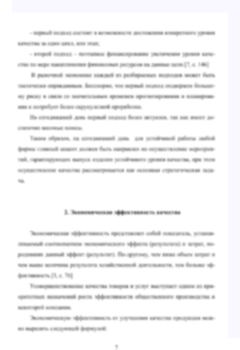
Формирование структуры мартенситностареющей стали в процессе вакуумной электронно-лучевой наплавки
В данной исследовательской работе были исследованы образцы после вакуумной электронно-лучевой наплавки мартенситностареющей 25Х12М12К10Н (ЭП928) стали и с последующим старением.
Целью данной работы является изучение структуры покрытия после электронно-лучевой наплавки в вакууме и последующего старения, и ее влияние на уровень микротвердости.
На сегодняшний день огромная роль отводится упрочнению поверхности механизмов и машин, поскольку примерно 50% выхода из строя данных несущих нагрузку деталей отводится износу. В настоящее время большинство наплавочных деталей после наплавки требует, как шлифования так и механической обработки, это возможно осуществить когда покрытие после наплавки имеет средний уровень тердости.
Введение ……………………………………………………………………………………………………… 18
1 Обзор литературы ………………………………………………………………………………….. 20
1.1 Мартенситные стали ……………………………………………………………………… 20
1.2 Мартенситностареющие стали ………………………………………………………….. 25
1.3 Мартенситные стали их особенности……………………………………………… 26
1.4 Сварка мартенситных сталей …………………………………………………………. 34
1.5 Существующие аддитивные технологиии ………………………………………. 39
1.6 Вакуумная электронно-лучевая наплавка ……………………………………….. 42
1.7 Оборудование для электронно-лучевой наплавки …………………………… 44
1.8 Концентрированные потоки энергии (КПЭ) …………………………………… 48
1.9 Постановка задачи …………………………………………………………………………. 50
2 Материалы, оборудование и методы исследования ……………………………………. 53
2.1 Технологическое оборудование для нанесения покрытий ………………….. 53
2.2 Применяемые наплавочные материалы …………………………………………….. 55
2.3 Структурно-фазовый анализ исследуемых покрытий ………………………… 56
2.4 Измерение микротвердости ………………………………………………………………. 58
3 Результаты и обсуждение ………………………………………………………………………….. 59
4. Финансовый менеджмент, ресурсоэффективность и ресурсосбережение …… 65
4.1 Предпроектный анализ ……………………………………………………………………… 65
4.1.1 Потенциальные потребители результатов исследования …………………. 65
4.1.2 Анализ конкурентных технических решений с позиции
ресурсоэффективности и ресурсосбережения …………………………………………. 66
4.2 Fast − анализ …………………………………………………………………………………….. 67
4.2.1 Описание главных, основных и вспомогательных функций,
выполняемых объектом ………………………………………………………………………….. 67
4.2.2 Определение значимости выполняемых функций объектом ……………. 69
4.2.3 Определение значимости функций …………………………………………………. 73
4.2.4 Анализ стоимости функций, выполняемых объектом исследования .. 74
4.2.5 Построение функционально-стоимостной диаграммы объекта и ее
анализ ……………………………………………………………………………………………………. 76
4.2.6 Оптимизация функций, выполняемых объектом …………………………….. 76
4.3 SWOT – анализ …………………………………………………………………………………. 77
4.4 Оценка готовности проекта к коммерциализации …………………………… 79
4.5 Методы коммерциализации результатов научно технического
исследования …………………………………………………………………………………………. 82
4.6 Инициация проекта …………………………………………………………………………… 82
4.7 Планирование управления проектом …………………………………………………. 85
4.7.1 Структура работ в рамках научного исследования ………………………….. 85
4.7.2 Определение трудоемкости выполнения работ ……………………………….. 86
4.7.3 Разработка графика проведения научного исследования …………………. 88
4.8 Бюджет научного исследования. Затраты на материалы и эксперименты
………………………………………………………………………………………………………………. 92
4.9 Расчет фонда заработной платы ………………………………………………………… 93
4.9 Определение ресурсной финансовой и бюджетной эффективности
исследования 97
4.9.1 Оценка сравнительной эффективности проекта ………………………………. 97
5 Социальная ответственность ………………………………………………………………… 101
5.1 Анализ выявленных вредных факторов проектируемой
производственной среды ………………………………………………………………………. 102
5.1.1 Электромагнитные поля в производственных помещениях; ………….. 102
5.1.2 Производственный шум ……………………………………………………………….. 104
5.1.3 Освещенность рабочей зоны ……………………………………………………… 105
5.1.4. Микроклимат в помещении …………………………………………………………. 109
5.2 Анализ выявленных опасных факторов проектируемой
производственной среды ………………………………………………………………………. 111
5.2.1 Факторы электрической природы …………………………………………………. 111
5.2.2 Факторы пожарной и взрывной природы………………………………………. 116
5.3 Охрана окружающей среды …………………………………………………………….. 119
5.4 Защита в ЧС ……………………………………………………………………………………. 120
5.5 Правовые и организационные вопросы обеспечения безопасности ….. 121
Заключение ……………………………………………………………………………………………….. 124
Список литературы ……………………………………………………………………………………. 126
Приложение А …………………………………………………………………………………………… 131
На сегодняшний день огромная роль отводится упрочнению поверхности
механизмов и машин, поскольку примерно 50% выхода из строя данных несущих
нагрузку деталей отводится износу.
В настоящее время качестве наплавочного материала используются
композиционные материалы с высокой исходной твердостью, которые
подвергаются после нанесения из них покрытий только шлифованию. Однако
ряд деталей после наплавки требует механической и последующей термической
обработки. Это возможно осуществить, когда покрытие после наплавки имеет
средний уровень твердости и, следовательно, его можно механически
обрабатывать.
Исходя из данных требований наиболее перспективными являются
покрытия на основе мартенситностареющих сталей со средним уровнем
твердости после наплавки ~4 ГПа, а после старения ~6 ГПа. Эти покрытия кроме
того, являются одними из наиболее перспективных материалов для создания
современных высокопрочных, коррозионностойких изделий, работающих в
условиях повышенных и сверхнизких температур, при высоких давлениях,
благодаря специфическому механизму упрочнения, высокой прочности и
технологичности таких материалов.
Целью данной работы является изучение структуры покрытия
непосредственно после электронно-лучевой наплавки в вакууме и последующего
старения, и ее влияние на уровень микротвердости.
Для достижения заданной цели в работе необходимо решить следующие
задачи.
1. Подготовить наплавочную смесь порошков.
2. Осуществить электронно – лучевую наплавку подготовленной смеси
порошков на основной металл (Сталь 20).
3. Провести термическую обработку (старение) части наплавленных
образцов.
4. Сделать анализ микроструктуры полученных покрытий.
5. Провести замеры микротвердости по толщине наплавок.
6. На основании полученных результатов дать рекомендации по
технологическим параметрам получения подобных покрытий.
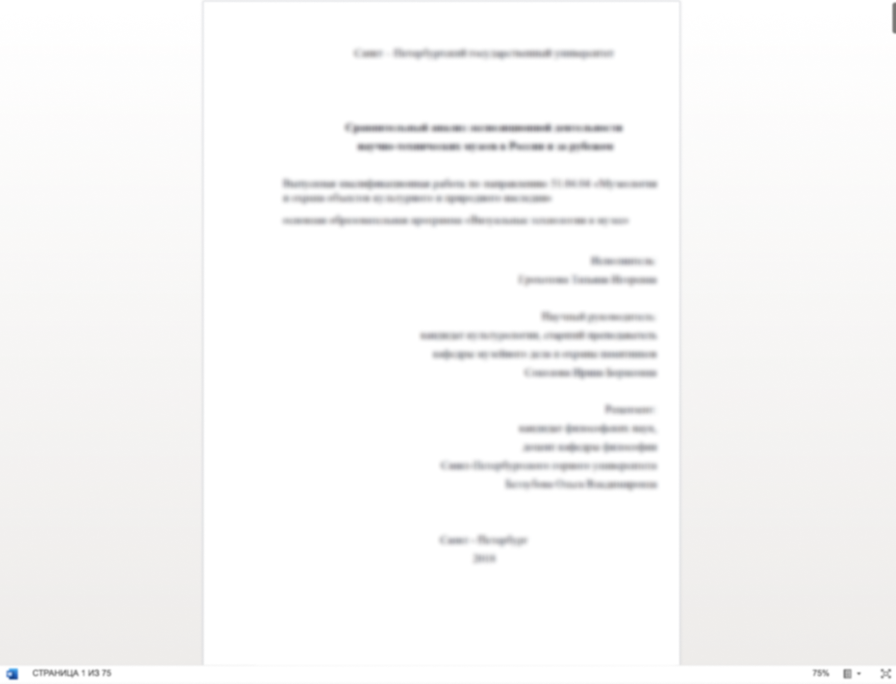
Хочешь уникальную работу?
Больше 3 000 экспертов уже готовы начать работу над твоим проектом!