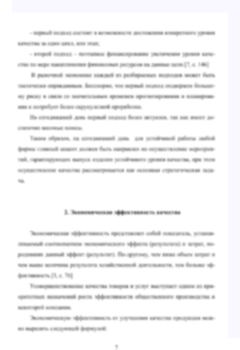
«Технологическое обеспечение послеремонтного ресурса трибомеханической системы “кольцо подшипника -корпус” коробок передач транспортно-технологических машин в АПК»
Введение
Глава 1. Технологические способы обеспечения послеремонтного ресурса трибомеханичской системы «кольцо подшипника – корпус»
транспортно – технологических машин
1.1 Сравнительный анализ доремонтной и послеремонтной
долговечности коробки передач
1.2 Анализ схем конструкций подшипниковых узлов коробок передач
1.3 Силы, действующие в подшипниковых опорах
1.4 Причины и процесс изнашивания отверстий под подшипники
в корпусных деталях
1.5 Существующие способы обеспечения послеремонтного ресурса
трибомеханической системы «кольцо подшипника – корпус»
1.6 Способ восстановления посадочных отверстий в коробках передач
полимерными материалами
Глава 2. Теоретические предпосылки повышения долговечности
трибомеханической системы «кольцо подшипника – корпус»
2.1 Структурная модель процесса изнашивания трибомеханической системы «кольцо подшипника – корпус»
2.2 Моделирование изнашивания деталей
трибомеханической системы «кольцо подшипника – корпус»
2.3 Расчетная модель изгиба наружного кольца подшипника
2.4 Теоретические обоснование несущей способности полимерной пленки
Глава 3. Методика экспериментальных исследований
3.1 Программа экспериментального исследования
3
3.2 Методика исследования величины износа отверстий
под подшипники качения
3.3 Методика профилографических исследований
изношенных поверхностей
3.4 Методика исследования модуля упругости полимерного материала
3.5 Методика исследования реологических свойств плёнок полимерного материала
3.6 Методика исследования деформационно-прочностных свойств
плёнок полимерного материала
3.7 Методика исследование изгиба наружного кольца подшипника
невосстановленной и восстановленной трибомеханической
системы «кольцо подшипника – корпус»
3.8 Методика исследования напряженно-деформированного состояния
трибомеханической системы «кольцо подшипника – корпус»
поляризационно – оптическим способом
3.9 Методика проведения эксплуатационных испытаний
Глава 4. Результаты экспериментальных исследования и их анализ
4.1 Определение параметров шероховатостей
изношенных поверхностей трибомеханической
системы «кольцо подшипника – корпус» коробок передач
4.1 Результаты микрометражных исследований отверстий под подшипники коробок передач транспортно-технологических машин АПК
4.3 Результаты исследования модуля упругости полимерного материала
4.4 Определение реологических свойств пленок
полимерного материала
4.5 Результаты исследования деформационно – прочностных свойств пленок
полимерного материала
4.6 Результаты исследования напряженно-деформированного состояния восстановленной трибомеханической системы «кольцо подшипника – корпус»
4.7 Результаты исследования изгиба наружного кольца подшипника
4.8 Результаты эксплуатационных испытаний
Глава 5. Эффективность использования полимерных материалов для повышения послеремонтной долговечности трибомеханической системы «кольцо подшипника – корпус»
5.1 Технология восстановления трибомеханической
системы «кольцо подшипника – корпус»
5.2 Расчет технологической себестоимости восстановления
трибомеханической системы «кольцо подшипника – корпус»
Заключение
Список литературы
Приложение А. Акты внедрения
Приложение Б. Патенты
Во введении обоснована актуальность и степень разработанности темы исследования, сформулированы цель и задачи исследования, объект, предмет исследования, научная гипотеза, научная новизна результатов исследования, теоретическая и практическая значимость работы, ос- новные положения, выносимые на защиту.
В первой главе «Технологические способы обеспечения послеремонтного ресурса трибо- механичской системы «кольцо подшипника – корпус» транспортно – технологических машин» проведен сравнительный анализ доремонтной и послеремонтной долговечности коробок передач транспортно -технологических машин. На его основании установлено, что относительно низкий ресурс элементов, и в целом КП, в послеремонтный период обусловлен влиянием отказа трибоме- ханической системы «кольцо подшипника – корпус».
Изнашивание поверхности посадочных отверстий под подшипники качения корпусных де- талях КП происходит в результате сложного комплекса воздействий в трибомеханической системе «кольцо подшипника – корпус», и этим объясняется тот факт, что, имеющиеся в литературе сведе- ния по этому вопросу неполны и часто противоречивы.
Основную долю в износе системы «кольцо подшипника – корпус» вносит износ посадоч- ного отверстия под подшипник в корпусной детали КП. Поэтому, в практике ремонтного произ- водства, восстановление трибомеханической системы «кольцо подшипника – корпус» сводится только к восстановлению первоначального размера отверстия под подшипник качения.
Для обеспечения послеремонтной долговечности «кольцо подшипника – корпус» общепри- нятым является способ номинальных размеров.
Изучению вопросов восстановления и повышения долговечности деталей сельскохозяй- ственной техники посвящены работы Александрова Ю.Д., Аскинази Б.М., Багмутова В.П., Бражюнаса А.И., Веселовского А.А., Гурьева А.В., Зуева A.A., Ильина В.К., Кошева Н.В., Лаба- рова Д.Б., Озорнина С.П., Ожегова Н.М., Пономаренко В.П., Рыжова Э.В., Сафронова Р.И., Сереб- ровского В.В., Серебровского В.И., Сковородина В.Я., Суслова А.Г., Тишкина Л.В., Федоровой Л.В., Элькина С. Ю., Юдина В.М. и других отечественных ученых.
Восстановление первоначальных размеров изношенных отверстий под подшипники в кор- пусных деталях КП осуществляется несколькими распространенными способами: тепловой обра- боткой, постановкой дополнительной ремонтной детали, гальваническим и электроискровым нара- щиваниями. Большинство способов связано с термическим воздействием на восстанавливаемые детали, что приводит к релаксации остаточных напряжений и изменению геометрических разме- ров, снижению усталостной прочности.
Поэтому существует необходимость в разработке способа повышения долговечности три- бомеханической системы «кольцо подшипника – корпус» в целом, а не только одного посадочного
места. В настоящее время в ремонтном производстве для восстановления работоспособного состо- яния трибомеханической системы «кольцо подшипника – корпус» используются полифункцио- нальные соединения акрилового ряда (polyfunctional compounds acrylic series (PCAS)), к числу ко- торых относятся анаэробные полимерные материалы. Вопросы исследования и применения поли- мерных материалов для обеспечения послеремонтной долговечности трбомеханической системы «кольцо подшипника – корпус» рассмотрены в работах Бочарова А. В., Бутина А. В., Гаджиева А. А., Дѐмина В. Е., Кондрашина С. И., Котина А. В., Курчаткина В. В., Ли Р. И., Машина Д. В., Мельниченко И. М., Сафонова В. В., Шубина А. Г..
Распространение способа обеспечения послеремонтной долговечности трибомеханической системы «кольцо подшипника – корпус» коробок передач транспортных и технологических машин АПК полимерными материалами сдерживается ввиду недостаточной несущей способности полу- чаемых покрытий, а следовательно, и долговечности восстановленных трибосистем.
Во второй главе – Теоретические предпосылки повышения долговечности трибомеханиче- ской системы «кольцо подшипника – корпус» рассмотрены процессы:
– генезиса контактных явлений, происходящих в поверхностных и подповерхностных слоях деталей;
– эволюции, разрушения, формирования рельефа и геометрической структуры повреждений
(ГСП) поверхностных и подповерхностных слоёв деталей;
– образования вторичных разупрочненных сред, а также частиц износа на поверхностных и
подповерхностных слоях деталей и их влияния на долговечность элементов;
– детерминирования ведущего вида изнашивания элементов;
– обеспечения послеремонтного ресурса применением полифункциональных соединений
акрилового ряда.
Функциональная причинно-следственная связь между частными процессами, проходящими
в трибомеханической системе «кольцо подшипника – корпус», показана в виде структурной схемы
(Рисунок 1).
Изнашивание элементов воз- можно вследствие протекания следую- щих последовательных и параллельных процессов:
1. разрушения микронеровностей на поверхностях деталей трибомехани- ческой системы «кольцо подшипника – корпус»;
2. структурирования контактных поверхностей элементов трибомехани- ческой системы «кольцо подшипника – корпус»;
3. активации сегрегационных процессов в материале отверстия под подшипник качения в корпусе КП,
4. диспергирования и разделения ультратонких метастабильных твёрдых растворов вторичных сред (от процесса
Рисунок 1 – Структурная схема взаимосвязи между частными процессами
в трибомеханической системе «кольцо подшип- ника – корпус»
сегрегатирования) поверхностного слоя материала посадочного места и удаления их из зоны кон- такта деталей;
5. абразивного изнашивания деталей трибосистемы.
Износ шероховатостей поверхности посадочного отверстия при упруго-пластическом кон- такте деталей определяется зависимостью:
Θ∙ (1− ) − = � �1+ ∙∆ ∙� � ∙ ,
h ′ 2 Θ , (1) 0
где ∆ – безразмерный коэффициент характеризующий шероховатость поверхности, – наибольшая высота неровностей профиля, мм;
– радиус единичной микронеровности, мм;
– параметр кривой опорной поверхности;
– параметр степенной аппроксимации кривой опорной поверхности; Θ – упругая постоянная Кирхгофа;
– номинальное контактное давление, мПа;
0 – предел текучести материала корпуса, мПа;
– параметр фрикционной усталости материалов; – коэффициент упрочнения молекулярной связи; , – коэффициент контурной площади контакта,
Из зависимости (1) следует, что на износ шероховатостей поверхности посадочного отвер- стия оказывает влияние начальная микрогеометрия и физико-механические свойства поверхности отверстия под подшипник качения в корпусной детали. Нагрузочный режим подшипника качения будет способствовать тому, что износ шероховатостей поверхности отверстия под подшипник в корпусной детали, будет увеличиваться, поскольку с течением времени произойдёт снижение ко- эффициента контурной площади и локализация контактного давления на поверхности посадочного места в корпусной детали КП.
Микроскопические изменения связаны с изменением структуры и субструктуры материала
детали и приводят к экстремальному и катастрофическому разрушению значительной части опор- ной поверхности контактирующих деталей.
Внешняя нагрузка приводит к деформации кристаллической решётки материала корпуса вблизи поверхности. Деформация решётки под действием переменной нагрузки является перво- причиной зарождения и развития усталостных поверхностных трещин (дислокация) поверхност- ного слоя материала корпуса. При значительных контактных нагрузках в приповерхностном слое происходит зарождение и перемещение дислокаций. Скопление дислокаций у препятствия, в ко- нечном итоге, вызывает образование коалесценции поверхностных трещин.
В условиях фрикционного контакта в подповерхностных слоях интенсифицируются про- цессы, связанные с миграцией атомов (ионов), что создаёт условия для образования пористости и макроскопических дефектов (поверхностных трещин).
Мера интенсивности деградации поверхностных слоёв материалов деталей, уровень напря- жений на поверхности контакта, эволюция сегрегационных процессов может быть выражена ко- эффициентом проскальзывания внешней поверхности наружного кольца подшипника в местах его изгиба в зоне контакта отверстия под подшип ник качения в корпусной детали КП и кольца под- шипника.
Коэффициент проскальзывания определяется зависимостью:
где – величина изгиба наружного кольца подшипника при > 0, мм;
= (2)
0 – величина изгиба наружного кольца подшипника при = 0, мм;
– внешняя нагрузка на подшипник качения, Н.
Таким образом, для обеспечения ресурса трибомеханической системы «кольцо подшипника
– корпус» необходимо выполнение условия, при котором → .
Обобщенная схема изнашивания элементов трибомеханической системы «кольцо подшип- ника – корпус» коробок передач транспотно-технологических машин приведена на Рисунке 2.
Рисунок 2 – Обобщённая структурная схема механизма изнашивания трибомеханической системы «кольцо подшипника – корпус»
Для обеспечения послеремонтного ресурса трибомеханической системы «кольцо подшип- ника – корпус» необходима разработка расчетной модели, учитывающей деформационно-проч- ностные свойства контакта кольца подшипника и корпуса с учетом величины перемещения наруж- ного кольца подшипника.
При рассмотрении контактного взаимодействия наружного кольца шарикового радиального подшипника с поверхностью посадочного отверстия в корпусе КП приняты следующие допуще- ния:
1. справедлива гипотеза Винклера о пропорциональности между осадкой в каком-либо се-
чении и отпором основания в том же сечении;
2. поперечное сечение симметрично относительно его центральной оси, перпендикулярной
к опорной поверхности, что обусловливает прямой изгиб бруса;
3. отсутствует перекос колец и вала в подшипнике качения.
С учётом этих допущений задача определения перемещения наружного кольца подшипника
зится, как:
+ 2 . ( + k0 2) ∙ ( 2 + 2)32
2
2 + 2 =− , (3)
сводится к решению дифференциального уравнения изгиба круговых брусьев малой кривизны:
где – радиальный изгиб бруса, который считается положительным, если он направлен к центру кривизны, м;
– изгибающий момент в брус, который считается положительным, если он со- здаёт сжимающие напряжения во внешних волокнах бруса, Н ∙ м;
– момент инерции поперечного сечения бруса относительно главной центральной оси параллельной его опорной поверхности, Н ∙ м2;
– радиус кривизны бруса (расстояние от центра тяжести поперечного сечения до центра кривизны бруса), м;
– модуль упругости материала наружного кольца подшипника, мПа; 2
2 – вторая производная от изгиба по длине дуги бруса.
Общее решение уравнения изгиба наружного кольца подшипника от единичной силы выра-
( −2 ) − = + = � ∙sin� ( + −2 )�+
sin� ( − )��
Общее решение (4) включает выражение затухающей гармоники, что характеризуется убы- ванием с ростом , вызванным изменением − .
Очевидным является, что изгиб наружного кольца подшипника будет максимальным
(4)
на величине угла начальной фазы tan� ( )�.
В шариковом радиальном подшипнике качения радиальная нагрузка воспринимается те-
лами качения в зоне, ограниченной углом не более 1800. Тогда к наружному кольцу подшипника в точках контакта приложена система сосредоточенных сил P , P , P , P , от тел качения.
В этом случае, формула (4) по определению изгиба наружного кольца подшипника, на ос- новании теоремы о независимости действующих внешних сил в упругих системах может быть
представлена в виде:
n
Pr
u=u +u =� j �ea�φ−2π�
1 2 j=1 �k0EJ(a2 + b2) j
∙ sin �b�φj + βj − 2π�� + e−aφ sin �b�βj − φj���
012j
2∑n Pr EFab + j=1 �k0EJ(a2 + b2) .
(5)
π(EF + k0r2) ∙ (a2 + b2)32
Пример решения уравнения (5) приведена на Рисунке 3.
где
h – толщина полимерного материала, мм; 0 – коэффициент Пуассона.
Рисунок 3 – Зависимость изгиба наружного кольца подшипника от угла контакта
фициент пропорциональности (коэффициент жёсткости упругого основания), с учетом из- гиба наружного кольца подшипника опреде- ляется, как (Рисунок 4):
0 – модуль упругости полимерного материала, мПа;
Найденные перемещения наружного
кольца подшипника позволяют выбрать соот- ношение прочностных характеристик поли- мерного материала (в частности коэффициент жесткости упругого основания), используе- мого для повышения долговечности трибоме- ханической системы «кольцо подшипника – корпус».
k =2 [h∙(1− )] , (6) 00 02−1
Тогда, необходимая величина k коэф- 0
Рисунок 4 – Зависимость коэффициент жёсткости упругого основания
от толщины полимерной пленки
Из выражения (6) следует, что коэффи- циент пропорциональнос0ти зависит от модуля упругости и толщины полимерной плёнки. Варьируя значениями и h можно обеспе- чить штатную величину изгиба кольца под- шипника, что позволит создать условия для увеличения ресурса трибомеханической си- стемы «кольцо подшипника – корпус».
При определении несущей способно- сти полимерного слоя решалась задача его плоского деформирования, при этом было принято, что смещения вдоль оси восстанов- ленного отверстия отсутствуют, что матери- алы наружного кольца подшипника и корпус- ной детали являются упругими и сжимае-
мыми, базисная деталь представляет собой абсолютно жесткую конструкцию. Процесс деформи- рования полимерной композиции за все время нагружения носит квазистатический характер. Мо- делирование несущей способности полимерной пленки производилось методом конечных элемен- тов (МКЭ) в среде ANSYS.
Рисунок 5 – Интенсивность напряжений в Рисунок 6 – Распределение напряжений по слое полимера, (в мПа) контактной поверхности (в мПа)
При проведении расчетных исследований напряженного состояния с помощью МКЭ (плос-
кая контактная задача теории упругости) использовали пакет прикладных программ ANSYS. Под- шипник и корпус считали выполненными из стали. Упругие свойства материала модели: модуль упругости Е=3 ГПа, коэффициент Пуассона =0,38. Средний размер конечных элементов был 0,1 мм. В связи с тем, что распределение нагрузки симметрично относительно линии действия силы при исследовании рассмотрена половина соединения. Картина изолиний интенсивности напряже- ний в слое полимера приведена на Рисунке 5. Распределение напряжений по контактной поверх- ности приведено на Рисунке 6. Отмечено удовлетворительное совпадение расчетных и экспери- ментальных значений напряжений, что свидетельствует о достаточной частоте разбивки сетки ко- нечных элементов и достоверности результатов расчета.
В дальнейших расчётах напряжённого состояния прослоек были использованы реальные их размеры (переменной толщины 0-200 мкм). Графическое представление результатов расчёта напряжённого состояния в таких тонких прослойках затруднено, поэтому далее приведены лишь графики изменения напряжений по длине дуги контакта (Рисунок 5,6).
Таким образом, максимальные напряжения имеют место на оси симметрии, дуга контакта при этом составляет 180 градусов.
Теоретические исследования показали:
1. Разрушение и деградация поверхностных слоёв посадочного отверстия связано с сегрега- цией углерода в поверхностные слои материала корпуса от действия изгиба кольца подшипника качения;
2. Зависимость для определения изгиба наружного кольца шарикового радиального под- шипника качения, может быть определена по теории изгиба бруса малого радиуса кривизны на упругом основании модели Винклера;
3. Соотношением модуля упругости и толщины полимерного материала, можно обеспечи- вается штатное функционирование трибомеханической системы «наружное кольцо подшипника – корпус».
4. Для обеспечения долговечности восстановленной трибомеханической системы «кольцо подшипника – корпус» плёнка полимерного материала должна находиться в состоянии гидроста- тического сжатия.
В третьей главе – «Методика экспериментальных исследований» приведена общая и част- ные методики экспериментальной части исследования.
Программа включала исследования:
пус»; 1. технического состояния деталей трибомеханической системы «кольцо подшипника – кор-
2. физико-механических свойств полимерного материала;
3. эксплуатационные испытания восстановленных трибомеханических систем «кольцо под- шипника – корпус» коробок передач транспортно-технологических машин.
Величина и характер износа посадочных мест под подшипники качения были получены пу- тём микрометражных исследований изношенных посадочных мест под подшипники коробок пе- редач зерноуборочного комбайна John Deer, и автомобиля КамАЗ в соответствии с требованиями ГОСТ 17510.
Измерение величины износа отверстий под подшипник качения в картере КП производи- лась в соответствии с требованиями ГОСТ 8.050 и ГОСТ 8.051 специализированным мерительным инструментом.
Для оценки изменения топографии и микрорельефа поверхности трения использовался ав- томатизированный прибор для бесконтактного измерения несплошности (топологии) поверхно- стей, созданный на базе микроскопа МИС – 11 (Рисунок 7).
Количественная информация о высотах микрорельефа получена с помощью фотограммет- рической обработки стереоизображений:
̇ + ̈ ̇ ̇ − ̈
= 2 cos (7); = 2 (8); = 2 sin (9);
где ̇ , ̈, ̇ – плоские координаты; – увеличение микроскопа; – угол съемки.
1 – персональный компьютер; 2 – мик- роскоп МИС – 11; 3 – исследуемая по- верхность; 4 – лазерный диод; 5 – кон- денсатор; 6 – фильтр; 7 – линзы освети- тельного тубуса; 8 – линзы измеритель- ного тубуса; 9 – CCD матрица
Рисунок 7 – Принципиальная (логиче- ская) схема стереографического комплекса
12Трёхмерная реконструкция микрорельефа по- верхности образца проводится с помощью специально разработанного пакета прикладных программ. Визуа- лизация и интерпретация результатов измерения и оценки дефектов (несплошностей) поверхности реали- зована с использованием графического интерфейса среды MATLAB.
Исследование модуля упругости полимерного материала проводили на многослойных клеёных об- разцах, изготовленных из чугуна СЧ 18 – 36 и стали ШХ 15, в условиях нормальной и повышенной (до 150 °С) температур.
Склеенный образец подвергали растяжению на разрывной машине ИР – 500 по стандартной методике. Реологические свойства полимерных компози- ций определяли на при различных значениях темпера- тур и времени нагружения (Рисунок 8). Нагрузка на об- разцы составляла 300, 500, 700 Н. Температура варьи- ровалась в интервале 50 – 120 0С, что соответствует ре- альной температуре подшипника качения при эксплу- атации. Время исследования ползучести составляла 8
ч.
Исследование деформационно-прочностных
свойств плёнок полимерного материала заключалось в определении предела прочности клеевого соединения при сдвиге образцов в виде двух пластин размером 2Х20Х60 мм с одинарной нахлёсткой длиной 15 мм.
Предел прочности п ри сдвиге образцов опреде-
лялся по формуле:
Нагружение подшипника осуществлялось што- ком пресса РГ – 4 через установочную призму 5. В цен- тровое отверстие, которой был установлен шарик из закаленной стали ШХ – 15, что обеспечивало центри- рование (относительно оси симметрии) нагружение всей конструкции. Нагрузка на подшипник выбира- лась исходя из 90% ресурса подшипника и составляла 3000, 5000 и 7000 Н (Рисунок 10).
Оценка напряженно – деформированного состояния полимерной пленки, в восстановленной трибомехани- ческой системе проводилась поляризационно – опти- ческим методом (Рисунок 11). Для наблюдения картин полос использовали круговой полярископ Zeiss-300, регистрация картин проведена с помощью цифровой камеры.
1 – нагружающее устройство;
2 – термокамера;
3 – терморегулятор Рисунок 8 – Общий вид эксперимен- тальной установки по определению реологических свойств полимерной композиции
Рисунок 9 – Общий вид образцов для определения предела прочности при сдвиге
где разрушающая нагрузка, Н;
– площадь склеивания, мм .
= (10)
13
1 – корпус; 2 – подшипник качения, 3 – рычажный пресс; 4 – динамометр; 5 – установочная призма. Рисунок 10 – Общий вид экспериментальной установки
Рисунок 11 – Модели для исследования напряженно-деформированного состояния
Эксплуатационные испытания восстановленных трибомеханических систем «кольцо под- шипника – корпус» проводили на первичном, промежуточном валах коробок передач. Выбор ко- личества объектов испытаний и обработку результатов проводили методами математической ста- тистики по ГОСТ 17510.
В четвертой главе – «Результаты экспериментальных исследований и их анализ» – приве- дены основные результаты исследования.
Зависимости распределения износа посадочных мест под подшипники первичного и проме- жуточного валов, построенные по результатам микрометражных исследований, приведены на Ри- сунке 12.
Как видно из Рисунка 12 распределения хорошо согласуются с теоретическим законом Вей- булла.
а)
б)
в)
а – отверстия под подшипники качения первичного вала КП автомобиля КамАЗ
б – отверстия под подшипники качения вторичного вала КП автомобиля КамАЗ в – отверстия под подшипники качения первичного вала КП комбайна John Deer г – отверстия под подшипники качения вторичного вала КП комбайна John Deer
Рисунок 12 – Распределение износов посадочных отверстий под подшипники в корпусах коробок передач
Проверка адекватности эмпирического распределения к конкретно найденному теоретиче- ски производилась по критерию Пирсона – квадрат.
Результаты расчета, проверенные по таблицам квантилей распределения – квадрат пока- зали, что для всех рассматриваемых случаев распределений износов посадочных мест вероятность случайного расхождения 0,0719 – 0,991 значительно выше стандартного значения 0,05. При этом статистические характеристики износа посадочных мест под подшипники первичного и промежу- точного валов колеблются в узких пределах. Среднее арифметическое значение износа равно 0,136 – 0,192 мм. При этом наибольший износ имеет отверстие под задний подшипник первичного вала, среднее квадратическое отклонение 0,07 – 0,125 мм.
Величина износа отверстий превышает величину допускаемых износов. Это доказывает необходимость восстановления посадочных отверстий.
На Рисунке 13, а, для сравнения, показана трехмерная интерпретация исходной поверхности посадочного места под подшипник качения в КП.
г)
а)
б)
в)
а – исходная поверхность посадочного места (средняя высота микронеровностей 0,32 мкм);
б – изношенная поверхность посадочного места (средняя высота микронеровностей 0,87 мкм);
в – поверхности посадочного места под подшипник качения в КП восстановленного анаэробным по- лимерным материалом Loctite 620 (средняя высота микронеровностей 0,42 мкм)
Рисунок 13 – Топология поверхностей посадочного места под подшипник качения в КП
Обработка результатов профилографических исследований показала, что посадочное отвер- стие имеет следы проскальзывания и характерные особенности повреждений в виде глубоких вы- рывов с оттеснением металла.
Представлена топология геометрической структуры повреждений поверхности посадоч-
ного отверстия в КП. Как видно, из сравнения (Рисунок 13), топология геометрической структуры повреждений изношенного отверстия претерпевает значительные изменения. Видно, что шерохо- ватость поверхности локальной зоны износа, соответствует 0,68 – 0,87 мкм. Это значение шерохо- ватости превышает шероховатость исходной поверхности в 2,1…2,7 раза (в натуральном выраже- нии на 0,35 – 0,50 мкм).
При наличии плёнки полимера существенной деградации поверхности отверстия под под- шипник качения в корпусе КП не происходит. На поверхности образца имеются некоторые следы износа без вырывов металла, что может свидетельствовать о надёжной защите полимерной плён- кой поверхности посадочного отверстия (значение величины шероховатости превышает величину исходной поверхности в 1,3 раза, в натуральном выражении на 10 мкм).
Сравнение содержания графита показывает увеличение содержания и коалесцирования сво- бодного графита в поверхностных слоях изношенных деталей по сравнению с новыми (Рисунок 14). Это также подтверждает теоретическую гипотезу о причинах разрушения посадочных отвер- стий в КП.
аб
а – новые (17 % С);
в
б – изношенные (26 – 32 % С);
в – с полимерной пленкой (19 % С)
Рисунок 14 – Содержание графита в поверхностных слоях посадочного места под подшипники качения в корпусе КП
Восстановление трибомеханической системы «кольцо подшипника – корпус» анаэробным герметиком предотвращает разрушение посадочных отверстий. При этом сокращается площадь поверхности занятой свободным графитом.
При эксплуатации, восстановленной трибомеханической системы разрушающие напряже- ния плёнок будут тем выше, чем меньше их толщина и соответственно велика вероятность долго- временной эксплуатации.
График зависимости предела прочности полимерной плёнки от её толщины приведён на Рисунке 15.
Согласно расчётам, проведённым в гл. 2 величина предела прочности, необходимая для обеспечения прочности восстановленной трибомеханической системы «кольцо подшипника – кор- пус» составляет 4 – 9 мПа.
Рисунок 15 – Зависимость предела прочности полимерной плёнки от ее толщины
Рисунок 16 – Зависимость предела прочно- сти герметика Loctite 620 от температуры и вре- мени полимеризации
Анализ экспериментальных исследо- ваний показывают, что температура полиме- ризации анаэробного герметика (Loctite 620) должна находится в пределах 333 – 3530 К при этом отверждение пленок полимерного материала происходит в течение 45 – 60 мин (Рисунок 16).
Экспериментальные исследования показывают, что рациональная толщина пленок, с учетом напряженного – деформи- рованного состояния, должна быть в диапа- зоне от 0,1 до 0,2 мм.
На Рисунках 17, 18 номерами обозна- чен порядок изолиний разности главных напряжений.
Качественный анализ картины траек- торий главных напряжений показывает, что расположение главных площадок напряже- ний наблюдается по радиусу и окружности модели клеевого шва. Область максималь-
В результате исследования предела прочности пленок полимерного материала, (многофакторный эксперимент) получено уравнение регрессии в кодовых единицах, описывающее температурно-временную за- висимость предела прочности, герметика Loctite 620:
ных напряжений расположена на оси симметрии и на некоторой глубине модели клеевого шва. Граница зоны контакта клеевого шва в случае его равномерного распределения составляет около 700, а в случае клеевого шва с эксцентриситетом – 3600.
= 210 + 7,8 1 + 5,8 2 − 3,1 12 − 0,8 2 − 2−1,3 1 2 (11)
где – время отверждения, мин.;
– температура отверждения, 0К.
100 Н а)
200 Н 300 Н б) в)
Рисунок 17 – Напряженное состояние модели с равномерным распределение клеевого шва
100 Н 200 Н 300 Н а) б) в) Рисунок 18 – Напряженное состояние модели с эксцентриситетным
распределением клеевого шва
Форма клеевого шва оказывает существенное влияние на напряженное состояние модели.
В случае равномерного распределения клеевого шва изолинии главных напряжений локализуются в узкой зоне на оси симметрии модели во всем диапазоне нагрузок на подшипник. Передача нагрузки через меньшую зону контакта приводит к изменению напряженного состояния клеевого слоя, в части снижения его несущей способности. Из картины полос на Рисунке 18, а, б, в, следует, что на свободном от нагрузки контуре действуют растягивающие напряжения. Максимальная ве- личина касательных напряжений наблюдается на дуге контакта в пределах 380 от оси симметрии для модели с равномерным распределение клеевого шва и составляет при внешней нагрузке на подшипник 300 Н. На нагруженном контуре клеевого шва действуют сжимающие напряжения, о чем свидетельствует сгущение полос изолиний (Рисунок 17, 18). Картины напряжений на Рисунке 18 свидетельствуют о существенном изменении условий контакта и перераспределении главных напряжений в клеевом шве эксцентриситетной формы, последствием которого может быть увели- чение несущей способности клеевого шва. Линии напряжений имеют симметричный характер. При наличии эксцентриситетной формы клеевого шва наблюдается прогрессивная форма зоны контактного взаимодействия тел, когда границы зоны контакта увеличиваются с ростом внешней нагрузки на подшипник. Таким образом, увеличение зоны контакта снижает уровень нормальных напряжений и увеличивает несущую способность эксцентриситетной формы клеевого шва.
Полученные экспериментальные данные о качественном распределении главных напряже- ний в клеевом шве имеют практическое применение для разработки математической модели несу- щей способности клеевого шва с учетом его распределения по поверхностям деталей трибоси- стемы и назначении минимального уровня эксплуатационных свойств полимерного материала, ис- пользуемого для восстановления номинально-неподвижных соединений подшипников качения.
Выявлено, что с увеличением зазора в посадке происходит локализация угла фактической зоны контакта кольца и корпуса, с уменьшением её до 60 – 70 градусов (против номинальной при зазоре 0 мм равной 180 градусов) (Рисунок 19).
Малый угол фактической зоны контакта является причиной снижения жёсткости трибоме- ханической системы «кольцо подшипника – корпус» вследствие появления изгибной деформации кольца. Поскольку большая часть внешней радиальной нагрузки воспринимается ограниченным числом тел качения подшипника, увеличивается вероятность преждевременного выхода его из строя по усталостным повреждениям рабочих элементов подшипника.
а)
б)
Рисунок 19 – Результаты измерения изгиба наружного
кольца подшипника в зависимости от угла контакта
Рисунок 20 – Зависимость изгиба наружного кольца подшипника от толщины пленки полимерного материала
В сопряжении с упругой прокладкой из полимерного материала наблюдается значительное снижение изгиба кольца подшипника (Рисунок 20). Причём с увеличением толщины полимерной прокладки обеспечивается практически равномерное распределение деформации по периметру наружного кольца подшипника. Угол фактической зоны контакта приближается к 200 – 270 граду-
сам. Сравнительный анализ зависимостей на Рисунке 20 показал, что увеличение толщины поли- мерного покрытия приводит к увеличению изгиба наружного кольца подшипника и может повлечь разрушение плёнки полимера. При увеличении плёнки до 0,2 мм происходит увеличение изгиба наружного кольца подшипника до 86 мкм, что может неблагоприятно отразится на долговечности полимерной плёнки.
На Рисунке 21 представлены результаты ресурсных испытаний трибомеханических систем «кольцо подшипника – корпус» первичного и вторичного валов КП автомобиля КамАЗ и зерно- уборочного комбайна John Deer.
а) б)
в) а, в–доремонтная наработка; г)
б, г – послеремонтная наработка
Рисунок 21 – Графики функции плотности распределения доремонтной и послеремонтной наработки триботмеханических систем «кольцо подшипника – корпус» КП автомобиля КамАЗ (а, б) и зерноуборочного комбайна John Deer (в, г)
Анализ зависимостей показывает, что после восстановления полимерным материалом ре- сурс увеличивается с 84 тыс. км до 103 тыс. км у первичного вала и с 115 до 127 тыс. км у вторич- ного вала КП автомобиля КамАЗ, увеличение ресурса КП зерноуборочного комбайна составляет с 1500 до 2100 га у первичного и с 2100 до 3000 гектаров у вторичного валов.
Технология применения полифункционального соединения акрилового ряда для обеспече- ния послеремонтного ресурса трибомеханической системы «кольцо подшипника-корпус» коробки передач транспортно-технологических машин, включает следующие операции: разборку КП, мойку корпусной детали КП, обезжиривание посадочных мест под подшипники качения в картере КП, нанесение полимерного материала на поверхности деталей, сборку коробки передач и термо- обработку полимерного материала. Предложенная технология позволяет на 25 – 40 % увеличить ресурс рабочих поверхностей системы.
В пятой главе «Эффективность использования полимерных материалов для повышения по- слеремонтной долговечности трибомеханической системы «кольцо подшипника – корпус»» – про- ведены результаты экономической эффективности применения полимерных материалов и техни- ческая целесообразность внедрения способа обеспечения послеремонтной долговечности, при этом удельная стоимость ед. наработки снижается с 0,23 руб./км до 0,06 руб./км. Расчетный годо- вой экономический эффект от внедрения разработанного технологического процесса составил 9894 руб. на одну КП.
III. ЗАКЛЮЧЕНИЕ
1. Установлено, что разрушение и деградация поверхностных слоёв посадочного отверстия связано с контактными нагрузками и сегрегацией углерода в поверхностные слои материала кор- пуса от действия изгиба кольца подшипника качения; зависимость для определения параметров изгиба наружного кольца шарикового радиального подшипника качения, определяется по теории изгиба бруса малого радиуса кривизны на упругом основании модели Винклера; для обеспечения долговечности восстановленной трибомеханической системы «кольцо подшипника – корпус» плёнка полимерного материала должна находиться в состоянии гидростатического сжатия.
2. Определено, что вне зависимости от толщины модели, имитирующей пленку, из анаэроб- ного герметика в восстановленной трибомеханической системе «кольцо подшипника – корпус», главные площадки напряжений располагаются по радиусу и по окружности. При этом напряжения составляют от 4 до 9 мПа и располагаются на оси симметрии модели, дуга контакта составляет 180 градусов.
3.Установлено, что среднее арифметическое значение износа отверстий под подшипники качения в корпусных деталях КП транспортных и технологических машин составляет 0,136 – 0,192 мм. При этом наибольший износ имеют отверстия под задний подшипник КП первичного вала, среднее квадратическое отклонение 0,07 – 0,125 мм, что превышает величину допускаемого износа
по техническим требованиям на ремонт, при этом шероховатость поверхности локальной зоны из- носа соответствует 0,68 – 0,87 мкм. Это значение шероховатости превышает шероховатость исход- ной поверхности на 0,35 – 0,50 мкм. При наличии пленки полимера существенной деградации по-
садочного места не наблюдается.
4 Экспериментально установлено, что рациональная толщина пленок, с учетом напряжен-
ного – деформированного состояния трибомеханической системы «кольцо подшипника -корпус», должна быть в диапазоне от 0,1 до 0,2 мм.
5. Установлено, что эффективная температура эксплуатации плёнок полимера составляет от 80 до 1000 C, что удовлетворяет режимам эксплуатации коробок передач транспортных и техноло- гических машин. При этом ползучесть пленок зависит от температуры и толщины. Плёнки поли- мерного материала толщиной до 0,1 мм обладают ползучесть в 4% (в сравнении с толщинами пле- нок до 0,3 мм – их ползучесть составляет около 10%), это обеспечивает стабильное взаимное рас- положение деталей в диапазоне рабочих температур и нагрузок.
6. Разработана технология применения полифункционального соединения акрилового ряда для обеспечения послеремонтного ресурса трибомеханической системы «кольцо подшипника-кор- пус» коробки передач транспортно-технологических машин, включающая следующие операции: разборку КП, мойку корпусной детали КП, обезжиривание посадочных мест под подшипники ка- чения в картере КП, нанесение полимерного материала на поверхности деталей, сборку коробки передач и термообработку полимерного материала.
7. В результате испытаний определен доремонтный ресурс в КП грузовых автомобилей. При восстановлении полимерным материалом ресурс увличиваеся с 84 тыс. км до 103 тыс. км у пер- вичного вала и с 115 до 127 тыс. км у вторичного вала. Послеремонтная наработка КП зерноубо- рочного комбайна увеличивается для первичного вала с 1500 до 2100 га и вторичного валов с 2100 до 3000 гектаров. При этом расчетный годовой экономический эффект от внедрения разработан- ного технологического процесса составил 9894 руб. на одну КП.
Рекомендации производству
Результаты выполненных исследований рекомендуется использовать предприятиям, экс- плуатирующим, обслуживающим транспортно-технологические машины, при разработке меро- приятий обеспечения послеремонтного ресурса машин, научно – исследовательским институтам, занимающимся вопросами надежности сельскохозяйственной техники, учебным заведениям, осу- ществляющим подготовку и повышение квалификации технических специалистов для АПК.
Перспективы дальнейшей разработки темы
Дальнейшие научные исследования должны быть направленны на повышение эффективно- сти технологии обеспечения послеремонтного ресурса трибомеханической системы «кольцо под- шипника – корпус» на основе разработки оптимизационной математической модели, учитываю- щей прочностные, реологические свойства полимерного материала.
Актуальность темы исследования. Показатели долговечности машины зависят от долго- вечности ее составных элементов. Значительная доля затрат и простоев в ремонте приходится на агрегаты трансмиссии и, особенно, на коробку передач (КП). На коробку передач автомобилей, в условиях рядовой эксплуатации, приходится до 76 % всех отказов трансмиссии, и около 50 % от- казов КП для зерноуборочных комбайнов. Одной из основных причин отказов КП (около 70 %) являются отказы трибомеханической системы «кольцо подшипника – корпус», ресурс которых ниже расчетного и находится в пределах от 2000 до 3800 мото-ч, а для автомобилей не превышает 150 тыс. км.
Отказ трибомеханической системы «кольцо подшипника – корпус», как правило, является следствием износа посадочного места под наружное кольцо в корпусе КП при ее эксплуатации. Износ отверстий под подшипники в корпусе КП происходит в результате проворачивания наруж- ных колец. При этом происходит чисто механический износ отверстия под подшипник качения в корпусе КП. Основную долю в износе системы «кольцо подшипника – корпус» вносит износ по- садочного отверстия под подшипник в корпусной детали КП.
Одним из способов восстановления послеремонтного ресурса трибомеханической системы «кольцо подшипника – корпус» коробок передач является использование полимерных материалов. При обеспечении послеремонтного ресурса трибомеханичской системы «кольцо подшип- ника – корпус» полимерными материалами, полимерная пленка выполняет роль демпфирующего слоя, что способствует равномерному распределению контактной нагрузки на поверхности кон-
такта кольца подшипника и посадочного места.
Таким образом, разработка и совершенствование технологических процессов, обеспечива-
ющих повышение долговечности трибомеханической системы «кольцо подшипника – корпус» ко- робок передач, является актуальной и представляет собой значимую научно-практическую задачу. Исследование выполнялось в соответствии с темой НИР СибИМЭ СФНЦА РАН No 0778- 2019-0023 «Разработать методику формирования адаптируемой системы обеспечения работоспо- собности мобильных энергетических средств для условий АПК Сибири», выполненной в рамках
Государственного задания.
Степень разработанности темы исследования. Исследованиями установлено, что отно-
сительно низкий ресурс элементов, и в целом коробки передач (КП), в послеремонтный период обусловлен влиянием износа поверхностей отверстий под подшипники качения в корпусных дета- лях КП. Вопросы исследования долговечности трибомеханической системы «кольцо подшипника – корпус» рассмотрены в работах Бейзельмана Р. Д., Гюнтера Д., Курчаткина В.В., Ли Р.М., Ней- берта Г., Переля Л. Я., Перетта Г., Саверского А. С., Сцешко И., Ульмана И.Е., Цыпкина Б.В., Шрейбера Г. и других отечественных и зарубежных ученых.
В настоящее время в ремонтном производстве для обеспечения послеремонтного ресурса трибомеханической системы «кольцо подшипника – корпус» используются полифункциональные соединения акрилового ряда (polyfunctional compounds acrylic series (PCAS)), к числу которых от- носятся анаэробные полимерные материалы.
Однако реализация этой возможности сдерживается малой изученностью проблемы рабо- тоспособного состояния восстановленных трибомеханических систем «кольцо подшипника – кор- пус» коробок передач в различных режимах нагружения. Не изучено влияние на их усталостную прочность деформационно-прочностных и адгезионных свойств полимера, режимов отверждения, масштабного фактора и т.п.
Цель исследования: обеспечение послеремонтного ресурса трибомехнической системы «кольцо подшипника – корпус» коробок передач (КП) транспортно-технологических машин в АПК с использованием полифункционального соединения акрилового ряда и технология его при- менения.
Задачи исследования:
– установить вид и параметры процесса изнашивания деталей трибомеханической системы «кольцо подшипника – корпус»; – определить напряженно-деформированное состояние пленки полимерного материала в
трибомеханической системе «кольцо подшипника-корпус» коробки передач транспортно-техноло- гических машин;
– определить физико-механические и реологические свойства полимерных пленок из поли- функционального соединения акрилового ряда и разработать технологию применения полифунк- ционального соединения акрилового ряда для обеспечения послеремонтного ресурса трибомеха- нической системе «кольцо подшипника-корпус» коробки передач транспортно-технологических
машин;- провести ресурсные испытания КП с восстановленными трибомеханическими системами «кольцо подшипника-корпус» и оценить экономическую эффективность предложенной техноло-
гии.
Объект исследования: процесс обеспечения послеремонтного ресурса трибомеханической
системы «кольцо подшипника-корпус» коробок передач с применением полифункциональных со- единений акрилового ряда.
Предмет исследования: закономерности процесса обеспечения послеремонтного ресурса трибомеханической системы «кольцо подшипника-корпус» коробок передач с применением поли- функциональных соединений акрилового ряда.
Рабочая гипотеза: обеспечение послеремонтного ресурса трибомеханической системы «подшипник качения – корпус» коробок передач транспортно-технологических машин АПК воз- можно с применением полифункциональных соединений акрилового ряда с учетом их физико-ме- ханических свойств и условий эксплуатации коробок передач.
Научная новизна заключается:
– в совершенствовании методики моделирования напряженно-деформированного состояния методом конечных элементов (МКЭ) однопараметрической трибомеханических систем типа «кольцо подшипника – корпус – физико – механические свойства полимерного материала – усло- вия эксплуатации», позволяющей изучить ее элементы, свойства и процессы, имеющие место, в подшипнике, полимерной пленке, механической системе и во внешней среде;
– в обоснованных квалификационных требованиях к полимерному материалу для компен- сации износа в трибомеханической системе «кольцо подшипника – корпус» КП
– в закономерностях изменения ресурса восстановленной трибомеханической системы «кольцо подшипника – корпус КП» в зависимости: от условий эксплуатации КП, физико-механи- ческих свойств и геометрических размеров пленок полимерного материала.
Теоретическая значимость: результаты, полученные в исследовании, дополняют имею- щиеся, теоретические представления в части определения ресурса однопараметрических систем типа «кольцо подшипника – корпус КП» с целью оптимизации параметров, определяющих после- ремонтный ресурс трибомеханической системы «кольцо подшипника – корпус» КП при их восста- новлении полимерными материалами акрилового ряда.
Практическая значимость: разработана технология обеспечения послеремонтного ре- сурса трибомеханической системы «кольцо подшипника – корпус» КП с применением полифунк- циональных соединений акрилового ряда, отличающаяся низкой трудоёмкостью реализации, по сравнению с другими методами, не требующая специализированного оборудования и высокой ква- лификации исполнителей. Значимость и актуальность диссертационной работы подтверждена внедрением результатов работы в реальном секторе сельскохозяйственного производства и транс- портных услуг.
Методология и методы исследования. Общей методологической основой исследования являлся системный подход, обеспечивающий анализ процесса обеспечения послеремонтного ре- сурса трибомеханической системы «кольцо подшипника – корпус» коробок передач транспортно- технологических машин, применением полифункциональных соединении акрилового ряда, с уче- том их физико-механических свойств и условий эксплуатации коробок передач. В процессе иссле- дования использовались положения теории: надежности, упругости, сопротивления материалов, динамики и прочности машин; методы: численного и статистического моделирования состояния трибомеханической системы «кольцо подшипника – корпус КП» в программных средах MathCad, Statistica, MSC. Patran/Marc, Ansys, Matlab. Экспериментальные исследования базировались на ме- тодах лабораторных и эксплуатационных испытаний КП транспортно-технологических машин. Исследования выполнены с применением стандартных, а также оригинальных методик, специ-
ально разработанного и серийного оборудования.
Положения, выносимые на защиту:
– методика моделирования напряженно-деформированного состояния трибомеханической
системы типа «кольцо подшипника – корпус – физико – механические свойства полимерного ма- териала – условия эксплуатации», позволяющая изучить ее элементы, свойства и процессы, имею- щие место, в подшипнике, полимерной пленке, механической системе;
– результаты: исследования физико – механических свойств пленок полимерного материала, напряженно-деформированного состояние полимерной пленки;
– результаты ресурсных испытаний трибомеханической системы «кольцо подшипника – корпус» КП транспортно-технологических машин.
Степень достоверности результатов исследования. Достоверность полученных резуль- татов исследований, обеспечивается методологией проведения эксперимента, устойчивой воспро- изводимостью результатов, использованием поверенного метрологического оборудования, обос- нованностью физических представлений, корректностью подготовки и проведения эксперимента, согласием с результатами других авторов.
Реализация результатов исследования. Технологический процесс применения полимер- ных материалов для обеспечения послеремонтной долговечности трибомеханической системы «кольцо подшипника – корпус КП» используется в ООО «Татэлектромаш Сибирь», г. Новоси- бирск. Результаты исследования используются учебном процессе ФГБОУ ВО Новосибирский гос- ударственный педагогический университет и ФГБОУ ВО Новосибирский государственный техни- ческий университет.
Апробация результатов исследования. Основные положения и результаты диссертацион- ной работы доложены, обсуждены и экспонировались на:
– научных конференциях профессорско-преподавательского состава, научных работников и аспирантов Челябинского государственного агроинженерного университета и Челябинской госу- дарственной агроинженерной академии в 1998 – 2016 г.г.;
– научных конференциях профессорско-преподавательского состава, научных работников и аспирантов Тюменского государственного нефтегазового университета в 2013 – 2015 г.г..;
– региональной научно – практической конференции студентов и аспирантов «Состояние и инновации технического сервиса машин и оборудования», г. Новосибирск, 2015 – 2017 г.;
– выставке «Достижения науки – агропромышленному комплексу», г. Челябинск, 2015 г.
– международной научно-практической конференции «Современное состояние и перспек- тивы развития агропромышленного комплекса», г. Курган, 2016 – 2017 г.
– международной научно-практической конференции «Чтения Терских», г. Иркутск,2017г.
– международной научно-практической конференции «Научно – техническое обеспечение АПК Сибири», г. Новосибирск, 2019 г.
– международной научно-технической конференции «Цифровые технологии и роботизиро- ванные технические средства для сельского хозяйства», г. Москва, 2019 г.
– международной научно-технической конференции “Пром-Инжиниринг», г Сочи, 2020 г.
Публикации. По теме диссертации опубликовано 26 печатных работах, из них 8 статей в журналах, рекомендованных ВАК РФ, 3 статьи в рецензируемых зарубежных журналах из базы SCOPUS, две статьи внесены в базу цитирования AGRIS, 7 статей в периодических сборниках, трудах и тезисах международных и всероссийских конференций, получено 5 патентов на изобре- тения и полезные модели, одно свидетельство на программу для ЭВМ.
Структура и объем работы. Диссертация состоит из введения, пяти глав, заключения, биб- лиографического списка и приложений. Объем работы составляет 228 страниц, из них 219 страниц основного текста, 73 рисунка, 3 таблицы. Библиографический список содержит 331 источник.
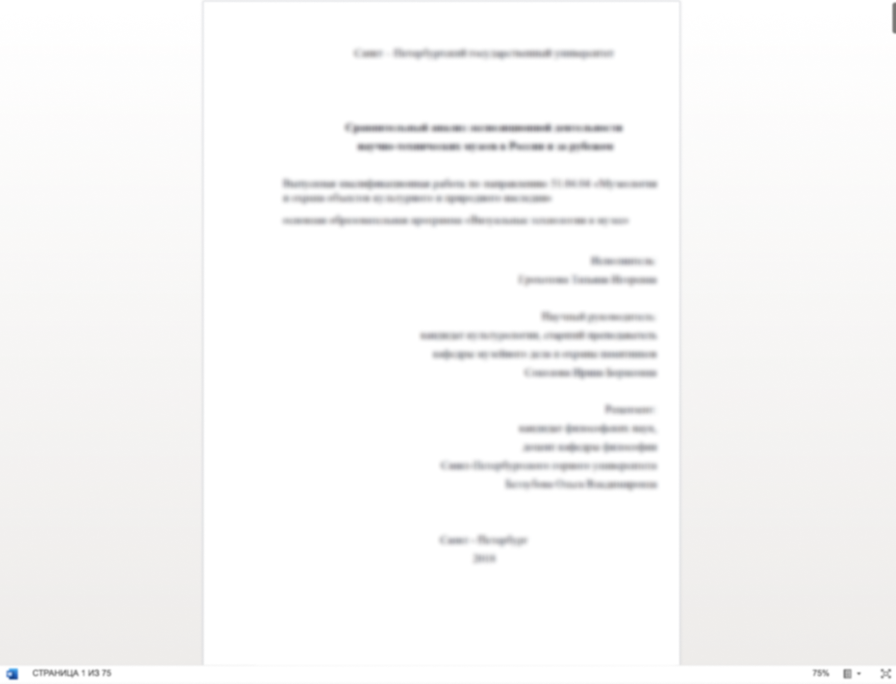
Публикации автора в научных журналах
Помогаем с подготовкой сопроводительных документов
Хочешь уникальную работу?
Больше 3 000 экспертов уже готовы начать работу над твоим проектом!