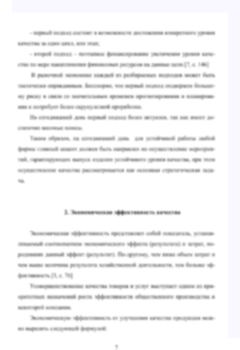
Разработка высокопроизводительного устройства размагничивания длинномерных изделий.
Работа посвящена разработке устройства размагничивания, реализующее метод, основанный на использовании постоянного магнитного поля, корректируемого по измеряемым в процессе размагничивания начальной и остаточной намагниченностям, является наиболее приемлемым при поточном контроле изделий, либо конвейерном размагничивании, из-за высокого быстродействия, низкого энергопотребления и достаточно высокого качества размагничивания. После проведения размагничивания остаточная намагниченность находится в рамках не препятствующих проведению сварки (менее 0,01 Тл), и не вызывает налипания ферромагнитных частиц более 0,1 мм.
Введение ……………………………………………………………………………………………………… 11
1 Размагничивание. Способы размагничивания ферромагнитных изделий ……. 13
2 Методы размагничивания………………………………………………………………………………………………. 19
2.1 Нагрев до температуры точки Кюри ……………………………………………………….. 19
2.2 Размагничивание знакопеременным магнитным полем с убывающей до нуля
амплитудой …………………………………………………………………………………………………. 22
2.2.1 Практические конструкции установок и устройств для размагничивания
ферромегнитных сталей ………………………………………………………………………………. 25
2.2.2 Автоматические устройства размагничивания ………………………………….. 26
2.2.2.1 Демагнетизатор DS10M ……………………………………………………………………. 26
2.3 Размагничивание в постоянных магнитных полях обратной полярности …. 29
2.3.1 Демагнетизатор ДМ – 404 …………………………………………………………………….. 31
2.4 Комбинированный метод размагничивания…………………………………………….. 32
2.4.1 Устройства размагничивания FOERSTER EMAG M/EMAG F ……………… 32
3 Рекомендации по применению методов …………………………………………………….. 33
4 Экспериментальные исследования…………………………………………………………….. 34
4.1 Получение опытных данных для построения петель гистерезиса …………….. 34
5 Разработка принципиальной схемы …………………………………………………………… 38
5.1 Рассчет индукционной обмотки ……………………………………………………………… 38
5.2 Рассчет фильтра высоких частот …………………………………………………………….. 39
5.3 Выбор АЦП ……………………………………………………………………………………………. 39
5.4 Выбор микроконтроллера ………………………………………………………………………. 42
5.5 Рассчет обмотки намагничивания …………………………………………………………… 44
5.6 Расчет усилителя мощности …………………………………………………………………… 46
5.7 Выбор и подключение ЦАП……………………………………………………………………. 47
5.8 Выбор схемы индикации ………………………………………………………………………… 48
5.9 Построение связи микропроцессором с ПК …………………………………………….. 50
6 Финансовый менеджмент, ресурсоэффективность и ресурсосбережение……. 54
6.1 Введение ………………………………………………………………………………………………… 54
6.2 Анализ конкурентных технических решений с позиции
ресурсоэффективности и ресурсосбережения……………………………………………….. 56
6.3 SWOT – анализ ……………………………………………………………………………………….. 59
6.4 План проекта ………………………………………………………………………………………….. 64
6.5 Бюджет научного исследования ……………………………………………………………… 66
6.5.1 Основная заработная плата ………………………………………………………………….. 68
6.5.2 Дополнительная заработная плата научно – производственного персонала
……………………………………………………………………………………………………………………. 71
6.6 Отчисления на социальные нужды …………………………………………………………. 72
6.7 Оплата работ, выполняемых сторонними организациями и предприятиями72
6.8 Накладные расходы………………………………………………………………………………… 73
6.9 Выводы по разделу…………………………………………………………………………………. 74
7 Социальная ответственность …………………………………………………………………….. 77
7.1 Введение ………………………………………………………………………………………………… 77
7.2 Производственная безопасность……………………………………………………………… 77
7.2.1 Анализ выявленных вредных факторов, возникающих при работе с
устройством ………………………………………………………………………………………………… 78
7.2.2 Анализ опасных факторов производственной среды………………………………81
7.3 Экологическая безопасность …………………………………………………………………… 83
7.4 Безопасность в чрезвычайных ситуациях ………………………………………………… 84
7.5 Правовые и организационные мероприятия обеспечения безопасности …… 85
7.5.1 Специальные (характерные для рабочей зоны исследователя) правовые
нормы трудового законодательства ……………………………………………………………… 85
7.5.2 Организационные мероприятия при компоновке рабочей зоны
исследователя ……………………………………………………………………………………………… 86
Заключение …………………………………………………………………………………………………. 88
Список публикаций студента ……………………………………………………………………….. 89
Список использованных источников ……………………………………………………………. 90
Приложение А ……………………………………………………………………………………………. 95
Приложение Б ……………………………………………………………………………………………. 113
«При осуществлении магнитного и вихретокового контроля изделий из
ферромагнитных материалов, как правило, применяется их намагничивание до
состояния близкого техническому насыщению. В первом случае эта операция
относится к числу основных для данного вида контроля, во втором –
осуществляется как вспомогательная для уменьшения влияния магнитных
неоднородностей на результаты контроля. Намагничивание изделий может
также произойти в результате сварочных работ, механической обработки,
использовании электромагнитов для перемещения или фиксации деталей и т.п.
При дуговой сварке конструкций из высокопрочных сталей нередко
наблюдается случаи возникновения «магнитного дутья». Оно является
следствием существования значительных магнитных полей в конструкциях и
нарушает стабильность процесса сварки, увеличивает разбрызгивание
электродного металла, ухудшает формирование шва»[1]. Известны случаи,
когда уровни магнитных полей столь велики, что процесс сварки становится
невозможным вследствие «сдувания» дуги и выброса жидкого металла
сварочной ванны. Опыт показывает, что швы, сварка которых сопровождалась
«магнитным дутьем», как правило, содержат дефекты, и в дальнейшем
необходима повторная заварка таких швов[2].
Магнитные поля в изделиях существенно усложняют и процесс
электроннолучевой сварки, отводя пучок электронов от места сварки или делая
его неуправляемым.
В то же время установлено, что максимальные значения индукции на
открытых кромках некоторых конструкций из высокопрочных сталей могут
достигать 0,01…0,017 Тл, а после сборки отдельных элементов под сварку, в
результате наложения магнитных полей, индукция в зазорах увеличивается в 5
– 10 раз и может превышать 0,1 Тл [5]. Сварка таких конструкций без
применения специальных средств уменьшающих воздействие магнитных
полей, практически невозможна.
Во всех случаях для дальнейшего использования изделия требуется их
размагничивание поскольку повышенная остаточная намагниченность может
вызвать нарушение нормальных условий работы близкорасположенных
приборов, повышенный износ трущихся намагниченных деталей из-за
налипания на их поверхность ферромагнитных частиц, препятствовать
проведению последующих технологический операций, таких как сборка
деталей в узлы, сварка, механическая обработка. Необходимость
размагничивания особенно актуальна для изделий из легированных сталей,
характеризующихся высокими значениями остаточной магнитной индукции и
коэрцитивной силы.
Необходимость размагничивания изделий, создания устройств и
методов, позволяющих его осуществить, появилась еще в 40-е годы при
разработке оборудования для магнитной дефектоскопии [6].
Достаточно размагниченными считались изделия, магнитное состояние
которых не приводило к нежелательным последствиям: искажению в работе
оборудования и приборов, интенсивному прилипанию опилок и т.д. В
большинстве случаев такие последствия не наблюдались при размагничивании
до (0,5…1,0)∙10−2 Тл.
В связи с развитием и широким внедрением электроннолучевой сварки,
повышением требований к качеству соединений потребовалось
размагничивание изделий до (1…5)∙10−4 Тл [3].
Новые высокопрочные конструкционные стали, выпуск которых
непрерывно растет, по магнитным свойствам следует отнести к магнитно –
жестким, коэрцитивная сила которых ≥8∙103 A/м. Повышенная
энерговооруженность производства с использованием различных
электротехнических устройств увеличивает вероятность неконтролируемого
трудно устранимого намагничивания заготовок из таких сталей при операциях
плазменной резки, механической обработки, наложения прихваток,
транспортировки и в условиях хранения на складах.
Существующие методы и средства промышленного размагничивания не
ориентированы на нужды конвейерного размагничивания изделий, что
приводит к их непригодности к встраиванию в транспортные рольганги
технологических потоков дефектоскопов. Основным критерием в этом случае
является низкая производительность демагнетизаторов. При скорости
вихретоковых дефектоскопов 2 – 6 м/c промышленные устройства
размагничивания имеют скорость не выше 1,5 м/c.
В данной работе будет представлен метод высокопроизводительного
размагничивания длинномерных цилиндрических изделий, показаны его
технологические возможности, преимущества и недостатки.
1 Размагничивание. Способы размагничивания ферромагнитных
изделий
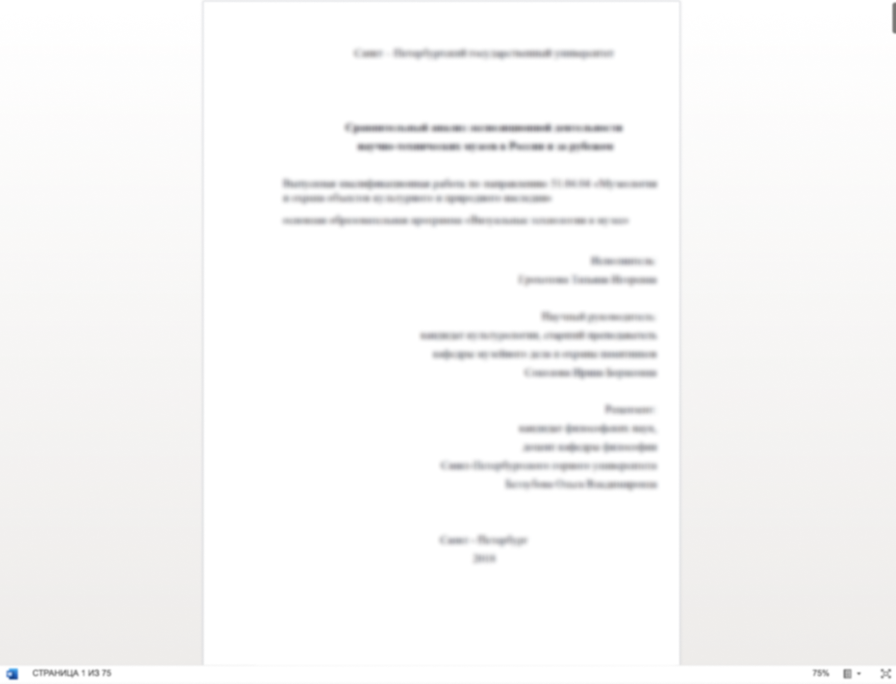
Хочешь уникальную работу?
Больше 3 000 экспертов уже готовы начать работу над твоим проектом!