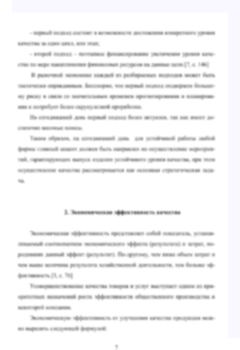
Разработка технологий окислительного обессеривания дизельных фракций
В процессе исследования проводились эксперименты по обессериванию дизельных фракций смесью перекиси водорода и муравьиной кислоты и в ходе каталитической гидроочистки, определялось общее содержание серы, групповой углеводородный состав, групповой состав серосодержащих групп соединений, элементный анализ для определения содержания общего азота, были рассчитаны эффективные константы скорости, степень десульфуризации дизельного топлива, рассчитаны термодинамические характеристики, составлена математическая модель, проведена оптимизация и составлена технологическая схема и схема автоматизации блока окислительного обессеривания, сконструирован реактор.
Введение ……………………………………………………………………..5
1 Современные процессы и технологические схемы удаления серы из
нефтяных фракций…………………………………………………………..…..10
2 Аналитический обзор……………………………………………………14
2.1 Теоретические основы десульфуризации…………………………….14
2.2 Пути и методы совершенствования технологии обессеривания ….15
2.3 Каталитическая гидроочистка……………………….…………….…17
2.4 Окислительная десульфуризация ……………………………….……21
3 Объект и методы исследования………………………..………………..25
3.1 Установка и параметры окислительного обессеривания..…….……25
3.2 Установка и параметры каталитической гидроочистки …….……..27
4 Экспериментальная часть……………………….……………..…….….28
4.1 Окислительное обессеривание……………………………………….28
4.1.1 Групповой состав серосодержащих соединений………………….30
4.2 Каталитическая гидроочистка и совмещение процессов ………….34
4.3 Разработка технологической схемы процесса окислительного
обессеривания ……………………………………………………………………37
4.3.1 Экспериментальное определение области оптимума………….…37
4.4 Технологическая схема окислительного обессеривания ……….….38
4.5 Моделирование и оптимизация процесса окислительного
обессеривания……………………………………………………………………..39
4.6 Технологические расчеты процесса и основных аппаратов…….…44
4.6.1 Расчет горизонтального реактора обессеривания………..………..46
4.6.1.1 Расчет первой секции…………………….…………………….…46
4.6.1.2 Расчет второй секции………………………………………….….50
4.6.1.3 Расчет третей секции……………………………………….….….52
4.6.1.4 Расчет четвертой секции…………………………………….…….53
4.6.1.5 Расчет пятой секции………………………………………………54
4.6.2 Материальный баланс реактора……………………………….……55
4.6.3 Объем отстойной зоны реактора……………………………………56
4.6.4 Объем реактора…………………………………….…………..…….56
4.6.5 Тепловой баланс реактора………………………………………….57
4.6.6 Расчет сырьевого насоса……………………………….………..….57
4.7 Прочностной расчет………………………………………..………….58
4.7.1 Расчет рубашки…………………….………………….….…………58
4.7.2 Расчет толщины обечаек……………………….…………….……..58
4.7.3 Расчет толщины днища………………………….………..…………59
4.7.4 Расчет изоляции аппарата……………………….……..……………59
4.7.5 Подбор штуцеров……………………………….……………………60
4.7.6 Расчет размеров опоры аппарата…………….…….……………….60
4.8 Автоматизация и управление процессом…………………………….61
5 Финансовый менеджмент, ресурсоэффективность и
ресурсосбережение……………………………………………………………………………………63
5.1 Потенциальные потребителиS результатов Sисследования……….64
5.2 Анализ конкурентных техническихS решений с позиции
ресурсоэффективности и ресурсосбережения………………….………………66
5.3 SWOT-анализ………………………………………………………….68
5.4 Цели и результат проекта…………………………………………….72
5.5 Организационная структура проекта………………………………..73
5.6 Бюджет научного исследования……………………………………..76
5.6.1 Сырье, материалы, покупные изделия и полуфабрикаты………..77
5.6.2 Специальное оборудование для научных работ…………………..77
5.6.3 Основная заработная плата…………………………………………78
5.6.4 Отчисления на социальные нужды…………………………………79
5.6.5 Накладные расходы…………………………………………………80
5.7 Реестр рисков проекта…………………………………………………81
5.8 Оценка сравнительной эффективности
исследования…………………………………………………………………..…82
6 Социальная ответственность……………………………………………85
Введение…………………….……………………………………………..85
6.1 Правовые и организационные вопросы обеспечения
безопасности……………………………………………………………………..85
6.2 Производственная безопасность……………………………………..88
6.2.1 Анализ вредных и опасных факторов, которые может создать
объект исследования……………………………………………………………..88
6.3 Отклонение показателей микроклимата в помещении……………..90
6.4 Повышенный уровень шума………………………………………….91
6.5 Повышенный уровень вибрации……………………………………..92
6.6 Недостаточная освещенность рабочей зоны…………………………92
6.7 Выявление опасных факторов в научно-исследовательской
лаборатории (при разработке и эксплуатации научного исследования)….….93
6.7.1 Пожарная безопасность……………………………………………..93
6.7.2 Термические опасности……………………………………………..96
6.7.3 Электробезопасность ……………………………………………….96
6.8 Требования к обеспечению взрывобезопасности технических
процессов…………………………………………………………………………98
6.9 Экологическая безопасность……………………………………..…100
6.10 Безопасность в чрезвычайных ситуациях………….…………….100
Заключение ………………………………………………………………102
Список публикаций студента……………………………………..……104
Список литературы………………………………………………..……..108
Дизельное топливо – один из самых востребованных нефтепродуктов на
мировом рынке; по прогнозам ОПЕК, доля транспортных средств, которые
используют дизельный двигатель, достигнет 45 % к 2021 году. Производство
его растет, на территории России с 2010 по 2017 год количество потребляемого
дизельного топлива достигло 76,831 млн.т [1]. Спрос на дизельное топливо
особенно высок на европейском и азиатском рынках. Рост экспорта в эти
страны сдерживает несоответствие качества дизельного топлива
экологическим требованиям, предъявляемым на этих территориях.
Содержание ароматических углеводородов в дизельном топливе жестко
контролируется, так как именно эта группа соединений ответственна за
большую часть несгорающих и твердых частиц в отработавших газах
дизельных двигателей [2, 3]. Особое внимание уделяют содержанию
полициклических углеводородов, так как они оказывают токсическое
воздействие. Содержание серы и азота, как нежелательных компонентов,
регламентируется ТР ТС 013/2011 от 18.10.2011 №826.
Содержание СС в дизельной фракции составляет от 0.02 до 2.00 %мас.
Существует условное деление на активные и неактивные соединения. К
активным сернистым соединениям относятся свободная сера, меркаптаны и
сероводород, которые вызывают коррозию при контакте с металлом. Их
наличие в нефтепродуктах не допустимо. Неактивные соединения
представлены сульфидами, дисульфидами, тиофеном и их производными и
составляют 70-80 % от общей массы соединений серы. Установлено, что
любые сернистые соединения в дизельном топливе при попадании в ДВС
становятся активными и, как следствие, вызывают коррозию
цилиндропоршневой группы [4]. СС отравляют катализаторы в процессе
переработки дизельного топлива, переходят в сернистый ангидрид при
окислении дизельного топлива и отравляют окружающую среду.
Кроме СС дизельная фракция содержит соединения азота,
представленные производными хинолина, индола, пиридина и карбазола [5].
Данная группа соединений оказывает отравляющее воздействие на
катализаторы ГО топлива [6]. Содержание азота в дизельной фракции
составляет от 0.01-0.03% мас.
Для достижения содержания серы менее 10 ppm требуется
реконструкция традиционного процесса ГО, которая позволит повысить
степень конверсии СС. Для этого нужно увеличение время контакта и расхода
водорода, использование дорогостоящих катализаторов [2]. Потребление
водорода увеличивается с «утяжелением» прямогонных дизельных фракций.
Отработанный катализатор ГО представляет собой твердые отходы при
утилизации которых происходят выбросы углекислого газа. Перечисленные
факторы подтверждают необходимость разработки более стабильной
технологии облагораживания дизельного топлива, способной повысить
эффективность ГО [7].
Перспективной технологией, позволяющей снизить стоимость
производства дизельного топлива с низким содержанием СС, является процесс
ОО. Экономическая целесообразность его применения зависит от состава
сырья и параметров проведения процесса [8]. Технология ОО является
альтернативой традиционной технологии гидродесульфаризации и
предполагает отказ от водорода и снижение капитальных затрат. При
проведении данного процесса с относительной легкостью происходит
разделение углеводородной части и продуктов окисления СС. Высокий
потенциал метода связан с высоким уровнем десульфуризации и
экономически ценными образующимися сульфоксидами и сульфонами.
Наиболее популярным окислительным агентом является пероксид водорода,
он является дешевым, экологичным и коммерчески доступным.
Достоинством процесса ОО перекисью водорода и муравьиной кислотой
по сравнению с каталитической ГО в том, что трудно десульфируемые
производные дибензтиофена легко окисляются при давлении 101,3 кПа и
температуре не выше 100 °С до образования продуктов окисления, которые
легко отделяются от дизельной фракции экстракцией или адсорбцией.
В большинстве работ по ОО представлены результаты окисления
модельных смесей с использованием различных окислительных агентов, что
не позволяет полноценно исследовать изменение группового и компонентного
состава дизельной фракции [9-16].
Актуальной является задача исследования процесса ОО для дизельных
фракций различного происхождения, а том числе в сочетании с ГО с целью
повышения эффективности обессеривания.
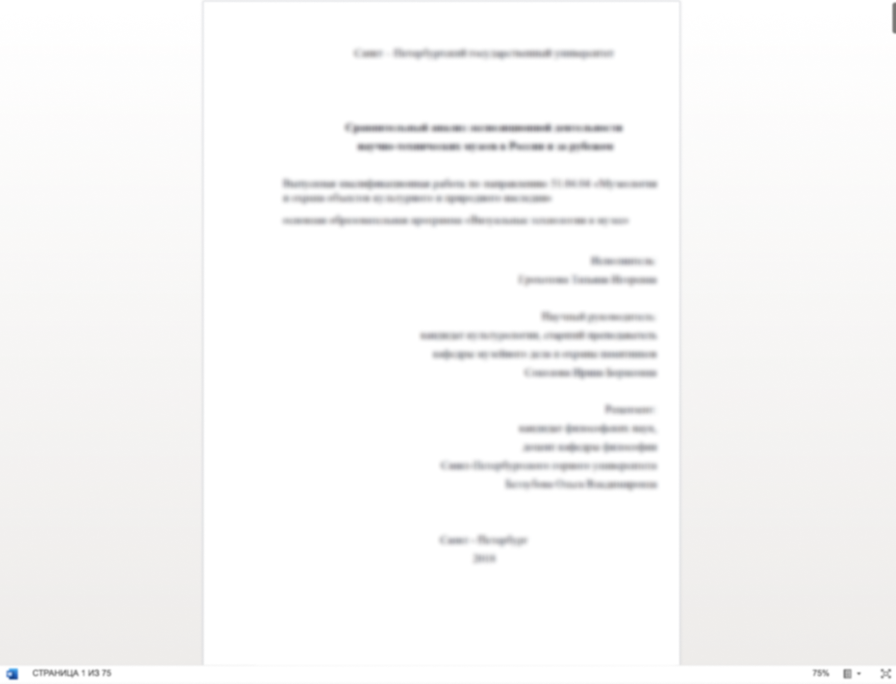
Хочешь уникальную работу?
Больше 3 000 экспертов уже готовы начать работу над твоим проектом!