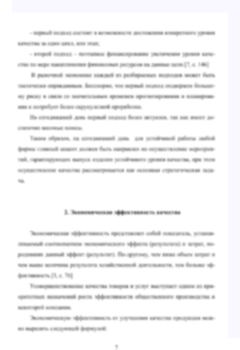
Автоматизированный контроль контуров регулирования нефтехимического производства
Объектом исследования является модель технологического процесса переработки сырой нефти разработанная в Honeywell UniSim design suite.
Целью магистерской диссертации является разработка и исследование автоматизированной системы мониторинга ключевых показателей эффективности контуров автоматического регулирования нефтехимического производства.
В работе представлены: анализ методов мониторинга контуров управления, анализ влияния контуров управления на технологический процесс, разработка интерфейса вывода технологических параметров, разработка системы мониторинга технологического процесса на языке программирования C#, построение контрольных карт Шухарта с автоматическим анализом данных.
Введение ……………………………………………………………………………………………………… 16
1 Требования к системе мониторинга контуров управления …………………………. 18
1.1 Требования к функциональным возможностям системы ………………………. 18
1.2 Требования к техническому обеспечению ……………………………………………. 18
1.3 Требования к программному обеспечению …………………………………………… 19
1.4 Требования к информационному обеспечению …………………………………….. 19
2 Современные системы мониторинга производительности контуров
управления ………………………………………………………………………………………………….. 21
2.1 Обзор решений ……………………………………………………………………………………. 21
2.2 Требования к мониторингу производительности контуров …………………… 22
2.3 Анализ производительности контура управления ………………………………… 23
2.4 Пользовательский интерфейс ………………………………………………………………. 25
2.5 Установка и настройка ………………………………………………………………………… 27
2.6 Преимущества программного обеспечения для оценки производительности
контуров …………………………………………………………………………………………………… 28
2.7 Proficy Plant Applications ……………………………………………………………………… 29
3 Разработка системы мониторинга контуров управления перегонкой сырой
нефти…………………………………………………………………………………………………………… 32
3.1 Анализ технологического процесс ……………………………………………………….. 32
3.1.1 Описание технологического процесса…………………………………………….. 32
3.1.2 Описание контуров регулирования…………………………………………………. 33
3.1.3 Технологические параметры контуров ……………………………………………. 42
3.1.4 Коэффициент полезного действия теплообменника ………………………… 44
3.1.5 Расчет кавитации клапана ………………………………………………………………. 45
3.2 Реализация программы ………………………………………………………………………… 46
3.2.1 Экспорт данных из UniSim …………………………………………………………….. 46
3.2.2 Вывод статистических данных по контурам …………………………………… 48
3.2.3 Статистические показатели пригодности процесса …………………………. 52
3.2.4 Контрольные карты Шухарта …………………………………………………………. 56
3.2.5 Анализ контрольных карт ………………………………………………………………. 61
3.3 Выводы по разделу ……………………………………………………………………………… 62
4 Финансовый менеджмент, ресурсоэффективность и ресурсосбережение ……. 64
4.1 Организация и планирование работ ……………………………………………………… 64
4.1.1 Продолжительность этапов работ …………………………………………………… 66
4.2 Расчет сметы затрат на выполнение проекта ………………………………………… 72
4.2.1 Расчет затрат на материалы ……………………………………………………………. 72
4.2.2 Расчет заработной платы ………………………………………………………………… 73
4.2.3 Расчет затрат на социальный налог ………………………………………………… 74
4.2.4 Расчет затрат на электроэнергию ……………………………………………………. 74
4.2.5 Расчет амортизационных расходов …………………………………………………. 75
4.2.6 Расчет расходов, учитываемых непосредственно на основе платежных
документов…………………………………………………………………………………………….. 76
4.2.7 Расчет прочих расходов …………………………………………………………………. 77
4.2.8 Расчет общей себестоимости разработки ………………………………………… 77
4.2.9 Расчет прибыли ……………………………………………………………………………… 78
4.2.10 Расчет НДС ………………………………………………………………………………….. 78
4.2.11 Цена разработки НИР …………………………………………………………………… 78
4.3 Оценка экономической эффективности проекта …………………………………… 78
5. Социальная ответственность ……………………………………………………………………. 80
5.1 Аннотация …………………………………………………………………………………………… 80
5.2 Правовые и организационные вопросы обеспечения безопасности ………. 82
5.3 Производственная безопасность …………………………………………………………. 83
5.4 Анализ опасных и вредных факторов …………………………………………………… 84
5.4.1 Микроклимат производственных помещений …………………………………. 84
5.4.2 Повышенный уровень шума …………………………………………………………… 85
5.4.3 Электромагнитные излучения ………………………………………………………… 86
5.4.4 Ионизирующее излучение ……………………………………………………………… 87
5.4.5 Освещённость рабочей зоны ………………………………………………………….. 88
5.4.6 Расчет освещенности рабочего места ……………………………………………… 89
5.4.7 Электробезопасность ……………………………………………………………………… 91
5.4.8 Пожарная безопасность ………………………………………………………………….. 92
5.5 Экологическая безопасность………………………………………………………………… 93
5.5.1 Анализ воздействия на окружающую среду ……………………………………. 93
5.6 Безопасность в чрезвычайных ситуациях …………………………………………….. 94
5.6.1 Перечень возможных чрезвычайных ситуаций на объекте………………. 94
5.7 Выводы по разделу ……………………………………………………………………………… 95
Заключение …………………………………………………………………………………………………. 96
Список используемой литературы ……………………………………………………………….. 97
Приложение A (справочное) Раздел на ИЯ …………………………………………………… 99
Нефтеперерабатывающее производство обеспечивается сотнями, иногда
тысячами контуров регулирования, которые управляют установкой в
соответствии с ее назначением. Установка может оптимально работать только
если все контуры регулирования идеально согласованы друг с другом. На
практике такое согласование до сих пор выполняется слишком длительным и
дорогим путем.
Для того чтобы достигнуть оптимальной производительности
технологического процесса, необходимо чтобы контура регулирования
параметров были всегда настроены на максимальную
производительность. Данный эффект может быть достигнут, только путем
непрерывного мониторинга производительности каждого контура
регулирования, а также при наличие принятых корректирующих действий в
случае обнаружения низкой производительности. Стоит отметить, что в
сложных и крупных технологических объектах диагностика и решение проблем
эффективности контуров управления достаточно затруднены.
Целью магистерской диссертации является разработка и исследование
автоматизированной системы мониторинга ключевых показателей
эффективности контуров автоматического регулирования нефтехимического
производства.
Для реализации поставленной цели необходимо решить следующие
задачи:
1. Изучить и описать технологический процесс перегонки нефти.
2. Проанализировать методы мониторинга контуров управления.
3. Проанализировать влияния контуров управления на
технологический процесс.
4. Разработать интерфейс вывода технологических параметров.
5. Разработать систему мониторинга технологических параметров на
языке программирования C#.
6. Разработать методику построения контрольных карт Шухарта с
автоматическим анализом данных.
1 Требования к системе мониторинга контуров управления
1.1 Требования к функциональным возможностям системы
Необходимо, чтобы система функционировала круглосуточно.
Система должна иметь переносные и встроенные средства
диагностирования и контроля, которые в свою очередь обязаны обеспечивать:
• Фоновый контроль компонентов АС (контроллеры, станции
персонала и операторов) во время функционирования.
• Тестовый контроль компонентов при включении или перезапуске,
предназначенный для детального самоконтроля и определения
функциональных отказов при включении устройства.
• Контроль элементов системы при проведении
ремонтно-восстановительных работ [1].
Система должна иметь гибкую структуру, легко адаптироваться к
изменению технологической схемы установки, обеспечивать
конфигурирование новых контуров измерения, контроля, регулирования и
программно-логического управления.
Система должна обеспечивать возможность управления установкой в
случае несущественных изменений технологии или методов управления путем
переналадки контуров управления силами обслуживающего персонала.
Система должна быть многофункциональным, восстанавливаемым,
ремонтируемым изделием.
1.2 Требования к техническому обеспечению
Комплекс используемых в системе технических средств должен быть
минимально достаточным для обеспечения функций, указанных в данном
техническом задании. Построение комплекса проводится на базе нижеуказанных
программно-технических комплексов:
• Контрольно-измерительные приборы и автоматика (датчики,
исполнительные механизмы, управляемые регуляторы и т.д.).
В ходе выполнения ВКР были проанализированы методы мониторинга
производительности контуров управления, был рассмотрен основной
функционал программных продуктов, изучены недостатки и преимущества
программного обеспечения для оценки производительности контуров. Также
были проведены анализ влияния контуров управления на технологический
процесс, оценка эффективности контуров управления.
Помимо этого, был разработан интерфейс вывода технологических
параметров, система мониторинга эффективности контуров на языке
программирования C#, а также методика построения и автоматический анализ
контрольных карт Шухарта.
Разработанная система мониторинга имеет возможность расширения и
модернизации, в соответствии с растущими требованиями и технологическими
возможностями.
1.Клюев А. С., Глазов Б. В., Дубровский А. Х., Клюев А. А.; под ред.
А.С.Клюева.Проектированиесистемавтоматизациитехнологических
процессов: справочное пособие. 2-е изд., перераб. и доп. – М.: Энергоатомиздат,
1990. – 464 с.
2.КомиссарчикВ.Ф.Автоматическоерегулирование
технологических процессов: учебное пособие. Тверь 2001. – 247 с.
3.Попович Н.Г.,КовальчукА.В.,КрасовскийЕ.П.,
Автоматизация производственных процессов и установок. – К.: Вищашк.
Головное изд-во, 1986. – 311с.
4.Tuning Guidelines for Utility Fossil Plant Process Control. Volume 2, The
Technician’s Guide to Tuning.EPRI , Palo Alto, CA: 1994. TR-102052.
5.N.F. Thornhill, M.A.A.S Choudhury, and S.L. Shah,The impact of
compression on data-driven process analyses, Journal of Process Control, 14, 389–398,
2004
6.N.F. Thornhill, B. Huang, H. Zhang, Detection of multiple oscillations in
control loops, Journal of Process Control 13, 91–100, 2003
7.L.D. Desborough, and T.J. Harris, Performance assessment measures for
univariate feedback control, Canadian Journal of Chemical Engineering, 70, 1186-
1197, 1992
8.Powermag. [Электронный ресурс] – Режим доступа – URL:
https://www.powermag.com/monitoring-control-loop-performance/(дата
обращения: 2.04.2018).
9.ГромаковЕ.И.,ЛиепиньшА.В.Проектирование
автоматизированных систем управления нефтегазовыми производствами:
учебно-методическое пособие: Томский политехнический университет. —
Томск, 2016, – 371с.
10. Виноградов С.Н., Таранцев К.В. Выбор и расчет теплообменников //
учебное пособие, Пенза 2001. – 100 с.
11. Cadis.[Электронныйресурс]–Режимдоступа–URL:
https://www.cad-is.ru/blog_post/floefd-gidrodinamika-kpd-teploobmennika(дата
обращения: 25.04.2018).
12. АДЛ (Разработка, производство и поставки оборудования для
инженерных систем) [Электронный ресурс] – Режим доступа – URL:
https://adl.ru/about/publications/truboprovodnaya-armatura/pravila-podbora-
reguliruyushchikh-klapanov (дата обращения: 28.04.2018).
13. ГОСТ Р ИСО 7870-2-2015 Статистические методы. Контрольные
карты. Часть 2. Контрольные карты Шухарта
14. ГОСТ12.1.005-88ССБТ.Общиесанитарно-гигиенические
требования к воздуху рабочей зоны.
15. ГОСТ 12.1.003-2014 ССБТ. Шум. Общие требования безопасности.
16. ГОСТ 12.1.006-84 ССБТ. Электромагнитные поля радиочастот.
Общие требования безопасности.
17. ГОСТ 15484-81 Излучения ионизирующие и их измерения, термины
и определения
18. ГОСТ Р 55710-2013 Освещение рабочих мест внутри зданий. Нормы
и методы измерений.
19. Сапронов,Ю.Г.Аттестациярабочихместпоусловиям
освещённости:лабораторныйпрактикумподисциплине«Безопасность
жизнедеятельности. – Шахты: ГОУ ВПО «ЮРГУЭС», 2010. – 64 с.
20. ГОСТ 12.1.019-2017 ССБТ. Электробезопасность. Общие требования
и номенклатура видов защиты
21. ГОСТ12.1.004-91ССБТ.Пожарнаябезопасность.Общие
требования.
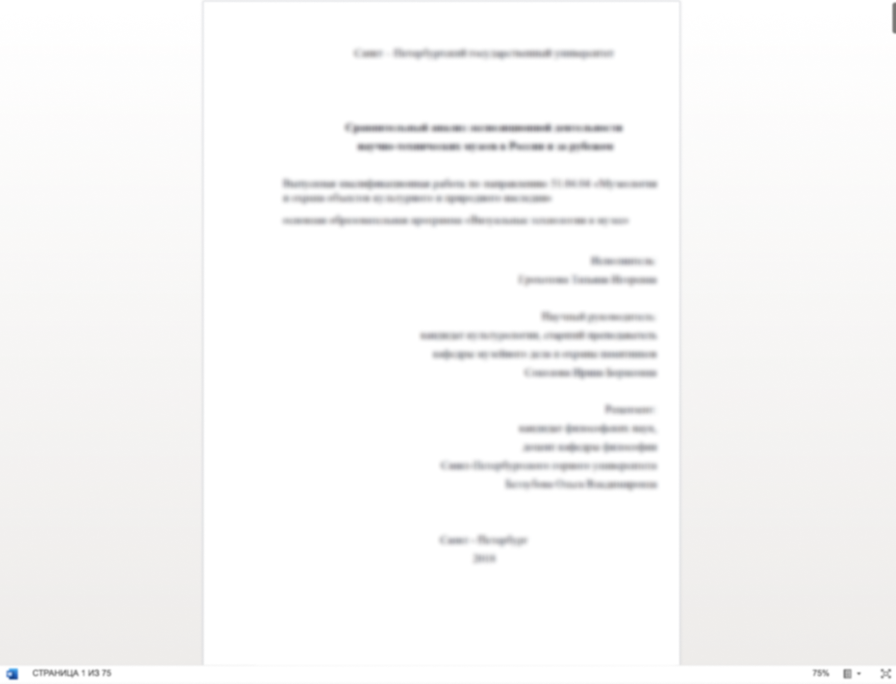
Хочешь уникальную работу?
Больше 3 000 экспертов уже готовы начать работу над твоим проектом!