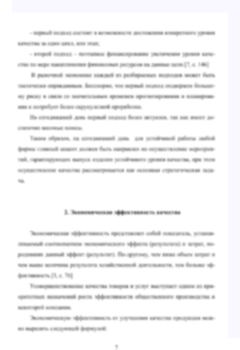
Закономерности формирования активных центров Zn-содержащих цеолитных катализаторов и их роль в процессе превращения легких углеводородов
ВВЕДЕНИЕ ……………………………………………………………………………………………….. 4
Глава 1 Литературный обзор …………………………………………………………………….. 10
1.1 Общие сведения о природном и попутном нефтяном газах: проблемы
утилизации и экологии …………………………………………………………………………….. 10
1.2 Пентасилсодержащие катализаторы для процесса ароматизации
углеводородных газов ………………………………………………………………………………. 15
1.2.1 Химический состав и структура высококремнеземных цеолитов .. 16
1.2.2 Гидротермальный синтез цеолитов ……………………………………………. 21
1.2.3 Изоморфные замещения в решетке цеолита ………………………………. 26
1.3 Ароматизация легких алканов на Zn-содержащих цеолитных
катализаторах …………………………………………………………………………………………… 29
1.3.1 Современные представления о природе активных центров цеолитных
катализаторов…………………………………………………………………………………………… 29
1.3.2 Активация алканов С3-С4 на цеолитных катализаторах ……………… 37
1.4 Современные каталитические процессы и катализаторы для переработки
газообразного углеводородного сырья в ароматические соединения, их
преимущества и недостатки ……………………………………………………………………… 43
Заключение ……………………………………………………………………………………………… 51
Глава 2 Экспериментальная часть …………………………………………………………….. 53
2.1 Методики приготовления катализаторов …………………………………………. 53
2.1.1 Методика синтеза Zn-алюмосиликата ……………………………………….. 53
2.1.2 Получение Zn-алюмосиликата с разной структурообразующей
добавкой ………………………………………………………………………………………………….. 54
2.1.3 Приготовление Zn-алюмосиликата с разным источником
кремния …………………………………………………………………………………………………… 55
2.1.4 Приготовление Zn-алюмосиликата с микро-мезопористой
структурой ……………………………………………………………………………………………….. 55
2.1.5 Методика получения Н-формы Zn-алюмосиликатов ………………….. 56
2.1.6 Характеристика промышленных катализаторов для переработки
газообразного углеводородного сырья в ароматические соединения …………. 56
2.2 Физико-химические методы исследования катализаторов………………… 57
2.3 Исследование процесса превращения пропана на цеолитных
катализаторах …………………………………………………………………………………………… 66
2.3.1 Обработка экспериментальных данных …………………………………….. 70
3.1 Исследование физико-химических свойств цинкалюмосиликатов
структурного типа MFI …………………………………………………………………………….. 72
3.1.1 Влияние концентрации ZnO………………………………………………………. 72
3.1.2 Влияние природы структурообразующей добавки …………………….. 79
3.1.3 Влияние природы источника кремния ……………………………………….. 91
3.1.4 Влияние второго темплата (технического углерода) ………………….. 94
3.2 Превращение пропана на цинкалюмосиликатах структурного
типа MFI ………………………………………………………………………………………………. 98
3.2.1 Влияние концентрации ZnO………………………………………………………. 98
3.1.2 Влияние природы структурообразующей добавки …………………… 101
3.2.3 Влияние природы источника кремния ……………………………………… 111
3.2.4 Влияние второго темплата (технического углерода) ………………… 118
ВЫВОДЫ ………………………………………………………………………………………………. 129
СПИСОК СОКРАЩЕНИЙ И УСЛОВНЫХ ОБОЗНАЧЕНИЙ …………………. 131
СПИСОК ЛИТЕРАТУРЫ……………………………………………………………………….. 132
Во введении обоснована актуальность диссертационной работы, сформулированы цель и задачи исследования, обозначены научная новизна работы и практическая значимость, приведены основные положения, выносимые на защиту.
В первой главе диссертации представлен литературный обзор, посвященный переработке и использованию природного и попутного нефтяного газов. Представлены общие сведения о природных углеводородных газах, рассмотрены проблемы утилизации и экологии. Обобщены данные о современных каталитических процессах и катализаторах для переработки газообразного углеводородного сырья в ароматические соединения. Рассмотрены вопросы синтеза цеолитов типа MFI и их модифицирования с целью повышения каталитической активности и селективности в процессе ароматизации низших алканов. Большое внимание уделено современным представлениям о природе активных центров, Zn-содержащих цеолитных катализаторов и механизму превращения алканов С3-С4 на Zn-содержащих цеолитах.
Во второй главе представлена методическая часть работы, включающая способы приготовления цинксодержащих катализаторов, методы исследования их физико-химических и каталитических свойств.
В качестве объекта исследования выступал цинксодержащий цеолит типа MFI (мольное отношение SiO2/Al2O3 + ZnO = 40, содержание ZnO в реакционной смеси составляло 0,82-2,16 % мас., а Al2O3 – 3,04-1,36 % мас.), полученный методом гидротермальной кристаллизации путем
частичной замены алюминия на цинк (Zn-AC). Источниками оксидов алюминия и цинка служили растворы их азотнокислых солей. В качестве структурообразующих компонентов использовали гексаметилендиамин (ГМДА), бикарбонат аммония (БКА) и бутанол.
Для приготовления Zn-алюмосиликата с разным источником кремния использовали жидкое стекло (ЖС) состава: 7 % Na2O, 19 % SiO2, 74 % H2O, белую сажу БС-100 (БС) и 40 % золь (З) кремниевой кислоты.
Синтез микро-мезопористого цинкалюмосиликата аналогичен синтезу микропористого цеолита, но при этом дополнительно в реакционную смесь добавляется технический углерод марки N660 в количестве 1,0-3,0 % мас.
Для всех Zn-алюмосиликатов были получены их водородные формы. Для проведения испытаний катализаторы прессовали в таблетки, измельчали и отбирали фракцию размером 0,5-1,0 мм.
Качественные показатели синтезируемых образцов Zn-AC контролировали с помощью ИК- спектроскопии (ИКС) и рентгенофазового анализа (РФА). Удельную поверхность Zn-содержащих цеолитов и параметры пористой структуры определяли методом низкотемпературной адсорбции азота. Тестирование кислотных свойств катализаторов проводили методами температурно- программированной десорбции (ТПД) аммиака и ИК-спектроскопии адсорбированных молекул СО. Определение формы и размеров частиц цеолитов проводили с помощью электронного микроскопа SEM LEO-420 с разрешением 15 Å при увеличении от 1000 до 5000. Микроструктуру и состав Zn-содержащих цеолитов исследовали методами просвечивающей электронной микроскопии высокого разрешения (ПЭМВР) и спектроскопии характеристического рентгеновского излучения (EDX). Термические исследования закоксованных катализаторов проводили методом дифференциального термического анализа (ДТА).
Каталитические испытания образцов осуществляли на стендовой установке проточного типа при атмосферном давлении, объемной скорости подачи сырья 250 ч–1 и с варьированием температуры реакции от 450 до 600 °С. Продукты реакции анализировали методом ГЖХ с использованием хроматографа «Хроматэк-Кристалл 5000.2».
В третьей главе приведены результаты исследования физико-химических и каталитических свойств полученных Zn-алюмосиликатов.
Влияние концентрации оксида цинка
Характеристики цинкалюмосиликатов, синтезированных с использованием жидкого стекла и ГМДА, представлены в табл. 1. По данным ИК-спектроскопии все катализаторы имеют структуру цеолита типа MFI и обладают высокой степенью кристалличности. Увеличение содержания цинка в Zn-АС приводит к небольшому снижению степени кристалличности цеолита,
что может быть обусловлено замедлением процесса кристаллизации силикат-ионов в присутствии катионов цинка.
Таблица 1 – Характеристика кристаллических цинкалюмосиликатов
Катализатор
0,82 % Zn-AC 1,89 % Zn-AC 2,16 % Zn-AC
Концентрация, % ZnO Al2O3 0,82 3,04 1,89 1,70 2,16 1,36
Мольное отношение
Степень кристалличности, % 100
86
SiO2/Al2O3 53
120
SiO2/ZnO 160 69
По данным ТЕМ частицы образца 0,82 % Zn-AC имеют глобулярную форму с шероховатостями поверхности и размерами около 5 мкм (рис. 1А). Эта морфология типична для частиц данного образца.
АБВГ
Рисунок 1 – Снимки ТЕМ: А – морфология цеолитового агрегата образца 0,82 % Zn-AC: Б – кристалл цеолита и агрегаты мелких частиц образца 1,89 % Zn-AC; В – агрегированные частицы цеолита в форме эллипсоидов образца 1,89 % Zn-AC; Г – расщепленный край эллипсоидной частицы образца 1,89 % Zn-AC
С увеличением содержания оксида цинка в цинкалюмосиликате наблюдается изменение морфологии частиц и для образца 1,89 % Zn-AC обнаружено присутствие частиц двух видов: 1 – кристаллы цеолита с размерами 1–3 мкм (преобладающая фракция) (рис. 1Б); 2 – поликристаллические частицы в форме вытянутых эллипсоидов с размерами 100 × 500 нм с расщеплением по краям на тонкие фрагменты с толщиной около 20 нм, что указывает на внутреннее микроблочное строение «эллипсоидов» с упорядочением в одномерную текстуру (рис. 1В, Г).
Все исследуемые образцы имеют два типа кислотных центров, о чем свидетельствует наличие двух форм десорбции аммиака на термодесорбционных кривых. Образец 0,82 % Zn-AC обладает наибольшей концентрацией кислотных центров обоих типов, имеющих большую силу по сравнению с другими образцами (табл. 2). При повышении содержания оксида цинка в цинкалюмосиликате до 1,89 % происходит незначительное снижение концентрации слабых и более существенное уменьшение содержания сильных кислотных центров. При дальнейшем повышении концентрации ZnO в цинкалюмосиликате происходит значительное снижение
8
количества кислотных центров обоих типов, что связано с ростом содержания ZnO на поверхности цеолита и увеличением степени его диффузии в каналы цеолита, где происходит взаимодействие с бренстедовскими кислотными центрами. Кроме того, с ростом концентрации оксида цинка в Zn- AC наблюдается уменьшение силы кислотных центров обоих типов, о чем свидетельствует смещение низко- и высокотемпературных пиков в область более низких температур.
Исследования методом низкотемпературной адсорбции азота показали, что наибольшую удельную поверхность и наибольший объем пор имеет образец 0,82 % Zn-AC, при этом он характеризуется наименьшим средним диаметром пор (табл. 2). С ростом содержания цинка в цинкалюмосиликате наблюдается снижение величины удельной поверхности и суммарного объема пор. Так, например, для катализатора 2,16 % Zn-AC величина удельной поверхности составляет 329 м2/г, тогда как для образца 0,82 % Zn-AC она была 393 м2/г.
Таблица 2 – Кислотные и текстурные характеристики цинкалюмосиликатов
Катализатор
0,82 % Zn-AC 1,89 % Zn-AC 2,16 % Zn-AC
Тмакс., оС
ТI ТII 220 450 210 430 170 420
Концентрация, мкмоль/г
СI СII С 529 294 823 489 229 718 392 186 578
Sуд., 2 м /г
393 358 329
Суммарный объем пор, см3/г 0,19 0,18 0,17
Средний диаметр пор, нм 1,8 1,9 2,0
Примечание. ТI, TII, – температуры максимумов низко- и высокотемпературных пиков на термодесорбционных кривых; СI, СII и С – концентрация слабых и сильных кислотных центров и их сумма, соответственно, Sуд. – удельная поверхность.
В табл. 3 представлены данные по влиянию концентрации оксида цинка в цинкалюмосиликате и температуры процесса на конверсию пропана и селективность образования продуктов реакции. Как видно из представленных данных, заметное превращение пропана на исследуемых катализаторах начинается при температуре реакции 450 оС, а при 500 оС и выше происходит существенное образование целевого продукта – ароматических углеводородов, состоящих преимущественно из бензола, толуола и ксилолов (БТК-фракция), в небольших количествах также образуются алкилбензолы С9+, нафталин и алкилнафталины. С ростом температуры процесса происходит увеличение степени превращения пропана и селективности образования ароматических углеводородов, которые при температуре реакции 600 оС на образце 0,82 % Zn-AC достигают соответственно 100 и 40,2 %. Аналогичные зависимости показателей ароматизации пропана от температуры процесса наблюдаются на других Zn-АС.
Таблица 3 – Основные показатели процесса превращения пропана на цинкалюмосиликатах Катализатор Т, оС Х, % YАрУ, % SАрУ, % Sкр, % Sдег,% SН2, %
0,82 % Zn-AC
450
550
40 77 97 100
2,3 22,3 36,5 40,2
5,7 28,8 37,5 40,2
66,7 59,2 54,9 53,4
9,7 7,8 5,2 3,0
1,9 2,0 2,3 3,3
1,89 % Zn-AC
450
550
19 39 84 99
1,8
6,5 26,4 38,8
9,5 16,7 31,4 39,1
57,0 62,3 58,7 54,8
12,0 10,0 4,7 1,9
6,8 7,1 4,4 4,2
2,16 % Zn-AC
450
550
13 36 83 99
1,2
4,7 19,1 35,5
9,6 13,0 23,1 35,7
57,3 67,7 67,2 58,3
10,9 8,7 4,4 1,8
8,1 7,1 5,0 4,3
Примечание. Х – конверсия пропана; YАрУ – выход ароматических углеводородов; SАрУ, Sкр и Sдег – селективность образования продуктов ароматизации, крекинга и дегидрирования; SН2 – селективность образования водорода.
Увеличение концентрации оксида цинка в катализаторе приводит к снижению его ароматизирующей активности и повышению крекирующей. Так, на образце 2,16 % Zn-AC выход ароматических углеводородов при температуре реакции 600 °С уменьшается на 4,7 % по сравнению с их выходом на образце 0,82 % Zn-AC.
Таким образом, наиболее эффективным катализатором данного процесса является образец 0,82 % Zn-AC, селективность образования ароматических углеводородов на котором при 600 оС достигает 40,2 % при полном превращении пропана.
Влияние природы структурообразующей добавки
Несмотря на то, что все члены семейства пентасилов имеют общую вторичную структурную единицу, на формирование их канальной системы и, следовательно, на физико- химические и каталитические свойства цеолитов большое влияние оказывает вид органического соединения, используемого при их синтезе. Роль природы органического компонента в процессе синтеза цеолитов до сих пор является предметом пристального внимания исследователей, так как один и тот же структурный тип цеолитов может быть получен как в присутствии различных структурообразователей, так и без них.
В данном разделе приведены результаты исследований физико-химических и каталитических свойств образца 0,82 % Zn-AC, полученного с использованием в качестве структурообразующих добавок различных соединений (ГМДА, БКА и Бутанола).
На рис. 2 представлены ИК-спектры в области валентных колебаний ОН-групп исследуемых образцов. Наиболее интенсивные сигналы в области 3611-3616 и 3746 см–1 характерны для ИК-спектров цеолитов типа MFI и отнесены к кислым мостиковым Si-O (H) -Al- группам и концевым некислотным Si-OH-группам, соответственно.
Полоса мостиковых групп Si-O (H) -Al для цеолита Zn-АС(Бутанол) асимметрична и содержит два компонента при 3606 и 3616 см–1. Плечи силанольных полос при 3738 и 3725-3730 см–1, вероятно, связаны со слабокислотными силанольными группами, расположенными во внутренних порах, или с дефектными силанольными группами OH, типичными для цеолитов и алюмосиликатов MCM-41.
Другие менее интенсивные полосы в области 3665-3690 см–1 могут быть отнесены к кислотным ОН-группам, присоединенным к трехкоординированным атомам Al, которые частично связаны с каркасом, в то время как сигнал
при 3777 см–1 может быть отнесен к слабокислотным гидроксильным группам. Мостиковые ОН- группы, связанные с атомом цинка, могут вносить вклад в полосу адсорбции при 3675 см–1. Широкая полоса при 3300-3550 см–1 относится к водородосвязанным OH-группам.
На рис. 3 показаны ИК-спектры в области валентных колебаний карбонильных групп СО, адсорбированного при температуре жидкого азота и c увеличением давления. Адсорбция CO на образцах Zn-AC(ГМДА) и Zn-AC(БКА) приводит к появлению следующих полос поглощения: 1 – полосы при 2233, 2225 и 2203 см–1, относящиеся к комплексам СО с координационно-ненасыщенными ионами (ЛКЦ); 2 – полоса при 2175 см–1, соответствующая комплексу СО с сильными бренстедовскими кислотными центрами, представляющими собой мостиковые Si-O(H)-Al группы; 3 − полоса при 2155-2157 см–1, относящаяся к комплексу СО со слабокислотными силанольными группами Si-OH; 4 − широкая полоса при 2138 см–1, относящаяся к капиллярной конденсации СО в (c) каналах цеолита. Повышение давления CO на образце Zn-AC(ГМДА) не приводит к изменению частоты полосы комплекса CO с сильным БКЦ при 2175 см–1, в то время как при более высоких давлениях СО на образце Zn-AC(БКА) наблюдается сдвиг этой полосы до 2173 см–1. Для образца Zn-AC(Бутанол) первые дозы CO приводят к появлению новой слабой полосы при 2178 см–1. С увеличением покрытия СО (до 10 см–1), наблюдаемые значения νco значительно снижаются, скорее всего, в результате латеральных взаимодействий
между молекулами монооксида углерода, адсорбированными на оксиде цинка. Полосы около 11
Рисунок 2 – ИК-спектры в области валентных колебаний ОН-групп образцов: Zn–АС(ГМДА) (а); Zn– АС(БКА) (b); Zn–АС(Бутанол) (c)
Рисунок 3 – ИК-спектры СО, адсорбированного на образцах при температуре жидкого азота и увеличении давления: Zn–АС(ГМДА) (а); Zn–АС(БКА) (b); Zn–АС(Бутанол)
2178-2168 см–1 в спектре образца Zn-AC(Бутанол), очевидно, могут быть отнесены к комплексу CO как с БКЦ, так и с ZnO.
Интегральная интенсивность более высоких частотных диапазонов 2225-2233 см–1 увеличивается в следующем порядке: Zn-АС(БКА) > Zn-АС(Бутанол) > Zn-АС(ГМДА). По- видимому, аналогичным образом изменяется концентрация изолированных ионов Zn2+ и небольших кластеров ZnO.
По данным микроскопических исследований морфология и размер кристаллов образцов Zn- AC, синтезированных с различными структурообразователями, заметно отличаются (рис. 4). Частицы Zn-АС(ГМДА) имеют вид поликристаллических сфероидов, состоящих из сросшихся монокристаллов, с размерами от 3 до 8 мкм. Форма и размеры кристаллов цеолита, полученного с БКА, имеют форму призм с размерами граней 3 × 4 × 5 мкм, в основании которых находятся вытянутые шестиугольники. Кристаллы цеолита, синтезированного с бутанолом, имеют неоднородный состав, встречаются как мелкие, так и крупные частицы.
ГМДА БКА Бутанол
Рисунок 4 – Микрофотографии цинкалюмосиликатов, синтезированных с различными структурообразователями
Элементный состав для частиц цинкалюмосиликатов, синтезированных с разной структурообразующей добавкой, полученные из спектров EDX с помощью программы спектрометра, представлены в табл. 4, из данных которой следует, что в образце Zn-АС(ГМДА) для цинка наблюдается небольшое его присутствие.
Таблица 4 – Элементный состав участков образцов цинкалюмосиликатов Концентрация элементов (ат.%)
Элемент
Al K Si K Zn K
Е (кеВ)
1,486 1,739 8,630
Zn-АС Zn-АС (ГМДА) (БКА)
3,70 3,95 96,18 93,00 0,13 3,04
участок 010 6,41 91,01 2,58
*Zn-АС(Бутанол) участок 011
7,09 92,47 0,44
участок 012 6,39 93,48 0,22
Примечание. *– выбранные участки представлены на рис. 5.
Для образца цинкалюмосиликата, синтезированного с БКА, зафиксированы более интенсивные сигналы Zn, а также увеличение концентрации по сравнению с образцом Zn- АС(ГМДА) (табл. 4), что, по-видимому, обусловлено увеличенной шероховатостью поверхности образца Zn-АС(БКА). Для образца Zn- AC(Бутанол) прослеживается неравномерность распределения Zn (рис. 5). Максимальное содержание Zn зафиксировано для фрагмента частицы наименьшего диаметра и толщины («010»). Для остальных участков («011» и «012») концентрация Zn уменьшается, и для самой крупной частицы «012» – концентрация почти на порядок ниже, чем для частицы «010». Образец Zn-АС(Бутанол) отличается большей неравномерностью распределения цинка как по разным пластинчатым частицам, так и даже в пределах объема одной
частицы.
Таким образом, Zn-алюмосиликаты, синтезированные из щелочных алюмокремнегелей с
использованием различных структурообразующих добавок, отличаются по физико-химическим свойствам, что обусловлено локальными неоднородностями в распределении алюминия в алюмосиликатном кристаллическом каркасе и различной кислотностью каталитических систем, что, в свою очередь, сказывается на каталитических свойствах исследуемых систем.
Результаты исследований по влиянию температуры процесса на конверсию пропана и селективность образования ароматических углеводородов на Zn-алюмосиликатах представлены на рис. 6. Заметное превращение пропана на образце Zn-АС(ГМДА) наблюдается при температуре 450 °C. При повышении температуры процесса до 550 ° C конверсия пропана резко увеличивается, достигая 97 %, а при 600 °C пропан превращается полностью. Селективность образования ароматических углеводородов на этом катализаторе также увеличивается, достигая максимального значения (40,2 %) при 600 °C. Аналогичная зависимость конверсии пропана от температуры процесса наблюдается для катализатора Zn-АС(БКА). Однако этот образец отличается низкой стабильностью работы. После трех часов непрерывной работы конверсия пропана на нем начинает снижаться, а последующее повышение температуры процесса до 600 °C не приводит к восстановлению активности катализатора, конверсия пропана составляет 80 %. Для катализатора Zn-АС(БКА) также характерно резкое увеличение ароматизирующей активности при повышении температуры процесса от 450 до 500 °C, однако при дальнейшем увеличении температуры процесса селективность образования ароматических углеводородов повышается незначительно.
Катализатор Zn-АС(Бутанол) характеризуется наименьшей общей каталитической активностью в исследованном диапазоне температур. При повышении температуры процесса от 450 до 550 °C наблюдается постепенное увеличение конверсии пропана, а при 550 °C достигается
максимальная его степень превращения – 75 %, что на 22 % ниже, чем для образца Zn-АС(ГМДА). 13
Рисунок 5 – Снимки HAADF-STEM частиц разной морфологии Zn-АС(Бутанол)
При дальнейшем повышении температуры процесса до 600 °C конверсия пропана резко падает, что указывает на быструю дезактивацию этого катализатора.
100 90 80 70 60 50 40 30 20
ГМДА
А
БКА
Температура, оC
Бутанол
БКА Бутанол
450 500
Температура, оС
ГМДА
50 45Б 40
30
20
10
5 0
450
550 600
Рисунок 6 – Зависимость конверсия пропана (А) и селективности образования ароматических углеводородов (Б) на Zn-AC, полученных с различными темплатами, от температуры процесса
Результаты исследования состава катализата показали, что основными жидкими продуктами превращения пропана на образцах Zn-АС являются бензол, толуол, алкилбензолы С8- С10, а также высокомолекулярные ароматические соединения, включая нафталин и его производные. По количественному соотношению ароматические углеводороды, образующиеся на образцах Zn-AC, полученных с различной структурообразующей добавкой, отличаются. На цеолите, синтезированном с бутанолом, образуется больше БТК-фракции и меньше нафталиновых углеводородов. Наибольшее количество алкилбензолов С9+ (4,0 %) получается на цеолите, синтезированном с ГМДА. На цеолите, синтезированном с БКА, образуется меньше всего БТК- фракции (75,5 %) и большее количество нафталиновых углеводородов.
Результаты исследований по влиянию продолжительности работы цеолитов, синтезированных с различными структурообразователями, на их активность в процессе ароматизации пропана приведены на рис. 7.
100А 80
60 40 20
50 40 30 20 10
Б
ГМДА БКА Бутанол
120 180
Время работы, мин
300
240 300 360
Рисунок 7 – Изменение конверсии пропана (А) и выхода ароматических углеводородов (Б), образующихся на Zn-содержащих цеолитах, со временем их работы (Т= 550 oС)
60 120 180
Время работы, мин
ГМДА БКА Бутанол
Конверсия, %
Конверсия пропана, %
Выход аренов, % мас.
Селективность по АрУ, %
Из приведенных на рис. 7 (А) данных, видно, что цинкалюмосиликаты, полученные с ГМДА и БКА, характеризуются практически одинаковой первоначальной активностью, но с увеличением времени работы для катализатора, синтезированного с БКА, наблюдается более резкое снижение активности. Степень превращения пропана на цинкалюмосиликате, полученном с ГМДА, за 360 мин его работы практически не снижается и составляет более 90 %, что позволяет продолжать процесс. Для образца Zn-AC(Бутанол) характерно почти линейное уменьшение его активности с ростом времени работы, при этом выход ароматических углеводородов за 300 мин реакции падает с 26,9 до 4,4 % (рис. 7(Б)).
По данным термического анализа наибольшее количество кокса образуется на показавшем максимальную ароматизирующую активность в процессе превращения пропана цинкалюмосиликате, полученном с БКА (рис. 8). Общая масса коксовых отложений для данного образца составляет 8,86 %, температура начала и максимум выгорания кокса смещены в область более высоких температур по сравнению с другими образцами, что свидетельствует об образовании на нем более плотных (конденсированных) углеродных отложений. Для цинкалюмосиликата, полученного с ГМДА, количество содержащегося на нем кокса составляет всего 4,34 %, что более чем в 2 раза меньше по сравнению с катализатором Zn-AC(БКА). Пики ДТГ и ДТА (с экзоэффектом при 605 оС) узкие, что свидетельствует об однородности углеродных отложений. Цинкалюмосиликат, полученный с бутанолом, характеризуется меньшей однородностью коксовых образований, что подтверждается наличием плеча на кривой ДТА в высокотемпературной области после температурного максимума при 605 оС. Полученные данные хорошо согласуются с результатами каталитических испытаний цинкалюмосиликатов. Так, в составе образующихся на образце Zn-AC(БКА) жидких продуктов значительно больше содержится ароматических углеводородов С9+, предшественников кокса, что и приводит к увеличению скорости протекания на нем процесса коксообразования.
АБВ
Рисунок 8 – Термограммы Zn-алюмосиликатов, синтезированных с использованием гексаметилендиамина (А), БКА (Б) и бутанола (В), проработавших при 550 oС в процессе превращения пропана в течение 6 ч
15
Таким образом, Zn-алюмосиликаты, синтезированные из щелочных алюмокремнегелей с использованием различных структурообразующих добавок, отличаются по каталитическим свойствам в процессе превращения пропана в ароматические углеводороды, что обусловлено локальными неоднородностями в распределении цинка по объему цеолитных образцов и разной их кислотностью. Наибольшей ароматизирующей активностью обладает цинкалюмосиликат, синтезированный с БКА, а максимальную стабильность работы проявляет Zn-содержащий катализатор, приготовленный с использованием в качестве структурообразующей добавки гексаметилендиамина.
Влияние природы источника кремния
На процесс кристаллизации, вызывающий изменение структуры, морфологии, дисперсного и химического составов кристаллов, кислотности и активности цеолитов значительное влияние оказывает природа и тип сырьевых реагентов, состав реакционной смеси, условия синтеза. При фазовых переходах в процессе кристаллизации из гидротермальных систем вначале образуется термодинамически наименее стабильная модификация, которая затем постепенно уступает место все более устойчивым формам. Такие превращения могут протекать только в определенной реакционноспособной среде. Все это заставляет использовать самые разные соединения в качестве источников катионов алюминия и кремния, а также готовить на их основе смеси, различные как по химическому составу, так и по физическим свойствам. В данном разделе представлены результаты исследований влияния природы источника кремния на физико-химические и каталитические свойства образца 0,82 % Zn-АС, синтезированного с ГМДА.
По данным ИК-спектроскопии установлено, что все синтезированные образцы имеют полосы поглощения, характерные для высококремнеземного цеолита типа MFI, и обладают 100 %- ой степенью кристалличности. При этом обнаружено, что скорость кристаллизации цеолитов зависит от источника кремния, используемого при их синтезе, и увеличивается в ряду: Zn-AC(ЖС) < Zn-AC(З) < Zn-AC(БС). Так, например, синтез Zn-AC(ЖС) протекает в течение 5 суток, а при
получении образца Zn-AC(БС) время синтеза сокращается до 2 суток.
На рис. 9 представлены рентгенограммы цинкалюмосиликатов, синтезированных с разным источником кремния. По результатам рентгенографических исследований установлена принадлежность всех синтезированных образцов к цеолиту типа MFI и к ромбической сингонии. Об этом свидетельствует наличие максимумов в области 2θ = 6-60°: триплета при 23,0; 24,0 и
Рисунок 9 – Рентгенограммы цинкалюмосиликатов, синтезированных с разным источником кремния
24,4°, пиков при 29,3 и 29,6° и дублета при 45,0-45,5°. Кроме того, рентгенограммы показывают присутствие рефлексов ZnO в области 2θ = 34,4–37,2°.
По данным термодесорбции аммиака Zn-алюмосиликаты, полученные с использованием разного источника кремния, значительно отличаются по кислотным характеристикам (табл. 5). Наименьшее количество сильных кислотных центров содержит цинкалюмосиликат, синтезированный с жидким стеклом. Кроме того, этот образец обладает и наименьшей силой кислотных центров обоих типов. Катализаторы, полученные с использованием в качестве источника кремния золя и белой сажи, характеризуются наличием слабых кислотных центров одинаковой силы, но в образце Zn-АС(З) их содержание выше. Для этого же образца наблюдается смещение максимума высокотемпературного пика в область более высоких температур, что свидетельствует об увеличении силы высокотемпературных центров.
Таблица 5 – Кислотные и текстурные характеристики цинкалюмосиликатов
Катализатор
Zn-AC(ЖС)
Zn-AC(З)
Zn-AC(БС)
Примечание. Обозначение см. табл. 2
Тмакс, оС
Концентрация, мкмоль/г
Sуд, 2 м /г
Суммарный объем пор, см3/г 0,143 0,175 0,187
Средний диаметр пор, нм 1,86 1,96 1,96
ТI ТII
225 460
230 475 1092 532 1624 385 230 465 989 551 1540 384
СI СII С 909 389 1298
Исследования текстурных свойств цинкалюмосиликатов, отличающихся природой используемого при синтезе источника кремния, показали, что наименьшую удельную поверхность и наименьший объем пор имеет цинкалюмосиликат, синтезированный с жидким стеклом, при этом данный образец характеризуется и наименьшим средним диаметром пор (табл. 5). Образцы, полученные с использованием золя и белой сажи, обладают практически одинаковой величиной удельной поверхности и одинаковым средним диаметром пор, при этом суммарный объем пор для второго образца несколько выше и составляет 0,187 см3/г.
Результаты исследований каталитических свойств Zn-алюмосиликатов, приготовленных с использованием разных источников кремния, представлены в табл. 6. Видно, что все исследуемые образцы проявляют достаточно высокую активность в процессе превращения пропана в ароматические углеводороды. С повышением температуры реакции на всех цинкалюмосиликатах наблюдается увеличение степени превращения пропана и при температуре 600 oС пропан превращается практически полностью. Наибольшей активностью и селективностью в отношении образования ароматических углеводородов обладает цинкалюмосиликат, полученный с белой сажей. Выход ароматических углеводородов на нем достигает 42,9 % при температуре 600 oС. Цинкалюмосиликат, синтезированный с использованием золя, не отличается по общей активности
от образца Zn-АС(БС), однако немного уступает ему по ароматизирующей активности. Это 17
свидетельствует о том, что использование при синтезе соответствующих источников кремния приводит к образованию близкого количества и одинаковых по природе активных центров, с участием которых происходит активация молекул пропана и дальнейшее превращение промежуточных продуктов в ароматические соединения, что подтверждается данными исследований кислотных свойств этих катализаторов. Образец, полученный с жидким стеклом, проявляет наименьшую ароматизирующую активность в процессе превращения пропана из исследуемых катализаторов.
Таблица 6 – Показатели процесса превращения пропана на цинкалюмосиликатах Катализатор Т, оС Х, % YАрУ, % SАрУ, % Sкр, % Sдег, % SН2, %
Zn-AC(ЖС)
450
550
40 77 97 100
2,3 22,3 36,5 40,2
5,7 29,0 37,5 40,2
82,7 61,2 55,0 53,5
9,7 7,8 5,2 3,0
1,9 2,0 2,3 3,3
Zn-АС(З)
450
550
42 86 98 99
1,6 34,3 39,3 42,7
3,8 39,9 40,1 43,1
89,7 54,7 54,2 50,8
4,8 3,1 2,6 2,4
1,7 2,3 3,1 3,7
Zn-АС(БС)
450
550
42 84 98 99
1,7 33,9 40,3 42,9
4,1 40,4 41,1 43,3
89,3 54,4 53,0 50,7
4,8 3,0 2,7 2,3
1,8 2,2 3,2 3,7
Примечание. Обозначение см. табл. 3
Исследования состава образующихся газообразных и жидких продуктов превращения пропана на Zn-алюмосиликатах, приготовленных с использованием разных источников кремния, показали, что по качественному составу они не отличаются друг от друга, но несколько отличаются по количественному содержанию отдельных компонентов (табл. 7). В составе газообразных продуктов реакции наибольшая доля приходится на метан и этан – основные продукты крекинга пропана, при этом на образце Zn-AC(ЖС) образуется меньше метана и больше этана по сравнению с катализаторами Zn-АС(З) и Zn-АС(БС). Можно отметить относительно низкое содержание в продуктах реакции олефинов, свидетельствующее о том, что они являются промежуточными продуктами, которые активно вступают в дальнейшие взаимодействия, приводящие к образованию ароматических углеводородов.
Таблица 7 – Состав продуктов превращения пропана на цинкалюмосиликатах (Т = 550 °С)
Состав жидких продуктов, % мас. Состав газообразных продуктов, % мас. Катализатор Бензол Толуол Алкил- Нафта- Н2 СН4 С2Н6 Алкены Алканы
бензолы лины
С2-С4 С3-С4 27,1 7,9 4,2 25,3 4,2 3,3 25,5 4,4 3,4
Zn-AC(ЖС) Zn-АС(З) Zn-АС(БС)
39,4 29,7 14,4 33,6 21,4 18,5 31,6 22,0 19,2
16,5 26,5 27,3
3,6 57,2 5,0 62,2 5,3 61,4
18
Наибольшее количество бензола и толуола образуется на катализаторе, синтезированном с жидким стеклом. Состав продуктов, образующихся на катализаторах, полученных с золем и белой сажей, отличается незначительно, лишь на последнем катализаторе несколько меньше образуется бензола и больше – алкилнафталинов.
Влияние второго темплата (технического углерода)
В настоящее время большое внимание уделяется созданию микро-мезопористых цеолитоподобных материалов (МММ). Создание вторичной пористости, благодаря образованию мезопор с диаметром 2-50 нм, которые облегчают процессы диффузии в катализаторе, может стать одним из путей повышения стабильности цеолитных катализаторов. В связи с этим, было проведено исследование влияния второго темплата на структурные, кислотные и каталитические свойства образца 0,82 % Zn-АС, синтезированного с БКА, в процессе превращения пропана в ароматические углеводороды.
100 80 60 40 20 0
Конверсия ВыходАрУ Селективность по АрУ
0123 Концентрация углерода, % мас.
На рис. 10 представлены данные по влиянию концентрации технического углерода, используемого при синтезе цинкалюмосиликата, на основные показатели процесса ароматизации.
Исходный микропористый цинкалюмосиликат характеризуется высокой активностью – при температуре реакции 550 °С выход ароматических углеводородов на нем достигает 55,5 % при конверсии пропана 96 %. Цинкалюмосиликат, полученный с использованием 1,0 % технического углерода, обладает несколько меньшей ароматизирующей активностью, при этом общая активность катализатора практически
Рисунок 10 – Показатели ароматизации пропана на Zn-AC, синтезированных с добавкой различного количества технического углерода (Т = 550 °С)
не изменяется. С увеличением количества добавляемого углерода в процессе синтеза цеолита происходит снижение ароматизирующей активности катализатора. Так, например, на образце Zn- AC/3,0 % С выход ароматических углеводородов составляет 43,9 %, что почти в 1,3 раза меньше, чем на исходном Zn-AC, полученном без добавки технического углерода. Следует отметить сохранение достаточно высокой селективности образования ароматических углеводородов на всех исследуемых образцах (более 45 %), что свидетельствует о наличии в них достаточного количества протонных кислотных центров для проведения реакции ароматизации пропана. При этом с ростом концентрации добавляемого углерода в процессе синтеза цинкалюмосиликатов в составе образующихся на них жидких продуктов увеличивается содержание БТК-фракции и уменьшается доля нафталиновых углеводородов, а концентрация алкилбензолов изменяется
Показатели ароматизации, %
незначительно по сравнению с другими ароматическими углеводородами. Наибольшее количество БТК-фракции образуется на образце Zn-AC/3,0 % С и составляет 82,1 %.
В таблице 8 представлены значения площади удельной поверхности и объема микро- и мезопор цинкалюмосиликатов, синтезированных с добавкой различного количества технического углерода. Наименьшая площадь удельной поверхности наблюдается у исходного Zn-AC и составляет 304 м2/г. При добавлении 1,0 и 2,0 % технического углерода на стадии гидротермального синтеза величина удельной поверхности цеолитов практически не изменяется. Дальнейшее повышение концентрации технического углерода, используемого при синтезе Zn-AC, приводит к увеличению площади удельной поверхности до 323 м2/г. Добавление технического углерода в кристаллизационный гель в процессе синтеза цинкалюмосиликата увеличивает общий объем пор вследствие увеличения объема мезопор – от 0,027 см3/г для Zn-AC до 0,061 см3/г для образца Zn-AC/3,0 % С. При этом объем микропор уменьшается от 0,122 до 0,111 см3/г.
Таблица 8 ‒ Площадь удельной поверхности и объем пор цинкалюмосиликатов
Катализатор SБЭТ, м2/г Sмикро, м2/г Vобщ., см3/г Zn-AC 304 249 0,149
Результаты исследований по влиянию времени работы цинкалюмосиликатов на их каталитические свойства приведены на рис. 11. Видно, что все исследуемые катализаторы характеризуются практически одинаковой первоначальной активностью, но с ростом продолжительности работы для исходного Zn-AC наблюдается более резкое снижение активности и через 6 ч конверсия пропана на нем снижается с 96 до 41 %, а выход образующихся ароматических углеводородов – с 55,5 до 17,9 %. Для цинкалюмосиликатов, синтезированных с добавкой технического углерода, наблюдается более плавное снижение этих показателей. Наиболее высокую стабильность работы показал образец Zn-AC/1,0 % С – через 6 ч непрерывной работы выход ароматических углеводородов на нем составил 33,7 % при конверсии пропана 74 % (рис. 11). Кроме этого, на протяжении всего реакционного цикла выход ароматических углеводородов, образующихся на данном катализаторе, выше, чем на других исследуемых катализаторах. Цинкалюмосиликат, синтезированный с добавкой 3,0 % С, по показателям общей и ароматизирующей активности близок к исходному Zn-AC.
Vмикро, см3/г Vмезо, см3/г 0,122 0,027 0,119 0,034 0,113 0,054 0,111 0,061
Zn-AC/1,0 % С
Zn-AC/2,0 % С
Zn-AC/3,0 % С
Примечание – SБЭТ – площадь удельной поверхности; Sмикро – площадь поверхности микропор; Vобщ. – суммарный объем пор; Vмикро – объем микропор; Vмезо – объем мезопор.
307 243 308 231 323 226
0,153 0,167 0,172
20
100 А 60 Б
80 60 40 20
50 40 30 20 10
Zn-AC Zn-AC/1,0 % C Zn-AC/2,0 % C Zn-AC/3,0 % C
123456 123456
Время работы, ч
Время работы, ч
Рисунок 11 – Изменение конверсии пропана (А) и выхода ароматических углеводородов (Б), образующихся на цинкалюмосиликатах (Т = 550 oС)
По данным дифференциально-термического анализа общая масса коксовых отложений для исходного микропористого образца составляет 8,86 %, температура начала и максимум выгорания кокса смещены в область более высоких температур по сравнению с другими Zn-AC, что свидетельствует об образовании на нем более плотных (конденсированных) углеродных отложений. На цинкалюмосиликатах, полученных с добавкой технического углерода, содержится меньше кокса, а образующиеся продукты уплотнения менее конденсированы, что подтверждается более низкой температурой конца горения кокса. Наименьшее количество коксовых отложений содержится на образце Zn-AC/1,0 % С и составляет 6,78 %.
Сравнительная характеристика свойств цеолитсодержащих катализаторов, полученных в лабораторных и промышленных условиях
Для сопоставления каталитических свойств цеолитсодержащих катализаторов в качестве лабораторного образца был выбран 0,82 % Zn-AC, полученный с использованием жидкого стекла и ГМДА. Выбор этого образца объясняется наибольшей его активностью и стабильностью в реакции ароматизации пропана. Для повышения механической прочности к цеолиту добавлялось 15 % связующего вещества – псевдобемита (0,82 % Zn-AC(ПБ)). В качестве промышленных образцов были исследованы катализаторы ИК-17М (г. Новосибирск), Zn-ZSM-5 (Китай), ЦСК (марка T-455, компания «Sűd-Chemie»). Промышленные катализаторы испытывали в полученной от производителя форме в виде гранул.
На гистограмме, представленной на рис. 12, приведены сравнительные данные по активности исследуемых катализаторов в процессе ароматизации пропана. Видно, что все катализаторы проявляют высокую активность в процессе превращения пропана – выход ароматических углеводородов на них при 600 °С составляет 38,2-40,5 % при практически полном превращении пропана.
Zn-AC Zn-AC/1,0 % C Zn-AC/2,0 % C Zn-AC/3,0 % C
Конверсия, %
Выход АрУ, % мас.
90
70
50
30
10
0
Конверсия
Выход АрУ
На основании проведенных исследований и полученных результатов можно заключить, что получен цеолитсодержащий катализатор, который по каталитической активности и селективности в процессе ароматизации пропана не уступает отечественным и зарубежным промышленным аналогам. Основной компонент катализатора – цинкалюмосиликат типа цеолита MFI, с высокими качественными характеристиками получается в одну стадию в процессе гидротермального синтеза и не
содержит дорогих и редких металлов.
ВЫВОДЫ
ИК-17М
Zn-ZSM-5
ЦСК «Sűd- Chemie»
0,82% Zn- AC(ПБ)
Рисунок 12 – Активность цеолитсодержащих катализаторов в процессе ароматизации пропана (Т = 600 °С)
1. Методом гидротермального синтеза из щелочных алюмокремнегелей синтезированы цинкалюмосиликаты структурного типа MFI, оптимизированы условия их синтеза и химический состав, обеспечивающие получение образцов с высокими качественными характеристиками и требуемыми каталитическими свойствами. Показано, что наиболее эффективным катализатором для процесса превращения пропана в ароматические углеводороды является образец 0,82 % Zn- AC, селективность образования ароматических углеводородов на котором при 600 oС достигает 40,2 % при полном превращении пропана.
2. Исследовано влияние природы структурообразующего агента на физико-химические и каталитические свойства цинкалюмосиликатов. Установлено формирование частиц Zn-AC различной морфологии, связанное с природой структурообразователя, и впервые показано, что в образцах Zn-АС(ГМДА) и Zn-АС(БКА) наблюдается однородное распределение цинка в цеолитном катализаторе, а в образце Zn-АС(Бутанол) – неоднородное распределение цинка как по частице, так и в пределах объема одной частицы. Установлено, что наибольшей ароматизирующей активностью обладает цинкалюмосиликат, синтезированный с бикарбонатом аммония, а максимальную стабильность работы проявляет образец, полученный с гексаметилендиамином.
3. Изучено превращение пропана в ароматические углеводороды на Zn-алюмосиликатах, синтезированных с разным источником кремния. Показано, что селективность образования ароматических углеводородов на полученных образцах достигает более 40 % при практически полном превращении исходного сырья. Установлено, что наибольшей ароматизирующей активностью обладает Zn-алюмосиликат, синтезированный с использованием белой сажи. Выход ароматических углеводородов на нем при 600 оС достигает 42,9 %, а конверсия – 99 %.
22
Конверсия, выход а ренов, %
4. Методом гидротермального синтеза с добавкой технического углерода в реакционную смесь получены цинкалюмосиликаты с микро-мезопористой структурой. Установлено, что оптимальное соотношение между объемом образовавшихся мезопор и числом активных центров достигается на цинкалюмосиликате, полученном при добавке на стадии его синтеза 1,0 % технического углерода, что приводит к уменьшению скорости коксообразования и соответственно к повышению стабильности работы катализатора.
5. Проведено сравнительное исследование каталитической активности цеолитсодержащих катализаторов, полученных в лабораторных и промышленных условиях, в процессе ароматизации пропана. Показано, что по активности и селективности образования целевого продукта полученный в лабораторных условиях катализатор не уступает известным отечественным и зарубежным аналогам. Селективность образования ароматических углеводородов на нем при температуре 600 оС и объемной скорости подачи сырья 250 ч–1 достигает 38,8 % при конверсии пропана 99 %, что сопоставимо с результатами, полученными при этих условиях процесса на катализаторах сравнения.
Актуальность проблемы
Рациональное использование попутного нефтяного газа является одной из
приоритетных задач, стоящих перед нефтегазовым комплексом России.
Несбалансированность добычи нефти и переработки сопутствующих
углеводородных газов приводит к тому, что объем ежегодно сжигаемого на
факелах попутного газа превышает, по официальным данным, 20 млрд. м3, в
действительности же безвозвратные потери его существенно выше. Все это
приводит к огромным экономическим потерям и серьезной угрозе для экологии
окружающей среды. Только квалифицированная переработка всех компонентов
природных и попутных нефтяных газов, а также газов нефтепереработки может
обеспечить решение этих задач. Преимущество глубокой переработки газового
сырья заключается в получении конечной химической продукции с высокой
добавочной стоимостью, которая положительно сказывается на экономической
эффективности предприятий, выпускающих подобную продукцию, а также на
экономике государства в целом. И здесь необходимо не только
усовершенствование существующих процессов, но и создание принципиально
новых, высокоэффективных методов получения ценных химических продуктов из
компонентов природного газа, метана, парафиновых углеводородов С2-С4,
углекислого газа, газового конденсата.
Альтернативным направлением переработки природного и попутного
нефтяного газов нефте- и газодобычи является неокислительная конверсия легких
углеводородов в присутствии каталитических систем на основе
высококремнеземных цеолитов, в результате которой происходит образование
ароматических соединений, широко используемых в химической и
нефтехимической промышленности. Возможность преобразования газообразных
углеводородов в жидкие продукты является достаточно перспективным
направлением, как с экономической, так и экологической точки зрения, и поэтому
привлекает повышенное внимание исследователей уже на протяжении многих лет
[1-4]. Опубликованные результаты исследований процесса ароматизации
углеводородов С2-С4 доказывают эффективность использования в нем
бифункциональных пентасилсодержащих катализаторов, характеризующихся
наличием кислотных центров высококремнеземного цеолита и активных
металлсодержащих центров, образующихся при введении в катализатор
промотирующих добавок и обладающих дегидрирующей способностью [5-8].
Перспективным методом модифицирования с целью улучшения тех или
иных свойств цеолитов является введение катионов металла в их каркас на стадии
гидротермального синтеза. Полученные элементоалюмосиликаты отличаются от
немодифицированных цеолитов по физико-химическим свойствам, которые
напрямую связаны со структурой каркасного алюмосиликата.
Другим перспективным направлением в области приготовления цеолитных
катализаторов является создание иерархических цеолитных структур,
сочетающих одновременно микро-, мезо- и макропоры. Микропоры обеспечивают
протекание каталитических реакций, а наличие мезо- и макропор облегчает
диффузионный массоперенос к активным центрам катализатора. Микро-
мезопористые материалы имеют ряд преимуществ как перед микропористыми
цеолитами структурного типа MFI (улучшенная диффузия молекул реагентов
внутрь кристалла, уменьшение диффузионного пути молекул реагентов и
молекул-прекурсоров кокса), так и перед мезопористыми материалами (высокая
стабильность в гидротермальных условиях, высокая кислотность, повышенная
селективность).
Параллельно с изучением каталитических свойств цеолитных систем
интенсивно ведутся исследования природы каталитически активных центров в
этих материалах, а также механизмов каталитических реакций, происходящих с
участием этих центров [9–11]. Вместе с тем, несмотря на глубокие исследования,
связанные с появлением в последние годы нового высокочувствительного
оборудования, и многочисленные публикации, в научной среде до настоящего
момента не сложилось единого мнения о природе каталитически активных
центров и механизмах каталитических реакций превращения низших алканов
даже для наиболее широко используемых цеолитных систем.
Цель и задачи исследования
Целью диссертационной работы явилось установление особенностей
активации молекул пропана на Zn-содержащих и кислотных центрах цеолита типа
MFI в зависимости от химического состава и условий приготовления
катализаторов.
Для достижения поставленной цели необходимо было решить следующие
задачи:
– установить влияние концентрации вводимого в цеолит оксида цинка
на основные показатели процесса ароматизации пропана;
– исследовать влияние природы структурообразующей добавки на
физико-химические и каталитические свойства цинкалюмосиликата в процессе
ароматизации пропана;
– изучить влияние природы источника кремния на физико-химические
свойства Zn-алюмосиликата и его активность в процессе ароматизации пропана;
– установить роль вторичного темплата (технического углерода) в
формировании микро-мезопористой структуры синтезируемого
цинкалюмосиликата, способствующей повышению стабильности работы
катализатора в процессе ароматизации пропана;
– выявить основные факторы, определяющие активность цеолитных
катализаторов (пространственное распределение и электронное состояние
металлов в цеолите, элементный состав, дисперсность, морфология и структура
образованных в цеолите кластеров).
Научная новизна работы заключается в том, что впервые:
– в условиях гидротермального синтеза получены и охарактеризованы
цинкалюмосиликаты (Zn-AC) со структурой цеолита типа MFI, оптимизированы
условия их синтеза и химический состав, обеспечивающие получение
фазовочистых образцов с высокой степенью кристалличности;
– установлено, что наибольшая активность и стабильность Zn-
содержащих катализаторов в процессе ароматизации пропана достигается при
использовании в качестве структурообразующей добавки гексаметилендиамина, а
в качестве источника кремния – жидкого стекла;
– показано, что добавление технического углерода в
кристаллизационный гель в процессе синтеза цинкалюмосиликата приводит к
повышению общего объема его пор в результате увеличения объема мезопор.
Установлено, что оптимальное соотношение между объемом образовавшихся
мезопор и числом активных центров достигается на цинкалюмосиликате,
полученном при добавке на стадии его синтеза 1,0 % технического углерода, что
приводит к уменьшению скорости коксообразования и соответственно к
повышению стабильности работы катализатора;
– получены данные о природе активных центров синтезированных
цинкалюмосиликатов, местах их локализации, а также о силе и концентрации
протонных и апротонных кислотных центров. Показано, что для
цинкалюмосиликата, синтезированного с использованием гексаметилендиамина,
активными центрами для активации пропана являются субнанометрические
кластеры ZnO внутри цеолитных каналов.
Практическая значимость работы
Полученные результаты по превращению пропана на синтезированных Zn-
содержащих цеолитных катализаторах могут послужить основой для разработки и
создания технологии переработки компонентов попутного нефтяного газа в
углеводороды большей химической ценности, а именно в ароматические
соединения. Оптимизирован состав каталитической системы и условия
проведения процесса, позволяющие получать максимально возможное количество
целевого продукта из газообразного углеводородного сырья. Промышленная
реализация данного процесса позволит рационально использовать попутный
нефтяной газ, что расширит сырьевые возможности нефтехимического сектора.
Положения, выносимые на защиту
– зависимость активности и селективности цинкалюмосиликатов в
процессе превращения пропана в ароматические углеводороды от концентрации
оксида цинка;
– закономерности изменения физико-химических и каталитических
свойств цинкалюмосиликатов в процессе превращения пропана в ароматические
углеводороды в зависимости от природы структурообразующей добавки;
– влияние природы источника кремния, используемого при синтезе
цинкалюмосиликата, на его физико-химические свойства и активность в процессе
ароматизации пропана;
– влияние второго темплата (технического углерода) на текстурные,
кислотные и каталитические свойства Zn-алюмосиликатов структурного типа
цеолита MFI в процессе превращения пропана в ароматические углеводороды.
Достоверность результатов
Результаты проведенного исследования и сформулированные выводы
подтверждаются большим объемом экспериментальных данных, полученных с
использованием комплекса современных методов исследования (ИК-
спектроскопия, рентгенофазовый анализ, электронная микроскопия,
температурно-программированная десорбция аммиака, дифференциально-
термический анализ и др.) на сертифицированном оборудовании. Достоверность
результатов каталитических исследований обеспечена проведением испытаний
образцов на лабораторной установке, оснащенной современным аналитическим
оборудованием, воспроизводимостью и согласованностью достигнутых на ней
экспериментальных данных.
Апробация работы
Материалы работы представлены и обсуждены на: XXII, XXIII, XXIV
Международных симпозиумах имени академика М.А. Усова студентов и молодых
ученых (Томск, 2018 г., 2019 г., 2020 г.); II Международной конференции
молодых ученых по нефтехимии (Звенигород, 2018 г.); X и XI Международных
конференциях «Химия нефти и газа» (Томск, 2018 г., 2020 г.); VIII Всероссийской
научно-практической конференции с международным участием, посвященной 50-
летию основания Института химии нефти «Добыча, подготовка, транспорт нефти
и газа» (Томск, 2019 г); ХХI Менделеевском съезде по общей и прикладной химии
(Санкт-Петербург, 2019 г.); VI Всероссийской научной молодежной школы-
конференции «Химия под знаком СИГМА: исследования, инновации,
технологии» (Омск, 18-20 мая 2020 г.); 6 International School-Conference on
Catalysis for Young Scientists «Catalyst Design: From Molecular to Industrial Level»
(Novosibirsk, 2021 г.); IV Российском конгрессе по катализу «Роскатализ» (Казань,
2021 г.).
Публикации
По материалам диссертации опубликовано 17 работ, в том числе, 3 статьи в
рецензируемых научных журналах, включенных в список ВАК и 3 статьи,
входящие в базу Web of Science. Кроме того, опубликованы материалы и тезисы
11 докладов на международных и российских конференциях.
Личный вклад автора
Автор диссертационной работы участвовал в постановке цели и задач
исследования, осуществлял поиск и проводил анализ литературных данных,
планировал проведение экспериментов, самостоятельно синтезировал
высококремнеземные цеолиты, проводил каталитические испытания образцов,
обрабатывал хроматограммы, принимал участие в обработке и обсуждении
результатов физико-химических методов исследования, в систематизации и
представлении полученных результатов в форме устных и стендовых докладов на
конференциях различного уровня, в подготовке статей к публикации в научных
журналах.
Структура и объем работы
Диссертационная работа состоит из введения, трех глав, выводов и списка
литературы, включающего 155 ссылок, изложена на 148 страницах и содержит 56
рисунков и 24 таблицы.
Читать «Закономерности формирования активных центров Zn-содержащих цеолитных катализаторов и их роль в процессе превращения легких углеводородов»
Публикации автора в научных журналах
Помогаем с подготовкой сопроводительных документов
Хочешь уникальную работу?
Больше 3 000 экспертов уже готовы начать работу над твоим проектом!