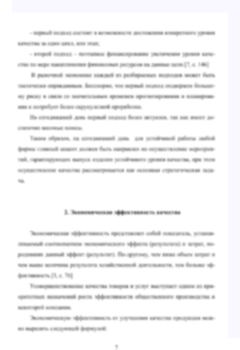
Влияние коррозионной среды и высокоэнергетических воздействий на прочность, прерывистую деформацию и разрушение алюминий-магниевых сплавов
Введение……………………………………………………………………………………. 4
Глава 1. Литературный обзор…………………………………………………………… 9
1.1. Виды коррозии………………………………………………………………………. 9
1.2. Коррозионные свойства промышленных алюминиевых сплавов……………….. 15
1.3. Механизмы коррозионного растрескивания под напряжением….………………. 16
1.4. Моделирование коррозионных процессов………………………………………… 20
1.4.1. Основы коррозионной кинетики……………………………………………….. 20
1.4.2. Самоорганизация коррозионных процессов…………………………………… 25
1.5. Лазерная обработка поверхности и коррозионные свойства алюминиевых
сплавов……………………………………………………………………………… 27
1.5.1. Взаимодействия лазерного излучения с металлами…………………………… 27
1.5.2. Особенности лазерной обработки алюминия и его сплавов…………………. 30
1.5.3. Нанесение антикоррозионных покрытий c помощью лазерных технологий.. 31
1.6. Постановка задачи исследования…………………………………………………… 34
Глава 2. Влияние коррозионной среды на прерывистую деформацию
и разрушение алюминий-магниевого сплава……………………………… 36
2.1. Экспериментальные исследования влияния коррозионной среды
на прерывистую ползучесть сплава АМг6………………………………………… 36
2.1.1. Инициация пластической неустойчивости локальным воздействием
агрессивной среды на поверхность деформируемого сплава ………………… 38
2.1.2. Акустический отклик на воздействие коррозионной среды………………….. 38
2.1.3. Микроструктурные исследования коррозионного питтинга…………………. 43
2.2. Моделирование влияния коррозионной среды на механическую
неустойчивость алюминиевого сплава…………………………………………….. 43
2.2.1. Модель растворения поликристаллического металла в жидкой среде……… 43
2.2.2. Морфологический переход от евклидовой к фрактальной морфологии
коррозионного фронта………………………………………………………….. 50
2.2.3. Моделирование скорости коррозионного разрушения……………………….. 52
2.2.4. Пространственное распределение концентраторов напряжения в условиях
стресс-коррозии………………………………………………………………… 59
2.2.5. Исследование скрытых корреляций в структуре внутренних напряжений.
Модель потери механической устойчивости в условиях стресс-коррозии…. 61
2.3. Выводы……………………………………………………………………………….. 67
Глава 3. Моделирование коррозии после лазерной обработки
поверхности алюминиевого сплава…………………………………………. 69
3.1. Моделирование температурного и упругого полей в ходе формирования
лазерного кратера…………………………………………………………………… 69
3.1.1. Модель воздействия лазерного излучения на поверхность сплава АМг6…… 69
3.1.2. Результаты моделирования и их обсуждение…………………………………. 73
3.2. Моделирование коррозии алюминиевого сплава после импульсной лазерной
обработки……………………………………………………………………………. 81
3.2.1. Модель коррозионного разрушения с учетом остаточных напряжений…… 81
3.2.2. Результаты моделирования коррозии после лазерной обработки
поверхности алюминиевого сплава…………………………………………… 82
3.3. Выводы……………………………………………………………………………….. 86
Глава 4. Исследование влияния лазерной обработки на коррозионную
устойчивость и прерывистую деформацию алюминий-магниевых
сплавов…………………………………………………………………………………… 88
4.1. Особенности методики обработки поверхности алюминиевого сплава
импульсным ИК-лазером………………………………………………………….. 88
4.2. Исследование влияния лазерной обработки на полосообразование
и механическую неустойчивость алюминиевого сплава…………………….. 91
4.2.1. Влияние лазерного укола на полособоразование……………………………… 91
4.2.2. Влияние лазерного укола на эффект Портевена-Ле Шателье………………… 99
4.3. Методика нанесения антикоррозионного покрытия на поверхность
алюминиевого сплава……………………………………………………………….. 102
4.4. Выводы………………………………………………………………………………. 107
Глава 5. Действие импульсного тока на зарождение полос деформации,
влияющих на коррозионное свойства алюминий-магниевых сплавов… 108
5.1. Экспериментальное исследование влияния пульсирующего тока на
образование деформационных полос в сплаве АМг6…………………………….. 108
5.2. Модель взаимодействия тока с частицами вторичной (Al3Mg2)-фазы………… 111
5.2.1. Формулирование модели………………………………………………………… 111
5.2.2. Результаты моделирования растворения током частиц -фазы
в сплаве АМг6…………………………………………………………………… 115
5.2.3. Электрохимический механизм подавления током деформационных полос… 126
5.3 Выводы………………………………………………………………………………… 127
Заключение………………………………………………………………………………… 129
Список литературы………………………………………………………………………. 131
Приложение………………………………………………………………………………… 140
В первой главе представлен обзор литературы по тематике диссертационного исследо-
вания: виды коррозии металлов, механизмы стресс-коррозии, межкристаллитная и транскри- сталлитная коррозия, влияние коррозии на важнейшие механические свойства металлов, а также влияние на коррозионные свойства алюминиевых сплавов предварительной лазерной обработки поверхности. Кратко изложены методы математического моделирования коррози- онных процессов и взаимодействия лазерного излучения с металлами.
Во второй главе представлены основные результаты исследования влияния коррозион- ной среды на прерывистую деформацию и разрушение алюминий-магниевого сплава.
В первом разделе изложены результаты экспериментального изучения влияния коррози- онной среды на прерывистую ползучесть алюминий-магниевого сплава АМг6 (Al − 6.15 мас. %Mg − 0.65 мас. % Mn − 0.25 мас. % Si − 0.21 мас. % Fe). В качестве коррозионной среды ис- пользовали 30%-й раствор соляной кислоты. Исследовали силовой, деформационный и аку- стоэмиссионный отклики на локальное действие кислоты на поверхность деформируемого сплава комплексом in situ методов исследования динамики деформационных полос с помо- щью высокоскоростной цифровой видеокамеры FASTCAM Mini UX50/100 (Photron), быстро- действующих датчиков измерения деформации (Riftec) и усилия (Zemic). Измерение акусти- ческого отклика в низкочастотном диапазоне 1-20 кГц проводили с помощью акустического датчика АР34 («ГлобалТест») Д1 и в высокочастотном диапазоне ~ 20-800 кГц с помощью акустоэмиссионного датчика Zetlab BC 601 (Д2). Испытания проводили в горизонтальной деформационной машине. Образцы нагружались одноосным растяжением в две последова- тельные стадии: стадии нагружения со скоростью 1.5 МПа/с до момента времени, соответ- ствующего приложенному напряжению 0 200 МПа и стадии ползучести при напряжении
0 const.Спустявремя~30снарабочуюповерхностьдеформируемогообразцананосилась
капля 30%-го раствора соляной кислоты, которая, растворяя оксидную поверхностную плен- ку Al2O3, активно реагирует с алюминием в соответствие с реакцией
2Al6HCl2AlCl3 3H2. (1)
В результате химического растворения локального участка поверхности через времен- ной интервал ~ 10 с деформируемый образец теряет механическую устойчивость и на его по- верхности развивается сложная структура деформационных полос, которая сопровождается макроскопическим скачком пластической деформации − ступенью на кривой ползучести ам- плитудой 1-3 % (рис. 1).
Таким образом, экспериментально установлено, что химический процесс растворения локального участка поверхности деформируемого алюминиевого сплава в условиях ползуче- сти вызывает развитие макроскопической неустойчивости в виде скачка пластической де- формации амплитудой несколько процентов.
Типичный низкочастотный акустический сигнал U1(t), измеренный датчиком Д1, имеет два последовательных колоколообразных скачка: «маленький», связанный с падением капли кислоты на поверхность деформируемого сплава и последующий скачок амплитудой
Рис. 1. Скачок деформации (1) и соответ- ствующий силовой отклик (2), инициированный химическим воздействием капли 30 %-го раствора HCl на поверхность деформируемого в условиях пол- зучести сплава АМг6. На вставке показана первичная полоса деформации на поверхности сплава. Стрелкой отмечен момент нанесения капли кислоты.
Рис. 2. Низкочастотный U1 (а) и высокоча- стотный U2 (б) акустические отклики на процесс травления алюминиевого сплава АМг6 концен- трированным раствором соляной кислоты. На вставках − типичные осциллограммы сигналов АЭ на разных стадиях травления.
на ~ 1.5 порядка больше первого длительностью переднего фронта 5-6 с и временем спада около 30 с (рис. 2а). Высокоскоростная акустическая эмиссия U2(t), сопровождающая процесс растворения алюминиевого сплава, измеренная датчиком Д2, зарегистрирована в виде квази- непрерывного сигнала в полосе частот ~ 30-600 кГц (рис. 2б). По данным видеосъемки со скоростью 5000 кадр/с основными источниками сигналов АЭ является наиболее быстрые со- бытия в динамике пузырьков водорода: коалесценция двух и более пузырьков и «взрыв», т.е. разрыв пленки пузырьков. На последних стадиях травления наблюдаются высокоамплитуд- ные дискретные импульсы АЭ, вызванные «выстреливанием» отдельных капелек от «взрыва» пузырьков и их падения на поверхность сплава.
Во втором разделе главы представлены результаты моделирования влияния коррозион- ной среды на механическую неустойчивость алюминиевого сплава. Разработана математиче- ская модель растворения металла в жидкой агрессивной среде, учитывающая поликристалли- ческую структуру сплава, зависимость коррозионной прочности зерна от кристаллографиче- ской ориентации, подавление активности травителя вследствие его истощения в ходе процес- са травления; учитывалось также, что диффузионный перенос к фазовой границе раствор- металл происходит значительно быстрее растворения металла. Установлено, что в ходе трав- ления происходит морфологический переход от евклидовой (оптически гладкой) к фракталь- ной (шероховатой) границе коррозионного фронта с размерностью df =1.323 0.002, хорошо согласующейся по результатам микроструктурных исследований с размерностью фронта травления поверхности сплава АМг6 30%-ным раствором соляной кислоты (рис. 3).
Рис. 3. Временна́я эволюция поверхности в процессе коррозионного разрушения. “Кадры” получены после 100 (а), 1500(б), 2500 (в) итераций расчета. Черным цветом показан раствор кислоты. На рис. 3г представлен СЭМ- микроснимок реального коррозионного фронта, полученного травлением сплава АМг6 30%-м раствором HCl. Увеличение 12 .
Рис. 4. Временные зависимости от- носительной массы (1) растворенного
металла и интегрального акустического отклика (2)..
Полученную в численном эксперименте временную зависимость безразмерной раство- ренноймассыметалла(t)mt/m0 (гдеmt иm0 −зависящаяотвременииконечнаямасса
растворенного металла, соответственно) аппроксимировали уравнением Колмогорова- Джонсона-Мейла-Аврами (КДМА), которое используется для моделирования топохимиче- ских реакций [1]
(t) 1exp[(t /)n], (2)
где − постоянная времени коррозионного процесса, n − показатель Аврами. Статистическая обработка 20-ти численных экспериментов дает средний показатель Аврами n = 1.110.01. Уравнение (2) хорошо аппроксимирует также интегральный акустический отклик (t), по- лученный интегрированием низкочастотного акустического сигнала U1(t) (см. Рис. 2а) в виде
Рис. 4 демонстрирует хорошую корреляцию между растворенной массой (t) и интеграль- ным низкочастотным откликом (t) с коэффициентом корреляции 0.9891. Эта корреляция
соответствует уравнению химической реакции (1) растворения алюминия в концентрирован- ной кислоте, из которой следует, что выход водорода пропорционален количеству растворен- ных ионов алюминия. Акустический отклик, источником которого по данным видеосъемки является «взрыв» пузырьков водорода, таким образом, несет информацию о кинетике корро- зии алюминия в растворе HCl.
В третьем разделе главы исследуется влияние фрактальной морфологии коррозионного фронта на механическую неустойчивость сплава в условиях стресс-коррозии. Методом ко- нечных элементов рассчитывали поле упругих напряжений в деформируемом металле с
t t 010
(t) U(t)dt trU(t)dt . (3)
8
фрактальной поверхностью, образованной в результате коррозионного воздействия кислоты. Упругие напряжения рассчитывали по формуле Мизеса [2]
1 / 2
[()2()2()2]/2 , (4)
(где 1 , 2 , 3 − главные напряжения) при помощи программной платформы COMSOL
Multiphysics. На рис. 5 показана типичная картина пространственного распределения упругих напряжений вблизи фрактальной поверхности деформируемого образца. Как и ожидалось, выступающие «фьорды» являются концентраторами напряжений в материале, в то же время “полуострова” оказываются разгруженными вследствие их экранирования фьордами. Оче- видно, представляет интерес расчет значений K в вершинах фьордов для оценки простран- ственного распределения потенциальных дислокационных источников и микротрещин. Рас- пределение расчетных коэффициентов K вдоль длины L фрактальной границы деформируе- мого материала представлено на рис. 6а. Как видно, структура зависимости K(L) имеет внеш- ние признаки фрактальности и самоподобия.
Исследование скрытых корреляций в пространственной структуре внутренних напряже- ний проводили методами статистического и фрактального анализа. Для проведения статисти-
ческого анализа строили функцию распределения D(s) N 1dN / ds нормированного коэф-
фициента концентрации напряжений s K / K , где N − общее количество концентраторов напряжения, K − среднее значение K для всей выборки. Из рис. 6 следует, что зависимость
lgD от lgs является приблизительно линейной с коэффициентом наклона = 1.0385. Это означает, что статистическая функция распределения коэффициентов концентрации напря-
жений подчиняется степенному закону D(s) ~ s (Рис. 6б). Статистическое распределение отрезков L между позициями на фрактальной границе также демонстрирует скейлинговую
форму D(L) ~ L с показателем степени = 0.5264 (Рис. 6в).
Рис. 5. Типичная расчетная картина полей напряжений вблизи фрактального коррозионного фронта. 9
M122313
Рис. 6. Пространственное распределение локальных концентраторов напряжения с коэффициентом концентрации напряжения K(L) вдоль границы коррозионного фронта в условиях коррозии под растягиваю- щем напряжением (а), гистограмма коэффициентов концентраций упругих напряжений K вдоль границы L коррозионного фронта (б), гистограмма отрезков L между концентраторами (в). На вставках показаны плот- ности статистического распределения нормализованного коэффициента концентрации s и расстояния L между концентраторами в двойных логарифмических координатах. Штриховые линии показывают отрица- тельные склоны этих распределений, которые равны – 1.0385 и – 0.5264 для распределений s и L , соответ- ственно. (г) и (д) − результаты расчета показателя Херста.
Скейлинговые законы для D(s) и D(L) указывают на состояние самоорганизующейся
критичности [3], которое характеризуется дальнодействующими корреляциями между боль- шим числом концентраторов упругих напряжений. Этот вывод подтверждается результатами фрактального R/S анализа по методу нормированного размаха Херста [4] с помощью выра-
жения: R/S ~ H , где R( ) − накопленное отклонение (размах) зависимости K(L) от среднего на отрезке вдоль береговой линии, S ( ) − стандартное отклонение функции K(L) на отрез-
ке , Н − показатель Херста, а фрактальная размерность этой функции d f 2 H .
На рис. 6г показана зависимость нормированного размаха R/S от величины (мкм) в двойных логарифмических координатах. Линейная аппроксимация этой зависимости дает среднее значение показателя Херста H = 0.72 и среднюю фрактальную размерность
df = 1.28. Степень мультифрактальности оценивали, как размах фрактальной размерности
df max df min . Для этого длину границы коррозионного фронта разбивали на части и рассчи-
тывали локальные показатели Херста. Пространственные вариации локального показателя Херста показаны на рис. 6д, из которого следует, что размах d f max d f min = 0.05. Таким обра-
зом, зависимость K(L) имеет почти монофрактальную структуру с размерностью d f = 1.28 0.05 и степенью мультифрактальности около 4 %. Отметим, что для случайного
процесса показатель Херста Н = 0.5. Значение H =0.72 указывает на то, что статистика коэф- фициентов напряжения значительно отличается от гауссовой и дополнительно указывает на наличие корреляций между концентраторами напряжения.
Из результатов моделирования следует, что в условиях стресс-коррозии локальные напряжения в области коррозионного пятна превышают на один-полтора порядка уровень приложенного напряжения ползучести. Если напряжение ползучести сопоставимо или боль- ше условного предела текучести поликристаллического сплава, то локальные напряжения в приповерхностном слое коррозионного пятна могут значительно превышать напряжения сра- батывания дислокационных источников, что с учетом выявленных дальнодействующих кор- реляций между концентраторами напряжения может спровоцировать коллективное срабаты- вания этих источников и развитие макроскопической дислокационной лавины, которая вызы- вает скачок деформации на кривой ползучести.
Третья глава посвящена моделированию коррозии алюминиевого сплава после лазер- ной обработки поверхности.
В первом разделе главы сформулирована модель локального воздействия импульсного лазерного излучения на поверхность алюминиевого сплава. Рассмотрено локальное воздей- ствие высокоинтенсивного лазерного излучения на поверхность алюминий-магниевого спла- ва. Показано, что лазерный луч мощностью 20 Вт, сфокусированный в пятно с гауссовым ра- диусом 50 мкм, «пробивает» образец алюминий-магниевого сплава толщиной 0.5 мм за 17.2 мс. При меньшей длительности лазерного импульса на поверхности сплава образуется кратер в форме полуэллипсоида (рис. 7). Получены пространственные распределения температуры, ее градиента, тепловых потоков и механических напряжений в различные моменты времени, а также пространственное распределение остаточных напряжений, возникновение которых обусловлено тепловой дилатацией и скачком удельного объема в процессе кристаллизации жидкой фазы.
Рис. 7. Профиль кратера, сформированно- го в процессе лазерного воздействия на алюми- ний-магниевый сплав АМг6 лазерным излуче- нием мощностью 20 Вт, сфокусированным в пятно радиусом 50 мкм за 16.8 мс.
Во втором разделе главы изложены резуль- таты моделирования коррозии поверхности алюминий-магниевого сплава, подвергнутой импульсной лазерной обработке. Численные исследования проводись с помощью дискрет- ной модели на основе клеточного автомата, разработанной во второй главе диссертации. Эта модель была модифицирована учетом вли- яния на скорость коррозии остаточных напря- жений вследствие механо-электро-химического эффекта, состоящем в снижении химического потенциала сплава на величину энергии де- формации, что приводит к росту анодного тока растворения [5].
В рассматриваемой модели принималась, согласно [6], линейная связь между локальной скоростью растворения и механическим напряжением М , что учитывалось линейным уменьшением коррозионной прочности ячеек
твердого тела с ростом локального напряжения как w w0 (1 k M / max ) , где w0 − коррози-
онная прочность ячеек в отсутствие механических напряжений, max − предел прочности
сплава, а 0 k 1 − параметр, зависящий от остаточных напряжений: при k = 0 остаточные
напряжения отсутствуют вследсвие термообработки сплава после лазерной обработки, при k =1 остаточные напряжения не снимались термообработкой, а случай 0 k 1 соответ-
ствует частичному снятию остаточных напряжений. Для того, чтобы исследовать влияние коррозионной среды на поверхность кратера, остальная (плоская) поверхность сплава по- крывалась в модели защитным покрытием, устойчивым к коррозии (белая область на рис. 8 а). Раствор кислоты, помеченный на рис. 8 черным цветом, полностью заполняет кратер. Рас- чет проводили при различных уровнях остаточных напряжений после лазерной обработки, задаваемых параметром k 1 =1, k 2 = 0.5, k 3 = 0.
Результаты расчетов, иллюстрированные на рис. 8, показывают, что по мере снятия остаточных напряжений после лазерной обработки уменьшается объем растворенного метал- ла и увеличивается количество кластеров (островков), полностью окруженных раствором кислоты. Для сравнения на рис. 9 представлены временные зависимость растворенной массы
mt для трех рассматриваемых случаев. Как видно, скорость коррозии возрастает с ростом остаточных напряжений и у образца, не прошедшего термообработку после лазерного воз-
действия ( k 1 = 1), общая растворенная масса на 15 % выше, чем у образца с k 2 = 0.5 и на 18 % выше, чем у образа без остаточных напряжений k 3 = 0.
Общее снижение коррозионной прочности привело к уменьшению локальной неодно- родности ячеек твердого тела, что проявилось в менее шероховатой фазовой границе и сни- жении количества кластеров, окруженных раствором кислоты. Несмотря на то, что начальная геометрия поверхности с лазерным кратером отличается от плоской, конечная фрактальная размерность для образца, в котором отсутствовали механические напряжения, также
Рис. 8. Результаты моделирования коррозионного разрушения для образцов, ранее подвергнутых лазер- ному воздействию. а – начальная конфигурация моде- ли, б-г − конечные структуры коррозионного фронта при различных уровнях остаточных напряжений: б − k 1 = 1; в − k 2 = 0.5; г − k 3 = 0.
Рис. 9. Уменьшение массы mt в процессе коррозионного растворения для образцов, подвергнутых лазерному воздействию при разном уровне остаточных напряжений, задаваемых параметром k : 1 − k 1 = 1; 2 −
k 2 = 0.5; 3 − k 3 = 0.
оказалась равной 1.33 ± 0.01, что является вполне логичным. Конечная фрактальная размер- ность для образца, с частичным снятием остаточных напряжений оказалась равной 1.30 ± 0.01 (ниже на 2%), а для образца без термической обработки – 1.28 ± 0.01 (ниже на 3.75%).
Таким образом, учет механо-электрохимического эффекта приводит к росту скорости коррозии образца, ранее подвергнутого лазерному излучению, по сравнению с образцом, по- верхность которого не была обработана лазерным излучением. Увеличение скорости корро- зии носит неравномерный характер и связан преимущественно с неоднородным простран- ственным распределением остаточных напряжений, которые возникают в процессе лазерного воздействия и последующего остывания металла. Показано, что для образцов, подвергнутых ранее высокоинтенсивному лазерному воздействию, термическая обработка, снимающая остаточные напряжения, увеличивает общую коррозионную прочность образцов.
В четвертой главе приведены результаты экспериментальных исследований влияния лазерной обработки на прочность, коррозионную стойкость и прерывистую деформацию сплавов Al-Mg.
В первом разделе главы описана разработанная экспериментальная методика обработки поверхности алюминиевого сплава импульсным ИК-лазером и методика высокоскоростного исследования динамики деформационных полос и скачков напряжения на деформационной кривой, вызванных импульсом волоконного иттербиевого ИК-лазера. С помощью разрабо- танной методики проведено экспериментальное исследование влияния импульсов ИК-лазера на прерывистую деформацию и полосообразование сплава АМг6. Результаты этого исследо- вания изложены во втором разделе главы.
Наиболее чувствительной к локальному лазерному воздействию оказывается область вблизи критической деформации c появления первого скачка на деформационной кривой.
По характеру инициации лазерным импульсом полосы деформации, вызывающей скачок раз- грузки, можно выделить две различные ситуации: 1) формирование полосы после окончания лазерного импульса, когда позиция лазерного укола и источник полосы не совпадают и нахо- дятся зачастую на противоположных боковых поверхностях плоского образца; 2) формиро- вание полосы деформации происходит во время лазерного импульса, а источник полосы находится непосредственно в зоне термического влияния. Первая ситуация типична для сравнительно небольших значений критической деформации c 1-2 %, и соответственно
низких напряжениях ~ 180-220 МПа, которые реализуются при скоростях деформирования
~ 10-3-10-4 c-1 при комнатной температуре. Для инициации полосы деформации достаточно сравнительно небольшие плотности энергии лазерного излучения ~ 30 Дж/см2. Вторая си-
0
туация характерна для больших критических деформаций c > 5 % и соответствующих
больших напряжений 280-300 МПа и плотностях энергии 100 Дж/см2.
На рис. 10 представлены данные видеосъемки со скоростью 10 000 кадр/с процесса за- рождения и роста полосы деформации, инициированной лазерным импульсом. Время роста полосы через все сечение образца составляет не более 300 мкс и полоса достигает проти- воположной боковой поверхности образца в момент окончания лазерного импульса. Воздей- ствие лазерного импульса сопровождается оптическим пробоем и образованием плазменного факела. Последний продолжает «выгорать» после окончания лазерного импульса еще около 1.5 мс. После выхода на противоположную поверхность полосы, формируется расширяюща- яся полоса, которая вызывает скачок разгрузки амплитудой 16 МПа и длительностью
около 1.5 мс, совпадающей с временем роста площади полосы.
В заключительной части главы изложены результаты экспериментального исследования
влияние лазерного воздействия на эффект Портевена-Ле Шателье (ПЛШ). В процессе растя- жения со скоростью 0 8104 c1 в испытательной машине Instron (3344) боковая поверх-
ность образца подвергалась одиночным лазерным уколам на разных стадиях упрочнения. По мере приближения к критической точке спонтанного появления первого скачка в отсутствие внешней воздействий (c 302 МПа, с = 12.5 %) материал становился всё более неустойчи-
вым по отношении к одиночному импульсному лазерному воздействию: если при напряже- нии = 200 МПа его влияние не заметно на кривой растяжения, то при = 270 МПа лазер- ный укол вызывает одиночный скачок разгрузки амплитудой около 5 МПа, за которым сле- дует гладкий участок кривой растяжения; наконец при cL 290 МПа, такой же лазерный
укол вызывает скачок разгрузки амплитудой 14 МПа, за которым следует зубчатая кри- вая ПЛШ до разрушения. При этом критическая деформация с уменьшается почти в полтора
раза (с 12.5 до 8.5 %), максимальное напряжение m почти не изменяется, а пластичность
(деформация до разрушения) падает в 1.2 раза (с 27 до 22.5 %).
Очевидно, лазерный укол играет роль лишь триггера развития макроскопической пла-
стической неустойчивости, по масштабу и продолжительности значительно превышающей
Рис. 10. Зарождение и рост по- лосы деформации, инициированной импульсом лазерного излучения мощностью 50 Вт и длительностью 0.8 мс, сфокусированным на боковую поверхность плоского образца сплава АМг6. Скорость видеосъемки 10 000 кадр/с. Числа − номера кадров.
инициирующее локальное импульсное воздействие: объ- ем зоны лазерного повреждения не превышает ~ 0.1 % объема образца, а длительность лазерного импульса не превышает ~ 10-5 продолжительности спровоцированной лазерным уколом прерывистой деформации. Следова- тельно, на гладком участке кривой деформации суще- ствует область неустойчивости по отношению к локаль- ному термическому (лазерному) импульсному воздей- ствию, начиная с некоторой критической деформации cL (2/3)c : при cL лазерный укол не оказывает
влияния на деформационное поведение материала или это влияние незначительно, а при cL такой же ла-
зерный укол провоцирует прерывистую деформацию ПЛШ, которая продолжается до разрушения образца.
Установлено, что даже одиночный лазерный укол длительностью до ~ 1 мс боковой поверхности деформи- руемого одноосным растяжением плоского образца сплава АМг6 может существенно (до 1.5 раза) умень- шить критическую деформацию появления первого скачка напряжения и спровоцировать преждевременное появление нескольких десятков скачков напряжения на кривой растяжения и, соответственно, полос деформации на поверхности металла. Показано, что это негативное явление может быть подавлено пропусканием через об- разец электрического тока малой плотности (~ 40 А/мм2), которое не только стабилизирует механическое поведе- ние сплава, но и увеличивает его пластичность почти в 1.2 раза при сохранении прочности на разрыв.
В главе 5 изложены результаты исследования электрохимического механизма действия импульсного электрического тока на прерывистую деформацию и зарождение деформацион- ных полос, негативно влияющих на коррозионные свойства алюминий-магниевых сплавов.
В первом разделе главы экспериментально исследуется влияние импульсного тока на прерывистую деформацию ПЛШ в сплаве АМг6. Особенность методики эксперимента состо- яла в разработанной и используемой системе обратной связи между акустическим сигналом − предвестником деформационного скачка − и генератором прямоугольного импульса электри- ческого тока, позволяющей пропускать импульсы тока заданной плотности и продолжитель- ности на разных стадиях эволюции деформационных полос.
В первой серии экспериментов генератор прямоугольных импульсов тока запускали от начального всплеска сигнала АЭ длительностью ~1 мс, вызванного зарождением деформаци- онной полосы. Установлено, что если постоянный ток плотностью j0 60 A/мм2 включается
сразу после зарождения полосы деформации, то он не оказывает заметного влияния на эво- люцию этой полосы и характеристики скачка напряжения, вызванного развитием данной по- лосы деформации. Поэтому причину эффекта подавления током прерывистой деформации
следует искать во влиянии тока на механизм зарождения деформационных полос. Для экспе- риментального изучения этого вопроса необходимо включать ток за некоторое время ttr до
ожидаемого скачка напряжения и измерять вероятность зарождения полосы деформации в зависимости от времени ttr , которое имеет смысл времени предварительной электротоковой
обработки металла до ожидаемого момента зарождения полосы.
Схема второй серии экспериментов состоит в следующем. На прерывистом участке кри-
вой деформации в отсутствие электротокового воздействия выбирается фрагмент содержа- щий 10-15 скачков напряжения и измеряется среднее время между скачками t . При задан- ных температурно-скоростных условиях эксперимента (0 3103 с-1, T 55 °C) это время
меняется от 1.0 с до 1.5 с с ростом деформирующего напряжения. Генератор импульса тока запускается от акустического сигнала по достижению величины всплеска сигнала АЭ некоторого порогового значения.
Статистический анализ попыток подавления очередного скачка прямоугольным импуль- сом тока амплитудой j0 60 A/мм2 показал, что при 0 ttr 0.3 с вероятность подавления
скачка напряжения равна нулю, при ttr 0.8 с эта вероятность близка единице, а в промежу- точнойобласти0.3сttr 0.8с,вероятностьподавлениямонотонновозрастаетот0до1.По-
этому, для подавления зарождения деформационных полос и, следовательно, скачков напря- жения необходима предварительная обработка данного сплава в течении не менее 0.8 с то-
ком плотностью не менее 60 A/мм2 (при 0 3103 с1 , T 55 °C). Предположительно это
время необходимо для растворения током преципитатов, образующихся на ранних стадиях старения сплава. Таким образом, экспериментально установлено, что электрический ток: а) подавляет процесс зарождения деформационных полос; б) не влияет на распространение полос, если зарождение произошло до включения тока. Из результатов работы следует, что электрический ток является примером селективного воздействия на процесс зарождения де- формационных полос и может быть использован для его изучения.
Во втором разделе главы представлены результаты моделирования взаимодействия тока
с частицами вторичной (Al3Mg2)-фазы в сплаве Al-Mg. Установлено, что под действием
диффузионного потока электромиграции, направленного против градиента плотности элек- трического тока, происходит растворение частицы включения преимущественно в направле- нии перпендикулярном току. Получены пространственные распределения концентрации ионов магния и плотности тока в области включения в различные моменты времени. Рассчи- таны зависимости характерного времени растворения от размера, формы и ориентации вклю- чений. Установлено, что время растворения частиц размером 150-250 нм находится в диапа- зоне 0.35-0.7 с после включения тока, которое хорошо согласуется с результатами электрото- ковых экспериментов и данными электронно-микроскопических исследований.
В третьем разделе главы на основе проведенных экспериментальных и теоретических исследований предложен электрохимический механизм подавления деформационных полос, вызывающих прерывистую деформацию алюминий-магниевого сплава, состоящий в раство- рении током частиц вторичной (Al3Mg2)-фазы − сильных стопоров движению дислокаций, − что вызывает гомогенизацию пластического течения и препятствует развитию макроскопи- ческих дислокационных лавин.
16
ЗАКЛЮЧЕНИЕ
1. Разработан комплексный подход к изучению влияния коррозионной среды и высокоэнер- гетических воздействий на механическую неустойчивость металлических сплавов, основан- ный на сочетании экспериментальных in situ исследований кинетики коррозии и кинетики локализации пластической деформации с методами математического моделирования процес- сов коррозии и электрохимического взаимодействия электрического тока выделениями вто- ричных фаз в деформируемых сплавах.
2. Экспериментально установлено, что химический процесс растворения концентрированной соляной кислотой локального участка поверхности деформируемого алюминий-магниевого сплава вызывает: а) генерирование широкополосного, в полосе от 0.1 Гц до 600 кГц, сигнала акустической эмиссии, обусловленного динамикой и разрушением многочисленных пузырь- ков водорода, образующихся в ходе коррозионного процесса; б) зарождение полос локализо- ванной пластической деформации, вызывающих развитие скачка деформации на кривой пол- зучести.
3. Разработана модель растворения поликристаллического металла в агрессивной жидкой среде. На основе численного расчета эволюции формы коррозионного фронта выявлен и экс- периментально верифицирован морфологический переход от евклидовой к фрактальной гео- метрии фазовой границы. Показано, что коррозия поликристаллического металла в жидкой агрессивной среде представляет новый пример топохимического процесса, кинетика которо- го описывается статистическим распределением Колмогорова-Джонсона-Мейла-Аврами.
4. Установлена корреляция между временной зависимостью растворенной массы металла и интегральным акустическим откликом, зарегистрированным в ходе травления алюминиевого сплава раствором соляной кислоты. Показано, что акустический отклик на коррозионный процесс несет информацию о кинетике растворения алюминия в соляной кислоте и может быть использован для разработки экспресс-метода контроля скорости коррозии и исследова- ния ее стадийности.
5. Предложен механизм потери механической устойчивости при коррозионном воздействии на поверхность деформируемого алюминиевого сплава на основе расчета полей упругих напряжений вблизи фрактальной границы коррозионного пятна. Показано, что в условиях коррозии под напряжением локальные напряжения превышают в 10-30 раз уровень прило- женного напряжения, что может спровоцировать коллективное срабатывание источников дислокаций и развитие макроскопической дислокационной лавины, которая вызывает скачок деформации на кривой растяжения.
6. Разработана модель коррозионного разрушения алюминиевого сплава, обработанного им- пульсом лазерного излучения. Показано, что остаточные напряжения ускоряют коррозию вслед- ствие механо-электрохимического эффекта, а термообработка, снимающая остаточные напряже- ния увеличивают коррозионную стойкость сплава после лазерной обработки. Для сплава АМг6 влияние остаточных напряжений после лазерной обработки составляет около 20 %.
7. Экспериментально установлено, что воздействие импульсного высокоинтенсивного лазер- ного излучения на поверхность деформируемого алюминиевого сплава АМг6 вызывает за- рождение полос локализованной деформации, снижающих коррозионную прочность сплава, а пропускание электрического тока плотностью 60 А/мм2 подавляет зарождение полос. Предложены механизмы зарождения и/или подавления деформационных полос в условиях лазерного и электротокового воздействий.
8. Разработан и экспериментально верифицирован электрохимический механизм действия импульсного тока на зарождение деформационных полос, основанный на растворении током включений вторичной фазы, вызывающего гомогенизацию пластической деформации.
Актуальность темы. Многие промышленные поликристаллические алюминиевые
сплавы систем Al-Mg-Mn, Al-Li-Mg, Al-Cu-Mg и др. широко используются как
конструкционные материалы в химическом машиностроении, автопроме и как
проводниковые материалы в электротехнической промышленности благодаря высокой
стойкости к коррозии, удельной прочности и электропроводности. В условиях
технологической обработки и эксплуатации эти сплавы могут подвергаться интенсивной
пластической деформации (прокатка, равноканальное угловое прессование и т.д.),
ударным нагружениям, воздействию лазерного излучения (лазерная сварка, маркировка,
гравировка, лазерная обработка поверхности и др.), действию агрессивной среды,
электромагнитных полей и т.д. Вместе с тем, эти сплавы демонстрируют прерывистую
деформацию, известную как эффект Портевена-Ле Шателье (ПЛШ) в широком
температурно-скоростном диапазоне механических испытаний. Несмотря на
многочисленные исследования эффекта ПЛШ механизмы этого явления, его связь с
формированием полос макролокализованной деформации до сих пор остаются
дискуссионными вопросами. Исследование влияния коррозионной среды и
высокоэнергетических внешних воздействий (лазерного излучения, электрического тока,
ударных волн и т.д.) на прерывистую деформацию и локализацию деформации в
макрополосах, являющихся центрами коррозии, представляет новое актуальное
направление исследования, важное как с научной, так и с практической точек зрения.
Как известно, коррозия под напряжением является одним из наиболее опасных видов
коррозии. В поликристаллических металлических сплавах, коррозия под напряжением,
как предполагается, происходит, в основном, по механизмам межкристаллитной и
транскристаллитной коррозии. В промышленных сплавах системы Al-Mg
межкристаллитная коррозия включает селективное растворение частиц вторичной
(Al3Mg2)-фазы, выделяющихся по границам зерен, распространение трещин в зоне,
обедненной магнием вдоль границ зерен или в результате водородного охрупчивания.
Транскристаллитная коррозия в этих сплавах происходит вследствие выноса атомов
магния на поверхность дислокационными скоплениями за счет динамического
деформационного старения (ДДС) дислокаций. Вместе с тем, ДДС и взаимодействие
дислокаций с преципитатами являются основными обсуждаемыми механизмами развития
прерывистой деформации и формирования деформационных полос. До настоящего
времени не проводились систематические исследования действия коррозионной среды и
внешних высокоэнергетических воздействий на формирование полос локализованной
деформации, негативно влияющих на коррозионные свойства алюминиевых сплавов.
Цель диссертационной работы: теоретическое и экспериментальное изучение
действия химически агрессивной жидкой среды и высокоэнергетических внешних полей
на прочность, прерывистую деформацию и коррозионное разрушение алюминий-
магниевых сплавов.
В соответствии с поставленной целью сформулированы следующие задачи
исследования:
− разработать методический подход к комплексному исследованию влияния
коррозионной среды и высокоэнергетических воздействий на механическую
неустойчивость и разрушение алюминий-магниевых сплавов;
− экспериментально исследовать влияние коррозионной среды на деформационное
поведение алюминиевого сплава в условиях ползучести;
− разработать модель растворения поликристаллического металла в жидкой химически
агрессивной среде;
− разработать механизм потери механической устойчивости алюминиевого сплава,
деформируемого в коррозионной среде, на основе расчета полей напряжений вблизи
1. Разработан комплексный подход к изучению влияния коррозионной среды и
высокоэнергетических воздействий на механическую неустойчивость металлических
сплавов, основанный на сочетании экспериментальных in situ исследований кинетики
коррозии и кинетики локализации пластической деформации с методами математического
моделирования процессов коррозии и электрохимического взаимодействия
электрического тока выделениями вторичных фаз в деформируемых сплавах.
2. Экспериментально установлено, что химический процесс растворения
концентрированной соляной кислотой локального участка поверхности деформируемого
алюминий-магниевого сплава вызывает: а) генерирование широкополосного, в полосе от
0.1 Гц до 600 кГц, сигнала акустической эмиссии, обусловленного динамикой и
разрушением многочисленных пузырьков водорода, образующихся в ходе коррозионного
процесса; б) зарождение полос локализованной пластической деформации, вызывающих
развитие скачка деформации на кривой ползучести.
3. Разработана модель растворения поликристаллического металла в агрессивной жидкой
среде. На основе численного расчета эволюции формы коррозионного фронта выявлен и
экспериментально верифицирован морфологический переход от евклидовой к
фрактальной геометрии фазовой границы. Показано, что коррозия поликристаллического
металла в жидкой агрессивной среде представляет новый пример топохимического
процесса, кинетика которого описывается статистическим распределением Колмогорова-
Джонсона-Мейла-Аврами.
4. Установлена корреляция между временной зависимостью растворенной массы металла
и интегральным акустическим откликом, зарегистрированным в ходе травления
алюминиевого сплава раствором соляной кислоты. Показано, что акустический отклик на
коррозионный процесс несет информацию о кинетике растворения алюминия в соляной
кислоте и может быть использован для разработки экспресс-метода контроля скорости
коррозии и исследования ее стадийности.
5. Предложен механизм потери механической устойчивости при коррозионном
воздействии на поверхность деформируемого алюминиевого сплава на основе расчета
полей упругих напряжений вблизи фрактальной границы коррозионного пятна. Показано,
что в условиях коррозии под напряжением локальные напряжения превышают в 10-30 раз
уровень приложенного напряжения, что может спровоцировать коллективное
срабатывание источников дислокаций и развитие макроскопической дислокационной
лавины, которая вызывает скачок деформации на кривой растяжения.
6. Разработана модель коррозионного разрушения алюминиевого сплава, обработанного
импульсом лазерного излучения. Показано, что остаточные напряжения ускоряют
коррозию вследствие механо-электрохимического эффекта, а термообработка, снимающая
остаточные напряжения увеличивают коррозионную стойкость сплава после лазерной
обработки. Для сплава АМг6 влияние остаточных напряжений после лазерной обработки
составляет около 20 %.
7. Экспериментально установлено, что воздействие импульсного высокоинтенсивного
лазерного излучения на поверхность деформируемого алюминиевого сплава АМг6
вызывает зарождение полос локализованной деформации, снижающих коррозионную
прочность сплава, а пропускание электрического тока плотностью 60 А/мм2 подавляет
зарождение полос. Предложены механизмы зарождения и/или подавления
деформационных полос в условиях лазерного и электротокового воздействий.
8. Разработан и экспериментально верифицирован электрохимический механизм действия
импульсного тока на зарождение деформационных полос, основанный на растворении
током включений вторичной фазы, вызывающего гомогенизацию пластической
деформации.
1. Roberge P.R. Handbook of corrosion engineering. New York.:McGraw-Hill. 2000. 1072 p.
2. Davis J.R. Corrosion of aluminium and aluminium alloys. ASM International. 1999. 313 p.
3. Schweitzer P.A. Fundamentals of Metallic Corrosion. CRC Press. 2006. 752 p.
4. Moore K.L., Sykes J.M., Grant P.S. An electrochemical study of repassivation of aluminium
alloys with SEM examination of the pit interiors using resin replicas // Corrosion Science.
2008. №50. P. 3233-3240.
5. Bocher F., Flower H.M., Ryan M.P. The effect of microstructure on localized corrosion in
creep age-formable aluminium alloys: identification of intermetallic particles and pit
initiation sites // Electrochemical Society. 2006. V.153. №12. P. B551-B554.
6. Bohni H., Uhlig H.H. Environmental factors affecting the critical pitting potential of
aluminium // Journal of Electrochemical Society. 1969. V.116. № 7. P. 906-914.
7. Monticelli C., Brunoro G., Frignani A., Trabanelli G. Evaluation of corrosion inhibitors by
electrochemical noise analysis // Electrochemical Society. 1992. V.139. №3. P. 706-711.
8. Adams A.A., Eagle K.E., Foley R.T. Synergistic effects of anions in the corrosion of
aluminum alloys // Electrochemical Society. 1972. V.119. №12. P. 1692-1694.
9. McKissick A.M., Adams A.A., Foley R.T. Synergistic effects of anions in the corrosion of
aluminum alloys // Electrochemical Society. 1970. V.117. №11. P. 1459-1460.
10. Fontana M.G. Corrosion Engineering. 1986. New York: Mcgraw-Hill, Inc. P. 51-152.
11. Sinyavskii V.S., Ulanova V.V., Kalinin V.D. On the mechanism of intergranular corrosion of
aluminium alloys // Protection of Metals. 2004. V.40. №5. P. 481-490.
12. Liao M., Bellinger N.C., Komorowski J.P. Modeling the effects of prior exfoliation
corrosion on fatigue life of aircraft wing skins // International Journal of Fatigue. 2003.
V.25. P. 1059-1067
13. Lucas K.A., Clarke H. Corrosion of aluminium-based metal matrix composites. // Research
Studies Ltd., Somerset England. 1993. P. 25-48.
14. Leblanc P.P., Frankel G.S. Investigation of filiform corrosion of epoxycoated 1045 carbon
steel by scanning Kelvin probe force microscopy // Electrochemical Society. 2004. V.151.
№3. P. B105-B113.
15. McMurray H.N., Williams G., O’Driscoll S. Chromate inhibition of filiform corrosion on
organic coated AA2024-T3 studied using the Scanning Kelvin Probe // Electrochemical
Society. 2004. V.151. №7. P. B406-B414.
16. LeBozec N., Persson D., Thierry D. Axelsen S.B. Effect of climatic parameters on filiform
corrosion of coated aluminium alloys. // Corrosion. 2004. V.60. №6. P. 584-592.
17. Leth-Olsen H., Nisancioglu K. Filiform corrosion of aluminium sheet. I. corrosion behaviour
of painted material. // Corrosion Science. 1998. V.40. №7. P. 1179-1194.
18. Craig B.D. Fundamental aspects of corrosion films in corrosion science. Plenum Press, New
York. 1991. 206 p.
19. Davo B., Conde A., Damborenea J.de. Stress corrosion cracking of B13, a new high strength
aluminium lithium alloy. // Corrosion Science. 2006. V.48. №12. P. 4113-4126
20. Popović M. Romhanji E. Stress corrosion cracking susceptibility of Al- Mg alloy sheet with
high Mg Content // Materials Processing Technology. 2002. V.125-126. P. 275-280.
21. Xiaodong L., Frankel G.S. Effect of comprehensive stress on localised corrosion in AA
2024-T3. // Corrosion Science. 2006. V.48. P. 3309-3329.
22. Vargel C. Corrosion of aluminium // Elsevier. First edition. 2004. 626 p.
23. Акимов Г. В. Теория и методы исследования коррозии металлов // М: Изд-во АН
СССР. 1945. 350 с.
24. Синявский В. С., Вальков В. Д., Калинин В. Д. Коррозия и защита алюминиевых
сплавов // М: Металлургия. 1986. 368 с.
25. Шрайера Л. Л. Коррозия. Справочное издание // М.: Металлургия. 1981. 632 с.
26. Magnin T., Combrade P. Environment Sensitive Fracture // Materials Science and
Technology Series. 2000. P. 216-318.
27. Jones R.H., in ASM Handbook, Volume 13A, Corrosion: Fundamentals, Testing and
Protection, edited by S. D. Cramer and B. S. Covino, Jr. ASM International, Materials Park,
OH, 2003. P. 346-366.
28. Sastri V.S., Ghali E., Elboujdaini M., Corrosion Prevention and Protection: Practical
Solutions. Wiley, Chichester,West Sussex, UK. 2007. 557 p.
29. Kaufman J.G., in ASM Handbook, Volume 13B, Corrosion: Materials, edited by S. D.
Cramer and B. S. Covino, Jr. ASM International, Materials Park, OH, 2005. P. 95–124.
30. ASM International Handbook Committee, in ASM Specialty Handbook, Aluminum and
Aluminum Alloys, edited by J.R. Davis. ASMInternational, Materials Park, OH, 1998, P.
199-484, 579-731.
31. Pugh E.N., in Encyclopedia of Materials Science and Engineering, V. 2. Pergamon Press,
Elmsford, NY, 1986. P. 889-890.
32. Ghali E., in Uhlig’s Corrosion Handbook, 2nd edition, edited by R. W. Revie. Wiley,
Hoboken, NJ, 2000. P. 677-715.
33. Taylor C.D., Marcus P. Molecular modeling of corrosion processes: scientific development
and engineering applications. John Wiley & Sons, 2015. 272 p.
34. Maurice V., Marcus P. Progress in corrosion science at atomic and nanometric scales //
Progress in Materials Science. 2018. V.95. P. 132-171.
35. Verma C., Lgaz H., Verma D., Ebenso E.E., Bahadur I., Quraishi M. Molecular dynamics
and Monte Carlo simulations as powerful tools for study of interfacial adsorption behavior of
corrosion inhibitors in aqueous phase: a review // J. Mol. Liq. 2018. V.260. P. 99-120.
36. Li S., Xu Y., Li H., Guan X. Uniform and pitting corrosion modeling for high-strength
bridge wires // J. Bridge. Eng. 2014. V.19. P. 04014025.
37. Huang Y., Tu S-T, Xuan F-Z. Pit to crack transition behavior in proportional and non-
proportional multiaxial corrosion fatigue of 304 stainless steel // Eng. Fract. Mech. 2017.
V.184. P. 259-272.
38. Bard A.J., Faulkner L.R., Leddy J., Zoski C.G. Electrochemical methods: fundamentals and
applications. New York: Wiley, 1980. 864 p.
39. Tsuyuki C, Yamanaka A, Ogimoto Y. Phase-field modeling for pH-dependent general and
pitting corrosion of iron // Sci Rep 2018. V.8. P. 12777.
40. Laycock N., White S., Noh J., Wilson P., Newman R. Perforated covers for propagating
pits // Electrochem. Soc. 1998. V.145. P. 1101-1108.
41. Liu M, Qiu D, Zhao M-C, Song G, Atrens A. The effect of crystallographic orientation on
the active corrosion of pure magnesium // Scripta Mater. 2008. V.58. P. 421-424.
42. Jafarzadeh S, Chen Z, Bobaru F. Peridynamic modeling of intergranular corrosion damage. //
Electrochem. Soc. 2018. V.165. P. 362-374.
43. Gutman E. M. Mechanochemistry of Solid Surfaces. World Scientific Pub Co Inc,
Singapore; River Edge, NJ, 1994. 322 p.
44. Adlakhaa I., Gholami Bazehhour B., Muthegowda N.C., Solanki K.N. Effect of mechanical
loading on the galvanic corrosion behavior of a magnesium-steel structural joint // Corrosion
Science. V.133. 2018. P. 300-309.
45. Simo J.C., Hughes T.J.R., Computational Inelasticity. Springer Science & Business Media,
2006. 392 p.
46. Хилл Р. Математическая теория пластичности. М.: Гостехиздат. 1956. 410 с.
47. Краснов К.С. , Воробьев Н.К., Горднев И.Н. Физическая химия. Книга 2. М.: Высш.
шк., 2001. 319 c.
48. Brewick P.T., Kota N., Lewis A.C., DeGiorgi V.G., Geltmacher A.B., Qidwai S.M.
Microstructure-sensitive modeling of pitting corrosion: Effect of the crystallographic
orientation // Corrosion Science. 2017. V.129. P. 54-69.
49. Brewick P.T., DeGiorgi V.G., Geltmacher A.B., Qidwai S.M. Modeling the influence of
microstructure on the stress distributions of corrosion pits // Corrosion Science. 2019.
№158. P. 108111.
50. Madrigal-Canoa M., Hallena J.M., Arce-Estradaa E.M., Tu Le Manha Effect of
crystallographic texture and microstructure on pitting corrosion behavior of low carbon
steels: A Monte Carlo model // Computational Materials Science. 2019. №161. P. 394-402.
51. Jafarzadeh S., Chen Z., Bobaru F. Computational modeling of pitting corrosion // Corrosion
reviews. 2019. V.37. №5. P. 419-439.
52. Gabrielli A., Baldassarri A., Sapoval B. Surface hardening and self-organized fractality
through etching of random solids // Physical Review. 2008. V.62. P. 3103-3116.
53. Santra S.B., Sapoval B. Critical fluctuation and self-organized fractality in chemical reaction:
Spontaneous gradient percolation in the etching of random solids // Physica A. 1999. V.266.
P. 160-172.
54. Silling S.A. Reformulation of elasticity theory for discontinuities and long-range forces. //
Mech Phys Solids. 2000. V.48. P. 175-209.
55. Mai W, Soghrati S. New phase field model for simulating galvanic and pitting corrosion
processes // Electrochim Acta. 2018. V. 260. P. 290-304.
56. Mai W, Soghrati S. A phase field model for simulating the stress corrosion cracking initiated
from pits // Corros. Sci. 2017. V.125. P. 87-98.
57. Анисимов С.И., Имас Я.А., Романов Г.С., Ходыко Ю.В. Действие излучения большой
мощности на металлы. Наука. М., 1970. 272 с.
58. Рэди Дж. Действие мощного лазерного излучения. Мир. М.,1974. 468 с.
59. Миркин Л.И. Физические основы обработки материалов лучами лазера. МГУ. М.,
1975. 384 с.
60. Вейко В. П., Либенсон М. Н., Червяков Г. Г., Яковлев Е. Б. Взаимодействие лазерного
излучения с веществом. ФИЗМАТЛИТ, 2008. 312 с.
61. Борисов Ю. С., Демченко В. Ф.Численное моделирование теплообмена и
гидродинамики при лазерно-плазменной обработке металлических материалов //
Автоматическая сварка. 2013. №4. C. 3-8.
62. Ионин А. А., Кудряшов С. И., Самохин А. А. Абляция поверхности материалов под
действием ультракоротких лазерных импульсов // Успехи физических наук. 2017.
Т. 187. № 2. C. 159-172.
63. Писарев В. В., Стариков С. В. Сопоставление 1D-, 2D- и 3D- атомистических моделей
лазерной абляции алюминия // Физико-химическая кинетика в газовой динамике. 2014.
Т.15 № 6. C. 1-3.
64. Григорьянц А. Г., Шиганов И. Н., Мисюров А. И. Технологические процессы лазерной
сварки. М: Изд-во МГТУ им Н. Э. Баумана. 2006. 664 с.
65. Никифоров Г.Д. Металлургия сварки плавлением алюминиевых сплавов. М.,
«Машиностроение», 1972. 264 с.
66. Парфенов В. А. Лазерная микрообработка материалов: Учеб. Пособие. СПб.: Изд-во
СПбГЭТУ «ЛЭТИ». 2011. 59 с.
67. Тукаев Р. Ф., Сисанбаев А. В. и др. Применение лазерной сварки при изготовлении
нефтегазового оборудования // Материаловедение и защита от коррозии. 2016. Т. 14.
№ 4. С. 162-166.
68. Хаскин В.Ю. Процессы упрочнения и нанесения покрытий с использованием
лазерного излучения (Обзор) // Автоматическая Варка. 2008. № 12. С. 24-32.
69. Харанжевский Е.В. Физические основы лазеров и аддитивных нанотехнологий:
учебное пособие. Ижевск: Изд. Центр «Удмуртский университет». 2020. 296 с.
70. Григорьянц А. Г., Мисюров А. И. Возможности и перспективы применения лазерной
наплавки // Технол. машиностр. 2005. № 10. С. 52-56.
71. Григорьянц А. Г., Сафонов А. Н. Лазерная техника и технология. Кн. 3: Методы
поверхностной лазерной обработки. М.: Высш. шк. 1987. 191 с.
72. Ушаков И.В., Симонов Ю.В. Управление физико-механическими свойствами
поверхности титановых сплавов короткоимпульсным лазерным излучением // Вестник
Московского государственного областного университета. Серия: Физика-Математика.
2019. № 4. С. 30-42.
73. Симонов Ю.В., Ушаков И.В. Механические свойства поверхностных структур
титанового сплава ВТ9 после многократной локальной обработке наносекундными
лазерными импульсами // Вестник Московскогогосударственного областного
университета. Серия: Физика-Математика. 2020. № 2. С. 19-35.
74. Завестовская И.Н., Игошин В.И., Канавин А.П. и др. Теоретическое исследование
процессов лазерной аморфизации и получения микрокристаллических структур // Тр.
ФИАН. 1993. №217. С. 3-12.
75. Steen W., Watkins K.G., Mazumder J. Laser Material Processing. Springer. 2010. 576 p.
76. Григорьянц А.Г., Сафонов А.Н., Шибаев В.В. и др. Лазерная наплавка фасок клапанов
двигателя внутреннего сгорания // Свароч. пр-во. 1984. № 5. С. 19-20.
77. Григорьянц А.Г., Шиганов И.Н., Шилов С.С., Алексеев Г.М. Лазерно-световая
обработка материалов как новое направление в гибридных процессах // Технол.
машиностр. 2005. № 10. С. 37-45.
78. Хорунов В. Ф., Шань Цзиго. Сварка и пайка с использованием светового луча дуговых
ксеноновых ламп (Обзор) // Автомат. сварка. 1995. № 5. С. 48-52.
79. Seyffarth P., Krivtsun I. V. Laser-arc processes and their applications in welding and
material treatment // Welding and allied processes. London: Taylor and Francis Books. 2002.
Vol. 1. 200 p.
80. Zreris R., Nowotny S., Berger L.-M. et al. Characterization of сoatings deposited by laser-
assisted atmospheric plasma spraying // Proc. of thermal spray conf., Orlando, USA. 2003.
P. 567-572.
81. Hai-ou Zhang, Ying-ping Qian, Gui-lan Wang. Study of rapid and direct thick coating
deposition by hybrid plasma – laser manufacturing // Surface & Coatings Technol. 2006.
№201. P. 1739-1744.
82. Wilden J., Bergmann J. P., Dolles M. Riporti superficiali laser: aumento di efficienza e
flessibilita tramite processi ibridi // Riv. Ital. Saldatura. 2005. P. 809-816.
83. Белл Дж.Ф. Экспериментальные основы механики деформируемых твердых тел. Ч.2. М.:
Наука. 1984. 432 с.
84. Shibkov A.A., Lebyodkin M.A., Lebedkina T.A., Gasanov M.F., Zolotov A.E., Denisov
A.A. Millisecond dynamics of deformation bands during discontinuous creep in an AlMg
polycrystal // Physical Review E. 2020. V. 102. P. 043003.
85. ШибковА.А.,ЗолотовА.Е.,ЖелтовМ.А.,ДенисовА.А.,ГасановМ.Ф.
Макролокализацияпластическойдеформациипри прерывистойползучести
алюминий-магниевого сплава AМг6 // Журнал технической физики. 2014. Т. 84. № 4.
С. 40-46.
86. Shibkov A.A., Gasanov M.F., Zheltov M.A., Zolotov A.E., IvolginV.I. Intermittent
plasticity associated with the spatio-temporal dynamics of deformation bands during creep
tests in an AlMg polycrystal // Int. J. Plast. V. 86. 2016. P. 37-55.
87. Gonzalez R. Digital image processing. New York: Pearson, 2018. 955 p.
88. Edgar G. Classics on fractals. Boulder: Westview Press, 2004. 271 p.
89. Feder J. Fractals. New York – London: Plenum press, 1988. 305 p.
90. Aurenhammer F. Voronoi diagrams − a survey of a fundamental geometric data structure //
ACM Computing Surveys. 1991. V. 23. № 3. P. 345-405.
91. Christian J. W. The theory of transformations in metals and alloys, Part I. New York:
Pergamon, 1975. 542 p.
92. Avrami M. Kinetics of phase change. General theory // Journal of Chemical Physics. 1939.
V. 7. P. 1103-1112.
93. Sangval K. Etching of crystals: theory, experiment, application. Amsterdam – Oxford – New
York –Tokyo: North Holland. 1987. 497 p.
94. Weibull W. A statistical distribution function of wide applicability // Journal of applied
mechanics. 1951. V. 18. P. 293-297.
95. Kolmogorov A. K statisticheskoj teorii kristallizacii metallov // Izv. Acad. Sci. USSR. Math.
Ser. 1. 1937. P. 355-359.
96. Dimmler K., Parris M., Butler D. et al. Switching kinetics in KNO3 ferroelectric thin-film
memories // J. Appl. Phys. 1995. V. 61, №12. P. 5467-5470.
97. Jensen H.J. Self-organized criticality. Cambridge University Press, Cambridge. 1998.
98. Bak P., Tang C., Wiessenfeld K. // Phys. Rev. A. 1988. V. 38. № 1. P. 364-374.
99. Svenungsson J., Choqueta Kaplan A.F.H. Laser welding process – a review of keyhole
welding modeling // Physics Procedia. 2015. № 78. P. 182-191.
100.Беляев А.И., Бочвар О.С., Буйнов Н.Н. Металловедение алюминия и его сплавов:
Справ. Изд. М.: Металлургия. 1983. 279 с.
101.Ландау Л.Д., Лифшиц Е.М. Теоретическая физика. Том VI. Гидродинамика. М.:
Наука. 1988. 736 с.
102.Bruere V., Touvrey C., Namy P. Authier N. Multiphysics modeling of pulsed laser
welding // Journal of laser applications. 2017. V.29. №2. P.022403.
103.Xu L.Y., Cheng Y.F. Development of a finite element model for simulation and
prediction of mechanoelectrochemical effect of pipeline corrosion // Corrosion Science.
2013. №73. p. 150-160.
104.Sun J., Cheng Y.F. Modelling of mechano-electrochemical interaction of multiple
longitudinally aligned corrosion defects on oil/gas pipelines // Engineering Structures. 2019.
№190. p. 9-19.
105.Русанов А.И. Термодинамические основы механохимии. СПб.: Наука. 2006. 221 с.
106.Зайнуллин Р.С. Обобщенное уравнение механохимической повреждаемости
металлов // Нефтегазовое дело. 2015. №3. С. 119-123.
107.Ажогин Ф.Ф. Коррозионное растрескивание и защита высокопрочных сталей. М.:
Металлургия, 1974. 256 с.
108. Долинский В.М. Изгиб тонких пластин, подверженных коррозионному износу //
Динамика и прочность машин. Харьков. 1975. №.21. С. 16-19.
109. КришталМ.М.,МерсонД.Л.Взаимосвязьмакролокализациидеформации,
прерывистой текучести и особенностей акустической эмиссии алюминиево-
магниевых сплавов // ФММ. 1996. Т. 81. № 1. С. 155.
110. Shibkov A.A., Zheltov M.A., Gasanov M.F., Zolotov A.E., Denisov A.A., Lebyodkin M.A.
Dynamics of deformation band formation investigated by high-speed techniques during
creep in an AlMg alloy // Materials Science & Engineering A. 2020. V. 772. P. 138777.
111. Estrin Y., Kubin L.P. Spatial сoupling and propagative plastic instabilities // Continuum
models for materials with microstructure. Edited by H.-B. Muhlhaus. New-York: Wiley &
Sons. 1995. P. 395-450.
112. Brechet Y., Estrin Y. On the influence of precipitation on the Portevin-Le Chatelier
effect // Acta Metal. Mater. 1995. V. 43. №3. P. 955.
113. Баскаков С.И. Радиотехнические цепи и сигналы. М.: Высш. шк. 2000. 462 с.
114. Vinogradov A., Lasarev A. Continuous acoustic emission during intermittent plastic flow
in -brass // Scr. Mater. 2012. V. 66. P. 745.
115. Лыков А.В. Теория теплопроводности. М.: Высш. шк. 1967. 600 с.
116. Шибков А.А., Кольцов Р.Ю., Желтов М.А., Шуклинов А.В., Лебедкин М.А.
Динамика спонтанной делокализации пластической деформации при неустойчивом
пластическом течении сплавов Al-Mg // Известия РАН. Серия физическая. 2006. Т.
70. № 9. С. 1372.
117. Головин Ю.И., Горбунов А.В., Шибков А.А. Динамика и электрическое поле
дефектов при лазерном повреждении поверхности ионных кристаллов // ФТТ. 1988.
Т. 30. № 7. С. 1931-1937.
118. Спицын В.И., Троицкий O.A. Электропластическая деформация металлов. М.: Наука.
1985. 161 с.
119. Троицкий О.А., Баранов Ю.В., Авраамов Ю.С., Шляпин А.Д. Физические основы и
технологии обработки современных материалов: Теория, технология, структура и
свойства: В 2 т.: Т. 1. Ижевск: Институт компьютерных исследований. 2004. 592 с.
120. Shibkov A.A., Denisov A.A., Zheltov M.A., Zolotov A.E., Gasanov M.F. The electric
current-induced suppression of the Portevin – Le Chatelier effectin Al-Mg alloys //
Materials Science & Engineering A 610. 2014. P. 338-343.
121. Шибков А.А., Золотов А.Е., Желтов М.А., Денисов А.А., Гасанов М.Ф. Исследование
механизмовподавленияпрерывистойдеформацииэлектрическимтоком//
Кристаллография 2015. Т. 60. № 6. С. 938-949.
122. Dolinsky Yu., Elperin T. Thermodynamics of nucleation in current-carrying conductors //
Phys. Rev. B. 1994. V. 50. P. 52.
123. Готтштайн Г. Физико-химические основы материаловедения – М.: БИНОМ.
Лаборатория знаний. 2014. 403 с.
124. Straumal B.B., Protasova S.G., Mazilkin A.A., Rabkin E., Goll D., Schütz G., Baretzky B.,
Valiev R. Deformation-driven formation of equilibrium phases in the Cu-Ni alloys //
Mater. Sci. 2012. V. 47. P. 360-367.
125. Разумов И.К., Ермаков А.Е., Горностырев Ю.Н., Страумал Б.Б. Неравновесные
фазовые превращения в сплавах при интенсивной пластической деформации // УФН.
2020. № 190. С. 785-810.
126. Гегузин Я.Е. Диффузионная зона. М.: Наука. 1979. 344 с.
127. Колобов Ю.Р. Зернограничная диффузия и свойства наноструктурных материалов.
Новосибирск: Наука. 2001. 232 с.
128. Сагарадзе В.В., Шабашов В.Л. Аномальные диффузионные фазовые превращения в
сталях при интенсивной холодной деформации/ ФММ. 2011. Т.112. №2. С .155-174.
129. Бокштейн Б.С. Диффузия в металлах. М.: Металлургия. 1978. 248 с.
129. Локшин Ф.Л., Шаханова Г.В., Агеева А.Т., Баканова Л.Н. Влияние температуры и
продолжительности отпуска на структуру и фазовый состав сплава АМг6 // МиТОМ.
1966. № 9. С. 59-61.
130. Tu K.N., Yeh C.C., Liu C.Y., Chin C. Effect of current crowding on vacancy diffusion and
void formation in electromigration // Appl. Phys. Lett. 2000. V.76. №.8. P. 988-990
131. Blech I.A. Electromigration in thin aluminum films on titanium nitride // J. Appl. Phys.
1976. V. 47. P. 1203.
132. Dolinsek J., Apih T., Jeglic P., Smiljanic I. Magnetic and transport properties of the giant-
unit-cell Al3.26Mg2 complex metallic alloy // Intermetallics. 2007. V. 15. P. 1367-1376.
133. Киттель Ч. Квантовая теория твердых тел. М.: Наука. 1967. 492 с.
134. Лившиц Б.Г., Крапошин В.С., Линецкий Я.Л. Физические свойства металлов и
сплавов. М.: Металлургия, 1980. 174 с.
Читать «Влияние коррозионной среды и высокоэнергетических воздействий на прочность, прерывистую деформацию и разрушение алюминий-магниевых сплавов»
Последние выполненные заказы
Хочешь уникальную работу?
Больше 3 000 экспертов уже готовы начать работу над твоим проектом!