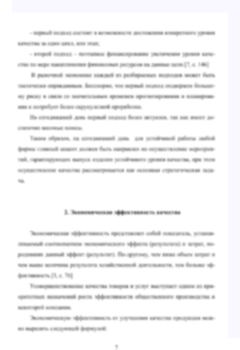
Повышение эффективности нефтяных скважин в условиях коррозионной агрессивности скважинной продукции
Объектом исследования является ингибиторы коррозии и насосно-компрессорные трубы.
Цель работы – провести глубокий анализ ингибиторов коррозии технологии подачи их в скважину и глубокий анализ насосно-компрессорные труб. Определить оптимальную дозировку реагента и оптимальный тип насосно-компрессорных труб для данных условий. В процессе исследования изучались негативные влияния коррозии на работу глубинно-насосного оборудование, рассматривались наиболее популярные технологии подачи ингибитора в скважину, а также проведён углубленный анализ ингибитор… Область применения: разработаны рекомендации для достижения наилучших показателей МРП и СНО.
Введение …………………………………………………………………………………………………………………………………… 9
1. ОБЗОР ПРОБЛЕМЫ КОРРОЗИИ НЕФТЕПРОМЫСЛОВОГО ПОДЗЕМНОГО
ОБОРУДОВАНИЯ СКВАЖИНЫ ………………………………………………………………………………………….. 11
1.1 Факторы, определяющие коррозионную агрессивность нефтяных скважин …… 11
1.2 Классификация типов коррозионных повреждений на нефтяных месторождениях …….. 16
1.3 Анализ причины коррозионного повреждения подземного оборудования в нефтяных
скважинах ………………………………………………………………………………………………………………………………. 20
2 СОВРЕМЕННЫЕ МЕТОДЫ ЗАЩИТЫ ОТ КОРРОЗИИ ПОДЗЕМНОГО
СКВАЖИННОГО ОБОРУДОВАНИЯ …………………………………………………………………………………… 29
2.1. Способы защиты от коррозии ………………………………………………………………………….. 29
2.1.1 Технология задавки ингибитора в призабойная зона пласта (ПЗП) ……………….. 31
2.1.2. Технология периодического дозирования ингибиторов коррозии (ИК) в
затрубное пространство скважины ………………………………………………………………………. 33
2.1.3. Технология непрерывного дозирования с помощью узел дозировки химриагента
(УД, УДХ) ………………………………………………………………………………………………………………… 35
2.1.4. Технология непрерывного дозирования с помощью скважинного контейнера . 36
2.1.5. Использование капсулированных ингибиторов………………………………………………. 38
2.2. Оценка коррозионного состояния оборудования……………………………………………………………. 39
2.2.1. Мониторинг коррозионного состояния извлекаемых НКТ ………………………… 40
2.2.2. Порядок подготовки образцов труб для последующего металлографического
исследования……………………………………………………………………………………………………………. 41
2.2.3. Отбор образцов НКТ от подвесок опытных скважин ………………………………. 41
2.2.4. Основные положения по отбору образцов …………………………………………………. 43
2.2.5. Осмотр образцов НКТ и их подготовка к исследованиям ………………………….. 45
2.2.6. Анализ поверхности исследуемых образцов и определение глубины
коррозионных повреждений ……………………………………………………………………………………. 48
3. АНАЛИЗ КАЧЕСТВА ТРУБ НКТ НА МЕСТОРОЖДЕНИИ «Х» …………………………………. 50
3.1. НКТ которые были использованы в 2015 году …………………………………………………… 50
3.2. Насосно-компрессорные трубы(НКТ) Majorpack…………………………………………… 50
3.3. Насосно-компрессорные трубы (НКТ) с внутренним покрытием ТС-3000 ….. 51
3.4. Насосно-компрессорные трубы (НКТ) с диффузионно цинковым покрытием
(ДЦП) ………………………………………………………………………………………………………………………. 51
4 ФИНАНСОВЫЙ МЕНЕДЖМЕНТ ………………………………………………………………………………… 63
5. СОЦИАЛЬНАЯ ОТВЕТСТВЕННОСТЬ ……………………………………………………………………………. 73
5. 1 Анализ вредных производственных факторов ………………………………………………….. 75
5.1.1. Повышенный уровень шума на рабочем месте ………………………………………………. 76
5.1.2. Отклонение показателей климата на открытом воздухе ……………………………. 77
5.2 Анализ опасных производственных факторов ………………………………………………….. 78
5.2.1. Механические опасности ……………………………………………………………………………….. 78
5.2.2. Статическое электричество…………………………………………………………………………. 79
5.3. Охрана окружающей среды ………………………………………………………………………………. 81
5.3.1.Охрана атмосферного воздуха от загрязнения ……………………………………………….. 82
5.4. Охрана поверхностных и подземных вод от загрязнения ………………………………………………. 83
5.5. Охрана и рациональное использование земель ……………………………………………………………… 83
5.6. Безопасность в чрезвычайных ситуациях………………………………………………………………………. 85
5.6.1 Существует несколько методов ликвидации разлива нефти: ……………………….. 86
5.7 Правовые и организационные вопросы обеспечения безопасности ………………………………. 87
Организационные мероприятия ……………………………………………………………………………… 87
Особенности законодательного регулирования проектных решений …………………….. 90
Список литературы ……………………………………………………………………………………………………………….. 92
Приложение А ………………………………………………………………………………………………………………………… 95
При добыче нефтепродуктов все компании сталкиваются с коррозией
подземного оборудования. Известен тот факт, что оборудование наземное
имеет больший срок эксплуатации, чем подземное. Подземное оборудование,
как правило, становится непригодным и выходит из строя в первый год
эксплуатации, и причиной этому зачастую служит именно коррозия.
С увеличением сроков эксплуатации внутрискважинного оборудования
значимость фактора коррозии среди причин отказов ГНО повышается.
Решению этой проблемы во многих компаниях уже сегодня уделяется
внимания не меньше, чем традиционной проблеме коррозионного разрушения
наземного оборудования. Представители добывающих компаний отмечают
рост доли коррозионного фонда и процента отказов внутрискважинного
оборудования, связанных с коррозией.
В добыче и переработке нефтепродуктов одной из важных проблем
стоит коррозия металла комплексов подземного оборудования.
Износ оборудования является одним из значительных факторов
опасности, влияющих на состояние промышленной безопасности,
возникновение отказов, разгерметизации трубопроводов, приводящих к
авариям, сопровождающимся разливами нефти, взрывами и разрушениями.
Главной и основной причиной аварий является коррозия металла.
Коррозией называется процесс разрушения материалов в результате
взаимодействия с агрессивной средой. При этом в результате химического или
физико-химического взаимодействия с окружающей средой происходит
потеря их эксплуатационных свойств. Нередко под коррозией
подразумевается лишь процесс разрушения металлов, что не совсем
правильно, так как понятие коррозии применимо и к неметаллам. Тем не менее
механизмы и кинетика коррозионных процессов для металлов и неметаллов
будут различными.
Коррозия металлов представляет собой разрушение их поверхности в
результате химического или электрохимического взаимодействия с
агрессивной средой. Термодинамически коррозия металлов возможна в
случае, если в результате коррозионного процесса уменьшается свободная
энергия системы.
В мире коррозия ежегодно приводит к миллиардным убыткам, причем
основной ущерб, причиняемый ею, заключается не в потере металла как
такового (в мире до 20% металла в год уходит именно в коррозионные
отходы), а в разрушении дорогостоящих изделий и оборудования. Еще
больший ущерб наносят косвенные потери при простоях оборудования при
замене прокорродировавших деталей и узлов, утечке нефти и газа, нарушении
технологических процессов. Убытки от коррозии, таким образом, нельзя
сводить лишь к прямым потерям – стоимости разрушившихся конструкций,
замены оборудования и затратам на мероприятия по защите от коррозии.
В США, по данным NACE, ущерб от коррозии, включая затраты на
борьбу с ней, составляют 3,1% ВВП ($276 млрд в год), в Германии – 2,8%
ВВП. В пределах 2–4% ВВП находится этот показатель и в других развитых
странах. При этом потери металла, включающие вышедшие из строя
металлические конструкции, изделия, оборудование, составляют 10–20%
годового производства стали.
В нашей стране нет официальной статистики, которая бы отражала
экономический ущерб от коррозии, но, по некоторым оценкам, он составляет
не менее 5% от ВВП. Это значит, что объем продукции, эквивалентный
годовому производству, к примеру, Новолипецкого металлургического
комбината, ежегодно тратится только на восполнение черного металла,
пораженного коррозией.
1. ОБЗОР ПРОБЛЕМЫ КОРРОЗИИ НЕФТЕПРОМЫСЛОВОГО
ПОДЗЕМНОГО ОБОРУДОВАНИЯ СКВАЖИНЫ
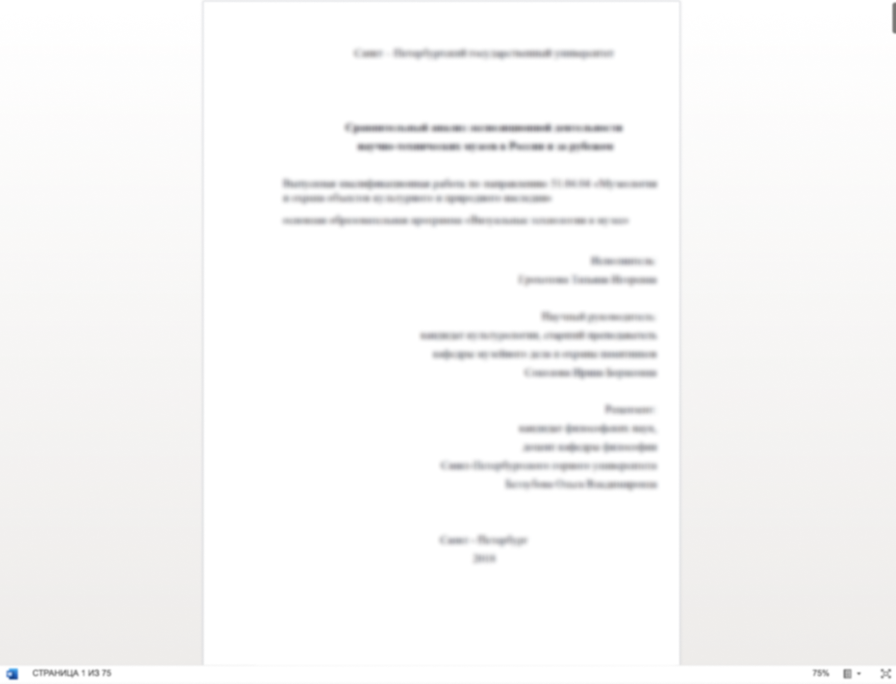
Хочешь уникальную работу?
Больше 3 000 экспертов уже готовы начать работу над твоим проектом!