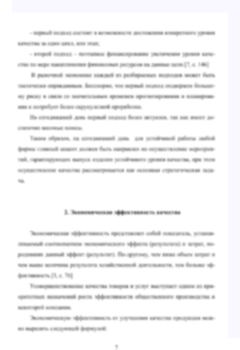
Получение материала электроискровым спеканием под давлением из механически сплавленных порошков Ti-45Nb
Объектом исследования был порошокTi-45Nb, полученный механическим легированием, и образцы, полученные электроискровым спеканием под давлением.
Целью настоящей работы было исследование особенностей формирования компактного материала из механически легированного порошка Ti-45Nb электроискровым спеканием под давлением. Оценка вклада гранулометрического состава порошка и режимов термообработки на строение и механические свойства полученного материала.
В результате исследований описано строение порошка сплаваTi-45Nb, полученного механическим легированием, выполнено электроискровое спекание под давлением порошка сплаваTi-45Nb двух фракций–80-200 мкм и более 200 мкм, описано строение и механические свойства полученных образцов в исходном состоянии и после отжига при температуре 400 ?С и 600 ?С.
Реферат …………………………………………………………………………………………………….. 5
Введение …………………………………………………………………………………………………… 9
1. Литературный обзор…………………………………………………………………………. 11
1.1. Механическое легирование ………………………………………………………… 11
1.1.1. Механизм механического легирования ………………………………… 11
1.1.2. Оборудование и параметры механического легирования……. 14
1.1.3. Механическое легирование в системе титан-ниобий …………….. 16
1.2. Электроискровое спекание под давлением ………………………………… 18
1.2.1. Механизмы электроискрового спекания под давлением …….. 19
1.2.2. Оборудование и параметры электроискрового спекания под
давлением …………………………………………………………………………………………. 21
1.3.3. Применение SPS для создания компактных материалов
медицинского назначения ………………………………………………………………… 26
2 Оборудование и методы исследования ……………………………………………….. 29
2.1 Механическая активация порошков …………………………………………….. 29
2.2 Использование SPS технологии для получение компактного
материала…………………………………………………………………………………………….. 30
2.3 Методы исследования структуры и свойств …………………………………. 31
3 Результаты исследований……………………………………………………………………. 34
3.1 Исследование порошка Ti-45Nb, полученного механическим
легированием ………………………………………………………………………………………. 34
3.2 Исследование образцов, полученный SPS …………………………………….. 37
3.3 Влияние отжига на строение образцов ………………………………………….. 44
4. Финансовый менеджмент, ресурсоэффективность и
ресурсосбережение …………………………………………………………………………………. 51
4.1 Введение………………………………………………………………………………………. 51
4.2 Анализ конкурентных технических решений с позиции
ресурсоэффективности и ресурсосбережения …………………………………….. 51
4.3 SWOT-анализ ……………………………………………………………………………… 53
4.4 Цели и результат проекта …………………………………………………………… 56
4.4.1. Контрольные события проекта …………………………………………….. 57
4.5 Потенциальные потребители результатов исследования ………….. 57
4.6 Расчет затрат ………………………………………………………………………………. 58
4.6.1 Расчет затрат на материалы …………………………………………………. 58
4.6.2. Расчет затрат на оборудование ……………………………………………… 59
4.6.3. Расчет амортизационных расходов ………………………………………. 60
4.6.4. Расчет заработной платы………………………………………………………. 61
4.6.5 Социальные отчисления работникам …………………………………… 68
4.6.6. Расчет затрат на электроэнергию …………………………………………. 68
4.6.7 Расчет общей себестоимости разработки ……………………………… 69
4.7 Определение ресурсной (ресурсосберегающей), финансовой,
бюджетной, социальной и экономической эффективности
исследования ……………………………………………………………………………………….. 70
4.7.1 Оценка абсолютной эффективности исследования ……………… 70
4.7.2 Оценка сравнительной эффективности исследования ………… 75
4.8 Заключение по разделу ……………………………………………………………….. 78
5. Социальная ответственность …………………………………………………………… 82
5.1 Введение………………………………………………………………………………………. 82
5.2 Правовые и организационные вопросы обеспечения безопасности
………………………………………………………………………………………………………………82
5.2.1 Организационные мероприятия обеспечения безопасности … 82
5.2.2 Эргономические требования к правильному расположению и
компоновке рабочей зоны ………………………………………………………………… 83
5.3 Производственная безопасность…………………………………………………. 84
5.3.1. Анализ опасных и вредных производственных факторов …… 85
5.3.2 Основные мероприятий по снижению уровней воздействия
опасных и вредных факторов на исследователя ……………………………… 91
5.4 Экологическая безопасность ………………………………………………………… 91
5.5. Безопасность в чрезвычайных ситуациях ……………………………………. 92
5.6 Анализ пожарной безопасности …………………………………………………….. 93
5.7 Заключение по разделу ………………………………………………………………….. 94
Заключения ……………………………………………………………………………………………. 96
Список публикаций ……………………………………………………………………………….. 97
Список использованных источников ……………………………………………………. 98
Приложение А ………………………………………………………………………………………. 103
Сплавы системы Ti-Nb являются перспективным материалом для
использования в электротехнике и медицине как основа для имплантатов [1-
2].Сложность получения данного сплава заключается в большой разнице
температур плавления [3]. Поэтому, наряду с получением данного сплава
плавлением, используется механическое легирование (МЛ) компонентов в
шаровых мельницах [4]. Особенностью механического сплавления является
порошкообразная форма получаемого продукта, требующая для создания
конструкционного материала дальнейшего компактирования.
Известно большое количество способов получения готовых изделий из
механически сплавленных порошков: обычным прессованием и спеканием
[5], спеканием при сверхвысоком давлении [6], электронно-лучевой
порошковой металлургией [7], селективным лазерным сплавлением [8-9] и
другие.
Одним из перспективных методов компактирования является
электроискровое спекание под давлением. В англoязычных научных
изданиях этот метод называется Spark Plasma Sintering (SPS) [10]. При
спекании порошка на материал одновременно воздействует постоянный ток в
импульсном режиме, температура и давление. Импульсный режим
обеспечивает локальный нагрев контактных зон на границе частиц и их
быстрое охлаждение, а высокая плотность межзеренных границ
механокомпозита и большой запас свободной энергии при последующем
нагреве способствуют интенсификации процесса спекания и сохранению
ценных структурных характеристик материала в спеченном состоянии.
Целью настоящей работы было исследование особенности
формирования компактного материала из механически легированного
порошка Ti-45Nb электроискровым спеканием под давлением. Оценка вклада
гранулометрического состава порошка и режимов термообработки на
строение и механические свойства полученного материала.
В работе были поставлены следующие задачи:
1. Исследовать строение порошка сплава Ti-45Nb, полученного
механическим легированием.
2. Выполнить электроискровое спекание под давлением порошка сплава
Ti-45Nb двух фракций – 80-200 мкм и более 200 мкм.
3. Исследовать строение и механические свойства полученных образцов.
4. Оценить влияние последующего отжига на строение и механические
свойства образцов.
1.1. Механическое легирование
Процесс механического легирования (МЛ) начинается с смешивания
порошков в нужной пропорции и загрузки порошковой смеси в мельницу
вместе с шлифовальной средой (как правило, стальные шарики). Эта смесь
измельчается в течение заданного периода времени до того, когда состав
каждой частицы порошка такой же, как доля элементов в стартовой смеси
порошка. Измельченный порошок затем консолидируется в объемную форму
и обрабатывается для получения желаемой микроструктуры и свойств [11-
14].
1. Исследованы морфология, гранулометрический и фазовый состав
порошка Ti-45Nb двух фракций 80-200 мкм и более 200 мкм, которые были
получены механическим легированием. Частицы имеют форму окатышей и
состоят из одной фазы β-TiNb с ОЦК решеткой. Количество Nb в объеме
частиц меняется от 38 до 49 мас. %, что свидетельствует о неравномерном
растворении компонентов друг в друге. Гранулометрический состав порошка
не влияет на его фазовый состав и строение.
2. В процессе электроискрового спекания под давлением из
порошка Ti-45Nb формируется компактный материал с низкой пористостью
в сотые доли процента. Образцы имеют зеренную микроструктуру с
размером в несколько микрометром и следами экструзии. Основной
структурной составляющей является β-TiNb. По границам зерен β-фазы
располагаются включения α-фазы – твердого раствора Nb в Ti с ГЦК
решеткой.
3. Размер компактируемых частиц в исследуемом интервале
практически не влияет на строение, фазовый состав и механические свойства
полученных образцов. Некоторое снижение значения микротвердости
материала, полученного из частиц большей фракции, может быть связано с
отличиями в протекании процессов компактирования, что приводит к
формированию в этом случае более равновесной структуры.
4. В процессе отжига до температуры 400 0С и 600 0С в материале
проходят процессы частичной перестройки микроструктуры: не наблюдается
следов экструзии, незначительно увеличивается доля α-фазы. Это приводит к
снижению прочностных характеристик при испытании на сжатие. При
увеличении температуры отжига эффект разупрочнения выше. Это относится
к образцам, полученным из обеих исследуемых фракций порошка.
Список публикаций
1. Токтасынов Е.Е., Мукашова Д.Д. Получение материала из механически
легированного порошка Ti-Nb методом электроискрового спекания под
давлением // Прогрессивные технологии и экономика в машиностроении:
сборник трудов XI Всероссийской научно-практической конференции для
студентов и учащейся молодежи / Юргинский технологический институт. –
Томск: Изд-во ТПУ, 2020. – С. 29–31.
2. Мукашова Д.Д., Токтасынов Е.Е., Криницын М.Г. Создание
селективным лазерным сплавлением трехмерных образцов из
интерметаллида // Прогрессивные технологии и экономика в
машиностроении: сборник трудов XI Всероссийской научно-практической
конференции для студентов и учащейся молодежи / Юргинский
технологический институт. – Томск: Изд-во ТПУ, 2020. – C. 55–57.
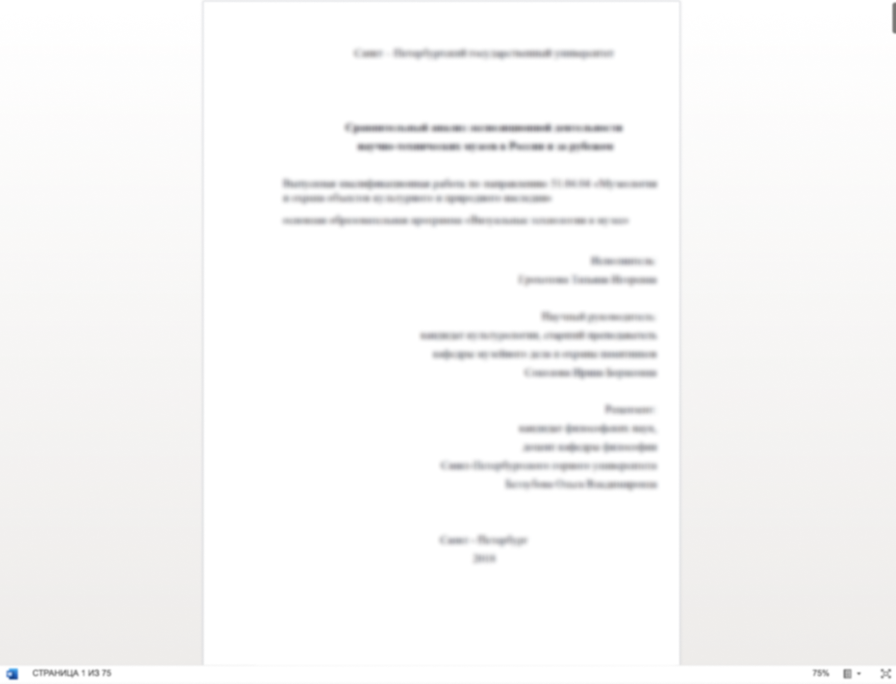
Хочешь уникальную работу?
Больше 3 000 экспертов уже готовы начать работу над твоим проектом!