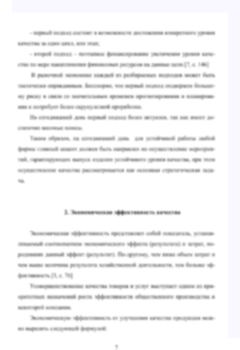
Автоматизированная система управления установкой для конверсии низкосортных топлив и промышленных отходов непрерывным световым потоком
В рамках магистерской диссертации предполагается разработать автоматизированную систему управления установкой для конверсии низкосортных топлив и промышленных отходов непрерывным световым потоком. Для данной системы будут разработаны функциональная схема, схема автоматизации, схема электрическая принципиальная, схема подключения внешних проводок и также, будет разработан внешний вид щита.
Введение……………………………………………………………………………………………….. 14
1 Классификация способов газификации твердого топлива ……………………. 17
2 Автотермический способ газификации ……………………………………………….. 18
3 Аллотермический способ свето-индуцированной газификации …………… 21
4 Результаты исследования ……………………………………………………………………. 24
4.1 Экспериментальная установка и методы исследования …………………….. 24
4.2 Описание калибровки экспериментальной установки ……………………….. 24
4.3 Описание эксперимента с использованием рабочей камеры ……………… 26
4.4 Методика регистрации температурного поля образца……………………….. 27
4.5 Методика регистрации изменения состава газа полученного в
рабочей камере ……………………………………………………………………………………… 28
4.6 Методика регистрации изменения массы образца в рабочей камере ….. 29
4.7 Результаты экспериментов и практические рекомендации ………………… 29
5 Анализ объекта автоматизации …………………………………………………………… 33
6 Разработка структуры автоматизированной системы управления ………… 35
6.1 Технические требования к АСУ ……………………………………………………….. 38
7 Разработка функциональной схемы автоматизированного управления … 42
8 Выбор технических средств и составление заказной спецификации …….. 46
8.1 Выбор датчика уровня ……………………………………………………………………… 46
8.2 Выбор микроволнового расходомера ……………………………………………….. 47
8.3 Выбор вихревого расходомера …………………………………………………………. 48
8.4 Выбор датчика температур ………………………………………………………………. 50
8.5 Выбор газоанализатора…………………………………………………………………….. 51
8.6 Выбор программируемого логического контроллера ………………………… 52
8.7 Выбор устройств защиты …………………………………………………………………. 56
8.8 Выбор исполнительного механизма …………………………………………………. 59
8.9 Выбор блока управления исполнительным механизмом …………………… 60
8.10 Выбор питания контроллера …………………………………………………………… 61
8.11 Выбор диодного модуля …………………………………………………………………. 62
8.12 Выбор трехходового клапана………………………………………………………….. 63
8.13 Выбор шиберной задвижки …………………………………………………………….. 64
8.14 Выбор электродвигателя ………………………………………………………………… 65
8.15 Выбор частотного преобразователя ………………………………………………… 66
8.16 Выбор источника света…………………………………………………………………… 68
8.17 Выбор автоматизированного рабочего места ………………………………….. 68
8.18 Составление заказной спецификации ……………………………………………… 70
9 Перечень входных и выходных сигналов…………………………………………….. 71
10 Проектирование принципиальное схема АСУ …………………………………… 74
11 Проектирование монтажной схемы АСУ …………………………………………… 76
12 Выбор проводов, кабелей и защитных труб……………………………………….. 78
13 Конструкторская разработка АСУ …………………………………………………….. 81
13.1 Щит автоматизации ……………………………………………………………………….. 81
14 Выбор регулирующего органа …………………………………………………………… 82
15 Разработка математического, программного и информационного
обеспечения ………………………………………………………………………………………….. 83
15.1 Математического обеспечения АСУ ………………………………………………. 83
15.2 Программное обеспечения АСУ …………………………………………………….. 84
15.3 Информационное обеспечения АСУ ………………………………………………. 87
16 Разработка SCADA-системы …………………………………………………………….. 88
17 Расчет параметров настройки регулятора ………………………………………….. 90
18 Финансовый менеджмент, ресурсоэффективность и
ресурсосбережение ……………………………………………………………………………… 101
18.1 Предпроектный анализ …………………………………………………………………. 102
18.1.1 Потенциальные потребители результатов исследования …………….. 102
18.1.2 Анализ конкурентоспособности технических решений ………………. 102
18.1.3 SWOT-анализ…………………………………………………………………………….. 104
18.2 Разработка перечня работ и оценка их выполнения ………………………. 107
18.3 Смета затрат на проект …………………………………………………………………. 110
18.3.1 Материальные затраты ………………………………………………………………. 110
18.3.1.1 Амортизация компьютерной техники………………………………………. 110
18.3.1.2 Затраты на заработную плату ………………………………………………….. 111
18.3.1.3 Затраты на социальные нужды ………………………………………………… 112
18.3.1.4 Прочие затраты……………………………………………………………………….. 112
18.3.1.5 Накладные расходы ………………………………………………………………… 112
18.3.2 Смета затрат на оборудование и монтажные работы…………………… 113
18.3.3 Определение экономической эффективности проекта ………………… 115
19 Социальная ответственность …………………………………………………………… 118
19.1 Правовые и организационные вопросы обеспечения безопасности .. 119
19.2 Производственная безопасность …………………………………………………… 120
19.2.1 Анализ опасных и вредных производственных факторов ……………. 121
19.2.2 Анализ вредных и опасных факторов, которые могут
возникнуть на рабочем месте при проведении исследований ……………….. 122
19.2.3 Обоснование мероприятий по снижению уровней воздействия
опасных и вредных факторов на исследователя (работающего) ……………. 127
19.3. Экологическая безопасность ……………………………………………………….. 128
19.3.1 Анализ влияния объекта исследования на окружающую среду …… 128
19.3.2 Анализ влияния процесса исследования на окружающую среду …. 129
19.3.3 Обоснование мероприятий по защите окружающей среды …………. 129
19.4 Безопасность в чрезвычайных ситуациях ……………………………………… 130
19.4.1 Анализ вероятных ЧС, которые может инициировать объект
исследований ………………………………………………………………………………………. 131
19.4.2 Анализ вероятных ЧС, которые могут возникнуть на рабочем
месте при проведении исследований ……………………………………………………. 131
19.4.3 Обоснование мероприятий по предотвращению ЧС и разработка
порядка действия в случае возникновения ЧС ……………………………………… 132
Заключение …………………………………………………………………………………………. 134
Список использованных источников ……………………………………………………. 136
Приложение А – Заказная спецификация приборов и средств
автоматизации …………………………………………………………………………………….. 143
Приложение Б – Обзор литературы на иностранном языке …………………… 145
Графические материалы: На отдельных листах
ФЮРА.421000.003 С1 Схема структурная
ФЮРА.421000.003 С2 Схема функциональная
ФЮРА.421000.003 Э3 Схема принципиальная электрическая
ФЮРА.421000.003 С4 Схема монтажная
ФЮРА.421000.003 ВО Общий вид щита АСУ
За последние 30 лет в мире наблюдается постоянно увеличивающиеся
темпы потребления не возобновляемых природных ресурсов. В свою
очередь, темпы увеличения потребления, приводят к повышению спроса на
ресурсы, и как следствие к повышению стоимости этих ресурсов. Так же,
стоит отметить тот факт, что в мире существуют большие площади
складирования отработанного топлива, которое может быть использовано
для целей энергопотребления человека. Таким образом, актуальной
становится задача разработки эффективных технологий комплексной
безотходной переработки горючих промышленных отходов и низкосортных
топлив. О важности и необходимости решения данной проблемы
свидетельствует то, что в седьмой рамочной программе научно-технического
сотрудничества стран ЕС предусмотрен специальный раздел по технологии
газификации горючи бытовых отходов и производства энергии с нулевыми
выбросами [1].
Одним из путей решения задачи по разработке эффективных
технологий, позволяющих использовать отработанное и низкосортное
топливо является – газификация.
Под газификацией понимается процесс преобразования органической
части твердого или жидкого топлива в горючие газы, под воздействием
высоких температур. Способ получения горючих газов, путем нагревания,
впервые был реализован французским ученым Филиппом Лебоне в 1799 г.
Данные способ газификации получил название сухая перегонка. До
начала 20-ого века, многие изобретатели и промышленные компании,
использовали метод, подобный сухой перегонки, иногда изменяя
конфигурацию рабочей камеры или способы загрузки топлива. Прорывом в
процессе газификации твердого топлива, послужило открытие химической
реакции, учеными Францом Фишером и Хансом Тропше. Суть этой реакции
заключалось в следующем, через раскалённый слой угля продували
перегретый водяной пар, продуктом такого процесса являлся водяной газ.
Водяной газ – это смесь оксида углерода и водорода.
Таким образом, открытие реакции «Фишер–Тропша» послужило
новым витком в развитии газификации твердых топлив. Данная технология
разрабатывалась и усовершенствовалась в Германии, так как Германия
обладала большими угольным запасами (Рурский угольный бассейн), но не
имела большого количества запасов нефти. Во времена Второй мировой
войны данная технология применялась для получения жидкого топлива,
которое использовалось в двигателях внутреннего сгорания немецкой
техники. После войны интерес к процессу «Фишер–Тропша» и технологиям
газификации резко снизился, так как были открыты крупные месторождения
полезных ископаемых и усовершенствование данной технологии потеряло
актуальность [2].
В начале 90-х годов, после осознания того, что полезные ископаемые
конечны, вновь вернулись к установкам, реализующим реакцию «Фишер–
Тропша» и были построены первые мощности по производству жидкого
топлива на основе этой реакции. В середине 2000-х годов, начали возникать
новые проблемы в окружающей среде, из-за загрязнений, вызванных
большими площадями скопившихся промышленных отходов и низкосортных
топлив. Научные сообщества стран, начали активно изучать новые способы
газификации промышленных отходов и низкосортных топлив.
В связи с этим необходимы исследования технологий газификации
твердого топлива, основных характеристик газогенераторных установок и
генераторных газов при использовании различных видов сырья, выбор
наиболее эффективных технологий, разработка принципов конструкций
оборудования для газификации низкосортного твердого топлива.
В настоящее время основным топливом для котельных и ТЭЦ
является природный газ, который является экологически чистым и дешевым
энергоносителем. Для повышения надежности котельных и ТЭЦ и
обеспечения бесперебойной работы источников тепловой энергии
необходимо резервное топливо.
Исходя из проанализированных данных, можно сделать вывод о том,
что создание автоматизированной системы управления установкой,
позволяющей повысить коэффициент использование низкосортного топлива,
приведет к повышению надежность ТЭЦ, снижению выбросов в атмосферу и
сокращению отвалы отработанного топлива.
Новый подход к созданию установки отличается от известных тем,
что полученные данные обеспечивают улучшенные технико-экономические
показатели по сравнению с предыдущими методиками и технологиями.
Практическая значимость исследований заключается в том, что:
1) с научной точки зрения разрабатывается новая технология, которая
может быть научно обоснована и запатентована. Она затрагивает такие
разделы науки как: тепломассообмен, механику жидкости и газа, БЖД;
2) с точки зрения обучения техническим специальностям, будут
разработаны новые методики обучения специалистов, которые впоследствии
могут быть внесены в программу обучения в университетах;
3) с точки зрения общенародного подхода, можно выделить то, что
снизиться вредных выбросов в атмосферу и повысится качество переработки
низкосортного топлива и промышленных отходов. Так же, за счет новой
технологии снизится себестоимость электроэнергии, за счет того, что в
стоимость реализации закладываются все экономические части производства,
в том числе и стоимость подготовки и производства топлива. И если
стоимость будет снижена, то снизится и стоимость реализации продукта.
Настоящая цель данной работы заключалась в следующем:
разработать и спроектировать автоматизированную систему управления
установкой для газификации низкосортного топлива, при использовании
которой будет реализован аллотермический способ конверсии топлива.
1 Классификация способов газификации твердого топлива
В рамках выполнения магистерской диссертации была разработана
автоматизированная система управления установкой для газификации
твердого низкосортного топлива. Разработанная система позволяет
автоматизировать процесс газификации, снизить риски возникновения
чрезвычайно ситуации, снизить количество вредных выбросов в атмосферу,
повысить качество переработки твердого топлива и сократить площади,
отведенные для хранения отработанного и низкосортного топлива.
Полученные результаты научных изысканий могут быть использованы
для масштабирования и создания серийного газогенераторного комплекса,
позволяющего газифицировать топлива для промышленности и социальных
нужд. По результатам научных изысканий был сформулирован ряд
практических рекомендаций по реализации предложенного подхода в
газификации топлива.
Спроектированная система состоит из трех уровней. Полевой уровень
представляет собой датчики измерения температур, давления, расхода, а
также комплект запорной арматуры и исполнительных механизмов. На
среднем уровне располагается щит контроля и управления АСУ, в составе
которого находится программируемый логический контроллер, верхний
уровень представляет собой АРМ оператора.
В ходе выполнения диссертации была разработана проектная
документация: схема структурная, схема функциональная, схема
принципиальная электрическая АСУ, схема монтажная соединений и общий
вид щита АСУ.
Пояснительная записка к проекту содержит подробное описание
экспериментального стенда, результатов выполненных экспериментальных
исследований, основного оборудования, приборов и технических средств
автоматизации, а также подробную методику выбора последних.
Кроме того, выполнены разделы «Социальная ответственность» и
«Менеджмент, ресурсоэффективность и ресурсосбережение», в котором
рассчитана общая сумма затрат на реализацию проекта (3,303 млн. руб.), а
рассчитанная эффективность проекта составила 858 тыс. рублей, что говорит
об эффективности реализации данного технического проекта.
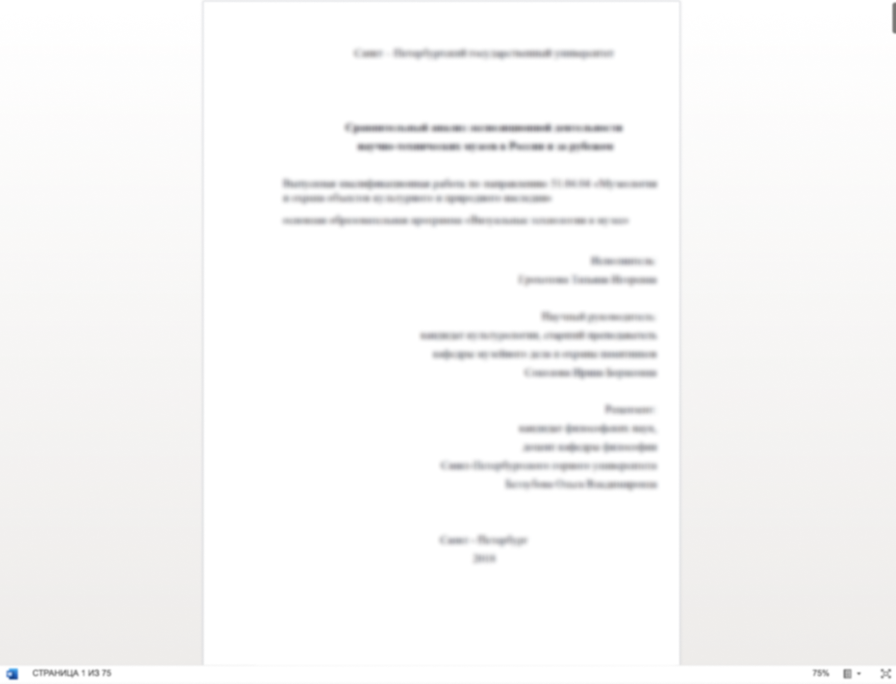
Хочешь уникальную работу?
Больше 3 000 экспертов уже готовы начать работу над твоим проектом!