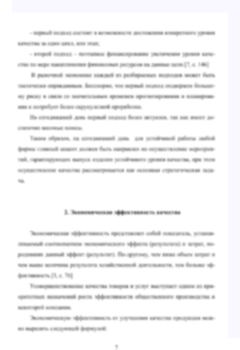
Детектирование и классификация дефектов в металлических заготовках с использованием методов машинного обучения
Целью выпускной квалификационной работы является статистический анализ данных технологического процесса и параметров конечной продукции для оценки ее качества, а также детектирования и классификации различных видов дефектов и отклонений выпускаемой продукции.
Обозначения и сокращения……………………………………………………………………………………………………. 14
Термины и определения…………………………………………………………………………………………………………. 15
Введение …………………………………………………………………………………………………………………………………. 17
1 Описание технологического процесса…………………………………………………………………………………. 23
1.1 АСУТП непрерывной разливки стали………………………………………………………………………….. 29
1.2 Система контроля качества ………………………………………………………………………………………….. 30
2 Стек технологий ………………………………………………………………………………………………………………….. 34
2.1 Выбор языка программирования …………………………………………………………………………………. 34
2.2 Среда разработки ………………………………………………………………………………………………………….. 35
2.3 Используемые библиотеки ……………………………………………………………………………………………. 36
3 Подготовка исходных данных …………………………………………………………………………………………….. 38
4 Реализация методов машинного обучения………………………………………………………………………….. 50
4.1 Описание задачи классификации …………………………………………………………………………………. 50
4.2 Метрики качества в задачах классификации ………………………………………………………………. 51
4.3 Формирование тренировочного и тестового наборов данных ……………………………………… 53
4.4 Используемые методы классификации ………………………………………………………………………… 54
4.4.1 Дерево решений ………………………………………………………………………………………………………. 55
4.4.2 Метод ближайших соседей………………………………………………………………………………………. 61
4.4.3 Логистическая регрессия ………………………………………………………………………………………… 65
4.4.4 Наивный Байес ……………………………………………………………………………………………………….. 69
4.4.5 Метод опорных векторов (SVM) …………………………………………………………………………….. 72
4.4.6 Метод XGBoost ………………………………………………………………………………………………………… 76
4.4.7 Сравнение результатов …………………………………………………………………………………………… 79
5 Интеграция модели МО в технологический процесс ………………………………………………………….. 82
6 Финансовый менеджмент, ресурсоэффективность и ресурсосбережение …………………………… 86
6.1 Организация и планирование работ …………………………………………………………………………….. 86
6.1.1 Продолжительность этапов работ…………………………………………………………………………… 88
6.2 Расчет сметы затрат на выполнение проекта ………………………………………………………………. 94
6.2.1 Затраты на материалы и покупные изделия ………………………………………………………….. 94
6.2.2 Затраты на заработную плату…………………………………………………………………………………. 95
6.2.3 Затраты на социальный налог ……………………………………………………………………………….. 96
6.2.4 Затраты на электроэнергию ……………………………………………………………………………………. 96
6.2.5 Амортизационные расходы …………………………………………………………………………………….. 97
6.2.6 Расходы, учитываемые непосредственно на основе платежных документов ………… 98
6.2.7 Прочие расходы ………………………………………………………………………………………………………. 99
6.2.8 Общая себестоимость разработки …………………………………………………………………………… 99
6.2.9 Доход ……………………………………………………………………………………………………………………….. 99
6.2.10 Затраты на НДС ……………………………………………………………………………………………………. 99
6.2.11 Цена разработки НИР …………………………………………………………………………………………… 99
6.3 Оценка экономической эффективности проекта ………………………………………………………… 100
7 Социальная ответственность…………………………………………………………………………………………….. 101
Введение ……………………………………………………………………………………………………………………………. 101
7.1 Аннотация……………………………………………………………………………………………………………………. 101
7.2 Правовые и организационные вопросы обеспечения безопасности …………………………… 103
7.3 Производственная безопасность …………………………………………………………………………………. 104
7.4 Анализ вредных и опасных факторов …………………………………………………………………………. 105
7.4.1 Электромагнитные излучения ……………………………………………………………………………… 105
7.4.2 Освещенность рабочего места ………………………………………………………………………………. 107
7.4.3 Повышенный уровень шума …………………………………………………………………………………. 110
7.4.4 Микроклимат в помещении ………………………………………………………………………………….. 111
7.5 Электробезопасность …………………………………………………………………………………………………… 113
7.6 Экологическая безопасность ……………………………………………………………………………………….. 113
7.6.1 Анализ влияния объекта на окружающую среду ………………………………………………….. 114
7.7 Безопасность в чрезвычайных ситуациях…………………………………………………………………… 115
7.7.1 Анализ вероятных ЧС, которые может инициировать объект исследований и
обоснование мероприятий по предотвращению ЧС……………………………………………………… 115
Вывод по разделу………………………………………………………………………………………………………………. 118
Заключение…………………………………………………………………………………………………………………………… 119
Список литературы ……………………………………………………………………………………………………………… 121
Приложение А (справочное) Раздел на английском языке………………………………………………….. 125
Проверка контроля качества заключается в проверке всех видов
значений (количественных, качественных и т.д.) процесса или продукции на
соответствие техническим требованиям. Процесс контроля качества является
неотъемлемой частью любого производственного процесса и позволяет
оценить надежность изготовления продукции и будущего ее использования.
Сущность такого контроля заключается в приобретении информации о
состоянии объекта и сопоставлении полученных результатов с
установленными требованиями, зафиксированными в стандартах, условиях
поставки и т.д. Основной задачей контроля является отделение качественных
изделий от бракованных. В современных условиях все больше предприятий
сосредотачиваются на тщательном контролировании процесса и
придерживаются концепции “менеджмента качества”, а не на детектировании
брака. Качество продукции – один из важнейших показателей, поэтому
выживаемость предприятия в рыночных условиях, повышение эффективности
производства и другие важнейшие аспекты напрямую зависят от повышения
контроля [1].
Если говорить о контроле качества в процессе литья заготовок, то
механические свойства, параметры геометрии являются основными
признаками объекта. Благодаря использованию АСУ производители
сталелитейной продукции обеспечивают потребителям вышеупомянутые
показатели.
Состояние поверхности продукта (сталелитейной заготовки) одна из
основных составляющих качества продукта в целом. Как правило, контроль
поверхности осуществляется на конечных этапах производства.
Для детектирования и классификации дефектов как правило
используются визуальные способы: либо применяются специальные системы,
либо внешний осмотр [3].
Проведение осмотра затрудняют такие факторы как высокая
температура продукта, окисление поверхности, а также движение полосы
(конвейера), в результате анализ дефектов возможен только после остывания.
Это приводит к увеличению количества бракованной продукции, особенно в
случае прокатного происхождения дефекта [2].
Как следствие необходимо как с высокой точностью обеспечивать
детектирование наличия дефекта, так и правильную его классификацию.
Проблематика
В период работы над магистерской диссертацией было изучено одно из
наиболее популярных направлений в настоящее время – машинное обучение.
Для выполнения целей и задач, поставленных в работе, был изучен основной
стек технологий, включающий язык программирования, среду разработки и
необходимые библиотеки, обоснование применения которых описано в главе
2.
Глава 3 полностью посвящена методам обработки исходной
информации, которые могут быть применены практически к любому набору
данных, используемому в дальнейшем для реализации методов машинного
обучения.
Также в работе (глава 4) описаны основные методы машинного
обучения, приведено математическое описание и обоснование используемых
в них алгоритмов. Были рассмотрены как классические методы, так и наиболее
современные разработки. Оценка точности моделей осуществлялась по
различным метрикам качества для более комплексного анализа. По
результатам оценок лучшим методом оказался “XGBoost” с показателями
точности 77% для детектирования и 88% для классификации дефектов.
Показатели точности не позволяет полностью доверяться вышеупомянутой
модели на данный момент, однако она может использоваться как инструмент
для первичного анализа качества. Дальнейшее накопление данных позволит
только увеличить точность модели, в результате чего она сможет играть роль
экспертной системы. Интеграция подобной модели в 3-х уровневую АСУТП
представляет собой 4-ый уровень (уровень управления цехом), на котором
будут решаться задачи планирования ресурсов, управления техническим
обслуживанием и другие.
Используемые в работе методы и модели являются гибким инструментом,
которые могут применяться для контроля качества практически в любой
отрасли, в связи с чем их применение особенно актуально в условиях
нацеленности большинства предприятий на цифровизацию производства.
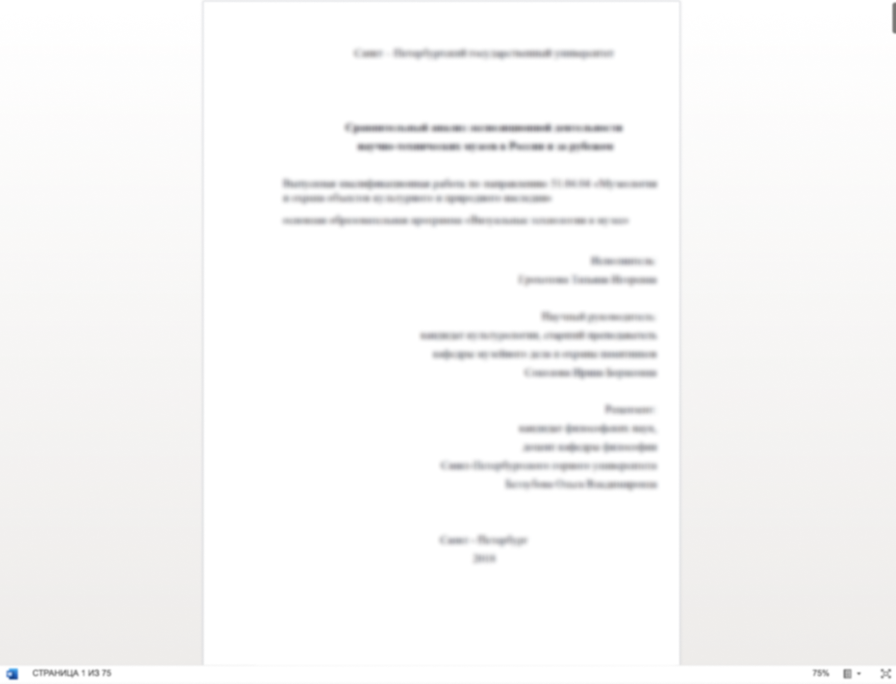
Хочешь уникальную работу?
Больше 3 000 экспертов уже готовы начать работу над твоим проектом!