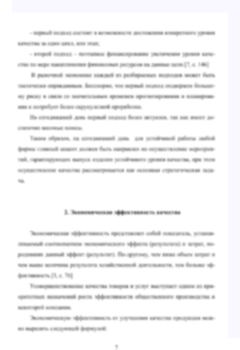
Разработка и регулирование процесса орбитальной сварки труб поверхностного нагрева диаметром до 60 мм с программированием режима
Цель работы – разработка процесса орбитальной сварки корневого слоя труб поверхностного нагрева с программированием режима сварки.
Объектом исследования является: процесс сварки неплавящимся вольфрамовым электродом в аргоне.
Предмет исследования – сварочная ванна в процессе сварки неповоротных стыков труб при сварке на постоянном токе.
В процессе исследования проводились анализ комплекса сил, действующих на сварочную ванну в процессе сварки и способы сварки неплавящимся электродом с применением импульсного питания сварочной дуги, проведен анализ моделей сварочной ванны и предложено феноменологическое описание сварочной ванны.
В результате исследования разработан способ сварки дугой, горящей в импульсном режиме и оборудование обеспечивающее его реализацию.
Введение ………………………………………………………………………………………………….. 17
1. Обзор литературы…………………………………………………………………………………. 20
1.1 Критическая масса сварочной ванны в процессе орбитальной сварки ….. 20
1.2 Основные силы, действующие на сварочную ванну …………………………….. 23
1.2.1 Механическое (силовое) воздействие дуги ……………………………………. 23
1.2.2 Поверхностное натяжение, действующее на сварочную ванну ………. 25
1.2.3 Вес сварочной ванны ……………………………………………………………………. 30
2 Объект и методы исследования ……………………………………………………………… 32
2.1 Материал сварной конструкции ………………………………………………………….. 32
2.2 Определение эквивалента углерода …………………………………………………….. 33
2.3 Разработка модели комплекса сил, действующих на сварочную ванну … 35
2.4 Характеристика сварочной ванны ……………………………………………………….. 35
2.5 Геометрические размеры сварочной ванны …………………………………………. 36
2.6 Модели сварочных ванн ……………………………………………………………………… 37
2.7 Комплекс сил, действующих на сварочную ванну ……………………………….. 38
2.7.1 Расчет составляющих силы поверхностного натяжения ………………… 39
2.8 Модель сварочной ванны для характеристики …………………………………….. 40
3 Описание экспериментальной установки ……………………………………………….. 49
3.1 Сварочная головка………………………………………………………………………………. 50
3.1.1 Устройство и работа головки ………………………………………………………… 51
3.2 Автомат ……………………………………………………………………………………………… 52
3.3 Система импульсного питания сварочной дуги …………………………………… 52
3.4 Блок управления …………………………………………………………………………………. 54
3.5 Описание центрирующего устройства…………………………………………………. 56
3.6 Центрирование труб и установка зазора………………………………………………. 58
4 Разработка программных режимов сварки и контроль качества ……………… 60
4.1 Разработка программных режимов сварки …………………………………………… 60
4.2 Контроль качества ………………………………………………………………………………. 61
5 Эксперимент и результаты …………………………………………………………………….. 66
6 Финансовый менеджмент, ресурсоэффективность и
русурсосбережение….. …………………………………………………………………………….. 70
6.1 Потенциальные потребители результатов исследования ……………………… 70
6.2 Анализ конкурентных технических решений ………………………………………. 71
6.3 SWOT – анализ …………………………………………………………………………………… 72
6.4 Определение возможных альтернатив проведения научных
исследований …………………………………………………………………………………………… 73
6.5 Планирование научно-исследовательских работ………………………………….. 75
6.5.1 Структура работ в рамках научного исследования ………………………… 75
6.5.2 Определение трудоемкости выполнения работ ……………………………… 75
6.5.3 Разработка графика проведения научного исследования ……………….. 76
6.5.4 Расчет материальных затрат НТИ …………………………………………………. 80
6.5.5 Основная и дополнительная заработная плата исполнителей темы … 81
6.5.6 Отчисления во внебюджетные фонды (страховые отчисления) ……… 82
6.5.7 Накладные расходы………………………………………………………………………. 83
6.5.8 Формирование бюджета затрат научно-исследовательского проекта
………………………………………………………………………………………………………………… 83
6.6 Определение ресурсной (ресурсосберегающей), финансовой, бюджетной,
социальной и экономической эффективности исследования ……………………… 84
7 Социальная ответственность …………………………………………………………………. 87
7.1 Введение …………………………………………………………………………………………….. 87
7.2 Производственная безопасность………………………………………………………….. 88
7.2.1 Вредные факторы …………………………………………………………………………. 89
7.2.1.1 Отклонение показателей микроклимата ……………………………………. 89
7.2.1.2 Уровень шума на рабочем месте ………………………………………………. 90
7.2.1.3 Освещенность рабочей зоны …………………………………………………….. 91
7.2.1.4 Повышенная запыленность и загазованность воздуха рабочей
зоны…………………………………………………………………………………………………………. 96
7.2.1.5 Повышенный уровень электромагнитных излучений ……………….. 97
7.2.2 Опасные факторы …………………………………………………………………………. 99
7.2.2.1 Электрический ток …………………………………………………………………… 99
7.2.2.2 Пожарная опасность ………………………………………………………………. 103
7.2.2.3 Движущаяся часть установки для сварки неплавящимся
электродом …………………………………………………………………………………………….. 106
7.3 Экологическая безопасность ……………………………………………………………… 107
7.4 Безопасность в условиях ЧС ……………………………………………………………… 108
Заключение ……………………………………………………………………………………………. 110
Список использованных источников ………………………………………………………. 111
Приложение I (Справочное) ……………………………………………………………………. 113
В бытовом и промышленном масштабах применяется трубы различных
диаметров. Для их соединения существует множество способов. Самый
распространенный метод для металлических изделий – сварка. Учитывая
диаметры изделий, у каждой категории есть свои особенности. Например,
трубы малого диаметра имеют свои сложности в ключе соединения при
помощи сварки, требующие привлечения опытного сварщика.
При сварке труб малого диаметра сварка делается за один проход,
поэтому металл все время нагревается, что может привести к пережогу и
изменяются силы, действующую на сварочную ванну. Необходим подбор
определенных параметров сварки, чтобы не превысить значения температуры
и критической массы сварочной ванны в процессе сварки.
Одним из наиболее актуальных инструментов для выполнения данных
работ является орбитальная сварка. Обычные виды сварки хорошо
обрабатывают лишь потолочный шов. В то же время, остальные участки
соединения получаются неравномерными и плохо обрабатываемыми.
Объектом исследования является: процесс сварки неплавящимся
вольфрамовым электродом в аргоне.
Предмет исследования – сварочная ванна, провисающая, стекающая
или отвисающая от трубы в процессе сварки неповоротных стыков труб в
определенном пространственном положении на постоянном токе.
Научная новизна исследования состоит в том, что в работе впервые
изучено влияние основных сил, действующих на сварочную ванну в процессе
орбитальной сварки.
Практическая значимость полученных результатов состоит в
использовании передовых технологий, с помощью которых можно добиться
снижения затрат на производство и повысить качество продукции.
Из преимуществ для орбитальной сварки можно выделить следующие:
1) возможна сварка практически любых металлов и сталей, включая
стали с ограниченной свариваемостью, в том числе никелевые сплавы,
алюминий, медь, титан, цирконий и их сплавы.
2) возможна сварка во всех пространственных положениях;
3) процесс сварки, вероятность образования дефектов в котором
менее 1%;
4) не образуются вредные дымы и шлак в процессе работы;
5) широкий диапазон регулирования параметров режима сварки;
6) возможность вести сварку и с присадочной проволокой, и без
присадочной проволоки;
7) возможность автоматического управления напряжением на дуге.
В то же время в технологии орбитальной сварки есть и недостатки. В
их число входят:
1) сравнительно низкая производительность в сравнении с другими
видами дуговых процессов;
2) разработка технологии и режимов сварки требует больших
усилий;
3) более дорогое оборудование, требующее наибольшего ухода и
капитальных инвестиций в сравнении с оборудованием для ручной дуговой
сварки.
В работе планируется разработать способ сварки, при котором будут
автоматически меняться параметры напряжения дуги, когда масса сварочной
ванны будет приближаться к ее критическому значению.
Таким образом, решение задач, связанных с изучением особенностей и
контролем процесса с помощью программирования режимов автоматической
аргонодуговой сварки является актуальным и своевременным [1].
Целью данной работы является разработка процесса орбитальной
сварки корневого слоя труб поверхностного нагрева с программированием
режима сварки.
Для достижения поставленной цели необходимо решить следующие
задачи:
1) Произвести анализ современного состояния орбитальной сварки
труб поверхностного нагрева.
2) Разработать модель комплекса сил, действующих на сварочную
ванну;
3) Разработать способ сварки корневого слоя для труб малых
диаметров при орбитальной сварке;
4) Разработать экспериментальную установку.
5) Провести проверку.
1 Обзор литературы
Проведя анализ действия равнодействующей силы относительно
положения сварочной головки, сравнив эти значения с действием веса
сварочной ванны, можно сделать вывод, что для каждого конкретного
положения (потолочное, вертикальное, нижнее) требуется уделить внимание,
так как в каждом определенном случае встречается своя проблема –
провисание сварочной ванны для потолочного положения, стекание в
положении сверху-вниз при выбранном нами направлении сварки против
часовой стрелки, отвисание при нижнем положении сварки и отставание при
сварке снизу-вверх.
На основании литературного обзора и инженерных расчетов был
подобран такой режим сварки и построена модель комплекса сил,
действующая на сварочную ванну, чтобы можно было проследить влияние
каждой из сил, входящих в комплекс и сделать вывод о значимости каждой
для любого пространственного положения.
После построения модели комплекса сил, действующих на сварочную
ванну, был разработан процесс орбитальной сварки, благодаря которому
можно управлять критической массой сварочной ванны.
Так же был проведен эксперимент с двумя образцами труб, сваренными
разными способами сварки (РД и импульсная орбитальная сварка с
программированием режима сварки). Результат эксперимента показал, что
образец, сваренный разработанным способом сварки, имеет гораздо меньшее
количество дефектов.
Результаты работы в полной мере показывают необходимость
продолжения исследований по данной теме, так как совершенствование
технологии орбитальной сварки в последствии может найти применение для
массового производства труб в бытовом и промышленном масштабах.
Внедрение разработанной технологии в производство возможно после
проведения опытов и различных видов контроля.
1.Справочник по орбитальной сварке Polysoude. Искусство сварки,
Полисуд С.А.С. (Франция), 2009, 56 с.
2.Третьяков Е. С., Коберник Н. В. Технологии автоматической
орбитальной сварки трубопроводов малого диаметра из углеродистых и
низколегированных сталей. // Машиностроение. – 2013. – №6. – С. 31-37.
3.Полосков С. И., Букаров В. А. Особенности управления
формированием корня шва при орбитальной сварке неповоротных стыков
труб. // Сварочное производство. – 2003. – №4. – С. 3-11.
4.Ерохин А. А. Основы сварки плавлением. Физико-химические
закономерности. – М.: Машиностроение, 1973. – 448 с.
5.Полосков С. И., Ищенко Ю. С. Анализ факторов, определяющих
формирование сварочной ванны при орбитальной сварке неповоротных
стыков труб. // Сварочное производство. – 2003. – №2. – С. 11-19.
6.Daehyun B., Hyeong S., Sang-Hu P. Development of an automatic
orbital welding system with robust weaving width control and a seam-tracking
function for narrow grooves // The International Journal of Advanced Manufacturing
Technology. – 2017. – №93. – С. 767-777
7.СемёновА.П.Методыматематическогомоделирования
процессов формирования и переноса капель электродного металла при сварке
плавящимся электродом (Обзор). // Автоматическая сварка. – 2014.
– №10. – С. 3-11.
8.Baeva M., Uhrlandt D. Nonequilibrium simulation analysis of the
power dissipation and the pressure produced by TIG welding arcs // Welding in the
World. – 2019. – №2. – С. 377-387.
9.Lohse M., Trautmann M., Siewert E. Predicting arc pressure in GTAW
for a variety of process parameters using a coupled sheath and LTE arc model //
Welding in the World. – 2018. – №62. – С. 629-635.
10. Poloskov, S. I., Ishchenko, Y. S. & Bukarov, V. A. Analysis of factors
determining the formation of the weld pool in the orbital welding of non-rotating
joints in pipes. // Welding in the World. – 2003. – №17. – С. 557-564.
11. Goldschmitz M., Karlsson L., Pedersen R. Developments in the
welding of supermartensitic stainless steels: recent developments and applications.
// Welding International. – 2004. – №18. – С. 543-549.
12. Poloskov S. I., Ishchenko Yu. S. & Bukarov V. A. Minimising the
probability of formation of external defects in welded joints in the process of
automatic orbital welding // Welding International. – 2004. – №18. – С. 216-222.
13. Князьков А. Ф., Веревкин A. B., Князьков С. А. Особенности
удержания сварочной ванны в положениях отличных от нижнего. // IV
Международная научно-техническая конференция «Современные проблемы
машиностроения» г. Томск Изд-во ТПУ, – 2008. – С. 323-328.
14. ЯкубовичД.И.Влияниеповерхностногонатяженияна
формирование сварочной ванны при сварке на весу тонколистового металла.
// Сварочное производство. – 2004. – №10. – С. 17-20.
15. Горшкова О.О. Орбитальная сварка трубопроводов. // Modern
High Technologies. – 2021. – №1. – С. 20-24.
16.Шипилов А.В., Ерофеев В.А. Физико-математическая модель
процесса орбитальной сварки неплавящимся электродом в инертных газах:
концепция и возможности. // Сварка и диагностика. – 2011. – №2. – С. 3-9.
17. ЧигаревВ.В.,СеровИ.В.Исследованиевзаимодействия
компонентов ванны при сварке деталей металлургического оборудования.
// Захист металургійних машин від поломок. – 2005. – №8. – С. 214-223.
18. LI X.R., ZHANG Y.M. Monitoring and Control of Penetration in
GTAW and Pipe Welding. // Welding Journal. – 2013. – №92. – С. 190-196.
19. Mamvura T.A. The impact of pipe geometry variations on hygiene and
success of orbital welding of brewing industry equipment. // Journal of The Institute
of Brewing. – 2017. – №123. – С. 81-97.
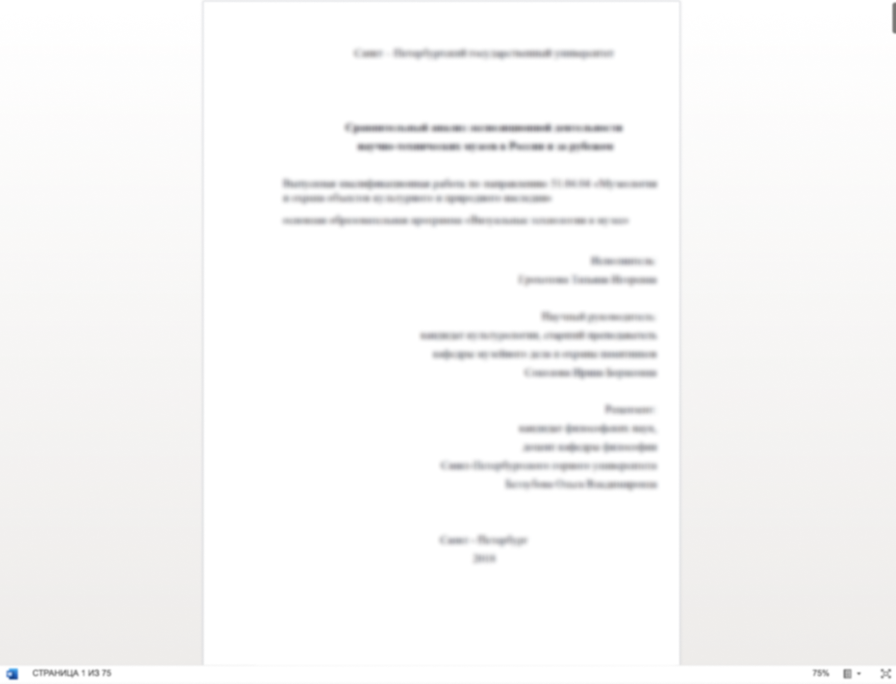
Хочешь уникальную работу?
Больше 3 000 экспертов уже готовы начать работу над твоим проектом!