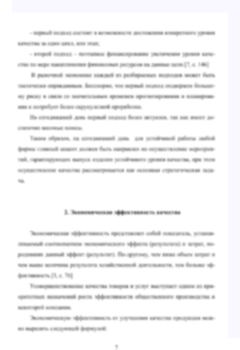
Тепловой вибротермографический контроль композитов с использованием резонансной ультразвуковой и оптической стимуляции
Термины и определения 4
Обозначения и сокращения 5
Введение 8
Глава 1. Обзор современных методов неразрушающего контроля композиционных 15
и полимерных материалов
1.1. Ультразвуковой неразрушающий контроль волоконно-композитных материалов 15
1.1.1 Традиционные ультразвуковые методы НК 15
1.1.2 Ввод ультразвука через воздух 17
1.1.3 Резонансная ультразвуковая спектроскопия 19
1.2. Акустическая эмиссия 20
1.3. Линейная и нелинейная виброметрия 21
1.4. Радиационный контроль 23
1.5. Визуально-оптический контроль 24
1.6. Радиоволновый контроль 24
1.7. Термографические методы неразрушающего контроля 25
1.8. Выводы по Главе 1 25
Глава 2. Развитие метода ультразвукового инфракрасного термографического 27
контроля с использованием магнитострикционного способа возбуждения ультразвука
2.1.Теоретические основы метода 27
2.2. Резюме ранних исследований, выполненных в ТПУ 31
2.3.Развитие магнитострикционного принципа возбуждения ультразвука 32
применительно к задачам неразрушающего контроля
2.3.1 Установка для непрерывной УЗ стимуляции 32
2.3.2 Установка для импульсной УЗ стимуляции 34
2.3.3Тепловизионная система теплового дефектоскопа 35
2.4. Магнитострикционный ультразвуковой инфракрасный дефектоскоп и 35
результаты его применения для обнаружения ударных повреждений в углепластике
2.5. Спектральная характеристика ультразвукового инфракрасного контроля 40
2.6. Модификация компьютерной программы ThermoSource 46
2.6.1. Результаты моделирования термоакустического отклика дефектов в 48
композиционных материалах (на примере углепластика)
2.6.2. Параметры дефектов 53
2.7. Преобразование акустической энергии в тепловую энергию 56
2.8. Выводы по Главе 2 64
Глава 3. Сравнительные экспериментальные исследования инфракрасного 67
термографического контроля композитов при оптической и ультразвуковой
стимуляции (синтез данных)
3.1. «Классический» тепловой контроль при оптической стимуляции 67
3.2. Исследуемые образцы 68
3.3. Контроль ударных повреждений в углепластиковых композитах 70
3.4. Выводы по Главе 3 74
Глава 4. Разработка метода маломощной резонансной стимуляции композитов с 76
регистрацией температурных полей методом инфракрасной термографии
4.1. Резонансная ультразвуковая инфракрасная термография 76
4.2. Аппаратурная база метода 77
4.3. Резонанс дефекта 79
4.4. Теплогенерация в результате резонансных вибраций дефектов 86
4.5. Эффективность резонансной УЗ ИК вибротермографии 96
4.6. Перспективные направления исследований 100
4.7. Сравнение мощной и маломощной УЗ ИК термографии 114
4.8. Выводы по Главе 4 126
Общие выводы 126
Публикации автора 129
Литература 131
Приложение А Теоретический расчет частоты резонанса пластины в области 137
прямоугольного отверстия
Приложение Б Теоретический расчет частоты резонанса пластины в области круглого 145
отверстия
Приложение В Акт использования результатов диссертационных исследований 151
Термины и определения
Инфракрасная термография – совокупность методов и технических средств для
дистанционной регистрации и анализа характеристик тепловых (температурных) полей
объектов по их тепловому (инфракрасному) излучению.
Температурное поле – распределение температуры на участке поверхности
контролируемого объекта.
Ультразвуковой неразрушающий контроль – метод (вид) неразрушающего контроля
материалов и изделий, основанный на исследовании процесса распространения
ультразвуковых колебаний с частотой от 0,5 до 50 МГц в объектах контроля с помощью
специализированного оборудования.
Ультразвуковая инфракрасная термография – совокупность методов и технических
средств для регистрации и анализа изменений температурного поля на поверхности объекта
исследования, возникающих в результате его акустической стимуляции.
Тепловой неразрушающий контроль – метод (вид) неразрушающего контроля
материалов и изделий, основанный на регистрации и анализе изменения температурных
сигналов, полученных в результате регистрации температурного поля на поверхности
объекта контроля.
Лазерная виброметрия – метод измерения скорости и смещения частиц среды на
поверхности объекта в ответ на различные виды возбуждения за счет использования
аппаратуры лазерной допплеровской виброметрии.
Обозначения и сокращения
– температурный сигнал, оС;
∆ – дифференциальный температурный сигнал, оС;
∆ – максимальный дифференциальный температурный сигнал, оС;
– температуропроводность материала, м2/с;
– теплопроводность материала, Вт/(м.К);
– плотность материала, кг/м3;
, – теплоемкость материала, Дж/(кг.К),
– текущее время, с;
с – скорость звука, м/с;
– длина акустической волны, м;
– частота колебаний, Гц;
ω – угловая (циклическая) частота колебаний, рад/с;
– колебательная скорость частиц среды, м/с;
0 – амплитуда колебательной скорости частиц среды, м/с;
– амплитуда колебательной скорости частиц среды в области дефекта, м/с;
– амплитуда колебательной скорости частиц среды в бездефектной зоне, м/с;
– частота резонанса дефекта, Гц;
– коэффициент усиления амплитуды вибраций за счет резонанса дефекта;
– максимальное смещение частиц среды относительно положения равновесия, мм;
Ɛ0 – относительная деформация изделия;
– амплитуда переменного акустического давления, Па;
– интенсивность звука, Вт/м2;
S – площадь поперечной площадки, расположенной перпендикулярно направлению
распространения акустической волны, м2;
эл. – электрическая мощность генератора акустических колебаний, Вт;
ак. – акустическая мощность излучателя, переносимая звуковой волной через поперечную
площадку, расположенную перпендикулярно распространению звука, Вт;
тепл. – тепловая мощность, затраченная на генерацию тепла в объеме материала, Вт;
эа – коэффициент преобразования электрической мощности излучателя в акустическую;
ат – коэффициент преобразования акустической мощности излучателя в тепловую
мощность, рассеиваемую дефектом;
эт – коэффициент преобразования электрической мощности излучателя в тепловую
мощность, рассеиваемую дефектом;
Рпот – потребляемая мощность, Вт;
Рвых – выходная мощность, Вт;
ΔР – шаг дискретизации мощности, Вт;
Uвых – выходное напряжение, В;
fвых – частота генерации УЗ колебаний, кГц;
Iподмагн. – ток подмагничивания, А;
L0 – расстояние между магнитострикционным излучателем и дефектами, мм;
Sпов. – площадь контролируемой поверхности, м2;
ΔTD1 – ΔTD6 – дифференциальное значение температурного сигнала в области дефектов 1-6
, оС;
, , – декартовы координаты, м;
q j – одна из декартовых координат x, y или z, м;
i – количество слоев и источников тепла, т.е. дефектов;
T i – дифференциальный температурный сигнал в i-й области, оС;
Tin – начальная температура изделия, оС;
– температуропроводность в i-ой области по координате , м2/с;
– теплопроводность в i-ой области по координате , Вт/(м.К);
w( x, y,τ ) – плотность мощности источников тепловыделения, Вт/м3;
Q( x, y, τ ) – плотность теплового потока, Вт/м2;
hF , hR – коэффициенты теплообмена на передней и задней поверхностях пластины,
Вт/(м2.К);
Tamb – температура окружающей среды, оС;
, , – геометрические размеры образца, м;
L – толщина изделия, м;
l – глубина залегания дефекта, м;
d – толщина дефекта, м;
V – объем материала, м3;
Q – мощность, затраченная на тепловыделение в области дефекта, мВт;
– эффективная жесткость, Н/м;
– эффективная масса, кг;
– радиус, мм;
– изгибная жесткость пластины, Па×м3;
– модуль Юнга (модуль упругости), Па;
, – коэффициент Пуассона.
УЗ – ультразвуковой
ИК – инфракрасный
ПЭП – пьезоэлектрический преобразователь
ТК – тепловой контроль
ТФХ – теплофизические характеристики
НК – неразрушающий контроль
АЧХ – амплитудно-частотная характеристика
АЭ – акустическая эмиссия
СВЧ – сверхвысокочастотные
УФО – ультразвуковая финишная обработка
ПММА – полиметилметакрилат
Обнаружение и моделирование повреждений материалов, влияющих на качество и
безопасность эксплуатации конструкций, являются взаимозависимыми областями научных
исследований, имеющими самостоятельное научно-техническое значение. В настоящее
время в различных технологических применениях находят все более широкое применение
композиционные материалы, обладающие уникальными свойствами, которые превышают по
свойства традиционно используемых материалов (древесины, стали, сплавов металлов).
Одним из наиболее важных преимуществ этих материалов является возможность их
предварительного проектирования соответственно техническим требованиям конкретного
изделия в определенной области применения, что позволяет организовать индивидуальный
подход к процессу производства материалов и изделий для решения конкретной научной
задачи. Однако, вследствие наличия микроструктурных неоднородностей и дефектов в
структуре композитов, их качество и состояние должны быть оценены и подвергнуты
количественным оценкам для прогнозирования прочности и срока службы как исходных
материалов, так и конкретных изделий. В связи с этим вопросы контроля качества, а также
исследования старения и усталости композиционных материалов приобретают значительную
актуальность.
В настоящее время мировыми научно-исследовательскими центрами разработан ряд
методов неразрушающего контроля материалов и изделий, позволяющих осуществлять
мониторинг развития повреждений в материале на всех стадиях до его полного разрушения в
процессе приложения нагрузки на образец или в ходе старения материала. Таким образом,
реализуется возможность постоянного контроля развития дефектов в различных материалах
при определенных внешних воздействиях и эксплуатационных условиях. Очевидно, что
решение вопроса об окончательной пригодности изделия является следствием непрерывно
наблюдаемого процесса в конкретном образце. После того, как механизмы появления и
развития дефектов материалов были исследованы с помощью неразрушающего контроля
(НК), полученные информативные параметры используют для прогнозирования роста
повреждений или трещин, а также вычисления предельных нагрузок структуры.
Исследование развития дефектов в широком диапазоне волоконно-матричных
(композиционных) структур позволяет проанализировать повреждения и создать общие
модели дефектов, а также выполнить их классификацию. В целом, считается, что
определение срока службы материалов и анализ процессов развития дефектов в них станут
более предсказуемыми и регулируемыми после внедрения в практику вышеописанных
подходов.
Известным фактором актуальности разработки именно тепловых/инфракрасных
методов являются известные недостатки так называемых «традиционных» методов
неразрушающих испытаний применительно к композитам. В частности, анализ зарубежной
литературы позволяет сделать вывод, что тепловой контроль (ТК) в настоящее время
является основным методом испытаний материалов и изделий авиакосмической техники.
Обзор соответствующих исследований был сделан в андидатских диссертациях В.С. Хорева,
И.А. Лариошиной, А.С. Попова и А.О. Чулкова, ранее защищенных в Национальном
исследовательском Томском политехническом университете (ТПУ).
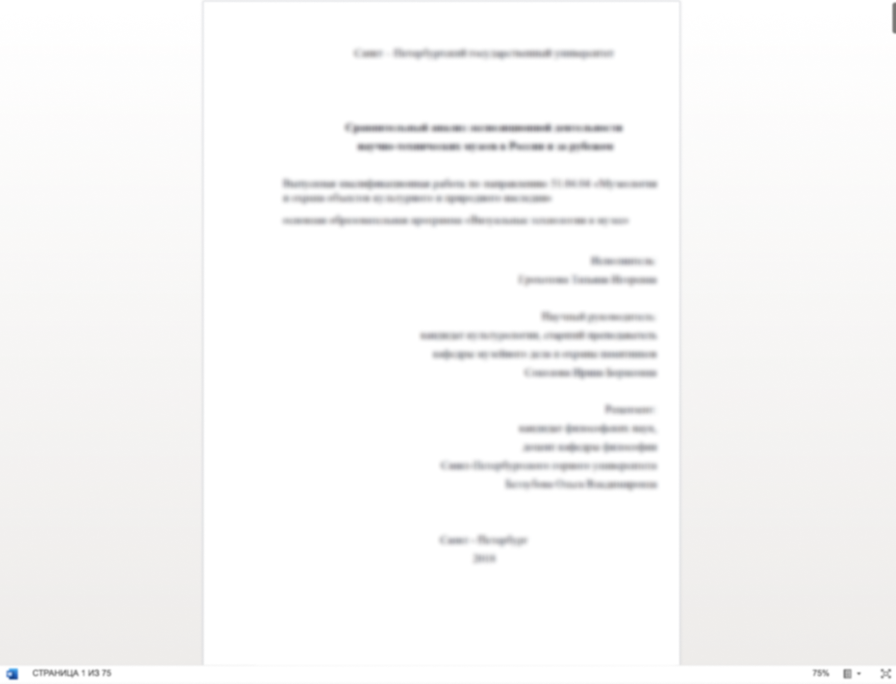
Помогаем с подготовкой сопроводительных документов
Хочешь уникальную работу?
Больше 3 000 экспертов уже готовы начать работу над твоим проектом!