примесей натрия и железа),
является компания Sasol Germany GmbH (Германия).
Степень разработанности темы диссертации. Распространенным методом
получения гранулированных носителей различных форм и размеров является
экструзионное формование. Согласно литературным данным [49-53], состав
формовочных паст для экструзии влияет на их реологические характеристики и на
текстурные и механические свойства получаемых экструдатов. Несмотря на
широкое применение η-Al2O3 в качестве носителя катализаторов, исследования
влияния фазового и дисперсного составов исходного сырья, состава
дисперсионной среды, а также влажности формовочной пасты на их
реологические характеристики и структурно-прочностные характеристики
конечного носителя в литературе не представлены.
Цель работы – разработка научных основ технологии получения
гранулированного η-Al2O3-носителя для катализаторов процесса изомеризации
углеводородов.
Исходя из поставленной цели, сформулированы следующие задачи:
1 обоснование условий осаждения тригидроксида алюминия – байерита,
обеспечивающих его максимальный выход и минимально возможное содержание
примесей натрия и железа в нем, и исследование физико-химических свойств
полученных осадков;
2 исследование реологических свойств и возможности использования
концентрированных суспензий – формовочных паст на основе байерита для
получения гранулированных η-Al2O3-носителей;
3 исследование влияния пластифицирующих добавок поверхностно-
активного вещества и кислоты-пептизатора на реологические характеристики
формовочных паст для экструзии и свойства получаемых из них гранулированных
носителей;
4 оценка влияния дисперсного и фазового состава гидроксидно-
оксидных компонентов формовочных паст на текстуру гранулированных
носителей;
5 определение эффективности использования гидроксида алюминия –
псевдобемита в составе формовочных паст для улучшения их реологических
характеристик и получения механически прочных носителей;
6 тестирование полученных образцов гранулированного
алюмооксидного носителя в модельном процессе изомеризации н-бутана;
7 разработка принципиальной технологической схемы получения
гранулированного алюмооксидного носителя и технологической инструкции на
процесс его изготовления для алюмоплатиновых катализаторов
низкотемпературной изомеризации углеводородов.
Научная новизна:
1 Определены и обоснованы температурно-временные условия
осаждения тригидроксида алюминия – байерита из водных растворов нитрата
алюминия и аммиака, обеспечивающие его максимальный выход и минимально
возможное содержание примесей натрия и железа в нем.
2 Впервые исследованы и охарактеризованы концентрированные
суспензии на основе байерита – формовочные пасты для экструдирования и
получения гранулированного η-Al2O3-носителя и выявлены их особенности как
высокодисперсных структурированных систем.
3 Впервые изучено влияние содержания поливинилового спирта в
формовочных пастах из байерита на их реологические характеристики и свойства
получаемых гранулированных носителей. Показано, что его оптимальное
содержание, обеспечивающее возможность экструдирования байерита и
получения тонкопористых гранул η-Al2O3, составляет (1,5 ± 0,1) %масс. от массы
гидроксида алюминия в пасте.
4 Исследовано влияние на текстуру гранулированных алюмооксидных
носителей введения в формовочные пасты из байерита инертной добавки –
порошка η-Al2O3. Установлено, что повышение содержания η-Al2O3 в
формовочной пасте ведет к росту как размеров пор, так и доли объема пор
диаметром 50 – 80 нм, что может быть применено для регулирования текстуры
η-Al2O3-носителей.
5 Изучено влияние введения гидроксида алюминия – псевдобемита в
состав формовочных паст из байерита и η-Al2O3 на характер их течения при
экструдировании. Обнаружено увеличение прочности как коагуляционной
структуры формовочных паст, так и механической прочности гранул полученных
алюмооксидных носителей.
6 Подана заявка на выдачу патента на изобретение (регистрационный
№2021114421 от 20.05.2021 года) «Способ приготовления гранулированного
активного оксида алюминия», совокупность условий которого обеспечивает
новизну технического решения.
Теоретическая и практическая значимость работы. Предложены
оптимальные параметры процесса осаждения гидроксида алюминия с
преимущественно байеритной структурой из водных растворов нитрата алюминия
и аммиака. Представлен массив данных о влиянии состава формовочных паст для
экструзии на основе синтезированных осадков на их реологические
характеристики и свойства гранулированного активного оксида алюминия для
хлорированных алюмоплатиновых катализаторов изомеризации углеводородов
(Pt/Al2O3-Cl). Полученные данные положены в основу разработки
принципиальной технологической схемы и технологической инструкции
получения гранулированного η-Al2O3-носителя для катализаторов процесса
низкотемпературной изомеризации углеводородов. Разработанная технология
апробирована выпуском опытных партий носителя и положительными
результатами их тестирования в модельном процессе изомеризации н-бутана.
Методология и методы диссертационной работы. Поставленная цель
диссертационной работы достигалась с помощью лабораторной базы кафедры
«Общей химической технологии и катализа», научной исследовательской
лаборатории «Каталитические технологии» и Инжинирингового центра Санкт-
Петербургского государственного технологического института (технического
университета) при использовании современных стандартизированных физико-
химических методов исследования. Методологическая основа исследований
базируется на системном подходе к анализу результатов исследований,
выявлении основных проблем и путей их решения, реализации обоснованных
методов исследований, применении теоретического подхода к интерпретации
экспериментальных результатов.
Положения, выносимые на защиту:
1 Закономерности изменения фазового состава осадков гидроксида
алюминия, получаемых из водных растворов нитрата алюминия и аммиака, в
зависимости от температуры реакционной среды и продолжительности процессов
осаждения и старения.
2 Результаты исследования реологических свойств формовочных паст
на основе байерита с различной влажностью.
3 Влияние введения поливинилового спирта в формовочные пасты из
байерита на их реологические характеристики, экструдируемость и свойства
получаемых гранул η-Al2O3.
4 Регулирование текстуры гранулированных носителей введением в
байеритсодержащие формовочные пасты порошка η-Al2O3.
5 Эффективность введения псевдобемита в состав формовочных паст с
целью изменения характера течения последних при экструзии и увеличения
прочности их коагуляционной структуры.
6 Результаты исследования активности синтезированных образцов
гранулированных носителей в модельном процессе изомеризации н-бутана.
7 Принципиальная технологическая схема получения гранулированного
алюмооксидного носителя для алюмоплатиновых катализаторов
низкотемпературной изомеризации углеводородов.
Достоверность полученных результатов обеспечивается многократной
воспроизводимостью синтеза с сохранением выявленных закономерностей для
одинаковых объектов исследования, интерпретацией полученных
экспериментальных данных с помощью теоретических подходов и
использованием современных физико-химических методов исследования и
оборудования.
Апробация работы. Основные положения и результаты диссертационной
работы представлялись и обсуждались на VII научно-технической конференции
студентов, аспирантов, молодых ученых «Неделя науки-2017» (Санкт-Петербург,
2017); IV Всероссийской научно-технической конференции с участием молодых
ученых «Инновационные материалы и технологии в дизайне» (Санкт-Петербург,
2018); XVII Международной научно-практической конференции
«Фундаментальные и прикладные научные исследования: актуальные вопросы,
достижения и инновации» (Пенза, 2018); IX научно-технической конференции
студентов, аспирантов, молодых ученых «Неделя науки-2019» (Санкт-Петербург,
2019); V Всероссийской научно-практической конференции с участием молодых
ученых «Инновационные материалы и технологии в дизайне» (Санкт-Петербург,
2019); Всероссийской научно-практической конференции студентов и
преподавателей с международным участием «Дни науки-2019» (Санкт-Петербург,
2019); XI Международном молодежном форуме «Образование. Наука.
Производство» (Белгород, 2019); Всероссийской научно-практической
конференции студентов и молодых ученых «Современные тенденции развития
химической технологии, промышленной экологии и техносферной безопасности»
(Санкт-Петербург, 2020).
Личный вклад автора. Автором самостоятельно проведен анализ
отечественных и зарубежных литературных источников по теме диссертации,
синтезированы предшественники, из которых получены, изучены и
протестированы образцы алюмооксидных носителей для катализаторов
изомеризации углеводородов. Полученные результаты критически
проанализированы, обобщены и оформлены в виде статей, тезисов докладов и
текста диссертации. Автор лично выступала с докладами на научных
конференциях, принимала участие в постановке цели и формулировании задач
диссертационной работы, планировании эксперимента.
Публикации. Основные результаты диссертационной работы
опубликованы в 11-ти научно-технических работах, из которых 3 статьи в
журналах, входящих в утвержденный Высшей аттестационной комиссией при
В работе изучено влияние условий осаждения гидроксида алюминия на
фазовый состав получаемого осадка, оценено влияние состава формовочных паст
на основе полученных осадков на их реологические характеристики, структурно-
прочностные свойства и каталитическую активность гранулированных носителей,
полученных из них.
По результатам проведенных исследований сделаны следующие выводы:
1 Определены температурно-временные условия осаждения гидроксида
алюминия – байерита из водных растворов нитрата алюминия и аммиака,
обеспечивающие его максимальный выход при минимальном содержании
примесей натрия и железа в полученных осадках на уровне менее 0,02 %масс.
Установлено, что в изотермических условиях содержание байерита в полученных
осадках, независимо от температуры проведения эксперимента, достигает
максимального значения в течение времени осаждения, равного ≈ 2 часам.
Повышение температуры процесса осаждения в интервале от 10 до 20 ⁰С
сопровождается увеличением количества образовавшегося байерита с 65 до
70 %масс., соответственно, повышением содержания псевдобемита и
уменьшением аморфной составляющей в смеси твердых фаз. Последующее
старение осадков с максимальным содержанием байерита в маточных растворах в
течение 24 часов при температурах процесса осаждения приводит к фазовому
превращению «аморфная фаза, псевдобемит → байерит» и получению
твердофазных смесей с содержанием байерита 80 – 85 %масс.
2 С целью получения формовочных паст для экструдирования и
приготовления гранулированного η-Al2O3-носителя исследованы
концентрированные суспензии на основе синтезированного байерита,
представляющие собой твердообразные структурированные жидкости.
Установлен тиксотропный характер их течения под воздействием нагрузок,
прилагаемых при экструдировании, препятствующий формообразованию и
получению гранул для дальнейшей переработки. Отрицательный эффект
чрезмерного тиксотропного течения, препятствующий формообразованию при
экструдировании, усиливается при введении в формовочные пасты пептизатора –
азотной кислоты.
3 Показано, что изменение влажности формовочных паст на основе
свежеосажденного гидроксида алюминия – байерита в диапазоне от 82,6 до
60,9 %масс. не влияет на характер их течения и способствует лишь изменению
прочностных и текстурных характеристик носителей, полученных из них, за счет
изменения плотности формовочных паст и прочности единичного контакта
частиц, осуществляемого через дисперсионную прослойку.
4 Установлено, что применение поливинилового спирта в качестве
пластификатора при приготовлении формовочных паст из порошка гидроксида
алюминия – байерита в количестве (1,5 ± 0,1) %масс. в пересчете на гидроксид
алюминия необходимо и достаточно для увеличения прочности коагуляционной
структуры формовочных паст и уменьшения степени выделения коллоидно-
связанной воды из межслоевого пространства байерита. Показано, что это
количество поливинилового спирта, несмотря на сохранение тиксотропного
характера течения, обеспечивает максимальную степень обволакивания всей
доступной поверхности твердой фазы в формовочных пастах, увеличивая тем
самым возможность их экструдирования без чрезмерного разжижения, что
обеспечивает тиксотропное восстановление структуры на выходе из фильеры
экструдера и высокие удельную поверхность, суммарный объем пор и прочность
алюмооксидных носителей на раздавливание.
5 Установлено, что введение в формовочные пасты из порошка
байерита инертной добавки – порошка η-Al2O3 позволяет регулировать пористую
структуру носителей, способствуя росту как размеров пор, так и доли пор
диаметром 50 – 80 нм.
6 Показано, что добавление порошка псевдобемита в количестве
20 %масс. в формовочные пасты как на основе порошка байерита, так и на основе
порошка η-Al2O3 позволяет изменить характер их течения, увеличивая при этом
прочность их коагуляционной структуры из-за большей реакционной способности
частиц псевдобемита по отношению к воде. Кроме того, добавка псевдобемита в
формовочные пасты позволяет изменять геометрические параметры пор в
носителях.
7 Показано, что применение в качестве пептизатора азотной кислоты
при приготовлении формовочных паст на основе смесей порошков псевдобемита
с байеритом и псевдобемита с η-Al2O3, приводит к уменьшению прочности
коагуляционной структуры этих паст в пределах их экструдируемости из-за
увеличения подвижности коагуляционных связей и позволяет увеличить
механическую прочность образцов носителей на раздавливание почти вдвое.
8 На основании проведенных испытаний гранулированных носителей в
модельном процессе изомеризации н-бутана подтверждена высокая
эффективность использования η-Al2O3 в данном процессе. Выявлено, что
полученные образцы алюмооксидного носителя позволяют обеспечить
достаточную активность и высокую селективность по изо-бутану, равную 94,2 –
96,4 %, сопоставимую с импортными и опытно-промышленными образцами
сравнения. Показано, что наилучшие каталитические свойства достигаются на
образцах алюмооксидного носителя, полученного из формовочной пасты на
основе порошка байерита с содержанием поливинилового спирта в количестве
(1,5 ± 0,1) %масс. в пересчете на гидроксид алюминия. Разработанная технология
получения гранулированного алюмооксидного носителя из формовочной пасты
на основе порошка байерита с добавкой поливинилового спирта может быть
использована и в случае промышленной реализации технологии производства
байерита по «алюминатной» технологии.
9 Разработаны принципиальная технологическая схема получения
гранулированного η-Al2O3-носителя и «Технологическая инструкция на процесс
изготовления алюмооксидных носителей Ба–1,5ПВС и Ба80–ПБ20–1,5ПВС»,
предназначенных для получения катализаторов низкотемпературной
изомеризации углеводородов. В соответствии с разработанной технологической
инструкцией наработаны опытные партии алюмооксидных носителей. Результаты
определения физико-химических, прочностных и текстурных характеристик
опытных партий алюмооксидных носителей катализаторов удостоверены актом
«О наработке опытных партий алюмооксидных носителей Ба–1,5ПВС и Ба80–
ПБ20–1,5ПВС».
По результатам исследований подготовлена и подана в Федеральный
институт промышленной собственности (ФИПС) «Федеральной службы по
интеллектуальной собственности, патентам и товарным знакам» заявка на выдачу
патента на изобретение (регистрационный №2021114421 от 20.05.2021 года).
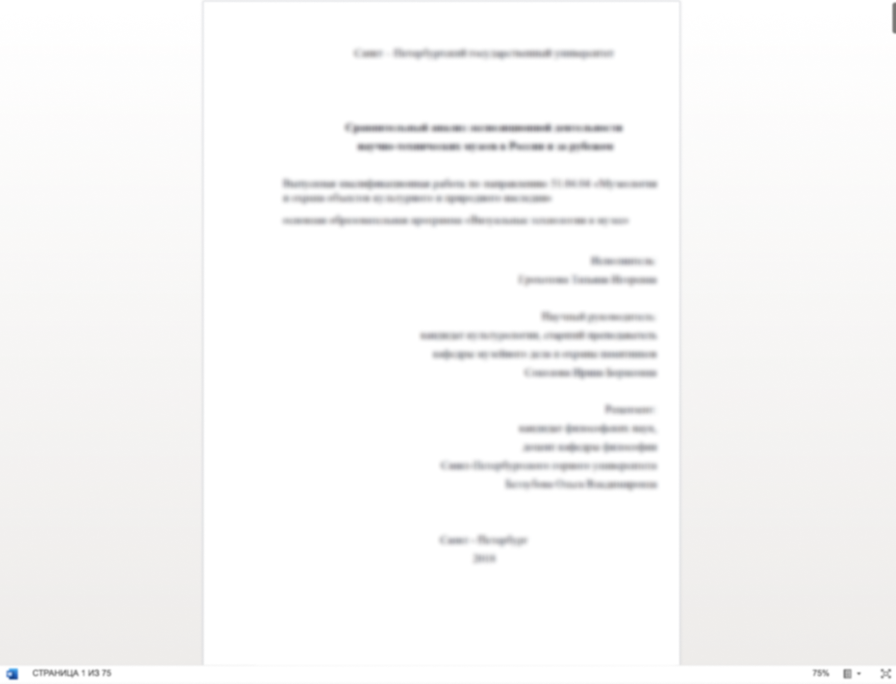
Помогаем с подготовкой сопроводительных документов
Хочешь уникальную работу?
Больше 3 000 экспертов уже готовы начать работу над твоим проектом!