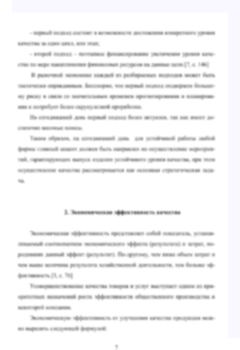
Методы ремонта дефектных участков линейной части магистральных газопроводов
В процессе исследования были рассмотрены методы обследования, и ремонта дефектных участков линейной части магистральных газопроводов, с целью выявления эффективных методов ремонта с учетом рекомендации ДДО. Так как сканер дефектоскоп с некоторой не точностью показывает расположение и размер дефектов, а также при обследовании бывает, что дефекты не подтверждаются.
Сокращение …………………………………………………………………………………………………………….. 14
Обзор литературы ………………………………………………………………………………………15
ВВЕДЕНИЕ ……………………………………………………………………………………………….17
1 Анализ дополнительного диагностического обследования дефектных
участков линейной части МГ при проведении в шурфах …………………………………… 20
1.1 Последовательность проведения дополнительного обследования …………… 20
1.2 Методика определения местоположения дефектов по данным
внутритрубной диагностики ………………………………………………………………………………. 22
1.3 Подготовка поверхности трубы к проведению дополнительного
обследования ……………………………………………………………………………………………………….. 26
1.4 Порядок проведения дополнительного обследования дефектов ………………. 28
1.4.1 Дефекты геометрии трубы ……………………………………………………………………… 28
1.4.2 Дефекты потери металла…………………………………………………………………………. 32
1.4.3 Дефекты стенки трубопровода ……………………………………………………………….. 37
1.4.4 Дефекты сварных швов (поперечных, продольных и спиральных)……. 43
1.4.5 Комбинированные дефекты ……………………………………………………………………. 46
1.5 Объемы и методы контроля труб и соединительных деталей
трубопроводов ……………………………………………………………………………………………………… 47
1.6 Порядок и сроки оформления документации по результатам
дополнительного обследования дефектов в шурфах, сроки хранения
результатов дополнительного обследования ……………………………………………..51
2 Анализ назначения методов ремонта дефектных участков линейной части
магистральных газопроводов ………………………………………………………………………………… 55
2.1 Методы ремонта трубных секций и сварных соединений, содержащих
дефекты, и отдельных дефектов ………………………………………………………………………… 55
2.2 Порядок назначения методов ремонта ………………………………………………………… 56
2.3 Критерии оценки взаимодействия дефектов ………………………………………………. 59
2.4 Критерии назначения метода ремонта дефектных труб ……………………………. 61
2.4.1 Назначение метода ремонта для ремонтной зоны ………………………………… 61
2.4.2 Ремонт контролируемой шлифовкой …………………………………………………….. 64
2.4.3 Ремонт муфтой …………………………………………………………………………………………. 64
2.4.4 Ремонт заменой катушки поверхностных дефектов трубы …………………. 73
2.4.1.1 Ограничения на применение муфт и катушек для ремонта трубы
и участка газопровода …………………………………………………………………………………….. 74
3 Расчет оценки работоспособности участков магистральных газопроводов с
коррозионными дефектами ………………………………………………………………………….75
3.1 Определение и схематизация одиночных дефектов ………………………………….. 75
3.1.1 Оценка работоспособности участка газопровода с одиночными
дефектами при учете напряжений от внутреннего давления ………………………. 76
3.1.2 Оценка работоспособности участка газопровода с одиночными
дефектами при учете напряжений от внутреннего давления, осевых и
изгибающих нагрузок и воздействий …………………………………………………………….. 78
3.2 Методы схематизации и оценка групповых дефектов с учетом их
взаимодействия ……………………………………………………………………………………………………. 81
3.2.1 Определение и схематизация групповых дефектов. Учет
взаимодействия дефектов ………………………………………………………………………………… 81
3.2.2 Оценка работоспособности участка газопровода с групповыми
дефектами при учете напряжений от внутреннего давления ……………………….. 84
4 Исследование дефектного участка действующего газопровода. Выбор
метода ремонта для дальнейшей эксплуатации трубопровода………………………..88
4.1 Выявление дефектов при ДДО с помощью методов НК. Оформление
отчетных документов для назначения методов ремонта …………………………………. 88
4.2 Назначение метода ремонта и подготовительные работы ………………………… 92
Заключение ………………………………………………………………………………………………..98
5 Социальная ответственность …………………………………………………………………….99
5.1 Производственная безопасность ………………………………………………………………….. 99
5.2 Анализ опасных производственных факторов …………………………………………. 100
5.3 Анализ основных вредных производственных факторов ………………………… 109
5.4 Экологическая безопасность при авариях на газопроводах …………………. 113
5.5 Мероприятия снижающие воздействие на окружающую среду при
эксплуатации газопроводов ……………………………………………………………………. 114
5.6 Мероприятия для безопасной эксплуатации газопроводов для
окружающей среды ……………………………………………………………………………….. 116
5.7 Безопасность на магистральных газопроводах при ЧС ……………………….. 117
6 Финансовый менеджмент, ресурсоэффективность и ресурсосбережение …… 119
6.1 Готовность проекта к коммерциализации …………………………………………………. 119
6.2 Календарный план проекта ………………………………………………………………………… 121
6.3 SWOТ-анализ ……………………………………………………………………………………………….. 123
Лист
Оглавление 12
Изм. Лист № докум. Подпись Дата
6.4 Материальные потери при проведении аварийно-восстановительных
работ ……………………………………………………………………………………………………………………. 124
6.5 Затраты на амортизационные отчисления ………………………………………………… 125
6.6 Затраты на материалы и оборудования ……………………………………………………… 125
6.7 Расчет затрат на оплаты труда рабочего персонала и специалистов ……… 125
Заключение ……………………………………………………………………………………………… 126
СПИСОК ЛИТЕРАТУРЫ …………………………………………………………………………. 127
ПРИЛОЖЕНИЕ А ……………………………………………………………………………………. 130
ПРИЛОЖЕНИЕ Б …………………………………………………………………………………….. 132
ПРИЛОЖЕНИЕ В ……………………………………………………………………………………. 135
ПРИЛОЖЕНИЕ Г …………………………………………………………………………………….. 136
ПРИЛОЖЕНИЕ Д ……………………………………………………………………………………. 137
ПРИЛОЖЕНИЕ Е…………………………………………………………………………………….. 138
ПРИЛОЖЕНИЕ Ж …………………………………………………………………………………… 139
ПРИЛОЖЕНИЕ З …………………………………………………………………………………….. 140
Обследование при помощи диагностических устройств части магистральных
газопроводов России, которое проводилось на протяжении последних 10 лет
внутритрубными интеллектуальными снарядами, на основе полученной
информации позволяет дать оценку техническому состоянию и принять меры,
повышающие надежность средств, которые находились в эксплуатации
длительный промежуток времени в сложных условиях таких как: финансовые
трудности и материальные ресурсы при реконструкции и ремонте дефектных
участков МГ.
Известно, что основное влияние на техническое состояние МГ оказывает
коррозия. Проанализировав распределение коррозионных дефектов,
расположенных на участках МГ Западно-Сибирского региона, полученных по
данным диагностических снарядов, показал неравномерность распределения
дефектов по длине, и что имеет прямую связь с различным давлением на
трубопроводе. Такой тип дефектов как «потеря металла» имеет зависимость от
факторов таких как степени заболоченности, а также участники имеющие
переходы между грунтами с различной несущей способностью.
Основная причина аварий и отказов связана с коррозионными дефектами и
напряженно-деформированным состоянием, которое не может выявить
внутритрубная инспекция, а также прогибами при похождении магистрального
газопровода через реки и болотистые места, участки с многолетним
промерзанием грунта. При оттаивании грунта происходит перемещение нитки
трубопровода в продольном профиле – это перемещение характеризуется
потерей устойчивости и выхода на поверхность трубопровода с образованием
дефекта «гофр» и арок.
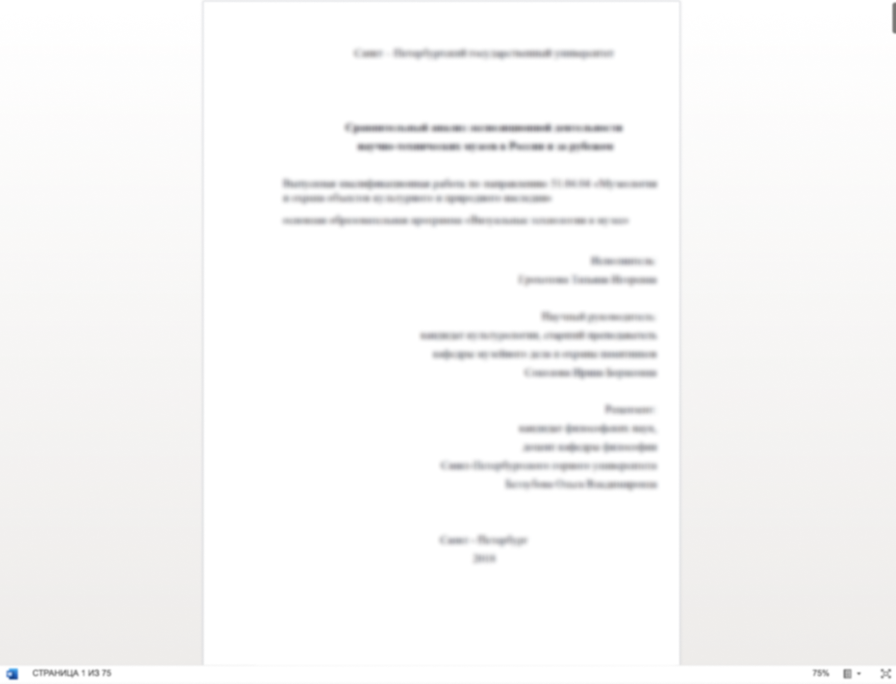
Хочешь уникальную работу?
Больше 3 000 экспертов уже готовы начать работу над твоим проектом!