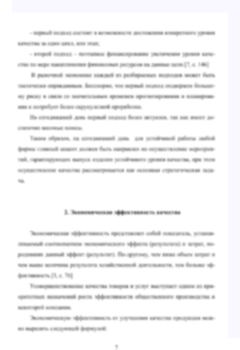
Акустический контроль геометрических параметров паллет
ВВЕДЕНИЕ ……………………………………………………………………………………………….. 4
ГЛАВА 1 КОНТРОЛЬ ГЕОМЕТРИЧЕСКИХ ПАРАМЕТРОВ ПАЛЛЕТ ………. 11
1.1 Характеристики объекта контроля…………………………………………………………… 11
1.2 Анализ методов контроля геометрических параметров паллет…………………. 20
1.3 Приборы контроля геометрических параметров паллет …………………………… 21
1.3.1 Автоматическая система контроля качества поддонов OCME ……………. 21
1.3.2 Система проверки пустых поддонов………………………………………………….. 25
1.3.3 Лазерный сканер повреждений………………………………………………………….. 27
1.4 Ультразвуковой контроль геометрических параметров паллет ………………… 29
1.4.1 Повышение точности при использовании различного порогового
напряжения …………………………………………………………………………………………………….. 35
1.4.2 Определение временной координаты начала эхо-сигнала определением
координат экстремумов первых периодов………………………………………………………… 38
1.4.3 Применение фазового метода для определения временного положения
акустического импульса ………………………………………………………………………………….. 40
1.4.4 Корреляционная обработка принятого сигнала ………………………………….. 43
1.4.5 Двухчастотный способ зондирования объекта контроля ……………………. 44
ГЛАВА 2 ТЕОРЕТИЧЕСКОЕ ИССЛЕДОВАНИЕ ДВУХЧАСТОТНОГО
СПОСОБА ЗОНДИРОВАНИЯ С ФАЗОВОЙ КОРРЕКЦИЕЙ ………………………. 47
2.1 Способ двухчастотного зондирования с фазовой коррекцией ……………………… 47
2.2 Теоретическое исследование способа двухчастотного зондирования с фазовой
коррекцией ……………………………………………………………………………………………………… 54
2.2.1 Описание математической модели…………………………………………………….. 58
2.2.2 Исследование влияния соотношения частот на точность определения
расстояния ………………………………………………………………………………………………………. 65
2.2.3 Исследование влияния порогового напряжения и измеряемого
расстояния на точностные характеристики способа …………………………………………. 74
2.3 Детектирование фазы сигнала при двухчастотном зондировании объекта
контроля …………………………………………………………………………………………………………. 78
ГЛАВА 3 ЭКСПЕРИМЕНТАЛЬНЫЕ ИССЛЕДОВАНИЯ ……………………………. 90
3.1 Экспериментальная установка ……………………………………………………………………. 90
3.2 Программный интерфейс дефектоскопа ……………………………………………………… 99
3.3 Расчет концентратора ………………………………………………………………………………. 105
3.4 Алгоритм реконструкции поверхности паллеты ……………………………………….. 114
ЗАКЛЮЧЕНИЕ ………………………………………………………………………………………. 125
СПИСОК ИСПОЛЬЗОВАННЫХ ИСТОЧНИКОВ …………………………………….. 127
ПРИЛОЖЕНИЕ А. АКТ ВНЕДРЕНИЯ РЕЗУЛЬТАТОВ ДИССЕРТАЦИОННОЙ
РАБОТЫ ………………………………………………………………………………………………… 141
ПРИЛОЖЕНИЕ Б. АКТ ВНЕДРЕНИЯ РАЗРАБОТКИ В УЧЕБНЫЙ ПРОЦЕСС
ТПУ ……………………………………………………………………………………………………….. 142
Актуальность
В наше время трудно представить предприятие массового производства
продукции, которое обходятся без транспортировочной и упаковочной тары.
Произведенную продукцию необходимо куда-то складировать, транспортировать
непосредственно к потребителю или к месту торговой точки. Чтобы обеспечить
сохранность транспортируемого товара от повреждений и потерь, его необходимо
правильно уложить, надежно закрепить и аккуратно довезти до места назначения.
Использование унифицированных поддонов для упаковки продукции,
обеспечивает сохранность товара, увеличивает удобство погрузочно-
разгрузочных работ, тем самым позволяет сократить затрачиваемое на это время.
Кроме того, компактное размещение продукции уменьшает занимаемую площадь
складского помещения. Деревянные поддоны являются многооборотной тарой,
т.е. могут использоваться неоднократно для перевозки, как тяжелых
малогабаритных грузов, так и крупногабаритных. Во время перемещения груза
паллеты могут быть повреждены в той или иной степени, что может привезти к
необратимой порче произведенного товара. Нарушение геометрических
параметров паллет приводит к отклонению в работе устройства автоматической
укладки выпускаемой продукции, при этом для устранения аварийной ситуации
необходим некоторый период время, что приводит к увеличению простоев и
издержек производства, что влечет за собой рост себестоимости продукции [1].
Выявление дефектов (целостность конструктивных элементов, отсутствие
посторонних предметов, трещин, сколов и т.п) с последующей комплексной
оценкой качества паллет и оперативное принятие верного решения для их
устранения с конвейерной ленты представляют собой сложнейшую задачу для
оператора.
Разработка нового оборудования для оперативного определения дефектной
транспортировочной тары позволит осуществлять отбор поддонов без каких-либо
повреждений и отклонений от нормы, что в свою очередь приведет к снижению
себестоимости выпускаемой продукции.
Целью диссертационной работы является разработка программно-аппаратного
В диссертации сформулированы и обоснованы основные принципы реализации
двухчастотного способа зондирования с фазовой коррекцией для задач
неразрушающего контроля геометрических параметров паллет.
Предложенный способ двухчастотного зондирования с фазовой коррекцией
позволяет получить погрешность определения временной координаты эхо-
сигнала менее 1%.
Проведенные исследования выявили основной источник высокой
погрешности контроля при двухчастотном зондировании, заключающийся в
срабатывании порогового устройства в разных периодах эхо-сигналов на двух
частотах. В диссертационной работе предложен способ определения номеров
периодов срабатывании порогового устройства и последующей корректировки
временной координаты срабатывания порогового устройства, который позволил
получить погрешность контроля менее 0,5%.
Для анализа возможностей двухчастотного способа зондирования с фазовой
коррекцией разработан программный комплекс, позволяющий моделировать
акустический тракт при изменении параметров зондирования, акустического
тракта и порогового устройства, что позволяет определять оптимальные
параметры дефектоскопа.
На основе созданной модели были исследованы метрологические
характеристики дефектоскопа в широком диапазоне изменения частот
зондирования и их соотношения. Показано, что для получения минимальной
погрешности контроля следует выбирать соотношение частот зондирования не
более 1,3. Однако при использовании алгоритма определения номеров периодов
срабатывании порогового устройства это ограничение становится
несущественным.
Важным моментом диссертационной работы является исследование
влияния параметров эхо-импульсов на результат контроля. Выявлено, что для
получения минимальной погрешности контроля необходимо обеспечить
одинаковую амплитуду и форму огибающей переднего фронта эхо-сигналов.
По результатам проведенных исследований был разработан программно-
аппаратный комплекс для контроля геометрических параметров паллет.
Использование двухчастотного способа зондирования с фазовой коррекцией
позволило получить погрешность контроля не более 1 мм. Для обеспечения таких
характеристик во всем диапазоне рабочих температур был применен опорный
канал для расчета текущей скорости распространения упругой волны после
контроля каждой паллеты в момент ее отсутствия на конвейере. Использование
антенной решетки в системе контроля позволило применить сканирование только
по одной координате и обеспечить тем самым высокую производительность
контроля.
Проведенные испытания системы контроля показали ее способность
детектировать дефекты различного характера (наличие посторонних предметов,
отсутствие досок паллета, сколов и т.д.).
Практическая эксплуатация разработанной системы контроля показала, что
разработанная система контроля геометрических параметров паллет имеет
достаточно высокую точность, надежность и скорость контроля паллет.
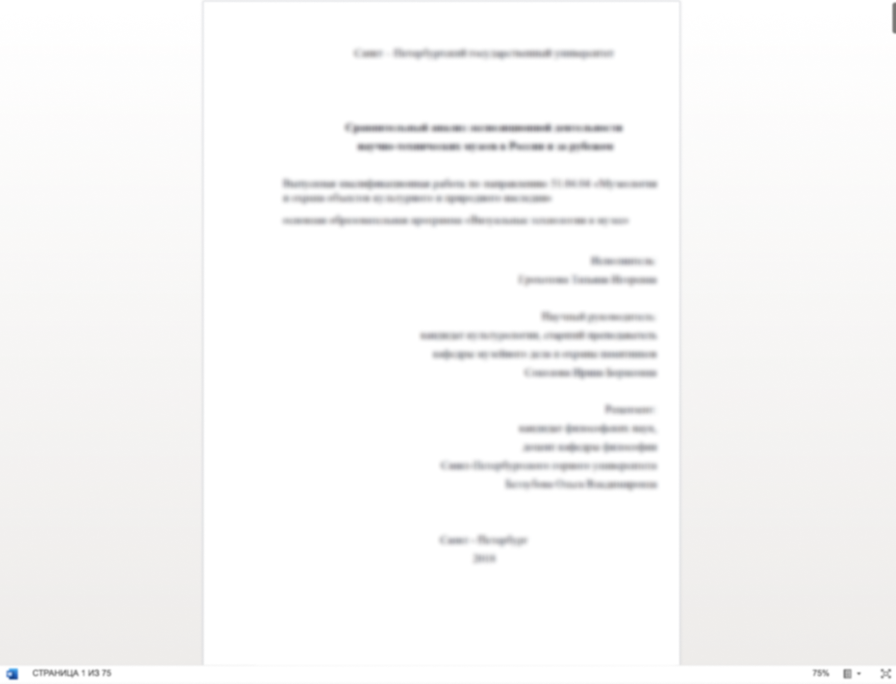
Помогаем с подготовкой сопроводительных документов
Хочешь уникальную работу?
Больше 3 000 экспертов уже готовы начать работу над твоим проектом!