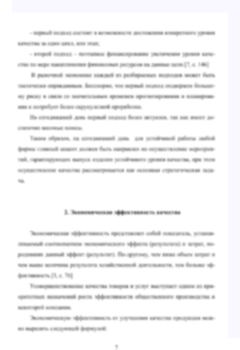
Влияние технологических параметров процесса азотирования на упрочнение стальной поверхности
Целью исследовательской работы является разработка и применение на практике нового вида химико-термической обработки–электродуговое азотирование для улучшения эксплуатационных свойств, которое станет одним из превалирующих процессов обработки материалов и изделий. Для достижения указанной цели нами были поставлены и решены следующие задач: установить влияние выбранной для исследования термической обработки на исходное структурное состояние изучаемой стали, выбрать необходимые параметры обработки- диапазоны технологических параметров азотирования (температуры, составы насыщающих сред, продолжительность насыщения), позволяющие в широком интервале целенаправленно варьировать фазовый состав упрочненного слоя.
Введение……………………………………………………………………….10
1. Основные виды и технологии азотирования сталей……………..…13
1.1. Азотирование сталей……………………………………………13
1.2. Основные технологии азотирования сталей и сплавов………14
1.3. Процессы формирования структуры азотированной зоны в
конструкционных сталях……………………………….………16
1.4. Азотирование в тлеющем разряде…………………………….19
1.5. Использование дуговых разрядов для азотирования
материалов…………………………………………………….…22
1.6. Свойства азотированных сталей…………………………….…23
2. Оборудование для азотирования сталей, материалы и методика
исследований……………………………………………………..27
2.1. Оборудование для азотирования сталей в дуговом
разряде……………………………………………………………27
2.2. Материалы для исследования…………………………………..32
2.3. Технология подготовки образцов к испытаниям и
исследованиям……………………………………………………33
2.4. Измерение микротвердости…………………………………..…35
2.5. Метод оптической металлографии…………………….……….38
3. Исследование температурно-временных характеристик …………..41
3.1. Описание процесса азотирования на модернизированной установке
«ННВ-6.6-И1»………………………………………………………..…41
3.2. Изготовление дополнительного источника нагрева…..………….47
3.3. Влияние напряжения смещения на динамику нагрева
образца……………………………………………………….……53
4. Исследование параметров азотированных слоев и определение
оптимальных режимов азотирования ………….……………………57
4.1. Параметры и схема эксперимента …………… ……………..….57
4.2. Измерение микротвердости поверхностного слоя после
азотирования при смещениях 400В, 600В, 900В …………….59
4.3. Измерение толщины нитридной зоны азотированных образцов
при смещениях 400В, 600В, 900 ………………………………..60
4.4. Влияние режима азотирования на качество модифицированного
слоя….……..………………….……….……………………………62
5. Финансовый менеджмент, ресурс эффективность………………………71
5.1. SWOT-анализ….………………….…….……………………………72
5.2. Инициация проекта….……….………………………………………74
5.2.1. Организационная структура проекта ……..……………………75
5.3. Ограничения и допущения проекта …….………………………76
5.3.1. Бюджет научного проекта …….….………………………………77
5.3.2. Отчисления на социальные нужды …….………………………79
5.3.3. Затраты на электроэнергию ……..…….…………………………79
5.3.4. Затраты на водоснабжение …….…….…….………………………80
5.3.5. Затраты на водоотведение …….….…….…………………………80
5.3.6. Полная смета затрат на выполнение НИР …….…….……………80
5.3.7. Расчет прибыли …….…….….…….………………………………81
6. Социальная ответственность . …….…….…………………………82
6.1 Правовые и организационные вопросы обеспечения безопасности…84
6.2 Производственная безопасность …………………………87
6.2.1 Анализ опасных и вредных производственных факторов ………88
6.2.1.1 Превышение уровня шума …………………………………89
6.2.1.2. Вредные вещества ….……………………………………………90
6.2.1.3. Отклонение показателей микроклимата…………………………91
6.2.1.4. Отсутствие или недостаток естественного света. Недостаточная
освещенность рабочей зоны………………………………………………………92
6.2.1.5. Опасность поражения электрическим током…………………… 93
6.2.2. Обоснование мероприятий по снижению уровней воздействия
опасных и вредных факторов на исследователя…………………………………95
6.2.2.1 Превышение уровня шума…………………………………………95
6.2.2.2 Вредные вещества …………………………………………………95
6.2.2.3 Отклонение показателей микроклимата …………………………96
6.2.2.4. Отсутствие или недостаток естественного света. Недостаточная
освещенность рабочей зоны ……………………………………………………97
6.2.2.5. Опасность поражения электрическим током …………………98
6.3 Экологическая безопасность ………………………………………99
6.4 Безопасность в чрезвычайных ситуациях …………………………100
Заключение …..……………………………….………………………………..104
Список используемой литературы …………….…………………………….107
Приложение ……………………………………………………………………111
Основной технологической базой, определяющей развитие всей
промышленности любого государства является машиностроительная отрасль.
Поэтому темпы роста машиностроения должны в значительной мере превышать
аналогичные показатели других отраслей народного хозяйства. В настоящее
время в связи со сложностью выпускаемого технологического оборудования и
его стоимости машиностроение сильно отстает от научно-технического
прогресса. При конструировании и производстве современных машин и
оборудования одним из обязательных требований является увеличение его
производительности. Повышение загруженности и напряженности эксплуатации
машин во многом влияет на их надежность. Потеря работоспособности лишь у
одной детали достаточна для отказа машины в целом. Борьба с
преждевременным износом детали и инструмента в настоящее время
приобретает все большее значение, поэтому разрабатываются различные
способы химико-термической обработки для повышения их эксплуатационных
характеристик.
Актуальность. Работоспособность детали машин и инструмента во
многом определяется состоянием поверхностного слоя. С ростом требований к
качеству упрочненного слоя, к показателям экономической эффективности
процессов, к подбору материалов в зависимости от поверхностных свойств,
диффузионному слою, а также вследствие увеличения объемной доли
легированных сталей и сплавов в процессе производства деталей и инструмента,
становится актуальным применение ионного азотирования.
В последнее время все большее развитие и применение получают методы и
способы ионного азотирования. Они не только позволяют избавиться от
недостатков традиционных методов, но и получить ряд преимуществ:
возможность регулирования параметров обработки в широком интервале
режимов и за счет этого – структуры, фазового состава, твердости,
износостойкости, шероховатости; высокую скорость насыщения; высокий класс
чистоты поверхностей; большую экономичность процесса за счет значительного
сокращения общего времени обработки; повышение коэффициента
использования электроэнергии; процесс не токсичен и отвечает требованиям по
защите окружающей среды.
Причиной повышенного внимания к проблеме высокотемпературного
азотирования являются уникальные свойства поверхности изделия, которые
формируются в результате обработки. Поэтому актуальное значение
приобретает создание различных технологических вариантов ХТО, которые
позволяют регулировать заданную структуру и фазовый состав поверхностного
слоя, обеспечивающие оптимальные характеристики изделий.
Для преодоления вышесказанных недостатков и совершенствования
процесса в направлении увеличения скорости формирования упрочненного слоя,
ресурсосбережения, безопасности требуются новые технические решения. В
данной работе в качестве решения таких проблем был предложен дуговой
газовый разряд на основе безводородной плазмы, работающий при давлениях
насыщающей среды в 1000 раз меньше, чем у тлеющего разряда. Этот способ
позволяет сформировать диффузионные слои при температуре 550°С за 5-6
часов.
Целью исследовательской работы является разработка и применение на
практике нового вида химико-термической обработки – электродуговое
азотирование для улучшения эксплуатационных свойств, которое станет одним
из превалирующих процессов обработки материалов и изделий.
Для достижения указанной цели нами были поставлены и решены
следующие задач:
– установить влияние выбранной для исследования термической обработки на
исходное структурное состояние изучаемой стали;
– выбрать необходимые параметры обработки- диапазоны технологических
параметров азотирования (температуры, составы насыщающих сред,
продолжительность насыщения), позволяющие в широком интервале
целенаправленно варьировать фазовый состав упрочненного слоя;
– определить комплекс экспериментальных методов исследования, позволяющих
получить необходимую информацию о строении и свойствах выбранной стали
после термической обработки;
– экспериментально установить особенности строения упрочненного слоя, его
микроструктуру, фазовый состав и толщину.
Объект исследования – технологический процесс электродугового
азотирования и его влияние на структуру стали, изменение прочностных
характеристик.
Предмет исследования – физико-термические процессы формирования
диффузионных упрочняющих слоев на поверхности стали марки 40Х.
Научная новизна работы состоит в совершенствовании на основе
теоретических и экспериментальных исследований методом поверхностного
упрочнения выбранной стали путем применения нового вида азотирования.
Практическая значимость заключается в обосновании эффективной
технологии упрочнения стали, обеспечивающей высокие эксплуатационные
свойства, в частности износостойкость и твердость.
Разработанная технология отличается высокой эффективностью, не
требует использования дорогих и дефицитных материалов, а также отвечает
требованиям экологической безопасности.
1 Основные виды и технологии азотирования сталей
1. Лахтин Ю. М. Химико-термическая обработка металлов / Ю. М. Лахтин, Б.
Н. Арзамасов. – М.: Металлургия. – 1985. – 256 с.
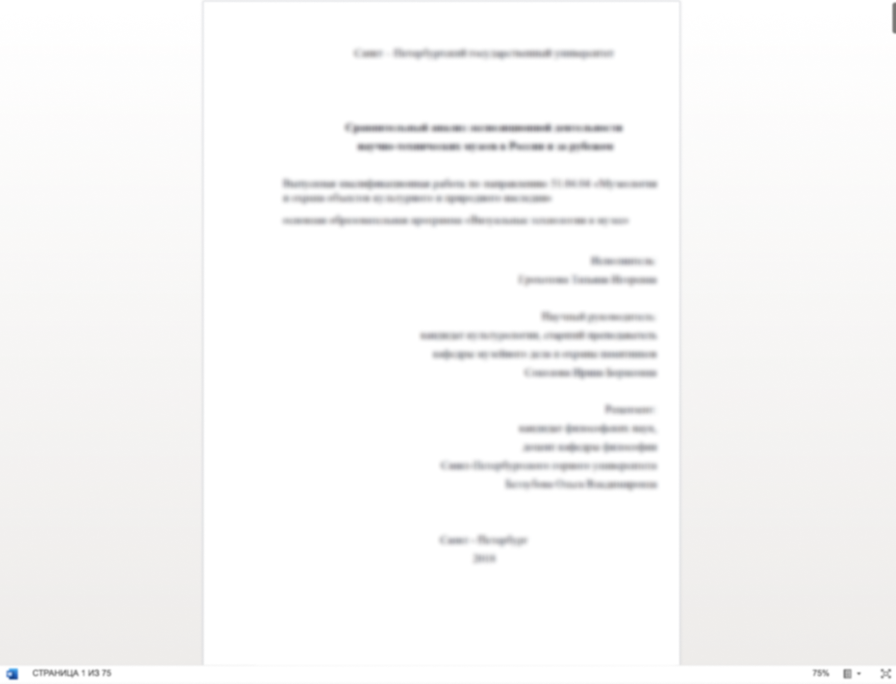
Хочешь уникальную работу?
Больше 3 000 экспертов уже готовы начать работу над твоим проектом!