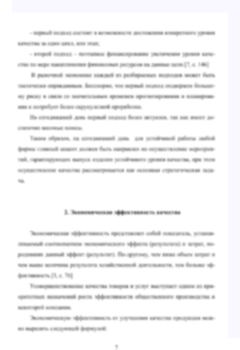
Влияние давления прессования на структуру и свойства спеченных изделий из порошковой смеси системы Fe-C-Cr
Цель работы – Исследовать влияние давления прессования на структуру и свойства спеченных изделий из порошковой смеси системы Fe-C-Cr.
В работе проводили подготовку поверхности образца (шлифовкой, полировкой, травлением), металлографический и рентгеноструктурный анализ, оценку пористости, расчет размер зерна, а также была измерена усадка, плотность и микротвердость.
Введение ……………………………………………………………………………………………………… 10
1 Порошковая металлургия ………………………………………………………………………….. 11
1.1 Этапы технологии порошковой металлургии ………………………………………….. 12
1.2 Преимущества порошковой металлургии ……………………………………………….. 13
1.3 Недостатки порошковой металлургии …………………………………………………….. 14
1.4 Получение порошков ……………………………………………………………………………… 14
1.5 Формование порошков (прессование) …………………………………………………….. 17
1.6 Режимы спекания порошков …………………………………………………………………… 21
1.7 Применение порошковых материалов …………………………………………………….. 23
2.1 Материалы исследований ……………………………………………………………………….. 25
2.2 Методики исследований …………………………………………………………………………. 25
2.2.1 Изготовление образцов ………………………………………………………………….. 25
2.2.2 Подготовка поверхности образцов для металлографических
исследований (шлифовка, полировка, травление) …………………………………… 27
2.2.3 Металлографические исследования ………………………………………………… 28
2.2.4 Определение пористости образца …………………………………………………… 29
2.2.5 Определение фазового состава образца ………………………………………….. 30
2.2.6 Измерение микротвердости ……………………………………………………………. 31
3. Исследование образцов порошковой стали 20Х13 …………………………………….. 33
3.1 Измерение образца …………………………………………………………………………………. 33
3.1.1 Измерение образца после прессования …………………………………………… 33
3.1.2 Измерение образца после спекания ………………………………………………… 35
3.2 Определение пористости для образцов с разным давлением прессования .. 37
3.3 Исследование структуры образцов после спекания …………………………………. 42
3.3.1 Определение фазового состава спеченных образцов ……………………….. 42
3.3.2Металлографический анализ образцов после спекания ……………………. 43
3.4 Рентгенофазовый анализ спеченных образцов 20Х13 ……………………………… 48
3.5 Определение микротвердости…………………………………………………………………. 51
3.6 Результаты проведенного исследования …………………………………………………. 52
4. Финансовый менеджмент, ресурсоэффективность и ресурсосбережение …… 56
4.1. Планирование научно-исследовательских работ…………………………………….. 57
4.1.1 Структура работ в рамках научного исследования ………………………….. 57
4.1.2 Определение трудоемкости выполнения работ ………………………………. 59
4.2 Бюджет научно-технического исследования ………………………………………….. 63
4.2.1 Расчет материальных затрат НТИ …………………………………………………… 63
4.2.2 Основная заработная плата исполнителей темы ……………………………… 65
4.2.3 Расчет затрат на социальный налог ………………………………………………… 68
4.2.4 Расчет амортизационных расходов …………………………………………………. 68
4.2.5 Расчет затрат на электроэнергию ……………………………………………………. 69
4.2.6 Расчет прочих расходов …………………………………………………………………. 70
4.2.7 Расчет общей себестоимости разработки ………………………………………… 70
4.2.8 Расчет прибыли ……………………………………………………………………………… 71
4.2.9 Расчет НДС ……………………………………………………………………………………. 72
4.2.10 Цена разработки НИР …………………………………………………………………… 72
4.3 Определение ресурсной (ресурсосберегающей), финансовой, бюджетной,
социальной и экономической эффективности исследования …………………………. 72
5. Социальная ответственность ……………………………………………………………………. 77
5.1 Техногенная безопасность………………………………………………………………………. 77
5.1.1 Анализ опасных факторов производственной среды……………………….. 77
5.1.2 Анализ вредных факторов производственной среды……………………….. 78
5.2. Региональная безопасность ……………………………………………………………………. 82
5.2.1 Защита атмосферы …………………………………………………………………………. 82
5.2.2 Защита гидросферы ……………………………………………………………………….. 82
5.2.3 Защита литосферы …………………………………………………………………………. 83
5.3. Организационные мероприятия обеспечения безопасности ……………………. 83
5.3.1 Техника безопасности при работе с нагревательными электропечами и
проведении термической обработки ……………………………………………………….. 85
5.3.2 Электробезопасность ……………………………………………………………………… 85
5.3.3 Одежда и средства индивидуальной защиты …………………………………… 86
5.4. Безопасность в чрезвычайных ситуациях ……………………………………………….. 88
5.5. Особенности законодательного регулирования проектных решений ………. 90
Заключение …………………………………………………………………………………………………. 91
Список литературы: …………………………………………………………………………………….. 93
Порошковая металлургия представляет собой науку, охватывающая
разные методы изготовления металлических порошков, разных соединений,
сплавов, полуфабрикатов и всевозможных изделий из смесей порошков.
Производство компонентов с помощью порошковой металлургии имеет
много потенциальных преимуществ по сравнению с их производством с
использованием обычных методов Некоторые из этих преимуществ
включают:
– изготовление большинства тугоплавких металлов и их соединений,
сложные сплавы, пористые материалы могут быть изготовлены только
методом порошковой металлургии;
-порошковая металлургия представляет собой процесс
формообразования с возможностью изготовления точных размеров;
– получение материалов с минимумом примесей, с точным химическим
составом.
Недостатки и ограничения порошковой металлургии для производства
деталей включают:
– высокая стоимость на производство порошков;
– инструмент и оборудование, требуемые для порошковой металлургии,
очень дороги, поэтому становится основной проблемой при низкой
производственной мощности;
– трудно производить крупные и сложные детали по порошковой
технологии.
Порошковая металлургия является начальной ступенью для новых
современных технологий, например, инжекционное формование изделий.
Данная работа посвящена исследованию спеченных образцов из стали
20Х13, полученных из отдельных порошков при разном давлении.
1 Порошковая металлургия
Порошковая металлургия (ПМ) представляет собой
металлообрабатывающий процесс для формирования прецизионных
металлических изделий из металлических порошков. Металлический порошок
сначала прессуют в форму продукта при комнатной температуре. За этим
следует нагрев в печи с контролируемой атмосферой (спекание), который
заставляет частицы порошка сплавляться вместе без плавления.Еѐ имеет
высокоточная формообразующая способность. Можно позволять изготовлять
детали со сложными характеристиками и точными размерами, имеющий
точный химический состав, часто процесс изготовления детали заканчивается
без необходимости механической обработки. Стоимость производства изделия
заданной формы и требуемых допусков на размеры для ПМ обычно ниже, чем
стоимость литья или делает ее как кованый продукт брагодаря чрезвычайно
низкому количеству отходов и меньшему количеству этапов обработки.
Преимущество в затратах является основной причиной выбора ПM в качестве
производственного технологии. Несмотря на то, что этот процесс существует
уже более 100 лет, за последние 25 лет он широко рассматривался как
превосходный способ производства высококачественных деталей для самых
различных применений. Изделия, производимые ПМ, обладают достаточными
физико-механическими свойствами, полностью удовлетворяя функциональным
характеристикам. Производя изделия с однородной структурой, ПМ позволяет
производителям производить продукты, которые являются более
последовательными и предсказуемыми в своем свойстве при разном
применении. Кроме того, ПМ обладает высокой степенью гибкости, позволяя
адаптировать физические характеристики продукта в соответствии с вашими
конкретными характеристиками и требованиями к производительности. К ним
относятся:
– конструктивные изделия со сложными формами;
– управляемая пористость;
– контролируемая производительность;
– специальные свойства, такие как твердость и износостойкость;
– отличная точность и хорошая отделка поверхности;
– большая серия деталей с узкими допусками;
Уникальная гибкость ПМ позволяет изготавливать изделия из
материалов, которые соответствуют вашим потребностям. Благодаря
использованию специально подобранных материалов эта возможность
позволяет уточнить механические свойстваизделия[1, 2].
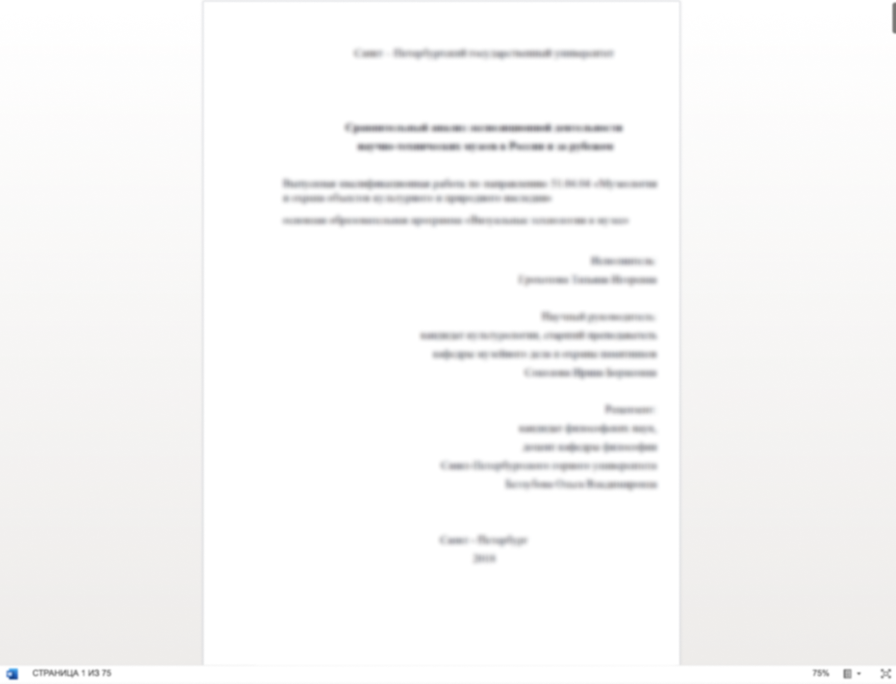
Хочешь уникальную работу?
Больше 3 000 экспертов уже готовы начать работу над твоим проектом!