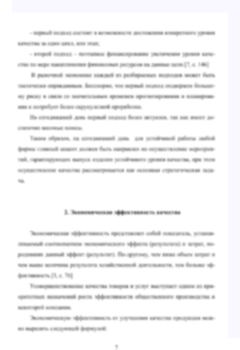
Совершенствование инструментов и технологического оборудования для точного сверления отверстий в крупногабаритных заготовках
ВВЕДЕНИЕ . . . . . . . . . . . . . . . . . . . . . . . . . . . . . . . . . . . . . . . . . . . . . . . . . . . 6
1 АНАЛИЗ ПРОИЗВОДСТВЕННОЙ ПРАКТИКИ И НАУЧНЫХ
ИССЛЕДОВАНИЙ В ОБЛАСТИ РАСЧЕТА СВЕРЛ
ТЕХНОЛОГИЧЕСКОГО ОБОРУДОВАНИЯ ДЛЯ СВЕРЛЕНИЯ
ОТВЕРСТИЙ В КРУПНОГАБАРИТНЫХ ЗАГОТОВКАХ
1.1 Производственная практика сверления отверстий в
крупногабаритных заготовках . . . . . . . . . . . . . . . . . . . . . . . . . . . . . . . . . . . 14
1.2 Анализ результатов научных публикаций по теме обработки
отверстий специальным оборудованием и РТК. . . . . . . . . . . . . . . . . . . . . . . 26
1.2.1 Анализ результатов научных исследований в области
моделирования и расчета стандартных спиральных сверл . . . . . . . . . . . . . 29
1.2.2 Анализ результатов научных исследований в области
моделирования процесса стружкообразования стандартными
спиральными сверлами . . . . . . . . . . . . . . . . . . . . . . . . . . . . . . . . . . . . . . . . . . 37
1.2.2.1 Анализ научных публикаций в области численного
моделирования стружкообразования, разработки моделей материалов и
их параметров . . . . . . . . . . . . . . . . . . . . . . . . . . . . . . . . . . . . . . . . . . . . . . . . . 38
1.2.2.2 Анализ научных публикаций в области моделирования
структур материалов, включая пористые и композитные структуры . . . . 46
1.2.3 Анализ результатов научных исследований в области
моделирования смещений податливого технологического оборудования. 49
1.3 Результаты анализа, цель и задачи работы . . . . . . . . . . . . . . . . . . . . . . 58
2 РАЗРАБОТКА ДИСКРЕТНЫХ МАТЕМАТИЧЕСКИХ МОДЕЛЕЙ
ИНСТРУМЕНТОВ И ТЕХНОЛОГИЧЕСКОГО ОБОРУДОВАНИЯ
И МОДЕЛИРОВАНИЕ ПРОЦЕССА ОБРАБОТКИ
2.1 Воксельное моделирование инструментов – спиральных сверл
2.1.1 Постановка задачи моделирования сверл . . . . . . . . . . . . . . . . . . . . . 62
2.1.2 Теоретическое исследование и воксельное моделирование
2.1.2.1 Моделирование поверхностей стружечных канавок . . . . . . . 62
2.1.2.2 Моделирование поверхностей ленточек и спинок сверла 74
2.1.2.3 Моделирование изменения параметров сверла в его осевой
плоскости . . . . . . . . . . . . . . . . . . . . . . . . . . . . . . . . . . . . . . . . . . . . . . . . . . . . 76
2.1.2.4 Моделирование главных задних поверхностей сверла . . . . . 78
2.1.3 Итоговые зависимости расчета вокселей тел и поверхностей
сверл . . . . . . . . . . . . . . . . . . . . . . . . . . . . . . . . . . . . . . . . . . . . . . . . . . . . . . . . . 98
2.2 Разработка воксельной и конечно-элементной модели податливого
технологического оборудования . . . . . . . . . . . . . . . . . . . . . . . . . . . . . . . . . 99
2.3 Разработка математической, конечно-элементной и SPG моделей
процесса обработки отверстий спиральными сверлами . . . . . . . . . . . . . . . 106
2.3.1 Разработка модели пористой структуры материала заготовки . . 109
2.3.2 Разработка модели дисперсно-армированной структуры
материала заготовки . . . . . . . . . . . . . . . . . . . . . . . . . . . . . . . . . . . . . . . . . . . 113
2.3.3 Разработка модели волоконной структуры материала заготовки
с заданным расположением волокон . . . . . . . . . . . . . . . . . . . . . . . . . . . . . . . 117
2.4 Формулирование общей модели точности обработки сверлением. . . . 121
3 ВЕРИФИКАЦИЯ СОЗДАННЫХ МАТЕМАТИЧЕСКИХ МОДЕЛЕЙ
ИНСТРУМЕНТОВ, ТЕХНОЛОГИЧЕСКОГО ОБОРУДОВАНИЯ
И ПРОЦЕССА СВЕРЛЕНИЯ . . . . . . . . . . . . . . . . . . . . . . . . . . . . . . . . . . . . . 124
3.1 Верификация математической модели стандартных спиральных
сверл путем расчета облаков узловых точек вокселей их поверхностей .. 124
3.2 Верификация математической модели стандартных спиральных
сверл путем расчета конечных элементов их тел и проведения натурных
экспериментов
3.2.1 Верификация математической модели стандартных спиральных
сверл путем расчета конечных элементов их тел . . . . . . . . . . . . . . . . . . . . 133
3.2.2 Верификация математической модели стандартных спиральных
сверл путем проведения натурных экспериментов . . . . . . . . . . . . . . . . . . 136
3.3 Моделирование процесса стружкообразования стандартными
спиральными сверлами при обработке заготовок из стали и
композитного материала . . . . . . . . . . . . . . . . . . . . . . . . . . . . . . . . . . . . . . . 139
3.4 Расчет воксельных и конечно-элементных моделей податливого
сверлильного оборудования и верификация расчетов натурными
экспериментами
3.4.1 Предварительный расчет воксельных и конечно-элементных
моделей податливого сверлильного оборудования и верификация
расчетов натурными экспериментами . . . . . . . . . . . . . . . . . . . . . . . . . . . . . . 148
3.4.2 Верификация предварительных расчетов смещений
сверлильного оборудования натурными экспериментами и внесение
изменений в расчетные модели . . . . . . . . . . . . . . . . . . . . . . . . . . . . . . . . . . 157
3.4.3 Расчет перемещений сверлильного оборудования с учетом
скорректированных моделей передаточных узлов приводов подач и
верификация окончательных расчетов натурными экспериментами . . . . . 163
4 ПРИМЕНЕНИЕ МАТЕМАТИЧЕСКИХ МОДЕЛЕЙ ИНСТРУМЕНТА,
ПОДАТЛИВОГО ТЕХНОЛОГИЧЕСКОГО ОБОРУДОВАНИЯ
И ОБРАБОТКИ ОТВЕРСТИЙ СВЕРЛЕНИЕМ. РАЗРАБОТКА
МЕТОДИК РАСЧЕТА И СОВЕРШЕНСТВОВАНИЕ СВЕРЛ И
ТЕХНОЛОГИЧЕСКОГО ОБОРУДОВАНИЯ
4.1 Проверка математических моделей обработки отверстий сверлением
4.1.1 Описание технологической операции и элементов
технологической системы. . . . . . . . . . . . . . . . . . . . . . . . . . . . . . . . . . . . . . . 167
4.1.2 Выполнение проектного расчета по определению деформаций
всех элементов технологической системы и уводу поперечной режущей
кромки сверла . . . . . . . . . . . . . . . . . . . . . . . . . . . . . . . . . . . . . . . . . . . . . . . . . . 169
4.1.3 Выполнение натурного эксперимента по определению
фактического положения отверстий, полученных сверлением . . . . . . . . . . 172
4.1.4 Разработка методики расчета отклонений режущей части сверл
при обработке отверстий с использованием податливого сверлильного
оборудования . . . . . . . . . . . . . . . . . . . . . . . . . . . . . . . . . . . . . . . . . . . . . . . . . . 180
4.2 Совершенствование инструментов и технологического оборудования
для точного сверления отверстий в крупногабаритных заготовках
4.2.1 Совершенствование инструментов для сверления отверстий
с минимальными отклонениями от заданного расположения осей . . . . . . 183
4.2.2. Совершенствование оборудования для сверления отверстий в
крупногабаритных заготовках . . . . . . . . . . . . . . . . . . . . . . . . . . . . . . . 190
ЗАКЛЮЧЕНИЕ. ОСНОВНЫЕ РЕЗУЛЬТАТЫ И ВЫВОДЫ . . . . . . . . . 206
СПИСОК ЛИТЕРАТУРЫ . . . . . . . . . . . . . . . . . . . . . . . . . . . . . . . . . . . . . . . . 208
ПРИЛОЖЕНИЕ А. Чертеж сверла с подточкой в виде правильной
пирамиды . . . . . . . . . . . . . . . . . . . . . . . . . . . . . . . . . . . . . . . . . . . . . . . . . . . . . 235
ПРИЛОЖЕНИЕ Б. Патент RU 2 718 025 C1. . . . . . . . . . . . . . . . . . . . . . . . 236
ПРИЛОЖЕНИЕ В. Сборочный чертеж на опору по патенту RU 2 718
025 C1. Чертежи на опору по патенту RU 2 718 025 C1 . . . . . . . . . . . . . . 237
ПРИЛОЖЕНИЕ Г. Патент RU 2 756 901 C1 . . . . . . . . . . . . . . . . . . . . . . . 239
ПРИЛОЖЕНИЕ Д. Сборочный чертеж на опору по патенту RU 2 756
901 C1. Чертежи на опору по патенту RU 2 756 901 C1 . . . . . . . . . . . . . . 240
Приложение Е. Акт на внедрение программы расчета сверл . . . . . . . . . . 242
Приложение Ж. Акт на внедрение программы расчета оборудования . . .. 243
Приложение З. Акт на испытание сверла с дополнительной подточкой 244
Приложение И. Титульный лист учебного пособия . . . . . . . . . . . . . . . . . . 245
Во введении показана область исследования, обоснована актуальность те-
мы диссертации, приведены цель, задачи и другие характеристики диссертации.
В первой главе приведены сведения из производственной практики и науч-
ных исследований в области производства крупногабаритных деталей аэрокосми-
ческой техники и связанных с ними расчетов сверл и компонентов СиМСС с ЧПУ
для точного сверления отверстий. Показаны причины низких темпов внедрения та-
кого оборудования в промышленность. Показано, что для внесения необходимых
корректировок в характеристики сверл или дооснащения оборудования разработ-
чику в каждом случае необходимо многократно выполнять проектные расчеты для
прогнозной оценки точности обработки. Установлено, что CAD/CAM/CAE техно-
логии позволяют достаточно точно описывать элементы технологической системы
и процессы обработки, однако в указанных выше сложных случаях высокая трудо-
емкость и индивидуальный подход для каждой конкретной технологической опе-
рации сдерживают такие проекты. В литературе не удалось обнаружить примеров
применения комплексных универсальных систем автоматизированного выполне-
ния всех таких расчетов; на практике они все еще не получили широкого распро-
странения. Одним из способов решения данной задачи является разработка универ-
сальных математических моделей рассматриваемых инструментов и оборудования,
а также фрагментов заготовок, включая композитные, для точного расчета сил ре-
зания. Такие модели позволили бы разработать методики расчета и получить ком-
пьютерное обеспечение с автоматизацией всех указанных проектных задач.
Поскольку такая задача связана с деформациями сверл, деформациями обо-
рудования и расчетом сил резания при сверлении заготовок из заданных материа-
лов, то далее были проанализированы научные публикации по каждому из этих
трех направлений. Анализ научных публикаций в области моделирования сверл и
других мерных инструментов показал, что наряду с традиционными геометриче-
скими подходами, которые нашли отражение в работах Г.А. Алексеева,
М.М, Алиева, О.Б. Арбузова, Е.В. Артамонова, В.А. Аршинова, А.И. Бокова, Ю.Л.
Борового, Л.Г. Дибнера, В.А. Гречишникова, Г.Г. Иноземцева, А.С. Каменковича,
А.С. Киселева, С.В. Кирсанова, Д.В. Кожевникова, В.И. Кокарева,
В.М. Матюшина, С.А. Попова, А.А. Рыжкина, Г.Н. Сахарова, И.С. Семенченко,
А.Г. Схиртладзе, К.Г. Щучева и других исследователей наиболее широкое приме-
нение получило использование аналитической геометрии, векторной алгебры и
дифференциального исчисления. По работам В.П. Астахова, Б.В. Лупкина,
Н.А. Киштопы, П.Р. Родина было установлено, что этот аналитический подход поз-
воляет установить связь уравнений поверхностей сверл с особенностями их изго-
товления. Однако основная цель таких расчетов – определение угловых параметров
режущих лезвий данных инструментов. Примеров разработки на этой основе уни-
версальных трехмерных моделей спиральных сверл и расчета их жесткости обна-
ружить не удалось. Получившее в последние десятилетия благодаря широкому
применению компьютерной техники классическое твердотельное моделирование
позволяет на основе решения систем уравнений поверхностей инструментов созда-
вать их адекватные геометрические модели. Установлено, что все виды моделей
можно разделить на две основные группы: модели с упрощенными поверхностями-
аналогами и модели с точными аналитически описываемыми поверхностями. Мо-
дели первой группы достаточны для последующего применения в расчетах, напри-
мер, жесткости инструментов, однако в расчетах процессов резания такие модели
могут показать неадекватные результаты: заточка задней поверхности сверл по
цилиндру или по винтовой поверхности обуславливает разные силы резания в про-
цессе обработки. Анализ элементов лезвий с использованием таких моделей пред-
ставляется сомнительным. В связи с этим все большее развитие получают модели
второй группы, включая описание сверл с инструментами второго порядка, что
нашло отражение в работах Ю.М. Панкратова. Модели с точным описанием от-
дельных поверхностей сверл нашли отражение и в публикациях зарубежных авто-
ров: J-F. Hsieh, P.D. Lin, K. Sambhav, S. G. Dhande, P. Tandon, S.G. Dhande, J.D. Jo-
vanovic, O. Spaic, E. Abele1, M. Fujara и др., однако в таких моделях сверло или
описывается не полностью, или такое описание требует итерационных расчетов и
дополнительных слабо формализованных методик. Проблема аналитического под-
хода заключается в том, что зачастую невозможно получить решение системы
сложных уравнений, которые описывают смежные участки двух и более поверхно-
стей инструмента. Было установлено, что все чаще применяются численные твер-
дотельные модели на основе алгебры множеств. К таким дискретным твердотель-
ным моделям относятся и воксельные модели для станков с ЧПУ, отраженные в
публикациях Г.К. Горанского и его учеников. Таким образом, анализ позволил
установить, что в настоящее время отсутствуют универсальные твердотельные ма-
тематические модели с точным описанием поверхностей спиральных сверл. Соот-
ветственно, невозможно в автоматизированном варианте проектирования получать
сетки конечных элементов таких инструментов для выполнения расчетов их жест-
кости и точного расчета сил резания при сверлении.
Далее были проанализированы публикации по расчету сил резания путем
применения численных моделей. Было установлено, что метод конечных элементов
(МКЭ) все чаще заменяется другими сеточными и бессеточными методами, имею-
щими известные преимущества в подобных расчетах (ALE, SPH, SPG, EFG и т.д.).
Все чаще моделируется резание не только резцами, но и сверлами. При этом начи-
нают появляться публикации по моделированию сверления композитных материа-
лов, широко применяемых в авиакосмической технике. Вместе с тем было установ-
лено, что задача расчета сил резания при сверлении в начальный момент обработки
не рассматривается, а именно в этот момент происходит образование начальной
конической поверхности, которая далее становится базирующей и определяет поло-
жение оси сверла. Было установлено, что моделирование композитов все еще осно-
вывается на идеализированном описании наполнителей и, таким образом, снижает
адекватность моделирования резания композитных заготовок.
Анализ третьей группы публикаций связан с расчетом податливости СиМСС
и РТК. Такие расчеты нашли отражение в современных публикациях (Ю.В. Васи-
левич, С.С. Довнар, Б.А. Еникеев, С.В. Каменев, А.Н. Поляков, М.А. Рубцов, В.И.
Туромша, M.D. Anand, R. Arora, M. Bugday, J. Cai, S.S. Dhami, R. Du, H. Fang, L.
Fang, K. He, G. Constantin, M. Karali, N. Prabhu, C. Pupaza, L.E. Ruban, A. Singh, Y.
Singh, L. Sun, X. Wang, J. Zhang, E. Zhou и др.) и показали одну из проблем: эти
расчеты, основанные на первоначальном создании CAD моделей и последующим
расчете по ним сеток конечных элементов (КЭ), обуславливают получение КЭ мо-
делей с несколькими миллионами узлов. Особое затруднение вызывает учет кон-
тактных пар. Такие расчеты сегодня возможны только с использованием суперком-
пьютерной техники и не могут быть использованы для повседневной практики тех-
нологов на имеющихся у них компьютерах. Кроме того, для таких расчетов требу-
ются полноценные CAD модели данных устройств, что является коммерческой
тайной их разработчиков. Следовательно, необходимо разработать методику для
практического решения этой задачи. На основании анализа была сформулированы
цель и задачи работы, определены методологические вопросы исследования.
Во второй главе приведены результаты разработки дискретных математиче-
ских моделей элементов технологической системы и процесса резания.
В первом подразделе второй главы были приведены зависимости для
дискретного твердотельного моделирования стандартных спиральных сверл.
В качестве параметров модели были приняты параметры сверл, отраженные в
государственных стандартах. На первом этапе были определены зависимости
для поверхностей стружечных канавок. Расчетная схема в радиальном сечении
сверла отражена на рисунке 1, а. Исходными данными являются параметры из
стандартов: d – диаметр сверла; d1 – диаметр сверла по спинкам; f – ширина
ленточки, которая может меняться по некоторому закону в зависимости от коор-
динаты z – оси сверла; a – половина толщины сердцевины; B – ширина пера; –
угол наклона винтовой канавки; – угол в плане; L – общая длина сверла; l –
длина рабочей части сверла, L1 – длина режущей части сверла. Кроме того, к
числу исходных данных относятся и параметры фрезы для получения стружечных
канавок сверла: Bm – ширина фрезы; r – радиус дуги большей окружности про-
филя фрезы; r1 – радиус дуги меньшей окружности профиля фрезы; b – расстоя-
ние от левого торца фрезы до центра окружности меньшего радиуса; c – расстоя-
ние от левого торца фрезы до риски; расстояние от наружного диаметра фрезы до
центра большей окружности h ; – угол между линией правого торца фрезы и ее
прямолинейной кромкой; f и hf – углы подточек ленточек; f , f1 , f h и f h1 –
размеры по ширине полных и подточенных участков ленточек; l1 и lh1 – длины
подточенных участков ленточек.
Для трех основных диапазонов варьирования полярного угла φ f в системе
стружечной канавки (Рисунок 1, в, г) получены следующие зависимости, позволя-
ющие определить точки вокселей внутри канавок (нестрогое неравенство) или на
их поверхностях (строгое равенство):
f = −…90 − , Ri r1 / cos( f ) ;(1)
f = −… − , Ri r1 ,(2)
f = −… − 270 , Ri (r − r1 ) cos( f − ) +((r − r1 )cos( f − ))2 − (r − r1 ) 2 +r 2 ,(3)
где в формуле (1), как это следует из рисунка 1, г, угол φf изменяется от оси x по
часовой стрелке, при этом от точки P1 до точки P2 используется уравнение прямой
линии в полярной системе координат; в формуле (2) от точки P2 до точки P3 угол φf
изменяется от оси x по часовой стрелке на величину f = − до угла f = , при
этом = − + . Угол определяется по одному из двух вариантов в зависимо-
сти от того, какой параметр чертежа использует конструктор. В работе получены
все необходимые зависимости для подстановки в вышеприведенные формулы.
Рисунок 1 – Радиальное сечение сверла (а), его вид сбоку (б), осевое сечение
фрезы для получения винтовой канавки сверла (в) и радиальное сечение
сверла для определения параметров ленточки и спинки (г)
Одним из важных параметров для расчета поверхностей канавок сверла яв-
ляются координаты центра системы координат канавки в системе координат свер-
ла: a f и b f , которые, как видно из рисунка 1, а, определяются соотношениями:
a f = −r1 − a , b f = S + Q / cos( ) − 0.5d + {r1 (1 − cos(2(n − 1) / n − ))} ,(4)
где r1 и a – параметры из стандартов, описанные выше; выражение в скобках учи-
тывает возможное количество перьев n для других инструментов. Также были по-
лучены все остальные необходимые параметры (S и Q), которые необходимо ис-
пользовать в итоговой зависимости для расчета координат точек поверхностей пер-
вой и второй стружечных канавок ( j = 1 и j = 2 ), а именно координат вектора
( x fi , y fi , z fi ) в системе координат этих канавок. Каждый такой вектор соответствует
вектору ( xi , yi , zi ) текущей точки с номером i в системе координат сверла для чего
используется общеизвестное уравнение преобразования систем координат вида:
x fi a f xi
y fi = M z (− − f ) M z ( + f ) b f − yi , (5)
0 z
z fi i
где Mz(…) – матрица преобразований поворота; χ=(0,π) – угол, отражающий
первую и вторую стружечные канавки, соответственно; ωf – угол поворота теку-
щего радиального сечения сверла, в зависимости от текущего значения аппликаты
z , связанного с винтовой направляющей линией стружечной канавки. Были полу-
чены зависимости для расчета профилей стружечной канавки сверла для различ-
ных условий касания участков этого профиля с окружностью его сердцевины
На втором этапе расчета сверл определены зависимости для поверхностей
ленточек и спинок сверла. По аналогии с формулами (1)…(3) определены формулы
для расчета граничных полярных углов φ1 … φ8, характеризующих элементы лезвий
на калибрующей части сверла (см. рисунок 1, г). Для этих диапазонов получены урав-
нения прямых линий и дуг окружностей в полярной системе координат (нестрогое не-
равенство дает координаты точек вокселей тела, а равенства – поверхностей сверла):
= 1…2 , R1 0.5d ,(6)
= 2 …3 , R1 0.5d cos( f ) / cos( − 0.5 − f − 2 ) ,(7)
при этом, если z L − L1 − l1 , то R1 = 0.5d ,
= 3…4 , R1 ( f − a) / cos() ,(8)
= 4 …5 , R1 0.5d1,(9)
= 5 …6 , R1 0.5 f h1 / cos( − h ) , h = 0.5(6 + 7 ) ,(10)
= 6 …7 , R1 0.5d ,(11)
= 7 …8 , R1 0.5d cos( f ) / cos( − 0.5 − f − 7 ) ,(12)
при этом, если z L − L1 − lh1, то R1 = 0.5d .
Далее были получены зависимости, отражающие изменения параметров
сверла в его осевой плоскости. На третьем этапе расчета сверл были получе-
ны зависимости для расчета их главных задних поверхностей. По отдельности
были рассмотрены четыре случая заточки сверл: по плоскости, по цилиндриче-
ской, по коническим поверхностям и по винтовой поверхности.
Для расчета точек сверла для заточки по плоской главной задней поверхно-
сти (рисунок 2, а) получены зависимости:
Ra ,1 (i , z ) ,(13)
R (i , z ) = D* / cos(i − arctan(V / W )) , D* = −( Fz + D) .(14)
V = sin(0 ) , W = cos( 0 ) / tg() , F = cos( 0 ) , D = a sin( 0 ) − L cos( 0 ) .(15)
В этой формуле i – не угол в плане сверла , а полярный угол радиус-вектора;
0 –задний угол в плоскости, параллельной оси сверла.
Были получены и другие зависимости для расчета остальных параметров и
расчета точек второй ( R , 2 ) главной задней поверхности сверла.
Для расчета точек для заточки по цилиндрической поверхности были полу-
чены зависимости на основе расчетной схемы рисунка 2, б. Расчет выполняется
по аналогичной формуле (13), при этом:
y = (−W − W 2 − 4VQ ) / 2V и R (i , z ) = y / sin(i ) ,(16)
где для расчета параметров для y были получены соответствующие зависимости.
Аналогично были получены и зависимости для расчета точек главных зад-
них поверхностей при заточках по конусу. В отличие от предыдущего случая:
Rc* ( z ) = kz + Rн , где k = tg() – тангенс угла конуса; Rн – радиус меньшей окруж-
ности усеченного конуса в сечении, проходящем через начало системы координат
сверла. На основании расчетных схем рисунка 3 были получены подобные выше-
приведенным для случая цилиндра зависимости для расчета требуемых координат
при заточках по конусу.
Рисунок 2 – Осевое сечение сверла у режущей части; заточка по плоскости (а);
осевое и радиальное сечения сверла и цилиндрическая главная задняя поверхность (б)
На последнем этапе описания главных задних поверхностей сверла по рас-
четной схеме рисунка 4 путем решения уравнения характеристики N V = 0 , ши-
роко представленного в работах П.Р. Родина, были получены зависимости для за-
точки по винтовой задней поверхности с параметрами i и z ‘ ‘ :
x = (Cc cos(i ) + ptg()) cos(i ) + z ‘ ‘ tg() sin(i )
y = (Cc cos(i ) + ptg()) sin(i ) + z ‘ ‘ tg() cos(i ) + C (i )) ,(17)
z = z ‘ ‘+ p
i
где x’ ‘ = Cc cos(i ) + ptg() , y’ ‘ = − z ‘ ‘ tg() ,(18)
где p – параметр винтового движения, τ – угол между плоским торцом абразивно-
го инструмента и осью сверла; Cc и C (i ) – параметры установки и движения аб-
разивного инструмента.
Полученные координаты были использованы в формуле, аналогичной (13).
Рисунок 3 – Осевое и радиальное сечения сверла и коническая главная
задняя поверхность: а) тип заточки 1, б) тип заточки 2
Рисунок 4 – Осевое сечение сверла
и след производящей поверхности
абразивного круга с произвольной
точкой M
На четвертом, завершающем этапе расчета спиральных сверл были по-
лучены итоговые зависимости расчета вокселей их тел и поверхностей. Полу-
ченные выше зависимости (1)…(18) и другие зависимости, описанные в диссерта-
ции, позволяют с учетом нижеприведенных формул определить координаты вок-
селей тел (19) и поверхностей (20) этих инструментов.
( Ri ) ( R1 ) ( R,1 ) ( R, 2 ) ,(19)
(( = Ri ) ( R1 ) ( R,1 ))
(( = Ri ) ( R1 ) ( R, 2 ))
(( Ri ) ( = R1 ) ( R,1 )) .(20)
(( Ri ) ( = R1 ) ( R, 2 ))
(( Ri ) ( R1 ) ( = R,1 ))
(( Ri ) ( R1 ) ( = R, 2 ))
В выражении (20) первая строка является условием принадлежности вокселей
передней поверхности и стружечной канавке для первого режущего клина сверла,
вторая строка, аналогично, для второго; третья строка является условием принад-
лежности вокселей к главной задней поверхности первого режущего клина сверла,
четвертая, аналогично для второго; пятая строка необходима для принадлежности
вокселей к ленточке и спинке, примыкающей к первому режущему клину и шестое
аналогично для второго клина. Повторный учет главных задних поверхностей в дан-
ном выражении отличает его от аналогичных решений для других инструментов
Выполненные исследования показали, что созданная единая дискретная твердо-
тельная модель сверл, устанавливающая взаимосвязь между координатами узловых
точек множеств вокселей поверхностей и тел почти всех стандартных сверл и опреде-
ленных в таких стандартах параметров этих инструментов, является достаточной для
получения указанных множеств и на основе этого сеток их конечных элементов.
Во втором подразделе второй главы были приведены зависимости для
дискретного твердотельного моделирования СиМСС. Показано, что для расче-
та податливости такого оборудования, которое представляет собой сборочное из-
делие, в первом приближении можно применить эквивалентную этому оборудо-
ванию деталь. Тогда на основании полных или упрощенных триангулированных
(для сохранения технической тайны) его CAD моделей можно получить регуляр-
ные сетки вокселей дискретного твердотельного моделирования. С этой целью
было предложено использовать следующие зависимости:
xmin xi xmax y min yi y max z min zi z max ,(21)
xmin = min{ x ( yi , z i )} , x max = max{ x ( yi , z i )} ,(22)
y min = min{ y ( xi , z i )} , y max = max{ y ( xi , z i )} ,(23)
z min = min{ z ( xi , y i )} , z max = max{ z ( xi , y i )} ,(24)
xi+1 = xi + x, yi+1 = yi + y, zi+1 = zi + z ,(25)
где xi , yi и z i – координаты каждой i -той узловой точки вокселя сетки;
x( yi , zi ) , y( xi , zi ) и z( xi , y i ) – координаты точек поверхностей CAD моделей,
включая триангулированные STL модели, для соответствующих значений координат
узлов вокселей, определяются по уравнениям поверхностей деталей СиМСС.
min и max – означает: для x , соответственно, слева и справа; для y , соответ-
ственно, спереди и сзади; для z , соответственно, снизу и сверху для каждого от-
резка линии внутри устройства. Отрезки должны лежать на прямых линиях, па-
раллельных координатным осям и проходящим через узел текущего вокселя с ко-
ординатами ( xi , yi , z i ); x , y и z – шаги воксельной сетки.
В диссертации приведены формулы для расчета по приведенным зависимо-
стям сетки узлов восьми-узловых конечных элементов оборудования.
В третьем подразделе второй главы были приведены зависимости для
моделирования процесса резания спиральными сверлами фрагментов заготовок
из металлических и композитных материалов. Были использованы КЭ модели ин-
струментов и SPG модели заготовок, для чего были отобраны феноменологиче-
ские модели материалов и выполнено моделирование волоконно-армированных и
дисперсно-армированных композитов. Отличительной особенностью моделей по-
следних стали исходные данные, полученные на основе предложенного авторско-
го подхода: сканирования на планшетном сканере частиц наполнителя. Это поз-
волило получить модели, наиболее близкие к реальным композитным структурам.
Таким образом, во второй главе были отражены результаты теоретических ис-
следований, связанных с разработкой единой комплексной твердотельной модели
стандартных спиральных сверл F1 , численной модели сверлильного оборудования
на основе его CAD моделей F2 , дискретной твердотельной модели фрагментов ме-
таллических и композитных заготовок F4 , а также модели F3 расчета сил резания на
основе МКЭ-SPG методов расчета и моделей F1 и F4 . Объединение всех этих трех
моделей дает модель точности сверления отверстий с податливым оборудованием, а
именно: величину смещения вершины сверла r :
r = F{F1 (d , d1 , f, a, B,…); F2 (( x( y, z), y( x, z)), z( x, y); F3 ( F1 , F4 ( xw (…), yw (…), z w (…)), nсв , sOсс )} (26)
В третьей главе приведены результаты верификации полученных выше
моделей и методик расчета. В первом и втором ее подразделах произведена ве-
рификация математической модели стандартных спиральных сверл путем
расчета облаков точек вокселей их поверхностей и расчета их КЭ (рисунок 5, а),
расчета деформаций (рисунок 5, б), проведения натурных экспериментов по опре-
делению жесткости сверл (рисунок 5, в).
Рисунок 5 – Инструменты, их узловые точки и КЭ (а), расчеты деформаций сверл
и зенкера (б), натурные эксперименты (в), моделирование сверления (г)
Расчеты были выполненные для семи сверл и зенкера. На рисунке 5, а видно,
что воксельные и КЭ сетки повторяют поверхности сверл. Расчеты жесткости
трех сверл были сопоставлены с натурными экспериментами. Отклонение экспе-
риментальных и расчетных данных не превысило 1%.
В третьем подразделе третьей главы выполнен расчет сил резания пу-
тем МКЭ–SPG моделирования процесса стружкообразования спиральными свер-
лами в начальный период обработки. Полученные картины деформаций и распре-
деления напряжений в стальной заготовке в разные моменты времени сверления
(рисунок 5, г), а также полученные графики сил и крутящего момента показали
результаты, не противоречащие публикациям других исследователей для условий
полного заглубления режущей части сверла.
В четвертом подразделе третьей главы приведены расчеты воксельных и
КЭ моделей СиМСС с ЧПУ и верификация этих расчетов натурными экспери-
ментами. Для подтверждения всеобщности разработанной методики расчета в ка-
честве примера первоначально были выполнены расчеты воксельной сетки станка
HAAS VF-2-I и на основе этого далее выполнены расчеты его деформаций. Далее
были выполнены расчеты для модульного сверлильного станка с ЧПУ. Первона-
чальная попытка рассчитать его податливость типовыми методами в WorkBench
оказалась неудачной по причине размерности сетки свыше одного миллиона с не-
допустимо различными по величине размерами ее КЭ. В связи с этим по разрабо-
танным формулам и созданной программе были рассчитаны воксельные и КЭ сет-
ки для трех характерных положений его узлов и рассчитаны его деформации (ри-
сунок 6, а). Для таких же положений были выполнены эксперименты по определе-
нию смещений детали для крепления привода вращения сверла (рисунок 6, б). Ока-
залось, что экспериментальные и расчетные данные отличаются на порядок.
Анализ позволил установить, что существенные погрешности были внесены
неадекватным описанием передаточных узлов приводов подач. Замена их моделей
на определенные в экспериментах модели эквивалентных деталей позволили по-
лучить новые воксельные и КЭ модели оборудования. Отличия расчетных данных
от экспериментальных в этом случае не превысили 18%.
В четвертой главе приведен пример практического применения матема-
тических моделей элементов технологической системы и обработки отверстий
сверлением, даны методики расчета, предоставлены проекты по усовершен-
ствованию сверл и оборудования. Для рассмотренного выше МСС с ЧПУ и свер-
ла диаметром 3,25 мм с использованием изложенных выше моделей, методики
проектирования данной технологической операции, разработанного и заимство-
ванного программного обеспечения был произведен расчет смещений режущей ча-
сти сверла при обработке заготовки из АЦ4Мг, которые составили 250 мкм. Для
этих же условий был реализован и натурный эксперимент (получено 105 кониче-
ских углублений, рисунок 6, в). Статистическая обработка его результатов показа-
ла, что отклонения расчетных и экспериментальных данных не превысили 20%.
По результатам исследований была разработана методика расчета увода
оси сверла в момент засверливания, включающая в себя расчет сверл, оборудова-
ния, процесса стружкообразования. Методика носит итерационный характер: если
в результате расчетов смещение сверла выходит за поле позиционного допуска, то
сначала вносятся изменения в сверло, расчеты повторяются, и при удовлетворе-
нии точности выполняется расчет сверла на прочность. По результатам такого
расчета принимаются дальнейшие рекомендованные в методике решения.
Рисунок 6 – Деформации СиМСС (а), измерение его податливости (б), сетка
просверленных отверстий и их отклонения от регулярной сетки прямых линий (в)
Во втором подразделе четвертой главы были рассмотрены усовершен-
ствованные конструкции сверл и оборудования для сверления отверстий. Для
уменьшения увода сверл предложен вариант подточки поперечной режущей
кромки двумя плоскостями, расположенными под заданными чертежом углами в
плане с образованием правильной пирамиды у оси сверла. С использованием мо-
дели и программ выполнены прогнозные расчеты и натурные эксперименты, под-
твердившие эффективность данного решения. Для СиМСС с ЧПУ балы изготов-
лена дополнительная магнитная опора, что позволило увеличить зону обработки.
Были предложены защищенные двумя патентами усовершенствования опор –
внесение дополнительной опоры, расположенной между двумя группами узлов
оборудования: группой переноса и группой обработки. Был рассчитан опорный
элемент станка переменой жесткости с термоактивируемым композитом: доказана
достаточность сил примагничивания для исключения смещения этой опоры от сил
резания.
ОСНОВНЫЕ РЕЗУЛЬТАТЫ И НАУЧНЫЕ ВЫВОДЫ
Основные результаты
1. Решена задача совершенствования методики автоматизированного расче-
та инструментов и податливого оборудования для повышения точности сверления
отверстий на основе прогноза отклонения расположения их осей на детали с ис-
пользованием МКЭ-SPG расчетов по разработанным дискретным твердотельным
моделям стандартных спиральных сверл, технологического оборудования, фраг-
ментов заготовок и процесса сверления, а также созданным на их основе методике
и программного обеспечения.
2. Разработаны дискретная твердотельная модель стандартных спиральных
сверл и податливого технологического оборудования (по предоставленным его
твердотельным моделям) и основанные на этих моделях их конечно-элементные
модели, МКЭ-SPG модели процесса резания сверлами фрагментов заготовок из
металлов и композитных материалов.
3. На основе созданных экспериментальных установок проведены натурные
эксперименты по определению жесткости сверл, податливого технологического
оборудования и точности сверления для верификации разработанных моделей,
методики расчета и компьютерной программы.
4. Спроектированы и изготовлены усовершенствованный инструмент –
сверло с плоскими подточками поперечной режущей кромки и дополнительные
опоры для податливого оборудования, позволяющие снизить такую податливость
и, как следствие, повысить точность обработки.
Основные научные выводы
1. Полученная численная математическая модель точности обработки от-
верстий стандартными спиральными сверлами и податливым оборудованием,
включающая в себя дискретную твердотельную модель этих сверл и оборудова-
ния, фрагментов заготовок и МКЭ-SPG модель процесса сверления, является до-
статочной для автоматизированного расчета смещений режущей части сверла в
начальный момент времени обработки и прогнозирования на этой основе откло-
нения оси получаемого на детали отверстия. Отклонения расчетных по этой моде-
ли и экспериментальных данных не превышают 20%.
2. Доказано, что созданная дискретная твердотельная модель стандартных
спиральных сверл является геометрически точной, поскольку включает в себя
точное (без допущений) описание геометрии всех элементов этих инструментов;
универсальной, поскольку охватывает подавляющее большинство конструкций
таких сверл из всех государственных стандартов на данные инструменты и ком-
плексной, поскольку позволяет рассчитать не только геометрические характери-
стики данных инструментов, но и получить сетки конечных элементов для реше-
ния физических задач: расчета жесткости инструментов и моделирования с их ис-
пользованием процесса резания.
3. Предложенная методика дискретного твердотельного моделирования по-
датливого технологического оборудования на основе принимаемых в качестве ис-
ходных данных его твердотельной модели является достаточной для расчета по-
датливости, при этом является обоснованной замена сборки оборудования его эк-
вивалентной деталью, а также является обоснованной замена передаточных узлов
приводов подач такого оборудования их эквивалентными по жесткости деталями.
Необходимое для практического использования количество узлов конечно-
элементной модели в этом случае не превышает одного миллиона. Отклонения
расчетных и экспериментальных смещений в этом случае не превышают 18%.
Обработка на компьютеризированном технологическом оборудовании:
станках с числовым программным управлением (ЧПУ) и робототехнических
комплексах (РТК) все шире используются в машиностроении. Такое
технологическое оборудование применяется как для обработки заготовок малых
размеров, так и для крупногабаритных заготовок, например, фюзеляжей
самолетов, ракетно-космической техники, морских судов и наземного транспорта.
Однако применение крупногабаритных станков в последнем случае, например,
для сверления отверстий ограничено по причине высокой стоимости такого
оборудования. Как правило, сверление таких отверстий приходится выполнять
вручную с использованием электродрелей. Робототехнические комплексы
отличаются большим рабочим пространством при их малой массе и меньшей
стоимости по сравнению с аналогичными компьютеризированными станками. В
связи с этим, применение роботов оказывается целесообразным в производстве
указанных выше крупногабаритных деталей. Несмотря на очевидные
преимущества, промышленные манипуляционные роботы все еще не находят
широкого применения для выполнения процессов резания инструментами: темпы
внедрения таких роботов намного меньше темпов внедрения сборочных,
сварочных и других аналогичных роботов. Кроме того, многоосевые возможности
таких роботов зачастую являются избыточными для сверления отверстий.
Нередко для операций сверления применяются более простые устройства,
специально изготовленные станки (модули, машины с автоматической подачей
инструментов) с приводами суппортов по трем координатам [1–3]. Но и эти
устройства отличаются высокой податливостью. Факт низких темпов внедрения
подобного технологического оборудования обусловлен одним из его
существенных недостатков – высокой податливостью и, как следствие, большими
уводами инструментов от сил резания. В частности, в начальный момент времени
сверления отверстий на инструменте возникает радиальная составляющая
суммарной силы резания, которая обуславливает как деформации сверла, так и
деформации такого оборудования. В этот момент режущая часть сверла
смещается от требуемого идеального положения и обуславливает смещение оси
получаемого отверстия. Зачастую это приводит к появлению негодных деталей. В
связи с этим, при проектировании операций сверления с использованием такого
нежесткого технологического оборудования необходимо прогнозировать
вероятность появления негодных деталей и при необходимости корректировать
режим обработки или вносить изменения в технологическую систему, включая
совершенствование ее конструкции. Для реализации такого прогноза на практике
разработчикам технологических операций машиностроительных предприятий
необходимо иметь соответствующее программное обеспечение, в основе которого
лежат математические модели инструмента, технологического оборудования и
процесса сверления. Большой рост количества научных публикаций,
посвященных данной тематике, указанное выше сдерживание применения
специальных сверлильных станков и РТК для процессов резания показывают, что
данная задача все еще до конца не решена и степень ее разработанности невысока.
Таким образом, обеспечение необходимой точности получения отверстий
сверлением с использованием нежесткого компьютеризированного
технологического оборудования, включая РТК путем компьютерного
моделирования операций обработки на основе универсальных комплексных
математических моделей сверл, технологического оборудования и процессов
сверления является актуальной задачей машиностроения.
Степень разработанности темы исследования
В производстве различных изделий существенную долю занимает
изготовление крупногабаритных деталей. Такие детали как обшивки, панели,
шпангоуты изготавливаются для авиакосмической техники, в судостроении,
наземном транспорте. Весомую долю всех операций изготовления составляет
сверление отверстий для заклепочных соединений. Необходимость сопряжения
отверстий обуславливает применение позиционных допусков на их расположение.
Для сверления таких отверстий применяется специальное и модульное сверлильное
оборудование, которое используется взамен дорогих крупногабаритных
традиционных станков. Все чаще в качестве обрабатывающего оборудования
применяются и робототехнические комплексы (РТК). Однако, несмотря на
преимущества, использование указанного оборудования все еще ограничено, что
связано с одним из его существенных недостатков – большой податливостью и, как
следствие, большими смещениями инструмента от сил резания. В частности, в
начальный момент времени сверления отверстий на инструменте возникает
радиальная составляющая суммарной силы резания, которая обуславливает как
деформации самого сверла, так и деформации такого оборудования. В этот момент
режущая часть сверла смещается от требуемого идеального положения, что
вызывает смещение оси получаемого отверстия. Зачастую это приводит к
появлению негодных деталей. В связи с этим при проектировании технологической
операции сверления с использованием податливого оборудования технологу
необходимо спрогнозировать вероятность появления негодных деталей и при
необходимости вместе с конструкторами изменить инструмент или это
оборудование. Для реализации такого прогноза необходимо иметь соответствующее
программное обеспечение, в основе которого лежат математические модели
инструмента, оборудования и процесса сверления. Большой рост количества
научных публикаций, посвященных данной тематике, и указанное выше
сдерживание применения специального и модульного сверлильного оборудования
для процессов резания показывают, что данная задача все еще до конца не решена.
Таким образом, обеспечение необходимой точности расположения отверстий,
полученных сверлением с использованием податливого оборудования, путем
компьютерного моделирования операций обработки на основе универсальных
комплексных математических моделей сверл, этого оборудования и процессов
сверления является актуальной задачей машиностроения.
Исходя из этого, были определены цель и задачи данного исследования.
Целью диссертационной работы является совершенствование элементов
технологической системы на основе разработки методик расчета спиральных
сверл, податливого технологического оборудования, увода этих сверл в момент
засверливания для повышения точности расположения осей отверстий в
крупногабаритных заготовках.
Для достижения данной цели необходимо решить следующие задачи.
1) Разработать единую универсальную дискретную твердотельную модель
стандартных спиральных сверл с учетом их стандартизованных геометрических
характеристик.
2) Разработать способ получения дискретной твердотельной и на основе ее
малоразмерной конечно-элементной моделей для податливого технологического
обрабатывающего оборудования.
3) Произвести верификацию данных моделей путем расчета облаков точек
вокселей и на основе этого конечно-элементных моделей для ряда представителей
таких элементов технологической системы, а также путем проведения натурных
экспериментов.
4) Разработать МКЭ-SPG модель процесса стружкообразования
стандартным спиральным сверлом заготовок из металлов и композитов и
выполнить тестовый расчет этого процесса в начальный момент засверливания с
определением радиальной составляющей суммарной силы резания на сверле.
5) Разработать методику расчета точности сверления, включающую
методики расчета инструментов, податливого технологического оборудования,
разработать на их основе программное обеспечение и верифицировать их
натурным экспериментом. Разработать усовершенствованный инструмент и
дополнительные устройства для податливого технологического оборудования,
направленные на повышение точности обработки отверстий сверлением.
Реализовать результаты исследований в производстве и учебном процессе.
Научная новизна работы: Впервые разработаны численные
математические трехмерные модели спиральных сверл, податливого
технологического оборудования и фрагментов заготовок из гомогенных и
композитных материалов, отличающиеся единой дискретной (воксельной)
основой, и связанные с этими моделями конечно-элементные и SPG модели
стружкообразования при засверливании, объединяющая их математическая
модель точности сверления с указанным технологическим оборудованием,
позволившие обоснованно усовершенствовать на такой базе данные
спиральные сверла и оборудование. Новизна соответствует п. 4 паспорта
специальности (см. ниже).
Теоретическая и практическая значимость работы. Теоретическая
значимость работы заключается в решении задачи дискретного твердотельного
моделирования группы инструментов – стандартных спиральных сверл и
компонентов податливого технологического оборудования механообработки, что
позволяет получать их геометрические и на этой основе физические (конечно-
элементные) модели для последующего определения смещений данных элементов
технологической системы от сил резания и, таким образом, через увод сверл
определять смещения осей отверстий получаемых деталей. Практическая
значимость работы заключается в решении актуальной технологической
задачи – предоставление разработчикам технологических операций средств
прогнозирования точности расположения получаемых в деталях отверстий путем
автоматизированного расчета деформаций стандартных спиральных сверл и
податливого технологического оборудования от действующих в процессе
обработки отверстий сил резания и предоставление на этой основе возможностей
по целенаправленному совершенствованию инструментов и данного
оборудования.
Методология и методы исследования. Объектом исследования являются
инструменты, податливое технологическое оборудование и процесс начала
сверления отверстий стандартными спиральными сверлами с использованием
такого оборудования. Предметом исследования является зависимость
радиального смещения режущей части спирального сверла в процессе
засверливания от жесткости этого сверла и податливости обрабатывающего
технологического оборудования. Направленность исследований связана с
обеспечением технически эффективного процесса обработки, а именно, с
обеспечением повышенной точности сверления отверстий в крупногабаритных
заготовках в условиях использования податливого технологического
оборудования. Методика исследования как система конкретных приемов,
способов его осуществления: получение на основе численных подходов
математических зависимостей, позволяющих в виде множеств узловых точек
описать поверхности, тела инструментов и податливого технологического
оборудования, максимально соответствующие их реальным аналогам и получение
на этой основе численных (МКЭ-SPG) моделей для физического моделирования
процесса стружкообразования сверлением путем расчета сил резания и
деформаций элементов технологической системы. Разработка на основе этих
зависимостей устройств для повышения точности получения отверстий
сверлением в крупногабаритных заготовках. Аппаратная и программная база
исследований: исследований: модульные станки с ЧПУ, стандартные спиральные
сверла, измерительная аппаратура исследования процессов резания,
вычислительная техника, средство разработки компьютерных программ Delphi 7,
академические версии программ численного моделирования ANSYS и LS-DYNA.
Соответствие темы работы приоритетным или прогнозным направлениям
развития научных исследований: данная тема отвечает технологическому
направлению «Фабрики будущего», плана мероприятий («дорожной карты»)
«Технет» (передовые производственные технологии) Национальной
технологической инициативы, одобренной 14 февраля 2017 года на заседании
президиума Совета при Президенте Российской Федерации по модернизации
экономики и инновационному развитию России.
Положения, выносимые на защиту:
– численная математическая модель точности обработки отверстий
стандартными спиральными сверлами с податливым технологическим
оборудованием, в которой установлена математическая взаимосвязь между
стандартными параметрами конструктивных элементов сверл, твердотельными
моделями оборудования, параметрами фрагментов обрабатываемых заготовок и
параметрами режима обработки, с одной стороны, и смещением режущей части сверл
в период засверливания, определяющим положение осей этих отверстий в получаемой
детали, с другой стороны. Модель отличается от известных использованием в ней в
качестве единой основы численного (воксельного) геометрического моделирования и
связанного с ним конечно-элементного и SPG физического моделирования объектов и
процессов в технологической системе;
– единая универсальная математическая модель рабочей части стандартных
спиральных сверл в составе модели точности, объединяющая в себе дискретную
твердотельную (воксельную) и конечно-элементные модели. Модель отличается
использованием в ней численного (воксельного) геометрического моделирования сверл,
что обеспечивает ее универсальность;
– методика расчета вокселей податливого оборудования на основе его
твердотельных моделей и расчета на этой основе регулярных малоразмерных
конечно-элементных сеток, отличающуюся использованием эквивалентных деталей
для сборок технологического оборудования и эквивалентных деталей их
передаточных узлов приводов подач. Методика отличается расчетом общей
воксельной сетки оборудования на основе его представления как одной детали и
представления его передаточных узлов приводов подач эквивалентными деталями;
– методика расчета координат точки пересечения оси получаемого отверстия с
поверхностью детали на основе расчета деформаций элементов технологической
системы (стандартных спиральных сверл и податливого оборудования),
отличающаяся единством расчетов на основе дискретных твердотельных моделей,
сеток конечных элементов и связанных с этим МКЭ и SPG расчетов сил резания с
использованием моделей фрагментов заготовок из гомогенных и композитных
материалов;
– результаты верификации предложенных моделей, методик, компьютерных
программ на основе реализации натурных экспериментов, связанных с определением
деформаций выбранных сверл и податливого технологического оборудования и
определением положений осей отверстий при сверлении с использованием указанных
элементов технологической системы;
– конструкции усовершенствованных сверл, отличающихся подточкой
поперечной режущей кромки двумя плоскостями, расположенными под углами в
плане сверла с образованием правильной пирамиды у его оси, и технологического
оборудования, отличающегося наличием дополнительной перемещаемой опоры,
расположенной между двумя группами узлов оборудования – группой переноса и
группой обработки. .
Степень достоверности и апробация результатов. Полученные на
основании разработанных математических моделей результаты расчетов были
верифицированы натурными экспериментами: рассчитанные смещения
выбранного технологического сверлильного оборудования отклонялись от
смещений в натурных экспериментах не более, чем на 18%; рассчитанные изгибы
выбранных сверл отличались от изгибов в натурных экспериментах не более, чем
на один процент; рассчитанные величины смещений рабочей части выбранного
сверла при обработке заготовки из АЦ4Мг на выбранном технологическом
оборудовании отличаются от отклонений полученных в натурных экспериментах
осей отверстий не более, чем на 20%.
Основные результаты
1. Решена задача совершенствования методики автоматизированного
расчета инструментов и податливого оборудования для повышения точности
сверления отверстий на основе прогноза отклонения расположения их осей на
детали с использованием МКЭ-SPG расчетов по разработанным дискретным
твердотельным моделям стандартных спиральных сверл, технологического
оборудования, фрагментов заготовок и процесса сверления, а также созданным на
их основе методике и программного обеспечения.
2. Разработаны дискретная твердотельная модель стандартных спиральных
сверл и податливого технологического оборудования (по предоставленным его
твердотельным моделям) и основанные на этих моделях их конечно-элементные
модели, МКЭ-SPG модели процесса резания сверлами фрагментов заготовок из
металлов и композитных материалов.
3. На основе созданных экспериментальных установок проведены натурные
эксперименты по определению жесткости сверл, податливого технологического
оборудования и точности сверления для верификации разработанных моделей,
методики расчета и компьютерной программы.
4. Спроектированы и изготовлены усовершенствованный инструмент –
сверло с плоскими подточками поперечной режущей кромки и дополнительные
опоры для податливого оборудования, позволяющие снизить такую податливость
и, как следствие, повысить точность обработки.
Основные научные выводы
1. Полученная численная математическая модель точности обработки
отверстий стандартными спиральными сверлами и податливым оборудованием,
включающая в себя дискретную твердотельную модель этих сверл и
оборудования, фрагментов заготовок и МКЭ-SPG модель процесса сверления,
является достаточной для автоматизированного расчета смещений режущей части
сверла в начальный момент времени обработки и прогнозирования на этой основе
отклонения оси получаемого на детали отверстия. Отклонения расчетных по этой
модели и экспериментальных данных не превышают 20%.
2. Доказано, что созданная дискретная твердотельная модель стандартных
спиральных сверл является геометрически точной, поскольку включает в себя
точное (без допущений) описание геометрии всех элементов этих инструментов;
универсальной, поскольку охватывает подавляющее большинство конструкций
таких сверл из всех государственных стандартов на данные инструменты и
комплексной, поскольку позволяет рассчитать не только геометрические
характеристики данных инструментов, но и получить сетки конечных элементов
для решения физических задач: расчета жесткости инструментов и
моделирования с их использованием процесса резания.
3. Предложенная методика дискретного твердотельного моделирования
податливого технологического оборудования на основе принимаемых в качестве
исходных данных его твердотельной модели является достаточной для расчета
податливости, при этом является обоснованной замена сборки оборудования его
эквивалентной деталью, а также является обоснованной замена передаточных
узлов приводов подач такого оборудования их эквивалентными по жесткости
деталями. Необходимое для практического использования количество узлов
конечно-элементной модели в этом случае не превышает одного миллиона.
Отклонения расчетных и экспериментальных смещений в этом случае не
превышают 18%.
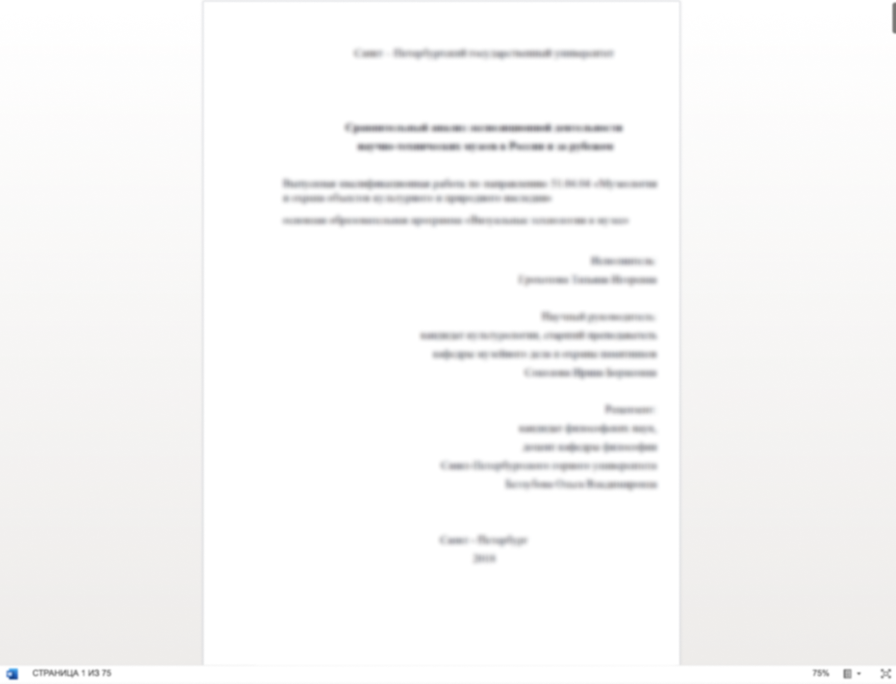
Публикации автора в научных журналах
Помогаем с подготовкой сопроводительных документов
Хочешь уникальную работу?
Больше 3 000 экспертов уже готовы начать работу над твоим проектом!